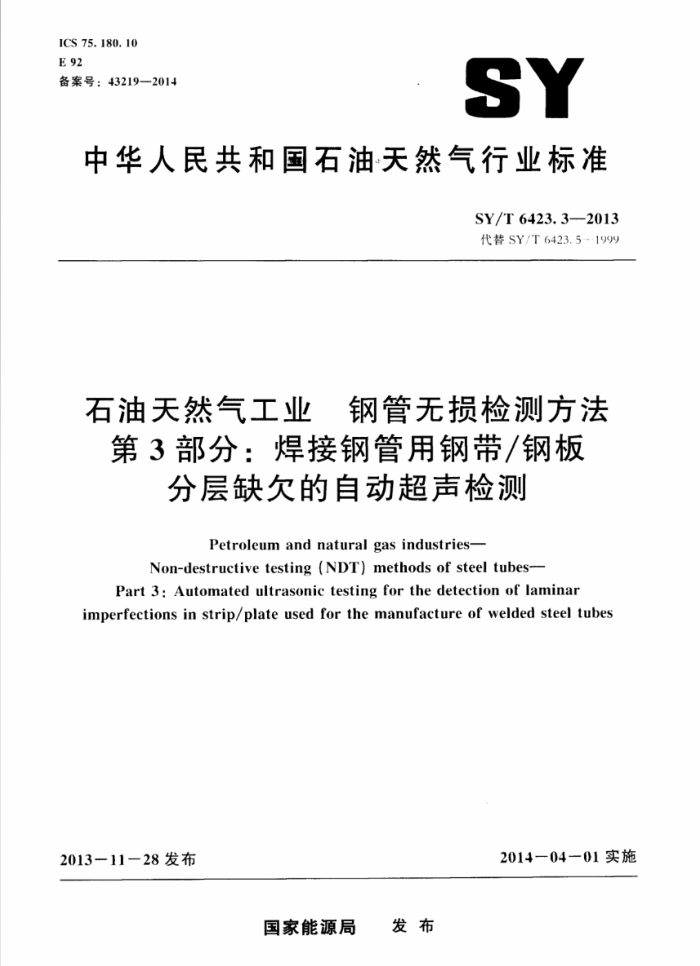
ICS 75.180.10 E 92 备案号:432192014
SY
中华人民共和国石油天然气行业标准
SY/T6423.3-2013 代替SY/T6423.5--·1999
石油天然气工业 钢管无损检测方法第3部分:焊接钢管用钢带/钢板
分层缺欠的自动超声检测
Petroleum and natural gas industries-
Non-destructive testing (NDT) methods of steel tubes-
Part 3 : Automated ultrasonic testing for the detection of laminar
imperfections in strip/plate used for the manufacture of welded steel tubes
2014-04-01实施
2013-11—28发布
国家能源局 发布
SY/T6423.3—2013
目 次
前言
范围 2 规范性引用文件 3 术语和定义 总要求 5 检测方法 6 对比试块 6. 1 总则 6.2 对比标样的尺寸 6.3对比标样的验证
设备校准和校验 H 验收
7
检测报告附录A(规范性附录)确定分层缺欠尺寸的手动超声波检测程序附录NA(资料性附录)SYT6423—1999各部分名称及其采标情况
SY/T 6423.3—2013
前言
SYT423《石油天然气T业钢管无损检测方法》分为以下几部分:
第1部分:焊接钢管焊缝缺欠的射线检测:第2部分:焊接钢管焊缝纵向和/或横向缺久的自动超声检测:第3部分:焊接钢管用钢带/钢板分层缺久的自动超声检测:第部分:无缝和焊接钢管分层缺欠的自动超声检测:第5部分:焊接钢管焊缝缺欠的数字射线检测:
-·第6部分:无缝和焊接(埋弧焊除外)铁磁性钢管纵向和。或横向缺欠的全周自动漏磁检测:
本部分为SY/T(23的第3部分。 本部分按照GB/T1.1-·-20《标准化工作导则第1部分:标准的结构和编写》给出的规则
起草:
本部分代替SY/T(23.5-19州石油天然气T业承压钢管无损检测方法焊接钢管制造用钢带,钢板分层缺欠的超声波检测,与SY/T6423.5--1999相比。除编辑性修改外,主要技术变化如下:
修改广范围。增加了“本部分也适用于圆形空心部件制造用钢带/钢板的检测”:
增加了规范性引用文件SY/T623.4.GB/T12604.1及1S01148:增加了第3章“术语和定义”一章;在第章总则中增加了对撑作人员检验过程的监督,以及3级人员对NDT检测授权的要求:在5.中增加了相控阵技术,并对晶片要求进行广修改。
本部分使用翻译法等同采用IS0)111893-9:2011钢管无损检测焊接钢管用钢带/钢板分层缺久的自动超声检测。
本部分对1S0)140893-9:2011的主要编辑性修改如下:修改了标准名称::-增加了规范性引用文件SY/T623.4 -增加了资料性附录NA.方便使用者了解所代替标准SYT623--1的情况。 请注意本文件的某些内容可能涉及专利。本文件的发布机构不承担识别这些专利的责任,车部分由石油管材专业标准化技术委员会提出并归口。 本部分起草单位:宝石油钢管有限责任公司(国家石油天然气管材工程技术研究中心)、中国
油集团石油管广程技术研究院。
本部分主要起草人:胡剑、付宏强、王慧、薛幕红、张锦刚、西民。
II
SY/T6423.3-2013
石油天然气工业 钢管无损检测方法
第3部分:焊接钢管用钢带/钢板分层缺欠的自动超声检测
1范围
SY/T6423的本部分规定了焊接钢管制造用铜带/钢板在生产钢管之前或生产过程中在制管厂完成的分层缺欠的自动超声检测要求。
注1:对于焊接钢管。由制造商选择,可在焊接之后按照SY/T623.4对分层缺欠进行相应的钢管超声检测作为
替代方法,
注2:由购方与制造商协议。本部分可适用于埋弧焊钢管焊接后的钢带/钢板的检测,本部分也适用于圆形空心部件制造用钢带/钢板的检测。
2规范性引用文件
下列文件对于本文件的应用是必不可少的。凡是注日期的引用文件,仅注日期的版本适用于本文件。凡是不注日期的引用文件。其最新版本(包括所有的修改单)适用于本文件。
GB/T0445无损检测人员资格鉴定与认证(GB/T9445--20M18.ISO9712:2005.IDT) GB/T12604.1无损检测术语超声检测(GB/T12604.1-2005,IS5577:2000.IDT) SY/T6423.石油天然气T业钢管无损检测方法第4部分:无缝和焊接钢管分层缺久的自
动超声检测(SY/T6423.—2013.IS)10893-8:2011,IDT)
IS0 11484 钢产品雇主对无损检测人员的资质认证体系[Steelproducts·Employer"s qualification system for non- destructive testing (NDT) personnelj
3术语和定义
GB/T12604.1和IS11484界定的以及下列术语和定义适用于本文件。
3. 1
对比标样 reference standard 用于校准无损检测设备的标样(即通孔。刻槽、凹槽等人工缺陷)
3. 2
对比(参考)试块referencesample 包含对比标样的试块(即钢板/钢带块)。
3. 3
钢管steel tube 任一横切断面的两端皆有开口的空心长条钢质产品。
3. 4
焊接钢管 Fwelded tube 将板/带材成型为空心轮廓,并将相邻边缘焊接在一起制成的钢管。随后可进行热加工或冷加工,
以获得量终尺寸。
SY/T 6423.32013
3. 5
制造商manufacturer 根据相关标准生产制造产品。月声明交付的所有产品符合相关标准的相应要求的组织
3. 6
协议agreement 在询间和签订合同时,制造商与购方达成的契约文件。
3. 7
分屋缺欠laminarimperfection 钢板或钢带中的缺欠,通常平行于钢板或钢带表面。 注:通过测量外表而的轮哪面积计算缺欠范围。
总要求
1.1应在钢管生产前或生产过程中对展平的钢带/钢板进行超声检测。 4.2待检钢带/钢板表面应平整且无异物,以确保检测的有效性。 .3本检测应由按照(iB/T9445及ISO)11484或等效标准培训.且评定合格的有资质操作人员进行。并出制造商指派具有相应能力的人员对检测进行监督。第一方检测时。购方与制造商应对此进行协商,
制造商应按照书面程序发出检测(操作)授权。NDT检测应由制造商批准的3级NDT人员授权。
注:可在GHT9445和ISO11484等相关标准中找到1级,2级、3级人员的定义。
5检测方法
5.1应采用超声脉冲回波技术对钢带,钢板的分层缺欠进行检测:超声波束以垂直于钢带/钢板表面发射:或由制造商选择使用超声穿透法进行检测。 5.2在检测过程中,钢带/钢板与探头装置之间应相对移动,沿平行或垂直于钢带/钢板轧制方向的等间距扫查线对钢带/钢板表面进行扫查。扫查的最小覆盖范围和相邻扫查轨迹之间的最大允许间距成符舍表1的规超。对于摆动扫查技术:其最小接盖范围应为表1规定数值的一半。检测过程中,相对移动建度波动不应大于土10% 5.3为检测表2规定的相应的最小缺欠长度Lmim,应对钢带/钢板纵向边缘宽度至少为15mm的范用进行10%的超声分层缺欠检测(适用时还应加上焊接前原始钢带/钢板要切除边缘的总宽度)。
确定可疑分层区域的范围:当两个相邻可区域的间距小于两个可疑区域的较小辅向民寸的较小
值时。应将这两个可疑区域视为一个分层区域。
注:织向边缘被定义为平行于轧制方向的边缘 5.任一方向上每个探头推荐最大宽度,或采用相控阵技术时每个有效直径宜为25mm。但是.只要这些品片能够检测所采用的对比标样,制造商可使用较大的晶片:有要求时,这种检测能力应经过证实
对于晶片装置内装有不同尺寸晶片的双晶探头·应使用最小晶片的尺寸计算覆盖范用 5.5借助白动触发/报警门限并结合标识和/或分选系统,白动检测设备应能区分合格钢带:钢板或可键钢带,钢板
"
SY/T 6423.3—2013
表1验收等级和钢带/钢板的最小覆盖范围以及相邻扫查轨迹间的最大间距
相邻扫查轨连间的最大间距
最小覆盖范围
验收等级
% 211 10 L
mm 1) 150 2400
U1 U2 U3
表2验收等级和钢带/钢板边缘所能检测到最小分层缺欠及可接受的最大分层缺欠
可接受的最大分层缺欠尺寸
应考虑的单个分层缺欠的最小尺寸长度
单个尺寸面积(长度与宽度的乘积》 铜板边缘每米长度范围内分层缺
当L且≤E时,钢带
验收等级
长度 L max mm 2 40 60
Lmin mm
Emax mm* 251 5H1 THHE
欠的最大数量
U1 U2 U3 :仅应考虑宽度(C.)超过6mm的分层缺欠。
10 24 341
3 4
6对比试块
6.1总则 6.1.1 本部分规定的对比标样是方便校准无损检测设备的标样(人工缺陷)。这些对比标样的人工缺陷尺寸不宜理解为该设备所能检测到的最小缺欠尺寸。 6.1.2超声波设备应采用平对比试块[见7.1a)进行底波回波高度法,或者采用带平底孔正方形或矩形刻槽的平对比试块「见7.1b)进行校准,采用机加工方法在平板对比试块表面加T平底孔,正方形或矩形刻槽(见图1)。
带平底孔的对比标样应作为确定检测灵敏度的主要方法。当采用其他类型的对比标样时。应调整检测灵教度,使之与采用平底孔对比标样时获得的检测灵敏度相当。
对于超声波穿透法,应在刻槽内填满合适的衰减材料,或者在试样表面上附加与对比标样具有相同尺寸的合适衰诚材料。 6.1.3应采用机加工、电火花蚀刻或者其他适宜的方法获得对比刻槽。
注:刻槽底部或底部棱角可为圆角。 6.1.4对比试块应与待检钢带/钢板具有相似的表面状态和声学性能(如声速。衰减系数)。校准用对比试块的长度和宽度应由制造商视方便情况选择。 6.2对比标样的尺寸
对比标样的刻槽尺寸应符合下列规定(见图1)。
宽度w*6*""mm.
a
b 深度d:T/4
长度l:≥6mm.最大为25mm
3
SY/T6423.3-2013
6.3对比标样的验证
应采用适当技术验证标样的尺寸和形状。
说明: rl 刻槽深度: 1
刻槽长度:
T- 公称厚度:
情宽度或直径。
L"
图1对比标样的刻槽形式
7 设备校准和校验
7.1每一检验周期开始前。应按照7.1a》的规定不采用对比标样或按照7.1b)的规定采用对比标样对设备进行静态校验。
不采用对比标样校验:将探头装置定位于待检钢带/钢板上,第一次底面回波满波幅减去 6dB作为设定设备的触发/报警门限,也可采用探头制造商提供的DAC(距离幅度修正)曲线:或者采用钢管或钢带/钢板制造商使用的DA曲线确定检测灵敏度,在这两种情况下,均应使用6mm的平底孔曲线。 在设定的灵敏度下,制造商应证实设备在静态下能够检测出6.1.2和图1中规定的对比标样的刻槽。如不能检测出,则在生产检测前应调整灵敏度。
b) 采用对比标样的校验:在静态条件下,当操头或中心支架上的每个探头对准对比标样上的
刻槽时,所产生的满幅信号应作为设定设备的触发/报警门限。
7.2在钢带/钢板生产检测过程中,应选择相对平移速度以及设备脉冲重复频率。使得能够达到表1 规定的相应最小覆盖范围和相邻扫查轨迹间的最大间距。 7.3在钢带,钢板的生产检测过程中,应定期校验设备的校准状态。
校验频次应每4h至少1次,但当设备操作员换班以及生产开始和结束时也应进行校验 7.→初次校验后。如果任一参数发生变化时,应重新校验设备。 7.5在生产检测校验过程中,如发现设备不满足校准要求,甚至考虑到系统漂移的情况,将灵缴度提高3dl3仍不满足校准要求时。则在设备重新校准后应对上次校验后检测的所有钢带/钢板重新进行复验。
-
SY/T 6423.3—2013
8验收
8.1未产生触发/报警门限信号的钢带/钢板应认为已通过该项检测。 8.2任何发出大于或等于触发/报警门限信号的钢带/钢板成视为可疑钢带/钢板。或由制造商选择。 可重新进行检测。如果两次连续复验的信号全部低于触发/报警门限,应将该钢带钢板视为通过该项检测:否则:应将该钢带/钢板标记为可疑钢带/钢板。
注:如适用,可根据DAC曲线进行评价。 8.3 根据产品标准要求。可疑钢带/钢板应按照下列一种或儿种方法处置:
a) 应采用手动超声纵波方法按照附录A的规定对可疑区域进行扫查,以确定分层缺欠的范围。
如果分层缺欠的尺寸和出现额次没有超过表2和表3规定的数值。则成认为通过该项检测。 如果分层缺久的宽度(超过须考虑的最小宽度((见表3注)。应以指示为中心对周围 500mm×500mm的区域进行10%扫查,以确定存在的超过B的其他分层缺欠,确定大于B但小于B的分层缺欠面积之和是否超过表3的允许值。如果检测出超过须考虑的最小宽度的另外一个分层缺欠时,则应以新的超声波指示为中心,对周用50mm×50mm的区域进行扫查以确定可疑分层区域的范围。当相邻可疑区域的间距小于可疑区域的两个较小轴向尺寸中的较小值时,应将这两个可疑区域规为一个分层区域。
by 应切除可疑区域。 c) 应认为钢带/钢板检测不合格。
表3 验收等级,钢带/钢板中检测到的最小分层缺欠尺寸和最大允许分层缺欠尺寸
啦考虑的单个最小分层
分层缺大的量大可接受面机
缺欠尽寸
单个分层面视的累加值(
与铜带钢板面积的百分比
最小宽度 . mm
验收等级 单个面租
单个面积 H... mm
B.. mm
带钢板长度范用内任意米
削带/钢板长度范围内平均米
最大 11. 5 1 2
最大 1
164I 量大值250mm
UI
1 fhp t/ 4
12 15 211
IF 2 最大值5mmm
U2
IfMl tc, 2h
2
1fh 量大值mm
U.3 当按照分层长度与宽度的乘积计算Bm和B.时,应圆整到邻近的10mm。 双为钢带“翻板宽度 imm
16lh
9检测报告
有规定时,制造商应向购方提供至少包括下列内容的检测报告: a)本部分的编号。 b)符合性说明。