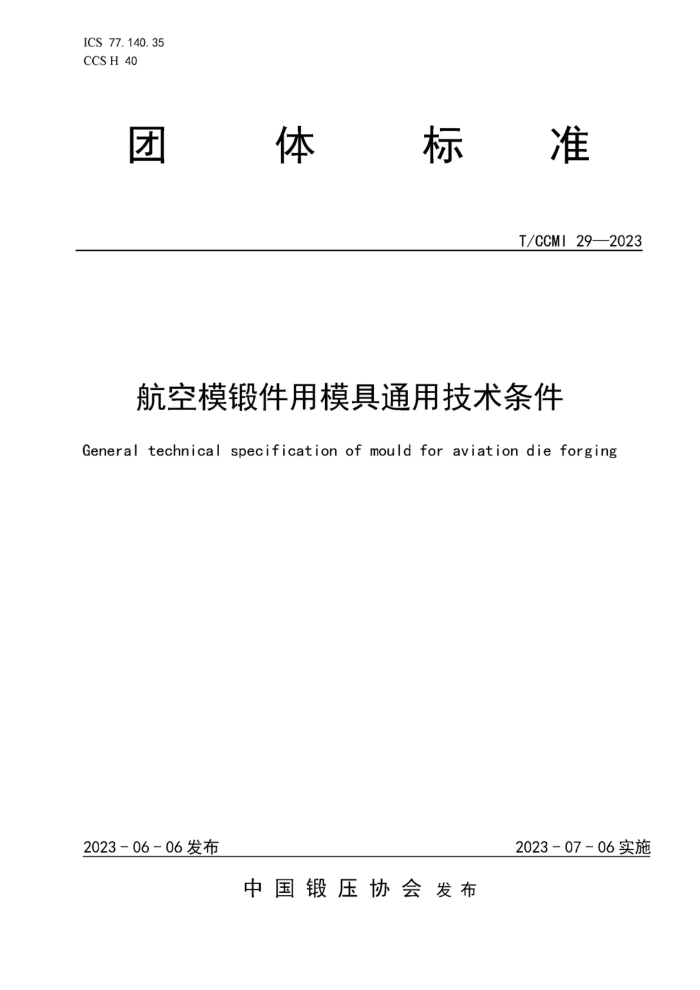
T/CCMI 292023
目 次
前言 1 范围 2 规范性引用文件 3 术语和定义 4 订货要求
II
技术要求. 6 试验方法,
5
P
检验规则 8 标志,
7
包装、运输和贮存附录A(资料性) 模具的使用和维护管理方法
Q
表1模块和模具材料选型参考表表2模具表面粗糙度要求,表A.1常用模具预热温度推荐表、 表A.2模具预热时间表.:表A.3模具型腔表面规定温度
:
.
T/CCMI 29-2023
前言
本文件按照GB/T1.1一2020《标准化工作导则第1部分:标准化文件的结构和起草规则》的规定起草。
请注意本文件的某些内容可能涉及专利。本文件的发布机构不承担识别专利的责任,本文件由中国锻压协会航空材料成形技术分会提出。 本文件由中国锻压协会归口。 本文件起草单位:浙江索特重工科技有限公司、中国航发北京航空材料研究院、中国航空技术国际
控股有限公司、贵州安大航空锻造有限责任公司、西安三角防务股份有限公司、中国第二重型机械集团德阳万航模锻有限公司、陕西宏远航空锻造有限责任公司、江西景航航空锻铸有限公司、中航重机股份有限公司、无锡派克新材料科技有限公司、西南铝业(集团)有限责任公司、无锡透平叶片有限公司、 中航特材工业(西安)有限公司、贵州航宇科技发展股份有限公司、四川钢研高纳锻造有限责任公司、 山西中工重型锻压有限公司、山西金瑞高压环件有限公司、连云港杰瑞自动化有限公司、贵阳安大宇航材料工程有限公司、湖北三环锻造有限公司、上海交通大学。
本文件主要起草人:汪敏、林海、王洋、曲敬龙、包建、谭江坪、张伟华、王龙祥、郑永灵、杨亚平、夏春林、杜常鹏、王海鹏、马玉斌、张睿、李蓬川、曾菁、阙基容、王平、郭敏、张健、韩志飞、 刘孝强、刘峰、刘其源、孙传华、杨雄、苏化冰、李晓婷、仲惟光、刘新权、侯伟、任永海、张桂兰、 杨良会、刘君、崔云迪、段忠园、陈鹏、汪云生、陈天赋、胡成亮。
本文件为首次发布。
II
T/CCMI29-2023
航空模锻件用模具通用技术条件
1范围
本文件规定了航空模锻件用模块及模具的订货要求、技术要求、试验方法、检验规则、标志、包装、 运输和贮存。
本文件适用于航空模锻件用模块及模具的订货、制造、检验,以及模具的使用和维护。
2规范性引用文件
2
下列文件的内容通过文中的规范性引用而构成本文件必不可少的条款。其中,注日期的引用文件仅该日期对应的版本适用于本文件。不注日期的引用文件,其最新版本(包括所有的修改单)适用于本文件。
GB/T 222 钢的成品化学成分允许偏差 GB/T223钢铁及合金化学分析方法(适用部分) GB/T 226 钢的低倍组织及缺陷酸蚀检验法检测标准 GB/T 230.1 金属材料洛氏硬度试验第1部分:试验方法 GB/T1800.2 产品儿何技术规范(GPS)线性尺寸公差ISO代号体系第2部分:标准公差带代号
和孔、轴的极限偏差表
GB/T 1184 形状和位置公差未注公差值 GB/T1299 工模具钢 GB/T 6402 钢锻件超声检测方法 GB/T 8541 锻压术语 GB/T 8845 模具术语 GB/T10561 钢中非金属夹杂物含量的测定标准评级图显微检验法 GB/T11170不锈钢的光电发射光谱分析方法 GB/T 11880 模锻锤和大型机械锻压机用模块技术条件 GB/T15822 无损检测磁粉检测(适用部分) GB/T20066 钢和铁化学成分测定用试样的取样和制样方法 GB/T 20123 钢铁总碳硫含量的测定高频感应炉燃烧后红外吸收法(常规方法) GB/T 20124 钢铁氮含量的测定情性气体熔融热导法(常规方法) GB/T20125 低合金钢多元素含量的测定电感耦合等离子体原子发射光谱法 GB/T31310 金属材料残余应力测定钻孔应变法 GB/T 37775 大型钢制自由锻件通用技术条件 GJB 904 锻造工艺质量控制 JB/T6396 大型合金结构钢锻件技术条件
术语和定义
3
GB/T8541和GB/T8845中界定的以及下列术语和定义适用于本文件。
1
T/CCMI 29-2023 3. 1
模块block 设有工作部分的模具主体,一般分为上模和下模。 [来源:GB/T8845,图100、图105]
3. 2
模具mould 将材料成形(成型)为具有特定形状和尺寸的制品、制件的工艺装备,类型包括冲模、塑料模、压
铸模、锻模、粉末冶金模、拉制模、辊压模、玻璃模、橡胶模、铸造模等。
4订货要求
4.1需方应在订货合同或协议中注明材料牌号、模具尺寸、热处理、加工制造要求、检验项目、包装运输标准以及其他附加说明 4.2需方需要提供成品模具时,应提供模具加工图样或数模。 4. 3 当需方有特殊要求时, 应经供需双方协议,并在订货合同或协议中注明
Oe
技术要求
5
5. 1 一般原则
S
模块的生产制造工序应包括:熔炼 一下料 锻造 粗加工 检验 包装。 模具的生产制造工序应包括:熔炼 下料 锻造 粗加工 热处理 (半精加工)(去应力)
5.1.1 5.1.2
精加工 抛光 检验 包装。
5.1.3模具的生产工艺排布应充分考虑整个制造物料流转过程的便利、生产成本的控制、产品质量要求、设备状况等方面要求。 5.1.1模具的原材料选择应充分考虑模具的用途、产品特性、使用环境等因素的影响。 5.1.2模具坏料的锻造工艺应充分考虑材料的变形抗力、金属流线、定位可靠性及设备偏心载荷等因素的影响,宜采用数值模拟对锻造工艺过程和锻造工艺参数进行优化。 5.1.3模具的加工工艺设计应充分考虑模具型腔的复杂程度、尺寸精度、表面质量要求,选择合适的制造工艺和生产设备 5. 2 模块和模具材料的选型
模块和模具常用材料的牌号、主要特性、主要用途及选型参考见表1。
表1 模块和模具材料选型参考表
牌号
出厂硬度 HBW
出厂状态
主要用途
钢材特性
中国
国外相近牌号
热作模具钢,具有较高的热强度和硬度,良好的耐磨性和韧性比5CrMnMo具有更加良好 用于各种中大型热锻的热强度,韧性和高淬透性 模、环锻模具及工装
用于各种中大型热锻模、环锻模具及工装
55NiCrMoV7
1. 2714
球化退火
≤220
5CrNiMo
L6/1.2713/SKT4 球化退火
≤210
2
T/CCMI 292023
表1 模块和模具材料选型参考表(续)
牌号
出厂硬度 HBW ≤210
钢材特性
主要用途
出厂状态
中国 5CrMnMo
国外相近牌号 6G/SKT5
耐热耐磨锻压模,具有良好 用于各种中小型热锻的热强度、韧性和高淬透性 模热作模具钢,具有较高的热
球化退火
用于热挤压模、压铸模和模锻模热挤压模、各种锻造模用于高温下要求高应
H13/1.2344/ 8402/SKD61
球化退火
强度和硬度,良好的耐磨性和韧性耐热热作模具钢
4Cr5MoSiV1
≤230
H11
球化退火
4Cr5MoSiV
≤220
具有耐热性、韧性、塑性和 力、高耐磨而不受冲击抗冷热疲劳性能一般
球化退火
3Cr2W8V
≤230
H21/SKD5
负荷的镁、锌、铝合金挤压模具适于使用温度在 500℃~600℃度范围内的热锻模具,如制作压力机用连杆锻模和齿合齿轮锻模适合制作受热温度较
O
CHO S SO
较H13钢具有更高的高温强度和耐热磨损能力
2Cr3Mo2NivSi
球化退火
≤220
高的热强性、热稳定性,良 高的黑色及有色金属好的韧性、导热性和工艺性 热挤压与压铸模具,寿能
球化退火
4Cr3Mo2VNb
220
命比 3Cr2W8V大幅提高适于制造热挤压模,热冲模、热锻模及塑压模等模具,主要用于铝合金压铸模
良好的淬透性,很高的韧具有高的硬度、热强性和耐磨性
球化退火
4Cr3Mo3SiV
≤229
注:包括但不限于表1所列牌号。
S
5. 3 钢锭的冶炼 5.3.1 钢锭宜采用电弧炉、电弧炉+真空脱气、电弧炉+电渣重熔、真空电弧重熔(VAR)及其他满足要求的方法冶炼,具体冶炼方法应在合同中注明。 5.3.2制造模具所用钢锭中的化学成分含量应符合GB/T1299,模块化学成分符合GB/T11880的规定,化学成分允许偏差应符合GB/T222的规定 5.3.3钢中的非金属夹杂物含量应符合GB/T10561中附录D类3级的规定。当需方有特殊要求时,应以需方要求为准。 5.4模块 5.4.1 模块锻造工艺 5.4.1.1模块坏料的锻造方法应符合JB/T6396的规定。 5.4.1.2铸坏应留有足够的切除量,确保成品锻件无缩孔、偏析等影响质量的缺陷。
3
T/CCMI 29-2023 5.4.1.3模块宜采用无冲击性的设备进行锻造开坏。模块锻造时至少三镦三拔(一次镦粗后接一次拔长,如此循环三次),且单次变形量不应小于40%,总锻造比应不小于7。 5.4.2模块金属流线 5.4.2.1方形模块的金属流线应与模块长度方向保持一致且连续流畅,圆形模块的金属流线应顺直径方向连续流畅 5.4.2.2模块应标明金属流线方向,且沿最大尺寸方向分布;当需方对金属流线方向有特殊要求时,应以需方要求为准。 5.4.2.3在金属流线平行方向的侧面上打印双箭头“←→”,指明本模块的钢材纤维方向。 5.4.3模块热处理
模块应进行锻后退火处理,材质退火要求应符合GB/T1299、GB/T11880的规定。 5.4.4模块力学性能 5.4.4.1模块应进行100%表面硬度检验,同一模块的表面硬度均匀性偏差应在10%以内,退火后硬度值应符合表1中的要求。 5.4.4.2模块的拉伸性能和冲击性能实验取样、制样方法应符合GB/T37775的规定。模块热处理后的拉伸性能和冲击性能应符合供需双方共同确认的图样、技术协议、供货合同的要求。 5.4.5模块表面质量
模块表面不应有斑疤、裂纹、折叠、磕碰、划痕等目视可见的缺陷。 5.4.6模块超声波检验
锻造完成的模块应进行超声波检测,
5.5模具 5.5.1模具表面质量 5.5.1.1模具表面不应有斑疤、裂纹、折叠、磕碰、划痕等目视可见的缺陷, 5.5.1.2模具应进行100%表面硬度检验,检验硬度值应符合需方图纸或技术协议的规定;同一模具的硬度均匀性偏差应在10%以内。当需方有特殊要求时,由供需双方协商确定。 5.5.1.3模具表面粗糙度Ra应按表2规定执行。
表2模具表面粗糙度要求
单位为微米型腔面 ≤0.8
类别表面粗糙度
模具外表面 ≤12.5
基准面 键槽、燕尾、锁扣 ≤1.6
模具安装配合面
≤1.6
≤3. 2
Ra 注:当需方有特殊要求时,需在合同或图样或协议中注明。
*为导柱、导套配合面。
5.5.2模具超声波检测
制造完成的模具应进行100%超声波检测。 5.5.3模具的尺寸及形位公差 4
T/CCMI 292023
目 次
前言 1 范围 2 规范性引用文件 3 术语和定义 4 订货要求
II
技术要求. 6 试验方法,
5
P
检验规则 8 标志,
7
包装、运输和贮存附录A(资料性) 模具的使用和维护管理方法
Q
表1模块和模具材料选型参考表表2模具表面粗糙度要求,表A.1常用模具预热温度推荐表、 表A.2模具预热时间表.:表A.3模具型腔表面规定温度
:
.
T/CCMI 29-2023
前言
本文件按照GB/T1.1一2020《标准化工作导则第1部分:标准化文件的结构和起草规则》的规定起草。
请注意本文件的某些内容可能涉及专利。本文件的发布机构不承担识别专利的责任,本文件由中国锻压协会航空材料成形技术分会提出。 本文件由中国锻压协会归口。 本文件起草单位:浙江索特重工科技有限公司、中国航发北京航空材料研究院、中国航空技术国际
控股有限公司、贵州安大航空锻造有限责任公司、西安三角防务股份有限公司、中国第二重型机械集团德阳万航模锻有限公司、陕西宏远航空锻造有限责任公司、江西景航航空锻铸有限公司、中航重机股份有限公司、无锡派克新材料科技有限公司、西南铝业(集团)有限责任公司、无锡透平叶片有限公司、 中航特材工业(西安)有限公司、贵州航宇科技发展股份有限公司、四川钢研高纳锻造有限责任公司、 山西中工重型锻压有限公司、山西金瑞高压环件有限公司、连云港杰瑞自动化有限公司、贵阳安大宇航材料工程有限公司、湖北三环锻造有限公司、上海交通大学。
本文件主要起草人:汪敏、林海、王洋、曲敬龙、包建、谭江坪、张伟华、王龙祥、郑永灵、杨亚平、夏春林、杜常鹏、王海鹏、马玉斌、张睿、李蓬川、曾菁、阙基容、王平、郭敏、张健、韩志飞、 刘孝强、刘峰、刘其源、孙传华、杨雄、苏化冰、李晓婷、仲惟光、刘新权、侯伟、任永海、张桂兰、 杨良会、刘君、崔云迪、段忠园、陈鹏、汪云生、陈天赋、胡成亮。
本文件为首次发布。
II
T/CCMI29-2023
航空模锻件用模具通用技术条件
1范围
本文件规定了航空模锻件用模块及模具的订货要求、技术要求、试验方法、检验规则、标志、包装、 运输和贮存。
本文件适用于航空模锻件用模块及模具的订货、制造、检验,以及模具的使用和维护。
2规范性引用文件
2
下列文件的内容通过文中的规范性引用而构成本文件必不可少的条款。其中,注日期的引用文件仅该日期对应的版本适用于本文件。不注日期的引用文件,其最新版本(包括所有的修改单)适用于本文件。
GB/T 222 钢的成品化学成分允许偏差 GB/T223钢铁及合金化学分析方法(适用部分) GB/T 226 钢的低倍组织及缺陷酸蚀检验法检测标准 GB/T 230.1 金属材料洛氏硬度试验第1部分:试验方法 GB/T1800.2 产品儿何技术规范(GPS)线性尺寸公差ISO代号体系第2部分:标准公差带代号
和孔、轴的极限偏差表
GB/T 1184 形状和位置公差未注公差值 GB/T1299 工模具钢 GB/T 6402 钢锻件超声检测方法 GB/T 8541 锻压术语 GB/T 8845 模具术语 GB/T10561 钢中非金属夹杂物含量的测定标准评级图显微检验法 GB/T11170不锈钢的光电发射光谱分析方法 GB/T 11880 模锻锤和大型机械锻压机用模块技术条件 GB/T15822 无损检测磁粉检测(适用部分) GB/T20066 钢和铁化学成分测定用试样的取样和制样方法 GB/T 20123 钢铁总碳硫含量的测定高频感应炉燃烧后红外吸收法(常规方法) GB/T 20124 钢铁氮含量的测定情性气体熔融热导法(常规方法) GB/T20125 低合金钢多元素含量的测定电感耦合等离子体原子发射光谱法 GB/T31310 金属材料残余应力测定钻孔应变法 GB/T 37775 大型钢制自由锻件通用技术条件 GJB 904 锻造工艺质量控制 JB/T6396 大型合金结构钢锻件技术条件
术语和定义
3
GB/T8541和GB/T8845中界定的以及下列术语和定义适用于本文件。
1
T/CCMI 29-2023 3. 1
模块block 设有工作部分的模具主体,一般分为上模和下模。 [来源:GB/T8845,图100、图105]
3. 2
模具mould 将材料成形(成型)为具有特定形状和尺寸的制品、制件的工艺装备,类型包括冲模、塑料模、压
铸模、锻模、粉末冶金模、拉制模、辊压模、玻璃模、橡胶模、铸造模等。
4订货要求
4.1需方应在订货合同或协议中注明材料牌号、模具尺寸、热处理、加工制造要求、检验项目、包装运输标准以及其他附加说明 4.2需方需要提供成品模具时,应提供模具加工图样或数模。 4. 3 当需方有特殊要求时, 应经供需双方协议,并在订货合同或协议中注明
Oe
技术要求
5
5. 1 一般原则
S
模块的生产制造工序应包括:熔炼 一下料 锻造 粗加工 检验 包装。 模具的生产制造工序应包括:熔炼 下料 锻造 粗加工 热处理 (半精加工)(去应力)
5.1.1 5.1.2
精加工 抛光 检验 包装。
5.1.3模具的生产工艺排布应充分考虑整个制造物料流转过程的便利、生产成本的控制、产品质量要求、设备状况等方面要求。 5.1.1模具的原材料选择应充分考虑模具的用途、产品特性、使用环境等因素的影响。 5.1.2模具坏料的锻造工艺应充分考虑材料的变形抗力、金属流线、定位可靠性及设备偏心载荷等因素的影响,宜采用数值模拟对锻造工艺过程和锻造工艺参数进行优化。 5.1.3模具的加工工艺设计应充分考虑模具型腔的复杂程度、尺寸精度、表面质量要求,选择合适的制造工艺和生产设备 5. 2 模块和模具材料的选型
模块和模具常用材料的牌号、主要特性、主要用途及选型参考见表1。
表1 模块和模具材料选型参考表
牌号
出厂硬度 HBW
出厂状态
主要用途
钢材特性
中国
国外相近牌号
热作模具钢,具有较高的热强度和硬度,良好的耐磨性和韧性比5CrMnMo具有更加良好 用于各种中大型热锻的热强度,韧性和高淬透性 模、环锻模具及工装
用于各种中大型热锻模、环锻模具及工装
55NiCrMoV7
1. 2714
球化退火
≤220
5CrNiMo
L6/1.2713/SKT4 球化退火
≤210
2
T/CCMI 292023
表1 模块和模具材料选型参考表(续)
牌号
出厂硬度 HBW ≤210
钢材特性
主要用途
出厂状态
中国 5CrMnMo
国外相近牌号 6G/SKT5
耐热耐磨锻压模,具有良好 用于各种中小型热锻的热强度、韧性和高淬透性 模热作模具钢,具有较高的热
球化退火
用于热挤压模、压铸模和模锻模热挤压模、各种锻造模用于高温下要求高应
H13/1.2344/ 8402/SKD61
球化退火
强度和硬度,良好的耐磨性和韧性耐热热作模具钢
4Cr5MoSiV1
≤230
H11
球化退火
4Cr5MoSiV
≤220
具有耐热性、韧性、塑性和 力、高耐磨而不受冲击抗冷热疲劳性能一般
球化退火
3Cr2W8V
≤230
H21/SKD5
负荷的镁、锌、铝合金挤压模具适于使用温度在 500℃~600℃度范围内的热锻模具,如制作压力机用连杆锻模和齿合齿轮锻模适合制作受热温度较
O
CHO S SO
较H13钢具有更高的高温强度和耐热磨损能力
2Cr3Mo2NivSi
球化退火
≤220
高的热强性、热稳定性,良 高的黑色及有色金属好的韧性、导热性和工艺性 热挤压与压铸模具,寿能
球化退火
4Cr3Mo2VNb
220
命比 3Cr2W8V大幅提高适于制造热挤压模,热冲模、热锻模及塑压模等模具,主要用于铝合金压铸模
良好的淬透性,很高的韧具有高的硬度、热强性和耐磨性
球化退火
4Cr3Mo3SiV
≤229
注:包括但不限于表1所列牌号。
S
5. 3 钢锭的冶炼 5.3.1 钢锭宜采用电弧炉、电弧炉+真空脱气、电弧炉+电渣重熔、真空电弧重熔(VAR)及其他满足要求的方法冶炼,具体冶炼方法应在合同中注明。 5.3.2制造模具所用钢锭中的化学成分含量应符合GB/T1299,模块化学成分符合GB/T11880的规定,化学成分允许偏差应符合GB/T222的规定 5.3.3钢中的非金属夹杂物含量应符合GB/T10561中附录D类3级的规定。当需方有特殊要求时,应以需方要求为准。 5.4模块 5.4.1 模块锻造工艺 5.4.1.1模块坏料的锻造方法应符合JB/T6396的规定。 5.4.1.2铸坏应留有足够的切除量,确保成品锻件无缩孔、偏析等影响质量的缺陷。
3
T/CCMI 29-2023 5.4.1.3模块宜采用无冲击性的设备进行锻造开坏。模块锻造时至少三镦三拔(一次镦粗后接一次拔长,如此循环三次),且单次变形量不应小于40%,总锻造比应不小于7。 5.4.2模块金属流线 5.4.2.1方形模块的金属流线应与模块长度方向保持一致且连续流畅,圆形模块的金属流线应顺直径方向连续流畅 5.4.2.2模块应标明金属流线方向,且沿最大尺寸方向分布;当需方对金属流线方向有特殊要求时,应以需方要求为准。 5.4.2.3在金属流线平行方向的侧面上打印双箭头“←→”,指明本模块的钢材纤维方向。 5.4.3模块热处理
模块应进行锻后退火处理,材质退火要求应符合GB/T1299、GB/T11880的规定。 5.4.4模块力学性能 5.4.4.1模块应进行100%表面硬度检验,同一模块的表面硬度均匀性偏差应在10%以内,退火后硬度值应符合表1中的要求。 5.4.4.2模块的拉伸性能和冲击性能实验取样、制样方法应符合GB/T37775的规定。模块热处理后的拉伸性能和冲击性能应符合供需双方共同确认的图样、技术协议、供货合同的要求。 5.4.5模块表面质量
模块表面不应有斑疤、裂纹、折叠、磕碰、划痕等目视可见的缺陷。 5.4.6模块超声波检验
锻造完成的模块应进行超声波检测,
5.5模具 5.5.1模具表面质量 5.5.1.1模具表面不应有斑疤、裂纹、折叠、磕碰、划痕等目视可见的缺陷, 5.5.1.2模具应进行100%表面硬度检验,检验硬度值应符合需方图纸或技术协议的规定;同一模具的硬度均匀性偏差应在10%以内。当需方有特殊要求时,由供需双方协商确定。 5.5.1.3模具表面粗糙度Ra应按表2规定执行。
表2模具表面粗糙度要求
单位为微米型腔面 ≤0.8
类别表面粗糙度
模具外表面 ≤12.5
基准面 键槽、燕尾、锁扣 ≤1.6
模具安装配合面
≤1.6
≤3. 2
Ra 注:当需方有特殊要求时,需在合同或图样或协议中注明。
*为导柱、导套配合面。
5.5.2模具超声波检测
制造完成的模具应进行100%超声波检测。 5.5.3模具的尺寸及形位公差 4