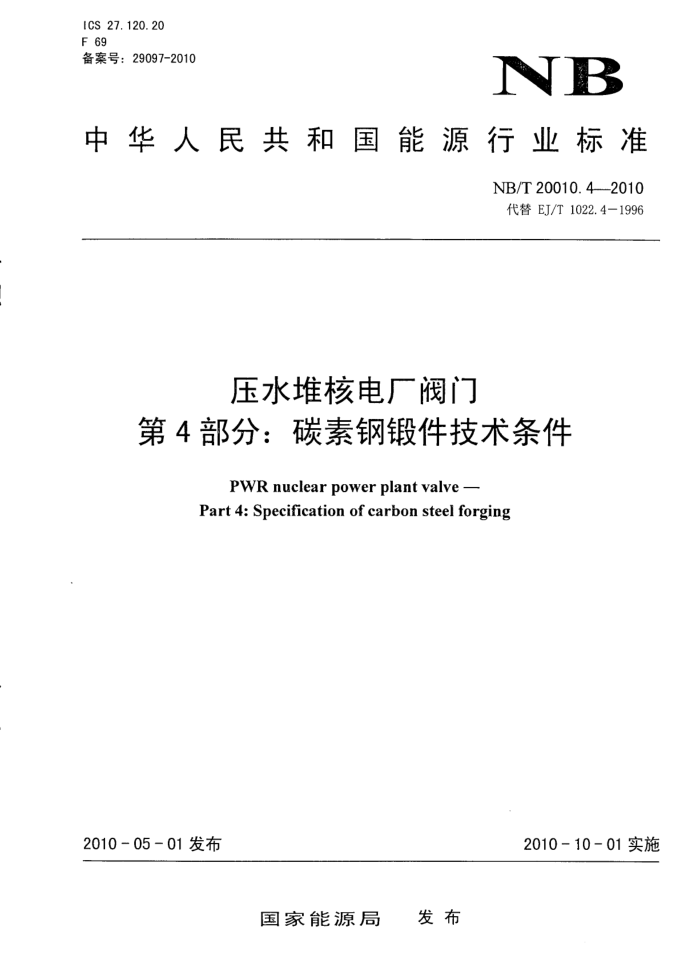
ICS 27.120.20 F 69 备案号:29097-2010
NB
中华人民共和国能源行业标准
NB/T 20010.4-2010 代替EJ/T1022.4-1996
压水堆核电厂阀门
第4部分:碳素钢锻件技术条件
PWR nuclear power plant valve - Part 4: Specification of carbon steel forging
2010-05-01发布
2010-10-01实施
发布
国家能源局
NB/T20010.42010
目 次
前言
II
范围 2 规范性引用文件 3 锻造用钢
1
牌号和化学成分 5 制造 6 力学性能, 7 无损检验. 8 金相检验,
4
8
9
试料保管 10 缺陷部位清除和整修 11 尺寸检查 12 标志 13 质量证明书 14 验收 15 清洁、包装、运输
9
1
10 10 10 10 11 11
NB/T20010.4—2010
前言
NB/T20010《压水堆核电厂阀门》分为15个部分:
第1部分:设计制造通则;第2部分:碳素钢铸件技术条件;第3部分:不锈钢铸件技术条件;第4部分:碳素钢锻件技术条件;第5部分:奥氏体不锈钢锻件技术条件;第6部分:紧固件技术条件:第7部分:包装、运输和贮存;第8部分:安装和维修技术条件;第9部分:产品出厂检查与试验;第10部分:应力分析和抗震分析:第11部分:电动装置;第12部分:气动装置:第13部分:核用非核级阀门技术条件;第14部分:柔性石墨填料技术条件;第15部分:柔性石墨金属缠绕垫片技术条件。
本部分为NB/T20010的第4部分。 本部分按照GB/T1.1一2009给出的规则起草。 本部分代替EJ/T1022.41996《压水堆核电厂阀门碳素钢和低合金钢锻件技术条件》,与EJ/T
1022.4-1996相比主要有以下变化:
增加了关于日视检验、液体渗透检验、磁粉检验和超声检验的引用标准和具体要求;增加牌号“P280GH”锻件的化学成分和力学性能的具体要求;第7章“缺陷检验”改为“无损检验”并增加无损检验人员的资格要求;补充第8章“金相检验”的具体要求。
本部分由核I业标准化研究所归口。 本部分起草单位:上海核工程研究设计院、大连大高阀门有限公司、上海阀门厂有限公司。 本部分主要起草人:乐秀辉、郎咸东、高连元、盛燮康。 EJ/T1022.4于1996年4月首次发布。
II
NB/T20010.42010
压水堆核电厂阀门
第4部分:碳素钢锻件技术条件
1范围
本部分规定了压水堆核电厂核安全相关阀门用碳素钢承压锻件(以下简称“锻件”)的技术要求。 本部分适用于压水堆核电厂2、3级阀门用锻件(阀体、阀盖、阀瓣等)。 核用非核级阀门用锻件也可参照使用。 本部分不适用于阀杆和紧固件。
2规范性引用文件
下列文件对于本文件的应用是必不可少的。凡是注日期的引用文件,仅所注日期的版本适用于本文件。凡是不注日期的引用文件,其最新版本(包括所有的修改单)适用于本文件。
GB/T223(所有部分)钢铁及合金化学分析法 GB/T228-2002金属材料室温拉伸试验方法(ISO6892:1998,MOD) GB/T229—2007金属材料夏比摆锤冲击试验方法(IS0148—1:2006,MOD) GB/T231.1金属布氏硬度试验第1部分:试验方法(GB/T231.1—2002,IS06506-1:1999,MOD) GB/T4338—2006金属材料高温拉伸试验方法(GB/T4338—2006,ISO783:1999,MOD) GB/T6394金属平均晶粒度测定方法(GB/T6394-2002,ASTME112:1996,MOD) GB/T10561 钢中非金属夹杂物含量的测定标准评级图显微检验法(GB/T10561--2005,IS04967:
1998,IDT)
GB/T 20066 钢和铁化学成分测定用试样的取样和制样方法(GB/T20066-2006,IS014284: 1996,IDT)
NB/T20003(所有部分) 核电广核岛机械设备无损检测 ASTMA105/A105M—2001管道元件用碳钢锻件(Specificationforcarbonsteelforgingsfor
piping applications)
ASTMA388/A388M大型钢锻件超声检验的标准操作方法(Standardpracticeforultrasonic examination of heavy steel forgings)
ASTME165液体渗透检验方法(Standardtestmethodfor1iquidpenetrantexamination) ASTME709磁粉检验导则(Guideformagneticparticletesting)
3锻造用钢 3.1钅 锻造用钢应采用电弧炉治炼,也可用其他相当的冶炼方法冶炼。 3.2阀门锻件也可采用钢厂提供的锻棒锻造,
4牌号和化学成分
4.1规定的牌号和化学成分
牌号和化学成分应符合表1的规定。 4.2化学成分检验 4.2.1熔炼分析
1
NB/T20010.4—2010
冶炼单位应对每炉或每包钢水进行化学分析,分析试样应从浇注过程中提取。分析结果应符合表1 的规定。当订货合同对A105M锻件熔炼炉次化学成分分析有要求时,应按订货合同及设备技术规格书的规定,并将分析结果报送需方或其代表。 4.2.2成品分析
应对锻件成品取样进行化学分析。当锻件重量大于500kg时,每件进行取样分析。当锻件重量等于或小于500kg时,按炉号对其中的一件进行取样分析。化学成分测定用试样的取样和制样方法按GB/T 20066的规定或取自力学性能试验用残余试样。对于A105M锻件成品化学成分允许偏差可按ASTM A105/A105M一2001表2的规定。成品分析结果应符合表1的规定。 4.2.3化学成分分析方法
化学成分分析方法按GB/T223的有关规定进行。
表1 化学成分
单位为%
牌号
化学元紫
P280GHa
20HD* 熔炼分析 成品分析 熔炼分析 成品分析 熔炼分析 成品分析 成品分析
A105M d
16MnHDa
≤0.22 ≤0.40
≤0.20 0.10~0.35 0.10~0.40 0.10~0.35
C ≤0. 18 ≤0.20 ≤0.20
≤0.22
≤0.35
主 Si ≤0. 30 ≤0.35 ≤0.35 要
0.8~1.50 0.801.50 0.80~1.60 0.80~1.60 0.60~1.05
元 Mn ≥0.60 ≥0.60 素 S ≤ 0.030 ≤0.035 ≤0.030 ≤0.035
≤0.015 ≤0.020
≤0.020 ≤0.025 ≤0.25 ≤0.50 ≤0.25 ≤0.10
≤0.040 ≤0.035 ≤0.40 ≤0.40 ≤0.30 ≤0.12 ≤0.05 ≤0.02
P ≤ 0.035 ≤0.040 ≤0.035 ≤ 0.040
0.18 ≤0.18 ≤0.25 ≤0.50 ≤0.50
Cu Ni ≤0.50 Cr
≤0.50 ≤0.25 ≤0.10
≤0.50
-
≤0.25 ≤0. 10 ≤0.05 ≤0.40
≤0.25 ≤0.10 ≤0.05 ≤0.40
残余 Mo 元紫
-
X
-
:
Nb Sn A1
-
-
1
≤0.030
≤0.030 0.02~0.05 0.02~0.05
1
-
对20HD和16MnHD白由锻锻件,熔炼分析和成品分析时Cu+6Sn≤0.33%。对20HD和16MnHD模锻件,熔炼分析和成品分析时Ni≤0.30%。 对于P280GH锻件,碳当量CE≤0.48。对用于给水流量控制系统的P280GH锻件,钢中的Cr含量应≥0.15%。 5对于A105M锻件允许的最大含碳量每下降0.01%,最大含锰量可增加0.06%,直至最大含量达1.35%时为止。残余元素Cu、Ni、Cr及Mo含量总和不应超过1.00%,其中Cr及Mo元紫含量总和不应超过0.32%。 对于A105M锻件,如订货合同中要求碳当量时,碳当量按CE=C+Mn/6+(Cr+Mo+V)/5+(Ni+Cu)/15计算。当最大截面厚度不大于50mm时,CE≤0.47;大于50mm时,CE≤0.48。
5制造
5.1制造程序
2
NB/T 20010.4—2010
5.1.1对于交货重量大于250kg的20HD、16MnHD、A105M锻件和所有重量的P280GH锻件,锻造厂在开始制造前应制定包括下列内容的制造程序:
a)钢的冶炼工艺; b) 所使用钢锭的重量和类型 c) 钢锭头尾切除百分率; d) 锻件在钢锭上的位置:
标注尺寸的锻造坏件图、经每一火次锻造后的锻件图。图中应标有每一火次锻造比和总锻造比; f) 热处理时的外形图、无损检验时的外形图和交货件的外形图; g) 成品的中间热处理和最终热处理方式; h) 验收试验用试料在锻件上的位置: i) 在试料上截取试样的平面图。
e)
5.1.2 锻造厂在开始制造前,应按制造先后顺序,用图或表格形式列出冶炼、锻造、机加工、热处理、 试料截取和无损检验的各个操作过程。 5.1.3若无特殊规定,对于交货重量小于250kg的20HD、16MnHD、A105M锻件,制造程序可只包括上面f)、g)、h)、i)四项和5.1.2的各个操作过程。但对于首次进行核安全相关阀门用锻件生产的制造厂,在开始制造前,仍应按5.1.1和5.1.2的规定执行。 5.1.4上述制造程序应通过验证和评定。可采用制造样件或以第一个产品锻件作为验证件进行验证和评定。 5.1.5在制造过程中,若改变5.1.1和5.1.2中的任何一项程序时,应对这一改变可能造成的后果作出评定,并进行必要的补充验证试验或对整个制造程序重新验证和评定。 5.2锻造 5.2.1锻造使用的钢锭或锻棒应有熔炼单位的质量证明书。 5.2.2锻件用钢锭锻造时,每个钢锭头尾应有足够的切除量,以确保锻件无缩孔及严重偏析等缺陷。 5.2.3锻件应在压机、锻锤或轧机上经受热机械成形。这些设备都应具有足够的能力,以使整个截面上的金属锻透。 5.2.4当采用钢锭锻造时,锻件的总锻造比不得小于3。当采用锻棒锻造时,按主截面计算锻造比不得小于1.6,其总锻造比不得小于3。 5.2.5在锻造过程中,应确保锻件在终锻后通过相变温度范围时缓慢冷却。 5.2.6锻件最终成形后,应使其冷却到500℃以下才能进行规定的热处理。 5.3机加工 5.3.1锻件成品热处理前,还件的外形应尽可能加工成接近交货件的外形。 5.3.2锻件成品热处理后,最终无损检验前,锻件应按交货件外形图及无损检验对表面粗糙度的要求进行机加工。 5.3.3锻件成品在机加工时发现锻造缺陷,该锻件应予报废。 5.4交货状态 5.4.1锻件(除P280GH锻件外)交货时热处理状态按下述规定:
a)厚度≤80mm的20HD、16MnHD和A105M锻件以正火热处理状态交货; b) 20HD、16MnHD锻件的热处理温度为850℃~950℃;A105M锻件的热处温度为843℃~927℃
保温后空冷; c) 厚度>80mm的20HD、16MnHD锻件以淬火加回火状态交货,回火温度应不低于600℃; d) 如需其他热处理状态交货时,应在设备技术规格书中另行规定。
5.4.2P280GH锻件交货时热处理状态按下述规定:
a) 当锻件厚度≤80mm时,以正火热处理状态交货。热处理温度为890℃~940℃,保温时间为
1min/mm,至少保温30min。冷却方法:静止空冷; b) 当锻件厚度>80mm时,以淬火+回火热处理状态交货。热处理温度为890℃~940℃,保温时间
为1min/mm,至少保温30min。冷却方法:水。回火温度不低于620℃。
3
NB/T20010.42010
5.4.3热处理炉内应至少有一根热电偶置于炉料中心的某一零件上,使其能精确地指示这一部位的温度。在保温期间,温度偏离规定的允许偏差为土15℃。
全部热处理过程应予记录,并列入热处理报告中。
6力学性能
6.1性能指标
锻件经交货状态热处理后的力学性能应符合表3的规定。 6.2取样规定 6.2.1力学性能试料应取自锻件的加长或加厚部分,该部分在截取前应始终与锻件相连,并同时经受锻造和热处理。 6.2.2模锻件的力学性能试料可取自能代表产品锻件的单独试块锻件上。但试块锻件应与产品锻件为同一熔炼炉次的材料,并与产品锻件有相同的锻造比、锻造工艺及公称厚度。试料锻件还应与产品锻件同炉热处理。 6.2.3试样截取后需作适当标记。 6.2.4试料应有足够大的尺寸,以便截取作规定的试验和可能进行重复试验所需的试样。 6.2.5A105M锻件在试料上截取试样时,按下列规定:
a) 圆柱形、圆筒形和圆饼形等自由锻锻件,应尽可能按切向取样,其他形状的锻件按横向取样: b) 当锻件厚度(或壁厚)等于或大于50mm时,应使试样的轴线到最近表面的距离至少等于25mm,
试样有效部位离其他表面的距离至少等于50mm;当锻件厚度(或壁厚)小于50mm时,应使试样的轴线到最近表面的距离为二分之一厚度。试样有效部位离其他表面的距离至少等于锻件厚度;若锻件的形状不许可,则应尽可能接近这些数值;
c) 冲击试样的缺口轴线应与主要锻造表面垂直。 6.2.620HD、16MnHD锻件的取样要求包括:
a)取样方向:
1) 自由锻锻件:如果锻件为环向,拉伸试样利冲击试样的轴线方向与锻造主方向平行(纵向
试样),即在切向截取。对其他形状的锻件,试样的轴线方向与锻造主方向垂直(横向试样): 2) 模锻件:根据锻件的实际情况,拉伸试样可截取纵向试样或横向试样中的一种;冲击试样
为纵向试样;
3)在自由锻锻件利模锻件上截取的冲击试样的缺口底线均应垂直于锻件表面。 b)试样的位置:
1)当锻件的形状允许,试样轴线距热处理表面的距离为:
(1)厚度e≤60mm的锻件,为e/2: (2)厚度e>60mm的锻件,至少为30mm(模锻件至少为20mm)。
2) 在其他方向,试样的有用部分与其他热处理表面的距离至少为:
(1)厚度e≤60mm的锻件,为e; (2)厚度e>60mm的锻件,至少为60mm(模锻件至少为40mm)。
3)如果锻件的厚度不允许,则应尽可能接近这些数值。
6.2.7P280GH锻件的取样要求包括:
a) 在锻件形状允许的范围内,截取的试样轴线应垂直于主锻造方向,且轴线与最近热处理表面的
距离为: 1)若锻件厚度e>40mm,则为20mm; 2)若锻件厚度e≤40mm,则为e/2。
b) 试样的试验有用部分到其他热处理表面的距离应不低于:
1)若锻件厚度e>40mm,则为40mm; 2)若锻件厚度e≤40mm,则为e。
6.3试验项目及数量 4
NB/T20010.42010
6.3.1交货状态的试料试验
试料从交货状态锻件或试块锻件上截取后,不再补充任何其他热处理即制成试样进行试验。对于交货重最大于250kg的锻件,应每件取一组试样进行试验。对于其他锻件,则按6.4的规定组成批,每批锻件取一组试样进行试验。每一组试样的试验项目及数量按表2的规定。
表2试验项目及数量
试验数量
试验温度室温 300℃ 0℃ 室温
试验项目拉伸试验高温拉仲试验冲击试验硬度试验
1 1 3 1
*当设备技术规格书中有要求时,进行高温拉仲试验。 b对给水流量控制系统用P280GH锻件的冲击试验温度应在-20℃进行。 °P280GH锻件可不进行硬度试验。
6.3.2模拟消除应力热处理后的试料试验 6.3.2.1如订货方要求,并在订货合同中注明要保证锻件在模拟消除应力热处理后的力学性能时,则需将从交货状态锻件或试块锻件上截取的试料进行模拟消除应力热处理后,再制成试样进行试验。模拟消除应力热处理应考虑锻件在制造过程中将要经受的所有热处理。 6.3.2.2订货时,需方应将这些热处理的方式及详细要求提供给锻造厂,并写入订货合同中。在锻造厂制定的制造程序中应列出模拟消除应力热处理的方式,尤其应注明400℃以上的加热速度及冷却速度、保温温度及保温时间。在温度超过400℃时的加热和冷却速率应符合以下规定:
当锻件的壁厚e≤25mm时,不超过220℃/h;当锻件的壁厚e>25mm时,不超过按下式计算的结果或55℃/h中的较大值: 220 ×25℃/h
e
6.3.2.3保温温度的精确度为土5℃。对P280GH锻件的保温温度为605℃,保温时间按焊接端厚度每毫米保温6min计算,但不得少于2h。其他锻件的保温时间应在订货合同中作出规定。保温时间应大于制造过程中实际热处理累计保温时间的80%,保温时间中应包括在制造过程中可能出现变故而增加的补充热处理时间。 6.3.2.4试样的截取条件、试验项目及数量同6.3.1的规定。试验结果应符合表3的规定。 6.4批的定义
批是由尺寸比较接近的一些锻件组成。例如:=mx≤1.1; ≤1.1;≤1.25;(e为锻件
min
S min
emin
厚度;Φ为锻件直径;S为锻件截面积)。
同一批锻件应来自同一熔炼炉次,并经受相同的制造过程和进行同一炉热处理。每批重量应不超过 3000kg. 6.5试验方法 6.5.1室温拉伸试验 6.5.1.1试样采用GB/T228—2002中直径10mm的圆形横截面比例试样。 6.5.1.2试验方法按GB/T228—2002的规定。 6.5.1.3对P280GH锻件,还应记录断后收缩率A(%)和断面收缩率Z(%)作为资料提供。
5