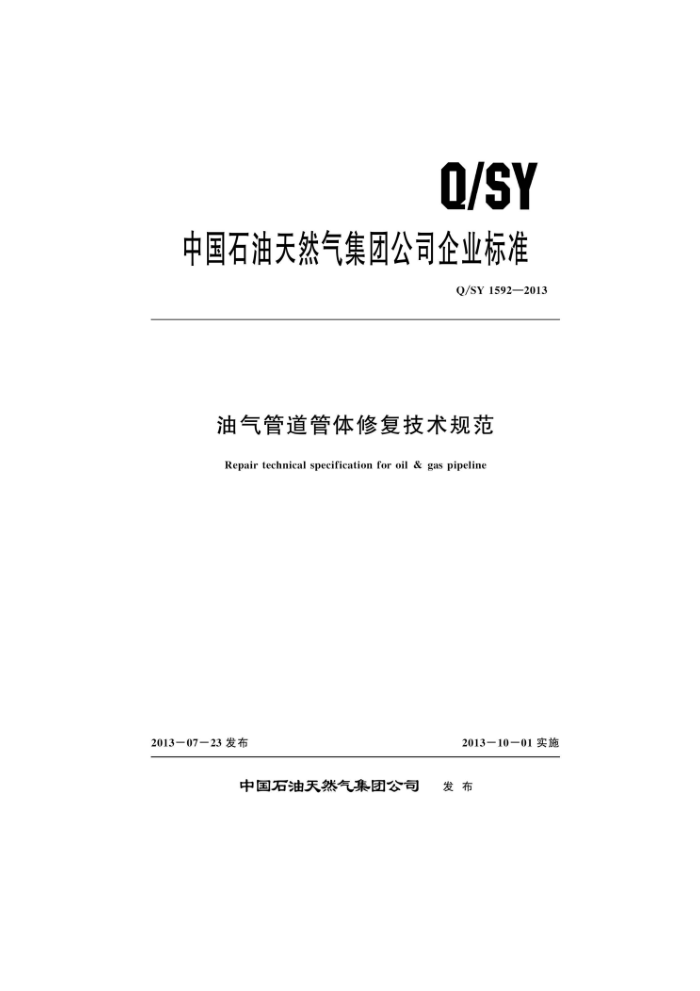
Q/SY
中国石油天然气集团公司企业标准
Q/SY1592—2013
油气管道管体修复技术规范
Repair technical specification for oil & gas pipeline
2013—07—23发布
2013-10-01实施
中国石油天然气集团公司 发布
Q/SY1592—2013
目 次
前言
范围规范性引用文件术语和定义修复技术选择
管体缺陷类型 4. 2 常用修复技术管体缺陷修复 5.1 管体缺陷修复原则 5. 2 管体泄漏 5. 3 管体外腐蚀 5. 4 管体内部缺陷或腐蚀 5. 5 管体凿槽或其他金属损失
4. 1
5
管体电弧烧伤、夹渣 5. 7 管体凹坑 5.8 管体硬点 5.9 管体裂纹 5.10 管体焊缝缺陷 5. 11 管体环焊缝缺陷 5.12 管体皱弯、弯曲缺陷· 5.13 管体砂眼、氢致裂纹缺陷 5. 14 管体打孔盗油(气)泄漏 6管体修复作业流程
5. 6
作业流程图 6.2 管体缺陷评价 6. 3 修复方案制定 6. 4 修复材料准备 6. 5 现场开挖
6. 1
旧防腐层清除及基材表面处理 6. 7 缺陷定位
6.6
缺陷修复 6.9 现场检测 6.10 修复层防腐及回填 6. 11 后期工作附录A(资料性附录) 修复技术
6.8
Q/SY 1592—2013 附录B(资料性附录) 管道打孔盗油(气)修复附录C(规范附录) 管道维修的HSE管理规定附录D(资料性附录) 管体缺陷与修复记录表附录E(资料性附录) 复合材料修复管道缺陷后的性能测试参考文献
22 25 27 29 32
+
...........
=
Q/SY 1592—2013
前 言
本标准按照GB/T1.1—2009《标准化工作导则 第1部分:标准的结构和编写》给出的规则起草。
本标准由中国石油天然气集团公司标准化委员会天然气与管道专业标准化技术委员会提出并归口。
本标准起草单位:西部管道分公司、天然气与管道分公司、管道分公司、北京天然气管道有限公司、西气东输管道分公司、天津大学。
本标准主要起草人:郭臣、杨永和、徐震、付立武、蒋金生、胡江锋、项卫东、高强、周永涛、 陈旭、高丽兰、孙震东、代鹏飞、马剑。
II
Q/SY 1592—2013
油气管道管体修复技术规范
范围本标准规定了油气管道管体修复技术的技术特点、修复要点及施工流程。 本标准适用于油气长输管道管体缺陷、打孔盗油(气)点等的修复工作。 规范性引用文件下列文件对于本文件的应用是必不可少的。凡是注日期的引用文件,仅注日期的版本适用于本文件。凡是不注日期的引用文件,其最新版本(包括所有的修改单)适用于本文件。
-
2
SY/T5918埋地钢质管道外防腐层修复技术规范
3术语和定义
下列术语和定义适用于本文件。 管体 tube 管道本体。 缺陷defeet 管体尺寸或特性超过允许界限的异常现象。 机械夹具 mechanical clamp 安装在泄漏缺陷部位外部形成密封空腔,提供强度和刚度保证的金属构件。 补板patch welding 为修补管道缺陷,而在缺陷处焊接一块与原管道材质和规格相同或相近的板材。 管帽 pipe cap 一端带封头的短管。 套筒修复 full encirclement steel sleeve repair 利用两个由钢板制成的半柱外壳覆盖在管道缺陷外,通过焊接连接在一起,套筒与管壁紧密结
3. 1
3. 2
3. 3
3. 4
3. 5
3. 6
合,协同变形,提高缺陷管体的承压能力。 3. 7
复合材料修复 nonmetallic composite repair 利用复合材料修复层的高强度和高模量,通过涂敷在缺陷部位的高强度填料,以及管体上和纤维
材料层间的强力胶,将作用管道损伤部位的应力均匀地传递到复合材料修复层上。
-I
Q/SY 15922013
修复技术选择
4
4. 1 管体缺陷类型
油气管道常见管体缺陷包括:泄漏(包括打孔盗油泄漏)、外腐蚀、内部缺陷或腐蚀、管体凿槽或其他金属损失、电弧烧伤或夹渣、回坑、硬点、裂纹、焊缝缺陷、皱弯或弯曲缺陷、砂眼及氢致裂纹。 4. 2 常用修复技术
管体缺陷常用修复技术包括:打磨、堆焊、补板、A型套筒、B型套筒、环氧钢套筒、复合材料、机械夹具及换管修复技术,具体介绍参见附录A。对于管体打孔盗油(气)泄漏,常采用管帽或补板修复,具体介绍参见附录B
油气管体不同缺陷类型宜选用的修复技术见表1。
表1油气管体不同缺陷类型与修复技术对应表
缺陷类型 打磨 推焊 补板 A 型 B型 环氧钢 复合 机械 换管
套筒 套筒 材料 夹具
否 永久 永久 否 临时 永久 修复
香 否 永久 套筒
泄漏或缺陷深度
永久 永久 永久 永久 永久 修复 修复
>0. 81 广蚀深度
修复
修复 修复
外腐蚀 点蚀深度 <0. 8I 永久
修复 修复 修复 修复 修复 修复 否 永久 修复
否
否 永久 永久 否 否 永久
否 否 修复 永久
焊缝损伤 否 否 秀 否 修复
修复否 否
修复
≥>0. 81
内部缺陷或腐蚀 否 否 香 永久 修复 永久
永久 否
永久 永久 修复
或腐蚀
永久
修复 修复 修复 修复” 香 香
其他金属损失 修复 修复 修复' 修复 修复 修复 修复 否 永久
管体凿槽或 永久 永久 永久 永久 永久 永久 永久
电弧烧伤、夹清 永久 永久 否 永久 永久 永久 永久 否 承久 修复
修复 修复
修复 修复 修复 修复
修复否 修复秀 永久
管体有应力集中的凹坑管体回坑深度环焊缝有应力 永久硬点裂纹深度 永久 永久
否 否 修复“. 永久 修复 永久 修复. 永久 永久
(深度<6%D) 修复 永久大于6%D 否 否 香 否 临时 修复 否 否
永久修复
[
集中的四坑 修复 否 否 香 修复 永久 否 否 否 修复
香
香 香 香 水久 水久 永久 香 香 永久
修复 修复
<0. 4r 修复 修复 香 修复 永久 修复 修复
永久 永久 永久 否 永久 修复
修复 修复
修复修复
裂
纹 裂纹深度 0. 4/≤ 否 永久 香 永久 永久 永久 永久 否 永久
修复 修复 修复· 修复
修复
<0. 8
2
Q/SY 1592—2013
表1(续)
缺陷类型 打席 堆焊 补板 A型 B 型 环氧钢
复合 机械 换管
套筒 套筒 套筒 材料
修复
修复 香 香 修复 永久 永久 修复 永久 修复 永久 爽具
永久
否 修复 永久
体积型缺陷
修复
焊缝 线缺陷 永久 否 香 永久 永久 永久 永久 否 永久
修复
缺陷
修复 修复” 修复 修复
修复否否
电阻焊焊
缝缺陷 否 否 否 否 修复 永久 否 否
否否
否 香 否 否 否 永久
环焊缝缺陷 修复“ 永久
皱弯、弯曲缺陷 否 否 香 否 修复 永久 修复: 永久 修复砂眼、氢致裂纹 否 否 永久 永久 永久 永久 否 否 否
否 否 否
修复 修复 修复 修复
注:1—管壁厚度,单位为毫米( (mm);D管体直径, 单位为毫米(mm), ·结合柔性堵漏夹具进行修复。 、缺陷长度应小于其扩展临界值。 :内部缺陷或腐蚀不会继续发展超出临界值。 “如果缺陷金属的去除量满足要求,打磨深度最大为0.4。 如果打磨清理缺陷部位,检测合格后,可修复深度小于0.81的缺陷。 「修复前,宜打磨清理缺陷部位且检测合格。 ,宜填充四坑,且进行疲劳评估。 "最大凹坑尺寸应满足规范要求。 打磨尺寸应满足规范要求。 )打磨去除缺陷,且焊接修复前后都应检测缺陷。 、套筒简设计应与管道缺陷形状、尺寸相符。 该修复技术在常规条件下不推荐,但非禁止项,在特定的情况下可以适用,需预先进行适用性评估。
5 管体缺陷修复 5.1 管体缺陷修复原则 5.1.1对于油气管道管体缺陷,若为体积型缺陷,应进行评价后确定是否需要修复,一般采用修复系数确定。当评估预测失效压力小于或等于1.1倍设计压力时,应立即修复;当评估预测失效压力大于1.1倍设计压力且小于或等于1.2倍设计压力时,应在1年内修复完成。一般情况下,大面积损伤壁厚达到20%~25%以上,立即进行修复,焊缝异常立即进行修复,凹坑深度大于6%管径立即进行修复。 5. 1. 2 管体缺陷修复技术中涉及焊接作业,应制定相应的焊接工艺评定和焊接工艺规程,才能施焊。 5. 2 管体泄漏 5.2.1 油气管道管体发生泄漏,或管体缺陷深度大于80%管道壁厚,可采用机械夹具临时修复,采用B型套筒、环氧钢套筒与柔性夹具组合或换管进行永久修复。B型套筒修复技术说明参见A.2.4。 5.2.2B型套简修复输气管道时,应泄压排气后进行焊接;修复输油管道时,修复作业时管道运行压力不应超过下列压力中的最低值
3
Q/SY 1592—2013
通过修复工艺所要求的压力评估计算值,但不超过0.8倍的运行压力 0.3倍的管道最小届服强度。 可安全排出或容许泄漏液体时的压力。
其中,对于输油管道,运行压力为近两个月内的最高运行压力;对于输气管道,运行压力为一年内的最高运行压力。 5. 2. 3 换管修复前,应保证管道已经降压到0.8倍的运行压力,缺陷管段已排空气体(若是油介质应排干),切除管道时,切除位置离缺陷或泄漏处顶端至少有100mm的距离,切除的管道长度应超过管道直径的3倍。 5.3 管体外腐蚀 5.3. 1 油气管道管体的外部金属损失小于80%管道壁厚,可采用堆焊、补板、A型套筒、B型套筒、环氧钢套筒、复合材料或换管修复中的任意一种技术,进行永久修复。堆焊修复时,油气管道剩余壁厚应大于或等于3.2mm。A型套筒修复技术说明参见A.2.3。 5.3.2油气管道管体的点蚀深度大于或等于80%管道壁厚,可采用补板、B型套筒、环氧钢套筒与柔性夹具组合或换管进行永久修复。补板和B型套筒修复时,输油管道压力应降低到通过修复工艺所要求的压力评估计算值,但不超过0.8倍的运行压力,输气管道应停气泄压后进行。 5.3.3油气管道管体的焊缝存在损伤或腐蚀时,宜采用B型套筒或复合材料永久修复。B型套简修复时,应确保缺陷长度小于其扩展临界值。复合材料修复时,以缺陷部位为中心进行缠绕,确保纤维与管道轴向垂直;修复时应尽量减少修复层的接头数量, 5.3.4B型套筒修复管体外腐蚀时,其侧焊缝和末端角焊缝应全焊透,相邻套简的末端角焊缝距离不应小于率个管径。 5.3.5换管修复前,应保证管道已经降压到0.8倍的运行压力,缺陷管段已排空气体(若是油介质应排干),切除管道时,切除位置离缺陷或泄漏处顶端至少有100mm的距离,切除的管道长度应超过管道直径的3倍。 5. 4 管体内部缺陷或腐蚀 5.4.1油气管道管体内部存在缺陷或腐蚀时,若内部缺陷或腐蚀不会继续发展超出其临界值,可采用A型套筒、环氧钢套筒或复合材料进行永久修复;否则,可采用B型套筒永久修复。 5.4.2A型套筒和B型套筒修复时,应确保套筒和缺陷部位紧密配合;B型套筒的侧焊缝和末端角焊缝应全焊透,相邻套筒的末端角焊缝距离不应小于0.5个管径。 5.5 管体凿槽或其他金属损失 5.5.1油气管道的管体存在凿槽或其他金属损失时,如果缺陷金属的去除量满足要求,可采用打磨修复,打磨深度最大为40%的管体壁厚。如果打磨清理缺陷部位后,检测合格,可采用B型套筒永久修复;否则,采用换管修复。 5. 5.2 如果管体缺陷深度小于80%壁厚,打磨清理缺陷部位,检测合格后,可采用堆焊、补板、A 型套筒、环氧钢套筒和复合材料中的任意一种技术,进行永久修复。 5. 6 管体电弧烧伤、夹渣 5.6.1油气管道的管体存在电弧烧伤、夹渣时,可采用A型套筒、B型套筒、环氧钢套筒或换管进行永久修复;如果缺陷金属的去除量满足要求,可采用打磨修复,打磨深度最大为40%的管体壁厚, 5. 6. 2 如果管体缺陷深度小于80%壁厚,打磨清理缺陷部位,检测合格后,可采用堆焊或复合材料进行永久修复
4