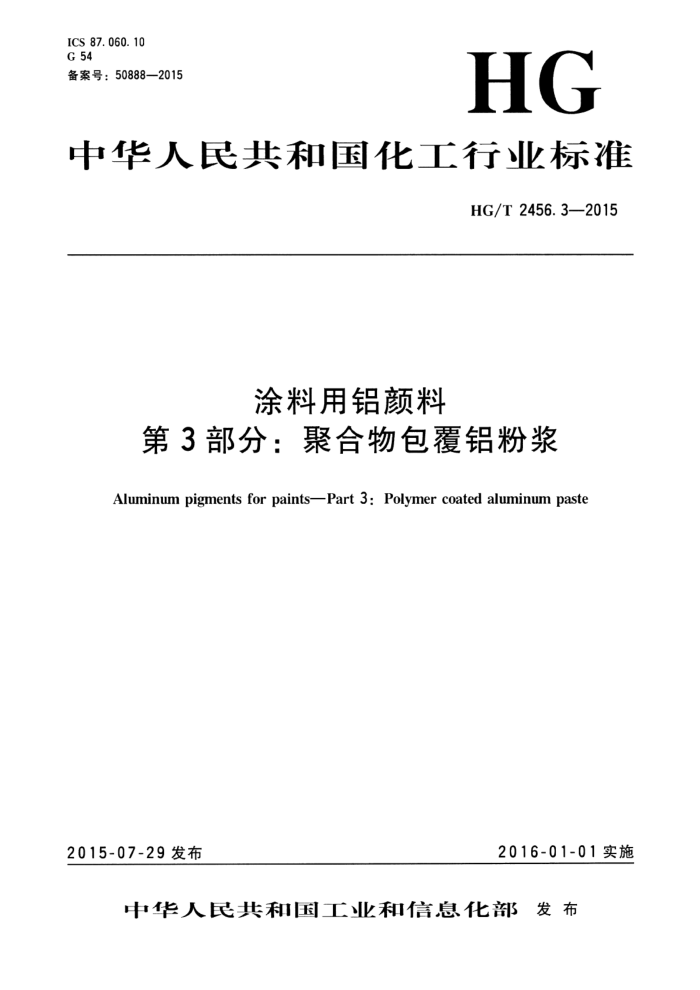
ICS 87.060.10 G 54 备案号:50888—2015
HG
中华人民共和国化工行业标准
HG/T 2456.3—2015
涂料用铝颜料
第3部分:聚合物包覆铝粉浆
Aluminum pigments for paints-Part 3: Polymer coated aluminum paste
2016-01-01实施
2015-07-29发布
中华人民共和国工业和信息化部发布
HG/T2456.3—2015
前言
HG/T2456《涂料用铝颜料》分为5个部分:
第1部分:铝粉浆;第2部分:铝粉;
-
第3部分:聚合物包覆铝粉浆;第4部分:真空镀铝悬浮液;第5部分:水性铝粉浆。
-
本部分为HG/T2456的第3部分。 本部分按照GB/T1.1一2009给出的规则起草。 本部分由中国石油和化学工业联合会提出。 本部分由全国涂料和颜料标准化技术委员会(SAC/TC5)归口。 本部分起草单位:长沙族兴新材料股份有限公司、中海油常州涂料化工研究院有限公司、合肥旭
阳铝颜料有限公司、星铂联雅思达颜料(济南)有限公司、章丘市金属颜料有限公司、苏州世名科技股份有限公司。
本部分主要起草人:周明、沈苏江、董前年、刘勤、刘恩鹏、杜长森。
I
HG/T2456.3—2015
涂料用铝颜料
第3部分:聚合物包覆铝粉浆
1范围
本部分规定了聚合物包覆铝粉浆的产品分类,要求,取样,试验方法,检验规则以及标志、包装和贮存。
本部分适用于用雾化铝粉、表面处理剂和有机溶剂在湿法球磨后再由带有活性基团的有机物经化学反应形成的聚合物包覆在片状铝粒子表面而成的聚合物包覆铝粉浆。产品主要用于涂料工业。 2规范性引用文件
下列文件对于本文件的应用是必不可少的。凡是注日期的引用文件,仅注日期的版本适用于本文件。凡是不注日期的引用文件,其最新版本(包括所有的修改单)适用于本文件。
GB/T17252007 色漆、清漆和塑料不挥发物含量的测定 GB/T1766—2008 色漆和清漆涂层老化的评级方法 GB/T3186 色漆、清漆和色漆与清漆用原材料取样 GB/T6682—2008 分析实验室用水规格和试验方法 GB/T6890—2012锌粉 GB/T 8170 数值修约规则与极限数值的表示和判定 GB/T 9271 色漆和清漆标准试板 GB/T9274—1988 色漆和清漆耐液体介质的测定 GB/T20975.3—2008 铝及铝合金化学分析方法第3部分:铜含量的测定 GB/T20975.5—2008 铝及铝合金化学分析方法第5部分:硅含量的测定 GB/T20975.8—2008 铝及铝合金化学分析方法第8部分:锌含量的测定 HG/T2456.1一2013涂料用铝颜料第1部分:铝粉浆
3产品分类
在本部分中,根据耐化学性将产品分为A、B、C3个类型,并分别对其主要用途做了说明,见表1。
表1聚合物包覆铝粉浆的分类
类型 A B c
耐化学性优良一般
用 途
主要用于耐候性、耐化学性要求较高的方面,如卷材涂料、建筑外墙涂料等。 主要用于对耐化学性、铝铅粉附着力有一定要求的方面.如塑料涂料、 油墨等。
4要求
产品应符合表2所列的要求。
HG/T2456.3—2015
表2要求
指 标
项 日
c 50
A
B
105℃不挥发物的质量分数/%
45
>
具有良好的银白色金属光泽及装饰性、平整性,与商定参照样品制备的涂膜外观接近
涂膜外观
180μm筛孔 45μm筛孔
无商定 24
筛余物的质量分数/%
耐碱性(浸人质量分数为5%的Na()H溶液)/h
48
6
耐酸性(浸人质量分数为5%的HC1溶液)
△E·≤3.0或不大于商定参照样品涂膜样板浸泡前后色差△E
施加商定直流电压。
施加2000V直流电压,正负极间隔10 正负极间隔10mm. mm.1min无放电、击穿现象
耐电压
1min无放电、击穿现象
≥
聚合物含量的质量分数/%
5
1
在50℃±2℃贴存商定天数后与室温贮存的对比,日视无颗粒、遮盖力无明显下降
在50℃±2℃购存30d后与室温贮存的对比,目视无颗粒、遮盖力无明显下降
贮存稳定性
水含量的质量分数/% 铁含量的质量分数/% 铅含量的质量分数/% 铜+铁+铅+硅+锌总含量的质量分数/%≤
N N A
0. 2 0. 2 0. 03 1. 0
5 取样
按GB/T3186的规定取受试产品的代表性样品。 6试验方法 6. 1 一般规定
除另有规定外,所用试剂的纯度应在分析纯及以上,实验用水应符合GB/T6682--2008中三级水的规格。 6.2105℃不挥发物
按GB/T1725--2007的规定进行。称样量约2g,烘烤温度105℃土2℃,烘烤时间3h。 6.3涂膜外观
按HG/T2456.1—2013中6.4的规定进行。 6.4 筛余物
按HG/T2456.1—2013中6.5的规定进行。
2
HG/T2456.3—2015
6.5耐碱性和耐酸性 6.5.1方法概述
将试样、商定参照样品先制成涂料,然后用相同方法制备试样和商定参照样品的涂膜样板,以适当方式干燥,再按GB/T9274--1988中5.4(浸泡法)的规定将样板浸人质量分数为5%的Va()H 溶液或质量分数为5%的HCI溶液中规定时间,测定试样和商定参照样品涂膜样板颜色变化,以试样涂膜样板浸泡前后色差△E,或与商定参照样品涂膜样板浸泡前后色差△E“比较的结果表示试样的耐碱性或耐酸性。 6.5.2材料和仪器 6.5.2.1分散介质;商定。
注:推荐使用丙烯酸类树脂。 6.5.2.2溶剂:与分散介质相适宜。 6.5.2.3底材:平整、不吸收。如合适尺寸的ABS塑料片、马口铁板、钢板、铝板、玻璃板等,马口铁板、钢板、铝板、玻璃板等底材的处理按照GB/T9271的规定进行。 6.5.2.4商定参照样品。 6.5.2.5天平:精度0.01g。 6.5.2.6喷漆设备或湿膜制备器。 6.5.2.7 测色仪。 6.5.2.8恒温干燥箱:能维持50℃±2℃。 6.5.2.9氢氧化钠。 6.5.2.10浓盐酸:质量分数浓度约37%,p~1.19g/mL。 6.5.3步骤 6.5.3.1制板
涂料制备条件:铝颜料:分散介质=10:100(质量比,均以不挥发物计算)。 将试样与分散介质(见6.5.2.1)和溶剂(见6.5.2.2)以适当的比例混合,采用低速搅拌使样
品充分分散到介质中。采用适当方法将其涂布于底材(见6.5.2.3)上,自然干燥或以商定的方式干燥,制备得到试样的涂膜样板
用相同方法制备商定参照样品的涂膜样板,注:可按下列方法制备涂料:称取10g样品(不挥发物50%时),放入烧杯中,加人25g溶剂,先手工搅拌5min分散
样品,再加人分散介质100g(不挥发物50%时),用搅拌器以300r/min~500r/min的搅拌速率搅拌15min。
6.5.3.2测定
按GB/T9274一1988中5.4的规定将样板浸入质量分数为5%的Na()H溶液或质量分数为5% 的HC溶液中,至规定的时间取出样板,用清水清洗干净后,用滤纸吸干表面水分,然后放人恒温干燥箱(见6.5.2.8),50℃烘烤3min后取出,冷却,目视观察,结果的评定按GB/T1766一2008 的规定进行。用测色仪(见6.5.2.7)测定试样和商定参照样品涂膜样板浸泡前后颜色变化△E,测定时所选取的测试区域(浸泡区域和未浸泡区域)位置离底材边缘的距离应大于10mm,选取的测试区域(浸泡区域和未浸泡区域)应分别至少5处,结果取5处测定值的平均值。 6.5.4结果表示
以试样涂膜样板浸泡前后色差△E'或与商定参照样品涂膜样板浸泡前后色差△E比较的结果表示试样的耐碱性或耐酸性。 6.6耐电压 6.6.1方法概述
将试样先制成涂料,然后用湿膜制备器将涂料刮涂在底材上,以适当方式于燥,得到试样的涂膜样板。用耐压测试仪测定涂膜样板在规定时间、规定间隔和规定电压作用下有无放电击穿现象.此
3
HG/T2456.3—2015 评价样品耐电压性能。 6.6.2材料和仪器 6.6.2.1底材:平整、不吸收,PET塑料片,尺寸100mm×150mm。 6.6.2.2湿膜制备器:规格100μm。 6.6.2.3天平:精度0.01g。 6.6.2.4耐压测试仪。 6.6.3步骤 6.6.3.1涂膜制备
涂料制备条件:铝额料:树脂=40:100(质量比,均以不挥发物计算)。 将试样与分散介质和溶剂以适当的方式混合,采用低速搅拌使样品充分分散到介质中。用100um
湿膜制备器(见6.6.2.2)将涂料刮涂在底材(见6.6.2.1)上,自然干燥或以商定的方式干燥,制备得到试样的涂膜样板。
注:可按下列方法制备涂料:称取20g样品(不挥发物50%时),放人烧杯中,加人50g溶剂,先手T.搅拌5min分散
样品,再加人分散介质50g(不挥发物50%时》,用搅拌器以300r/min~500r/min的搅拌速率搅15min。
6.6.3.2测定
按照耐压测试仪(见6.6.2.4)操作说明书进行测定。测试电压为直流2000V或商定的测试电压值。
测定时,将正、负极探头置于涂膜之上,间距10mm土0.5mm,通电时间1min,观察并记录有无放电击穿现象。
测试时,在涂膜样板上、中、下部分各随机选取1个点共3个点进行测试,所选取的点离底材边缘的距离应大于10mm。 6.6.4结果判定
在1min内,所测试的3个点均无放电击穿现象,判定为符合本项目要求。 6.7聚合物含量 6.7.1方法原理
试样先用混合溶剂清洗,去除原有溶剂、油脂及可溶物,然后用混合酸与铝粉反应除去铝。最后将反应后的溶液过滤,干燥并称量.计算得到聚合物含量。 6.7.2试剂 6.7.2.1甲苯。 6.7.2.2丙酮。 6.7.2.3浓盐酸:质量分数浓度约37%,p~1.19g/mlL。 6.7.2.4浓硝酸:质量分数浓度约70%,p~1.42g/mL。 6.7.2.5混合溶剂:由3份(体积)甲苯与1份(体积)丙酮混合而得。 6.7.2.6混合酸溶液:3份(体积)浓盐酸与1份(体积)浓硝酸混合,再将此混合酸稀释3倍制得。 6.7.3仪器 6.7.3.1烧结玻璃过滤埚:牌号P16(孔径大于10um且小于等于16m)。 6.7.3.2天平:精度0.001g。 6.7.3.3烘箱:能维持50℃±2℃和105℃±2℃。 6.7.4步骤 6.7.4.1试样
称取铝粉浆约10g(m),精确至0.001g。
!
HG/T2456.3—2015
6.7.4.2测定
将试样置于250mL烧杯中,加入100mL混合溶剂(见6.7.2.5),摇晃烧杯中的物料使其分散。 完全分散后,再加入50mL混合溶剂(见6.7.2.5),摇晃烧杯使其完全混匀,静置1h。然后摇晃烧杯使铝粉再次混勾,将此分散液通过已知质量(m1)的烧结玻璃过滤埚(见6.7.3.1)抽滤到一清洁烧瓶内。用适量混合溶剂(见6.7.2.5)将烧杯中的剩余物再次分散,将此分散液通过过滤进行抽滤。用适量丙酮(见6.7.2.2)冲洗干净烧杯,洗液倒入过滤进行抽滤。用适量丙酮(见 6.7.2.2)抽滤洗涤埚中滤饼,并在滤饼近干后再抽吸30min,然后将埚与滤饼一起放入50℃土 2℃的烘箱中烘烤1h,取出后放人干燥器中冷却,称量(m2)。
称取上述去油脂后的铝粉约3g(m3),精确至0.001g。将其置于个1000mL烧杯中,先加人 20ml.蒸馏水,用玻璃棒搅拌烧杯中的物料使其分散,然后缓慢滴加100ml.混合酸溶液(见 6.7.2.6),在滴加的同时不停地搅拌,使烧杯中的物料分散均匀,直至混合酸溶液滴加完毕,继续搅拌15min后,再加人50mL.混合酸溶液(见6.7.2.6),搅拌使其完全混匀,然后静置足够长时间,使铝粉完全反应。
在上述反应完全后的溶液中加人500mL蒸馏水,至少搅拌15min,然后将溶液倒人一个已恒重(m4)的烧结玻璃过滤(见6.7.3.1)中进行抽滤,用蒸馏水清洗干净烧杯,洗液倒人过滤埚中,再用500mL.以上的蒸馏水冲洗剩余物,边冲洗边过滤,过滤完毕后,将埚及剩余物置于105℃土2℃ 烘箱中加热,放入干燥器中冷却,称量(ms),直至恒重。 6.7.4.3结果表示
按公式(1)计算聚合物含量,以质量分数表示
-"="×"×100%
...... (1)
m
m3
式中: m2— 过滤用埚及去油脂后铝粉的质量的数值,单位为克(g); m1— 得到去油脂后铝粉所用过滤埚的质量的数值单位为克(g); m 称取铝粉浆的质量的数值,单位为克(g); ms- 过滤用埚及剩余物的质量的数值,单位为克(g); m4 得到剩余物(聚合物)所用过滤埚的质量的数值,单位为克(g); m3 称取去油脂后铝粉的质量的数值,单位为克(g)。
-
-
6.8贮存稳定性 6.8.1方法概述
将热贮存试验[(50土2)℃,30d后的样品与同时室温贮存的样品分别制成涂料,刮涂制备得到由热贮存试验后与同时室温贮存的样品制备的涂膜样板,目视比较,以其外观变化情况评价试样的贮存稳定性。 6.8.2材料和仪器 6.8.2.1压盖式金属漆罐:容积100mL。 6.8.2.2遮盖力测试纸(黑白卡纸)。 6.8.2.3恒温干燥箱:能维持50℃士2℃。 6.8.2.4天平;精度0.01g。 6.8.2.5湿膜制备器:规格100um。 6.8.3步骤
在4个压盖式金属漆罐(见6.8.2.1)中分别装入约30g样品,将盖盖紧。 称量已装入样品的金属漆罐质量,精确至0.01g。随机选取1罐留作对比样,室温放置。另3罐
放入恒温干燥箱(见6.8.2.3)中,将干燥箱从室温升至50℃士2℃,保温30d,保温结束后将样品
5
HG/T2456.3—2015 罐从干燥箱中取出,在室温下自然冷却大于16h。
称量热贮存试验后的金属漆罐质量,如与贮存前的质量差值≤2%,则认为符合实际存放时的包装条件。
注:如贮存前后金属漆罐的质量差异>2%,则认为包装异常,需重新试验。 按如下方法制备得到热贮存试验后样品的涂料:从符合条件的罐中称取约10g样品,放人清洁
的烧杯中,加人25g溶剂,先手工搅拌5min分散样品,然后补加100g分散介质(树脂),再用搅拌器以300r/min~500r/min的搅拌速率搅拌15min。
用相同方法制备室温贮存(未经热贮存试验)的样品的涂料。 用规格100μm的湿膜制备器(见6.8.2.5)在遮盖力测试纸(黑白卡纸)(见6.8.2.2)上刮涂
一道上述涂料,按适当方式完全干燥后得到由热贮存试验后与同时室温贮存的样品制备的涂膜样板,目视观察比较涂膜表面状况 6.8.4结果表示
以热贮存试验后涂膜表面有无颗粒以及与同时室温贮存的样品涂膜样板对比后遮盖力有无明显下降表示结果。 6.9水含量
按HG/T2456.1—2013中6.9的规定进行。 6.10铁含蛋
按GB/T6890一2012附录C(火焰原子吸收光谱法)的规定进行。 6.11铅含量
按GB/T6890一2012附录C(火焰原子吸收光谱法)的规定进行。 6.12铜+铁+铅+硅+锌总含量 6.12.1铜含量
按GB/T20975.3一2008“方法二:火焰原子吸收光谱法”的规定进行。 6.12.2硅含量
按GB/T20975.5一2008“方法一:钥蓝分光光度法”的规定进行。 6.12.3锌含量
按GB/T20975.8一2008“方法二:火焰原子吸收光谱法”的规定进行。 6.12.4铜+铁+铅+硅+锌总含量
将按6.12.1、6.10、6.11、6.12.2、6.12.3测定得到的结果加和,计算出铜十铁十铅十硅十锌总含量。
注:铁、铅、铜、锌含基也可使用其他合适的分析仪器,如电感耦合等离子体原子发射光谱仪(ICP-()ES),根
据仪器制造商的相关说明进行测试得到。
7检验规则 7.1检验分类 7.1.1产品检验分为出厂检验和型式检验。 7.1.2出厂检验项目包括105℃不挥发物、涂膜外观、筛余物、耐碱性共4个项目。 7.1.3型式检验项目包括本部分所列的全部技术要求。在正常生产情况下,每年至少进行一次型式检验。 7.2检验结果的判定 7.2.1检验结果的判定按GB/T8170中修约值比较法进行。 7.2.2所有项目的检验结果均达到本部分要求时,该试验样品为符合本部分要求。
6