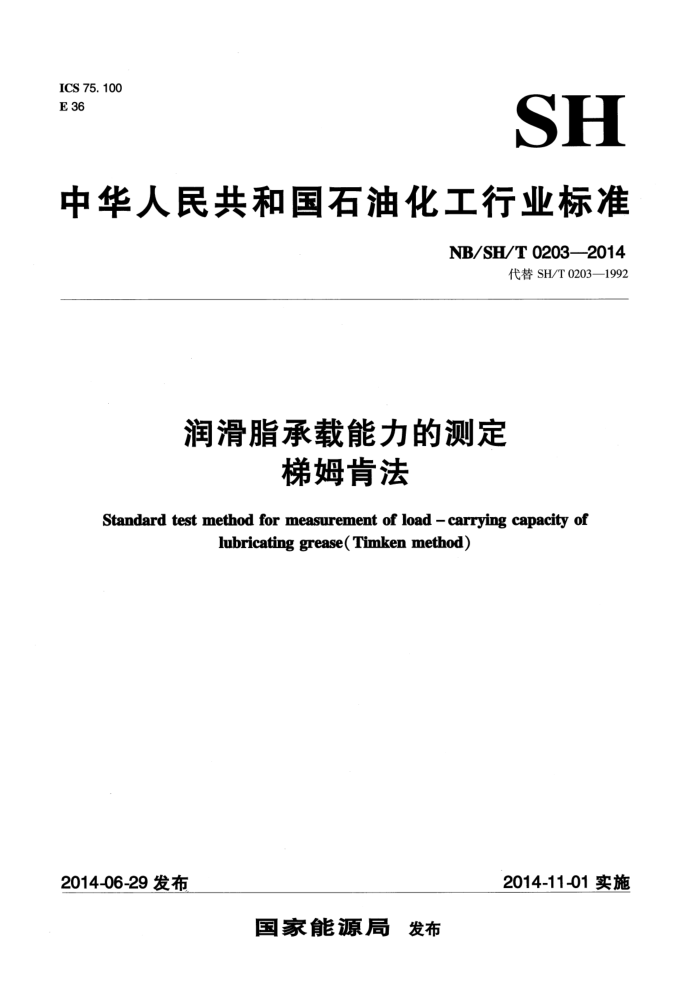
ICS 75.100 E 36
SH
中华人民共和国石油化工行业标准
NB/SH/T 02032014
代替SH/T0203—1992
润滑脂承载能力的测定
梯姆肯法
Standard test method for measurement of load -carrying capacity of
lubricating grease(Timkenmethod)
2014-11-01实施
2014-06-29 发布
国家能源局发布
NB/SH/T02032014
目 次
前言
范围 2 规范性引用文件 3 术语和定义 4 方法概要 5 方法应用 6 仪器 7 试剂与材料 8 仪器的准备· 9 试验步骤 10 结果计算和报告 11 精密度和偏差附录A(规范性附录)有关安全问题附录B(规范性附录)梯姆肯极压试验机附录C(规范性附录)刮伤判断明显有疑问情况下的试验程序附录D(资料性附录)摩擦试验的操作
1
3
+
8
11 12
NB/SH/T0203—2014
前言
本标准按照GB/T1.1—2009给出的规则起草。 本标准代替SH/T0203一1992《润滑脂极压性能测定法(梯姆肯试验机法)》,本标准与SH/T
0203—1992相比的主要变化如下:
将标准名称修改为“润滑脂承载能力的测定梯姆肯法”;根据GB/T17754—1999“摩擦学术语”,本标准将SH/T0203-1992中的术语“擦伤”、“擦伤值”统一修改为“刮伤”、“刮伤值”; SH/T0203一1992标准对刮伤判断:在光滑的磨痕内有刮伤或条纹产生,但未延伸到磨痕之外,这种情况认为是刮伤。本标准对刮伤判断:在光滑的磨痕内有刮伤或条纹产生,但未延伸到磨痕之外,这种情况不认为是刮伤。 本标准的OK值和刮伤值的结果报告均以N(kg)为单位;SH/T0203一1992的OK值和刮伤值的结果报告以N(Ibf)为单位;本标准的重复性为不大于平均值的23%,再现性为不大于平均值的59%;SH/T0203一1992 的重复性为不大于两个负荷级,再现性为不大于四个负荷级;增加了规范性附录A“有关安全问题”;增加了规范性附录B“梯姆肯极压试验机”;增加了规范性附录C“刮伤判断明显有疑问情况下的试验程序”;增加了资料性附录D“摩擦试验的操作”。
本标准采用重新起草法修改采用美国试验与材料协会标准ASTMD2509-03(2008)《润滑脂承载能力测定法(梯姆肯法)》。
为了更适合我国国情,在采用ASTMD2509-03(2008)时,本标准做了一些修改。本标准与 ASTMD2509-03(2008)的主要差异及其原因如下:
删除了ASTMD2509-03(2008)引用标准中没有被本标准直接引用的标准,引用了的标准采用我国相应的现行标准。 删除了ASTMD2509-03(2008)中有关对精密度说明的内容。 -删除了ASTMD2509-03(2008)中第12章“关键词”。
本标准由中国石油化工集团公司提出。 本标准由全国石油产品和润滑剂标准化技术委员会石油燃料和润滑剂分技术委员会(SAC/TC280/
SC1)归口。
本标准起草单位:中国石油天然气股份有限公司兰州润滑油研究开发中心。 本标准主要起草人:李彤、雷爱莲、谢惊春、朱文静、夏群英。 本标准所代替标准的历次版本发布情况为:
SH/T0203—1992。
I
NB/SH/T0203—2014
润滑脂承载能力的测定 梯姆肯法
警告:本标准涉及某些有危险的材料、操作和设备,但是无意对与此有关的所有安全问题都提出建议。因此,用户
在使用本标准之前应建立适当的安全和防护措施,并确定相关规章限制的适用性。详见附录A。
1范围
本标准规定了使用梯姆肯极压试验机测定润滑脂承载能力的标准方法。 本标准适用于评价润滑脂的承载能力。 注:本标准采用国际单位制【SI】单位,括号内为英制单位。
2规范性引用文件
下列文件对于本文件的应用是必不可少的。凡是注日期的引用文件,仅所注日期的版本适用于本文件。凡是不注日期的引用文件,其最新版本(包括所有的修改单)适用于本文件。
GB/T686化学试剂丙酮 GB1922—2006油漆及清洗用溶剂油 GB/T17754—1999摩擦学术语
3术语和定义
下列术语和定义适用于本文件。 3.1通用术语定义 3. 1. 1
润滑脂承载能力load-carryingcapacityofalubricatinggrease 通常指在给定的试验条件下,摩擦副正常运转时,接触表面不产生刮伤、卡咬或者金属间的表面
焊着等破坏形式的最大负荷或压力。
注:润滑脂承载能力的值是随着不同试验方法而变化的。 3. 1. 2
刮伤scoring 在摩擦表面滑动方向上形成广泛的沟槽和划痕的严重磨损形式。 注:如果润滑剂能够持续地保持,试块上则得到光滑的磨痕。当润滑膜破裂,则发生刮伤或试块的表面破坏,见图
1。最简单且最容易辨认的刮伤形式是:试块上磨痕比较宽,且有犁痕产生,金属从试块上转移到试环的接触表面上,这种表面破坏的形式经常会遇到。但是,也有如下的情况产生:磨痕表面比较光滑,但存在局部的破坏,即划痕延伸到磨痕之外,这种情况也视为刮伤。还有一种情况是:虽然在光滑的磨痕内有划痕产生,但未延伸到磨痕之外,在本方法中不认为是刮伤。
[GB/T17754—1999中5.39条] 3.1. 3
卡咬或焊着seizureorwelding 摩擦表面产生严重粘着或转移,使相对运动停止或断续停止的现象。或在摩擦学中,指直接接触
1
NB/SH/T 0203—2014
典型的OK无刮伤
安装不正确
刮伤磨痕
图1试块上的各种典型磨痕示意图
的金属表面于任何温度下形成的键合。
「GB/T17754—1999中5.42条】 3. 1. 4
磨损 wear 固体表面和其接触的物体做相对运动时,该固体接触表面的物质不断损失,产生残余变形或其它
损伤。
[GB/T17754—1999中2.4条] 3.2·专用术语定义 3. 2. 1
OK值OKvalue 在测定润滑剂承载能力过程中,没有引起刮伤或卡咬时加在负荷杠杆磁码盘上的最大质量。
3. 2. 2
刮伤值scorevalue 在测定润滑剂承载能力的过程中,出现刮伤或卡咬现象时加在负荷杠杆磁码盘上的最小质量。
4方法概要
4.1试验时,一个钢制试环紧贴着一个钢制试块转动。转动速度为123.71m/min±0.77m/min,此速 2
NB/SH/T0203—2014
度相当于轴速800r/min±5r/min。润滑脂的温度为24℃±6℃。 4.2需要测定两个值:使旋转的试环和固定的试块之间的润滑膜破裂而引起磨损的最小负荷,即刮伤值。使旋转的试环和固定的试块之间的润滑膜不破裂而不引起磨损的最大负荷,即OK值。
5方法应用
本试验方法被广泛用来做油品规格试验,用来区分具有低、中、高不同承载能力的润滑脂。试验结果与实际使用结果之间可能不存在关联性。
6仪器
6.1梯姆肯极压试验机:详见附录B和图2、图3。 6.2试样供给装置:用于给试件提供润滑脂,详见附录B。 6.3加载装置:要求能以8.92N/s~13.33N/s.(2Ib/s~3Ib/s)的均匀速率施加和卸除加载祛码,详见附录B。 6.4试环:渗碳钢制,洛氏硬度HRC为58~62,或维氏硬度HV为653~746。试环宽度为13.06mm
±0. 05 mm,周长为 154.51 mm±0.23mm,直径为49.228第二。 最大率轻偏心率为0.013mm。 粗糙度为0.51μm~0.76μm:注:试环可由FALEX公司提供,零件号是:F-25061。 6.5试块:渗碳钢制,洛氏硬度HRC为58-62,或维氏硬度为 653~746。试快表面宽度 12.32mm±0.10mm,长为19.05mm±0.41mm,每个试块有四不试验表面,表面粗糙度为0.51μm 0.76μmc 6.6显微镜:低倍数(50倍~60倍),有足够的清晰度,且带有测微 以便测量磨痕宽度,测量精度为±0.05mm。 6.7计时器,要有“分”和“秒”刻度度量。 7 试剂与材料 7.1丙酮:符合GB/T686的要求。 7.2 清洗溶剂:符合GB1922—2006中2.号溶剂油的要求。 8.仪器的准备 8.1用清洗溶剂和丙酮依次清洗与试样接触的零部件,吹干。盖上油池出口,切断油泵, 以避免未使 8.2选一套新试件,并用清洗溶剂清洗干净,接着用洁净绸布或过滤纸擦干。在安装试件时,先用蘸有丙酮的脱脂棉擦拭干净,随后吹干。切忌用具有承载性能的溶剂(如:四氯化嵌或其它)擦拭试件,以免影响试验结果。 8.3仔细安装试验机,见图4,把试环装在主轴上,紧固试环,避免过紧而变形。按同样的要求,把加载装置的加载盘上,将加载盘上的弹簧挂在负荷杠杆末端的坡口上,要避免冲击试件。用试验脂涂抹试块和试环,慢慢用手或其他方法转动主轴几周,如果安装正确,覆盖在试环上的脂样将被涂拭
表面
注:试块可由FALEX公司提供,零件号是:F-25001。
用油泵的磨损。用润滑脂供给装置代替储油器。
试块装在试块架中。调整杠杆系统,使所有刀刃全部对准,使杠杆严格保持水平,将选定的码放在
3
NB/SH/T0203—2014
均匀。
注:建议用数字式检测器检查主轴上的试环的径向跳动,不应大于0.025mm。
单位为毫米
试环
滑动轴承
负荷杠杆
6LE
试块
摩擦力杠杆
试块架模形块定位销、
381.0
8
020 30 40 50.60 70 80 90 100
50
95.
95.3
215.9
图2 梯姆肯试验机
9试验步骤
9.1润滑脂温度控制在24℃±6℃。将润滑脂充入润滑脂供给装置,避免产生气泡,将试验脂抹在试环和试块上,在导向衬块上完全抹上润滑脂,不要加热润滑脂。 9.2.将润滑脂温度控制在在24℃±6℃,以45g/min±9g/min(0.1lb/min±0.02lb/min)的流量供到试块上。启动电机并试运转30s,如果试验设备配有加速控制系统,启动电机后均匀增加速度,15s 后达到800r/min±5r/min,再运转15s完成试运转。 9.330s试运转之后,启动计时器并以8.9N/s~13.3N/s(2Ib/s~3lb/s)的速率施加负荷。在无法估计时,提供负荷为133.4N(301bf)(建议起始负荷为133.4N(30Ibf))。负荷杠杆臂、弹簧和加载盘组件质量在负荷施加中不考虑。初始化加载程序后,如试件表面不发生刮伤,让设备以800r/min ±5r/min的转速运转10min±15s。如果在试验过程中出现噪音和振动,有明显的刮伤迹象,应立即 4
NB/SH/T02032014
单位为毫米
试环
滑动轴承
试块楔形块
6'96T
108.0
12.7
12.7
317.5 342.9
图3梯姆肯试验机(A-A)
停机,关掉润滑脂供应,并卸掉负荷。 9.4如果在负荷施加后有明显的刮伤迹象,如有异常振动、噪声等应立即停机,关闭加脂开关并卸掉负荷。因为深度刮伤产生高温,甚至会改变整个试块的表面特性,导致试块报废。值得注意的是:在这种情况下,试验机和试块过热,应避免直接接触。 9.5如果没有发生刮伤迹象,让试验机在初始负荷下运转10min±15s,在10min±15s的运转周期结束后,关闭加载装置,从负荷杠杆上卸下负荷,关闭主轴电机,使电机自然停转,关闭润滑脂出口阀,移开负荷杠杆,取出试块,观察试块表面,只要磨痕出现任何刮伤或焊着,则试样在此一级负荷下失效。
注:不能使用显微镜观察来确定刮伤的产生,但有经验的操作人员可以使用显微镜观察磨损痕迹,提供更多信息。
9.6如果不发生刮伤,翻转试块,使用其另一个接触面并选用一个新的试环,在此负荷下增加44.5N (10lbf)的负荷重复试验,如果不发生刮伤,每次增加44.5N(101bf)的负荷进行试验,直至出现刮伤为止。然后再由此负荷降低22.2N(5Ibf),进行最后的确认试验。 9.7如果在133.4N(30bf)负荷下发生刮伤,在此负荷下减少26.7N(6Ibf)进行试验,直到不出现刮伤,然后再由此负荷增加13.3N(3lbf)的负荷,进行最后的确认试验。 9.8如果某一级负荷的磨痕对于确定开始刮伤有疑问,则在此相同负荷下,重复试验。如果第二次试验产生刮伤,则这一级负荷为刮伤负荷。如果第二次试验不产生刮伤,则此负荷为不刮伤负荷。如果第二次试验仍产生疑问,不要简单地对这一负荷级做评价。可在高一级负荷下进行试验,借助高一级负荷试验结果确定有疑问一级负荷的结果。如果高一级负荷下是刮伤,则原先有疑问一级负荷也应判断为刮伤(详见附录C)。摩擦实验的操作详见附录D。
5
ICS 75.100 E 36
SH
中华人民共和国石油化工行业标准
NB/SH/T 02032014
代替SH/T0203—1992
润滑脂承载能力的测定
梯姆肯法
Standard test method for measurement of load -carrying capacity of
lubricating grease(Timkenmethod)
2014-11-01实施
2014-06-29 发布
国家能源局发布
NB/SH/T02032014
目 次
前言
范围 2 规范性引用文件 3 术语和定义 4 方法概要 5 方法应用 6 仪器 7 试剂与材料 8 仪器的准备· 9 试验步骤 10 结果计算和报告 11 精密度和偏差附录A(规范性附录)有关安全问题附录B(规范性附录)梯姆肯极压试验机附录C(规范性附录)刮伤判断明显有疑问情况下的试验程序附录D(资料性附录)摩擦试验的操作
1
3
+
8
11 12
NB/SH/T0203—2014
前言
本标准按照GB/T1.1—2009给出的规则起草。 本标准代替SH/T0203一1992《润滑脂极压性能测定法(梯姆肯试验机法)》,本标准与SH/T
0203—1992相比的主要变化如下:
将标准名称修改为“润滑脂承载能力的测定梯姆肯法”;根据GB/T17754—1999“摩擦学术语”,本标准将SH/T0203-1992中的术语“擦伤”、“擦伤值”统一修改为“刮伤”、“刮伤值”; SH/T0203一1992标准对刮伤判断:在光滑的磨痕内有刮伤或条纹产生,但未延伸到磨痕之外,这种情况认为是刮伤。本标准对刮伤判断:在光滑的磨痕内有刮伤或条纹产生,但未延伸到磨痕之外,这种情况不认为是刮伤。 本标准的OK值和刮伤值的结果报告均以N(kg)为单位;SH/T0203一1992的OK值和刮伤值的结果报告以N(Ibf)为单位;本标准的重复性为不大于平均值的23%,再现性为不大于平均值的59%;SH/T0203一1992 的重复性为不大于两个负荷级,再现性为不大于四个负荷级;增加了规范性附录A“有关安全问题”;增加了规范性附录B“梯姆肯极压试验机”;增加了规范性附录C“刮伤判断明显有疑问情况下的试验程序”;增加了资料性附录D“摩擦试验的操作”。
本标准采用重新起草法修改采用美国试验与材料协会标准ASTMD2509-03(2008)《润滑脂承载能力测定法(梯姆肯法)》。
为了更适合我国国情,在采用ASTMD2509-03(2008)时,本标准做了一些修改。本标准与 ASTMD2509-03(2008)的主要差异及其原因如下:
删除了ASTMD2509-03(2008)引用标准中没有被本标准直接引用的标准,引用了的标准采用我国相应的现行标准。 删除了ASTMD2509-03(2008)中有关对精密度说明的内容。 -删除了ASTMD2509-03(2008)中第12章“关键词”。
本标准由中国石油化工集团公司提出。 本标准由全国石油产品和润滑剂标准化技术委员会石油燃料和润滑剂分技术委员会(SAC/TC280/
SC1)归口。
本标准起草单位:中国石油天然气股份有限公司兰州润滑油研究开发中心。 本标准主要起草人:李彤、雷爱莲、谢惊春、朱文静、夏群英。 本标准所代替标准的历次版本发布情况为:
SH/T0203—1992。
I
NB/SH/T0203—2014
润滑脂承载能力的测定 梯姆肯法
警告:本标准涉及某些有危险的材料、操作和设备,但是无意对与此有关的所有安全问题都提出建议。因此,用户
在使用本标准之前应建立适当的安全和防护措施,并确定相关规章限制的适用性。详见附录A。
1范围
本标准规定了使用梯姆肯极压试验机测定润滑脂承载能力的标准方法。 本标准适用于评价润滑脂的承载能力。 注:本标准采用国际单位制【SI】单位,括号内为英制单位。
2规范性引用文件
下列文件对于本文件的应用是必不可少的。凡是注日期的引用文件,仅所注日期的版本适用于本文件。凡是不注日期的引用文件,其最新版本(包括所有的修改单)适用于本文件。
GB/T686化学试剂丙酮 GB1922—2006油漆及清洗用溶剂油 GB/T17754—1999摩擦学术语
3术语和定义
下列术语和定义适用于本文件。 3.1通用术语定义 3. 1. 1
润滑脂承载能力load-carryingcapacityofalubricatinggrease 通常指在给定的试验条件下,摩擦副正常运转时,接触表面不产生刮伤、卡咬或者金属间的表面
焊着等破坏形式的最大负荷或压力。
注:润滑脂承载能力的值是随着不同试验方法而变化的。 3. 1. 2
刮伤scoring 在摩擦表面滑动方向上形成广泛的沟槽和划痕的严重磨损形式。 注:如果润滑剂能够持续地保持,试块上则得到光滑的磨痕。当润滑膜破裂,则发生刮伤或试块的表面破坏,见图
1。最简单且最容易辨认的刮伤形式是:试块上磨痕比较宽,且有犁痕产生,金属从试块上转移到试环的接触表面上,这种表面破坏的形式经常会遇到。但是,也有如下的情况产生:磨痕表面比较光滑,但存在局部的破坏,即划痕延伸到磨痕之外,这种情况也视为刮伤。还有一种情况是:虽然在光滑的磨痕内有划痕产生,但未延伸到磨痕之外,在本方法中不认为是刮伤。
[GB/T17754—1999中5.39条] 3.1. 3
卡咬或焊着seizureorwelding 摩擦表面产生严重粘着或转移,使相对运动停止或断续停止的现象。或在摩擦学中,指直接接触
1
NB/SH/T 0203—2014
典型的OK无刮伤
安装不正确
刮伤磨痕
图1试块上的各种典型磨痕示意图
的金属表面于任何温度下形成的键合。
「GB/T17754—1999中5.42条】 3. 1. 4
磨损 wear 固体表面和其接触的物体做相对运动时,该固体接触表面的物质不断损失,产生残余变形或其它
损伤。
[GB/T17754—1999中2.4条] 3.2·专用术语定义 3. 2. 1
OK值OKvalue 在测定润滑剂承载能力过程中,没有引起刮伤或卡咬时加在负荷杠杆磁码盘上的最大质量。
3. 2. 2
刮伤值scorevalue 在测定润滑剂承载能力的过程中,出现刮伤或卡咬现象时加在负荷杠杆磁码盘上的最小质量。
4方法概要
4.1试验时,一个钢制试环紧贴着一个钢制试块转动。转动速度为123.71m/min±0.77m/min,此速 2
NB/SH/T0203—2014
度相当于轴速800r/min±5r/min。润滑脂的温度为24℃±6℃。 4.2需要测定两个值:使旋转的试环和固定的试块之间的润滑膜破裂而引起磨损的最小负荷,即刮伤值。使旋转的试环和固定的试块之间的润滑膜不破裂而不引起磨损的最大负荷,即OK值。
5方法应用
本试验方法被广泛用来做油品规格试验,用来区分具有低、中、高不同承载能力的润滑脂。试验结果与实际使用结果之间可能不存在关联性。
6仪器
6.1梯姆肯极压试验机:详见附录B和图2、图3。 6.2试样供给装置:用于给试件提供润滑脂,详见附录B。 6.3加载装置:要求能以8.92N/s~13.33N/s.(2Ib/s~3Ib/s)的均匀速率施加和卸除加载祛码,详见附录B。 6.4试环:渗碳钢制,洛氏硬度HRC为58~62,或维氏硬度HV为653~746。试环宽度为13.06mm
±0. 05 mm,周长为 154.51 mm±0.23mm,直径为49.228第二。 最大率轻偏心率为0.013mm。 粗糙度为0.51μm~0.76μm:注:试环可由FALEX公司提供,零件号是:F-25061。 6.5试块:渗碳钢制,洛氏硬度HRC为58-62,或维氏硬度为 653~746。试快表面宽度 12.32mm±0.10mm,长为19.05mm±0.41mm,每个试块有四不试验表面,表面粗糙度为0.51μm 0.76μmc 6.6显微镜:低倍数(50倍~60倍),有足够的清晰度,且带有测微 以便测量磨痕宽度,测量精度为±0.05mm。 6.7计时器,要有“分”和“秒”刻度度量。 7 试剂与材料 7.1丙酮:符合GB/T686的要求。 7.2 清洗溶剂:符合GB1922—2006中2.号溶剂油的要求。 8.仪器的准备 8.1用清洗溶剂和丙酮依次清洗与试样接触的零部件,吹干。盖上油池出口,切断油泵, 以避免未使 8.2选一套新试件,并用清洗溶剂清洗干净,接着用洁净绸布或过滤纸擦干。在安装试件时,先用蘸有丙酮的脱脂棉擦拭干净,随后吹干。切忌用具有承载性能的溶剂(如:四氯化嵌或其它)擦拭试件,以免影响试验结果。 8.3仔细安装试验机,见图4,把试环装在主轴上,紧固试环,避免过紧而变形。按同样的要求,把加载装置的加载盘上,将加载盘上的弹簧挂在负荷杠杆末端的坡口上,要避免冲击试件。用试验脂涂抹试块和试环,慢慢用手或其他方法转动主轴几周,如果安装正确,覆盖在试环上的脂样将被涂拭
表面
注:试块可由FALEX公司提供,零件号是:F-25001。
用油泵的磨损。用润滑脂供给装置代替储油器。
试块装在试块架中。调整杠杆系统,使所有刀刃全部对准,使杠杆严格保持水平,将选定的码放在
3
NB/SH/T0203—2014
均匀。
注:建议用数字式检测器检查主轴上的试环的径向跳动,不应大于0.025mm。
单位为毫米
试环
滑动轴承
负荷杠杆
6LE
试块
摩擦力杠杆
试块架模形块定位销、
381.0
8
020 30 40 50.60 70 80 90 100
50
95.
95.3
215.9
图2 梯姆肯试验机
9试验步骤
9.1润滑脂温度控制在24℃±6℃。将润滑脂充入润滑脂供给装置,避免产生气泡,将试验脂抹在试环和试块上,在导向衬块上完全抹上润滑脂,不要加热润滑脂。 9.2.将润滑脂温度控制在在24℃±6℃,以45g/min±9g/min(0.1lb/min±0.02lb/min)的流量供到试块上。启动电机并试运转30s,如果试验设备配有加速控制系统,启动电机后均匀增加速度,15s 后达到800r/min±5r/min,再运转15s完成试运转。 9.330s试运转之后,启动计时器并以8.9N/s~13.3N/s(2Ib/s~3lb/s)的速率施加负荷。在无法估计时,提供负荷为133.4N(301bf)(建议起始负荷为133.4N(30Ibf))。负荷杠杆臂、弹簧和加载盘组件质量在负荷施加中不考虑。初始化加载程序后,如试件表面不发生刮伤,让设备以800r/min ±5r/min的转速运转10min±15s。如果在试验过程中出现噪音和振动,有明显的刮伤迹象,应立即 4
NB/SH/T02032014
单位为毫米
试环
滑动轴承
试块楔形块
6'96T
108.0
12.7
12.7
317.5 342.9
图3梯姆肯试验机(A-A)
停机,关掉润滑脂供应,并卸掉负荷。 9.4如果在负荷施加后有明显的刮伤迹象,如有异常振动、噪声等应立即停机,关闭加脂开关并卸掉负荷。因为深度刮伤产生高温,甚至会改变整个试块的表面特性,导致试块报废。值得注意的是:在这种情况下,试验机和试块过热,应避免直接接触。 9.5如果没有发生刮伤迹象,让试验机在初始负荷下运转10min±15s,在10min±15s的运转周期结束后,关闭加载装置,从负荷杠杆上卸下负荷,关闭主轴电机,使电机自然停转,关闭润滑脂出口阀,移开负荷杠杆,取出试块,观察试块表面,只要磨痕出现任何刮伤或焊着,则试样在此一级负荷下失效。
注:不能使用显微镜观察来确定刮伤的产生,但有经验的操作人员可以使用显微镜观察磨损痕迹,提供更多信息。
9.6如果不发生刮伤,翻转试块,使用其另一个接触面并选用一个新的试环,在此负荷下增加44.5N (10lbf)的负荷重复试验,如果不发生刮伤,每次增加44.5N(101bf)的负荷进行试验,直至出现刮伤为止。然后再由此负荷降低22.2N(5Ibf),进行最后的确认试验。 9.7如果在133.4N(30bf)负荷下发生刮伤,在此负荷下减少26.7N(6Ibf)进行试验,直到不出现刮伤,然后再由此负荷增加13.3N(3lbf)的负荷,进行最后的确认试验。 9.8如果某一级负荷的磨痕对于确定开始刮伤有疑问,则在此相同负荷下,重复试验。如果第二次试验产生刮伤,则这一级负荷为刮伤负荷。如果第二次试验不产生刮伤,则此负荷为不刮伤负荷。如果第二次试验仍产生疑问,不要简单地对这一负荷级做评价。可在高一级负荷下进行试验,借助高一级负荷试验结果确定有疑问一级负荷的结果。如果高一级负荷下是刮伤,则原先有疑问一级负荷也应判断为刮伤(详见附录C)。摩擦实验的操作详见附录D。
5