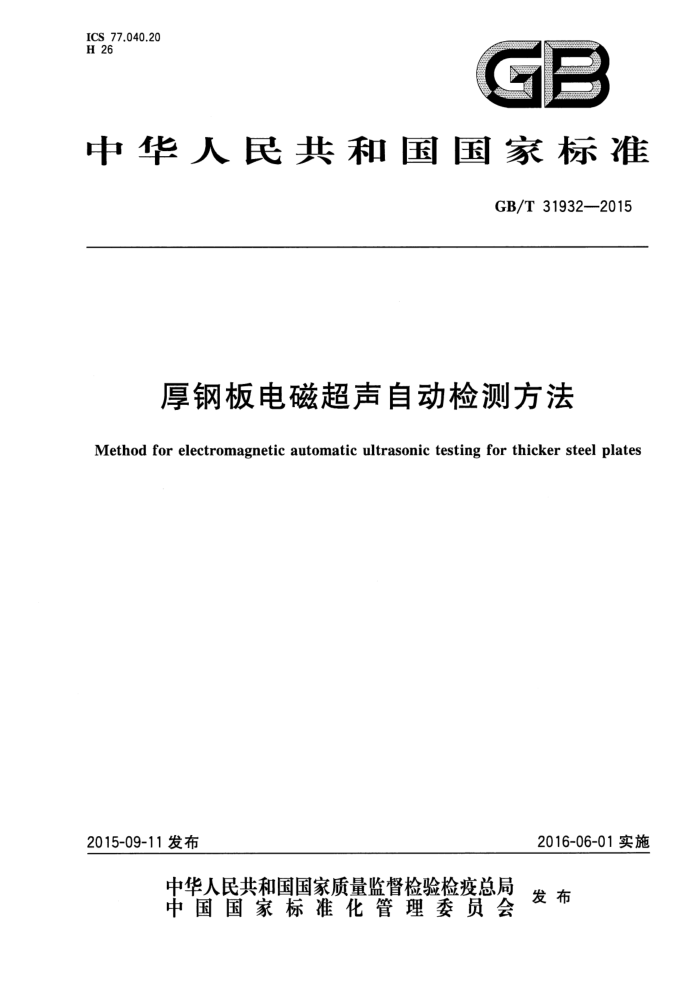
ICS 77.040.20 H 26
C
中华人民共和国国家标准
GB/T31932—2015
厚钢板电磁超声自动检测方法
Method for electromagnetic automatic ultrasonic testing for thicker steel plate
2016-06-01实施
2015-09-11发布
中华人民共和国国家质量监督检验检疫总局中国国家标准化管理委员会
发布
GB/T 31932—2015
前 言
本标准按照GB/T1.1一2009给出的规则起草。 本标准由中国钢铁工业协会提出。 本标准由全国钢标准化技术委员会(SAC/TC183)归口。 本标准主要起草单位:湖南华菱湘潭钢铁有限公司、中电科信息产业有限公司、冶金工业信息标准
研究院。
本标准主要起草人:曹志强、衰仁平、钱宏亮、董莉、陈佩英、李小莉、刘应庆、闫重强、张维旭。
I
GB/T 31932—2015
厚钢板电磁超声自动检测方法
1范围
本标准规定了厚钢板电磁超声自动检测的术语和定义、一般要求、对比试样、探伤装置、检测方法、 检测记录和缺陷的评定、钢板的质量分级、检验报告等内容。
本标准适用于厚度不小于6mm的锅炉、压力容器、桥梁、建筑、造船、管线、模具等用途钢板的电磁超声波自动检测。其他规格的钢板可参照本标准执行。
2规范性引用文件
下列文件对于本文件的应用是必不可少的。凡是注日期的引用文件,仅注日期的版本适用于本文件。凡是不注日期的引用文件,其最新版本(包括所有的修改单)适用于本文件。
GB/T2970厚钢板超声波检验方法 GB/T9445无损检测人员资格鉴定与认证 GB/T12604.1无损检测术语超声检测 GB/T20935.1金属材料电磁超声检验方法第1部分:电磁超声波换能器指南
3术语和定义
GB/T12604.1GB/T20935.1界定的定义和术语适用于本文件。
4一般要求
4.1被检板材表面应平整,不得有影响检测结果的异物。 4.2被检验钢板的尺寸、板形应满足自动探伤检验设备的要求。 4.3检验场地应避免强光、强磁场、强振动、腐蚀性气体、严重粉尘等影响电磁超声波探伤仪稳定性或检验人员可靠观察的因素。 4.4从事钢板超声自动检测的人员应按GB/T9445培训,熟悉设备性能,熟练操作计算机及超声自动检测系统和设备,并取得相关部门颁发的超声探伤专业1级及其以上资格证书。签发报告者应取得相关部门颁发的超声探伤专业2级及其以上资格证书。 4.5所采用的电磁超声波波型为横波。
5 对比试样
5.1对比试样材质、超声特性、声学性能应与被检验钢板相同或相似,并应保证内部不存在影响检验的缺陷。 5.2对比试样应具有分步检验每个换能器、每个通道的性能。 5.3对比试样应设计加工一定数量的直径为5mm、孔深为1/2对比试样板厚的平底孔缺陷。也可根
1
GB/T 31932—2015
据需要加工长50mm、宽10mm、槽深3mm的平底刻槽缺陷,或其他尺寸、形状的人工缺陷,且应避免边角发射和人工缺陷反射相互干扰。 5.4对比试样上平底孔和人工刻槽应垂直于钢板表面,且表面平滑。 5.5对比试样的制作可参考附录A进行。
6探伤装置
6.1电磁超声波自动探伤装置的组成
电磁超声波自动探伤装置由探伤系统和辅助设施组成。探伤系统至少应包括电磁超声换能器(EMAT)、探伤仪、计算机系统。辅助设施应包括辅助检测、控制系统、电气系统、机械系统、动力能源系统等设备。 6.2探伤系统 6.2.1探伤系统为系统成套产品,EMAT与探伤仪配套使用。 6.2.2EMAT每个通道具有独立的收发功能,工作频率在1MHz~10MHz之间选择,通用频率为 5 MHz 6.2.3探伤系统的性能指标:检测灵敏度5mmFBH,信噪比不小于6dB,误报率不大于2%,漏报率不大于1%,钢板头部和尾部检测盲区:剪切状态不大于50mm,未剪切状态不大于100mm;钢板边部检测盲区:剪切状态不大于12mm,未剪切状态不大于25mm,具备自动判定缺陷大小的功能。 6.3计算机系统
计算机系统探伤专用软件根据探伤仪性能、缺陷的测定、缺陷的评定、钢板的质量分级或需方的要求来编制,保证探伤结果评定准确。 6.4辅助设施
辅助设施应能保障探伤系统正常工作。
7检测方法
7.1探头扫查形式
检测时,探头可沿垂直于轧制方向扫查,也可沿平行于钢板轧制方向扫查。应保证100%扫查整张钢板表面。 7.2检测速度
电磁超声波探伤时检测速度应不超过2m/s。 7.3检测灵敏度 7.3.1电磁超声波自动探伤装置的检测灵敏度可采用电子技术校准,也可采用对比试样进行校准。 7.3.2当采用电子技术校准时,探伤系统的灵敏度由被检钢板无缺陷部位的一次底波,根据探头的大平底DGS曲线、探头的直径5mm平底孔DGS曲线或直径5mm平底孔DAC曲线进行设定,并将直径5mm平底孔的DGS曲线或DAC曲线设为报警门限。探头的DGS曲线可由探头制造商提供,DAC
2
GB/T31932—2015
曲线则应采用带有不同深度直径5mm平底孔的对比试样实际测量。 7.3.3采用对比试样进行校准时,一种方法是在对比试样无缺陷部位将第一次反射波高度调整到满刻度的50%,再提高对比试样第一次反射波与直径5mm平底孔孔波dB差(实际测量)作为检验灵敏度;另一种方法是在对比试样上的3mm平底槽的第一次反射波高度调整到满刻度的50%,再降低3mm 平底槽与直径5mm平底孔孔波dB差(实际测量)作为检验灵敏度。 7.4校准 7.4.1电磁超声波自动探伤装置应定期进行校准。 7.4.2在设备连续工作中,至少每隔8h用对比试样对检测灵敏度校准一次。若检测结果与对比试样的标准结果相比较的变化值不小于10%时,应对探伤系统进行调整,使探伤系统的性能达到规定的要求;也应对上一次校准后所检测的钢板重新进行探伤检测。
8检测记录和缺陷的评定
8.1检测记录
按照探伤系统设定的被检测单元的尺寸(长×宽)大小,被检测钢板被分为若干个被检测单元。探伤系统记录每个被检测单元的检测数据(包括:缺陷位置、深度、缺陷大小、缺陷个数),或将检测数据传输到计算机系统进行数据存储和数据处理。 8.2缺陷的边界或指示长度的测定方法 8.2.1缺陷的记录 8.2.1.1缺陷第一次反射波波高大于或等于荧光屏满刻度的50%或报警门限。 8.2.1.2当底面第一次反射波波高未达到荧光屏满刻度时,缺陷第一次反射波波高与底面第一次反射波波高之比大于或等于50%。 8.2.1.3当底面第一次反射波波高低于满刻度的50%或报警门限。 8.2.2缺陷的确定
缺陷的边界或指示长度由电磁超声波自动探伤装置自动计算,也可用人工手动方法确定。发现可疑缺陷时,可手动移动探测结果上的坐标,读出长度、宽度方向的起始坐标(X。,Y。)和终点坐标(X,, Y),利用坐标差计算指示长度(X,一X。)和指示宽度(Y一Y。)对缺陷进行确认。 8.3缺陷的评定规则
缺陷指示长度、缺陷指示面积和缺陷密集度的评定规则按GB/T2970的评定规则执行,或按需方的要求执行。
9钢板的质量分级
9.1钢板的质量分级按GB/T2970执行,或按需方的要求执行。 9.2在钢板周边50mm(板厚大于100mm时,取板厚的一半)检验区域内,单个缺陷的指示长度不得大于50mm,或按需方的要求执行。
3
GB/T 31932—2015
10 检验报告
检验报告应包含下列内容: a) 产品标准、本标准编号; b) 钢板信息:规格、牌号、炉号、编号等; c) 检验条件:探伤仪型号、探头类型、探头标准频率、对比试样等; d) 检验结果:缺陷位置、缺陷面积、钢板质量等级及其他; e) 其他:检验人员、报告签发人的姓名及资格等级、检验日期、报告签发日期等。
4
GB/T 31932—2015
附录A (资料性附录)对比试样的制作
A.1适用范围
本附录适用于检验宽度不大于4.9m、厚度不大于100mm的一般钢板的对比试样的制作。其他规格对比试样的制作可参照本附录制作。
A.2 2对比试样的制作
A.2.1 对比试样材质、超声特性、声学性能与被检验钢板相同或相似。 A.2.2 用超声波无损检测的方法进行缺陷检查,内部不允许存在直径大于1mm的缺陷。 A.2.3 对比试样的宽度4.9m,长度6.0m,厚度30mm,平整度不大于2mm/m,总平整度不大于3mm。 A.2.4 对比试样的人工(平底孔和人工刻槽)缺陷如图A.1和图A.2所示。
6 000
1 530
3 000
道
530
4
00 F(1: 1G- G(1:1) —H(1: 1)
SOR 10孔 Lo
400 中心线
DD(1: 1)
GQ(A图2)
+2
H
*x
A
RO. 4孔 45 +0. 1
U
啤翔
司
文 Z SDf fD
NN 田优 WIA
00S009
7
玉玉
RO. 1
T
EE(1: 1) 4%45+0.
-
正 T
T WIA
00S DO
M
TE TE
5
RRe
TDF TD
M
4±(1:2)
5
ET TET 000 1
A
45
H
22
TD
石T
2
000 T Df TD
00S 44 T 00S
1
U
10x45-L(1:5)R76. 3
A
一
子
400
两边
sL400
T (4图2)
B
中
nF
Kod
FF
2265
C—C(1:1)2 处5孔
$30
B(1: 5)
3
15015015050
注:L-开槽位置坐标:距中心线40mm,距上端400mm。
图A.1
5
GB/T 31932—2015
Q (1:1) (A图2) 2处
J (1:1) (4图2) 2处
双 双效
中
效
人 400 k
H
K—K (1 :1) 5 +0.1
R _05 +0, 1 hl
@5 +0. 1 52孔
05 +0, 1 52孔
52孔_5+0.1
52孔
a
51
RO.
R—R (1:1) 85 +0. 52孔g
@5+0, 51孔
$5 +0. 1
@5 +0.
52孔 52孔
52丑5+0.
5
0
化
RO.
图A.2
A.2.5对比试样上平底孔和人工刻槽侧表面垂直于钢板表面,非垂直度最大0.1mm。 A.2.6对比试样上平底孔和人工刻槽的表面平滑,表面粗糙度Ra为3.2μm。 A.2.7对比试样上平底孔的累计孔距误差小于士1mm。
6