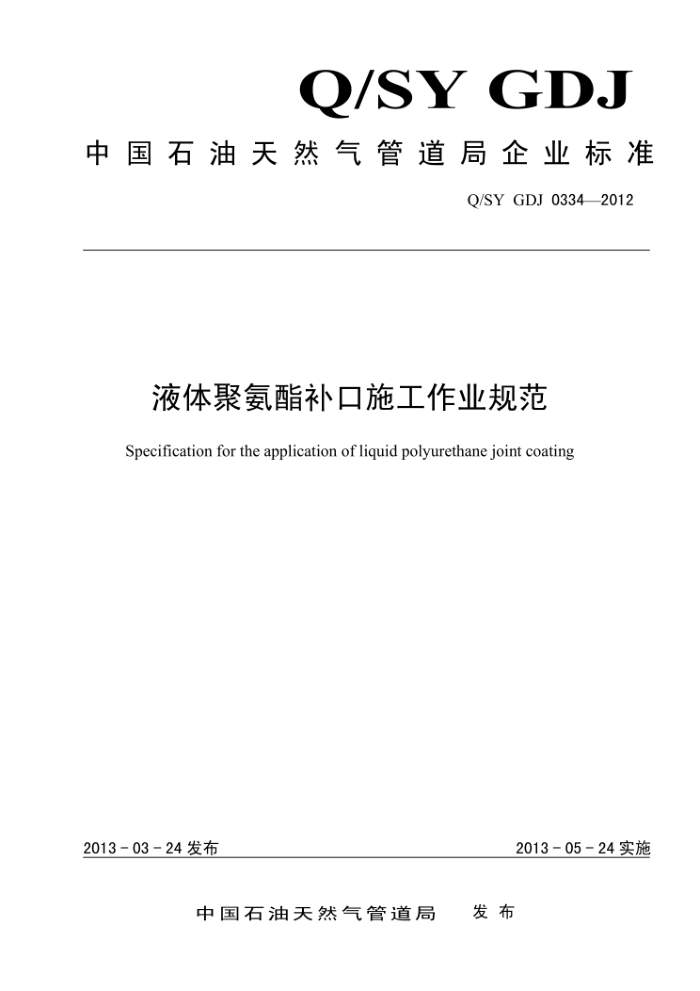
Q/SY GDJ
中国石油天然气管道局企业标准
Q/SY GDJ 03342012
液体聚氨酯补口施工作业规范
Specification for the application of liquid polyurethane joint coating
2013-03-24发布
2013-05-24实施
发布
中国石油天然气管道局
Q/SYGDJ03342012
目 次
前言范围,
II
1 2 规范性引用文件 3 原材料验收与储存
3. 1 - 一般规定 3.2 原材料储存 4施工程序 4. 1 一般规定 4. 2 表面处理程序 4. 3 液体聚氨酯喷涂程序 5质量检验程序 5. 1 一般规定 5. 2 表面处理质量检验 5. 3 涂敷过程检验 5. 4 补口防腐层质量检验 6 修补、 复涂及重涂 6. 1 修补 6. 2 复涂 6.3 重涂 7 健康、 安全与环境保护 7. 1 般规定. 7. 2 喷砂作业要求 7. 3 涂敷作业要求
X
8
9
9
9
交工文件附录A(规范性附录) 工艺试验. 附录B(资料性附录) 质量检查表,
8
9 11 13
Q/SY GDJ03342012
前言
本标准依据GB/T1.1一2009《标准化工作导则第1部分:标准的结构和编写》起草。 本标准由中国石油天然气管道局标准化委员会提出并归口。 本标准起草单位:中油管道防腐工程有限责任公司。 本标准主要起草人:廖宇平、刘毅、王留彬、李晓鹏、龚汉波、武淑倩、牛辉。
II
Q/SYGDJ03342012
液体聚氨酯补口施工作业规范
1范围
本标准规定了埋地钢质管道液体聚氨酯补口施工的材料、机具、施工工艺、安全等的基本要求,以及质量检验的标准。
本标准适用于输送介质温度不大于80℃的管线主体采用三层结构聚烯烃、环氧类防腐层的埋地钢制管道液体聚氨酯补口防腐层的施工及检验。
规范性引用文件
2
下列文件对于本文件的应用是必不可少的。凡是注日期的引用文件,仅所注日期的版本适用于本文
件。凡是不注日期的引用文件,其最新版木(包括所有的修改单)适用于本文件。
GB/T 1724 涂料细度测定法
漆膜、腻子膜干燥时间测定法塑料和硬橡胶使用硬度计测定压痕硬度(邵氏硬度)涂装作业安全规程涂漆工艺安全及其通风净化涂装作业安全规程涂漆前处理工艺安全及其通风净化
GB/T 1728 GB/T 2411 GB 6514 GB 7692 GB/T8923.1涂覆涂料前钢材表面处理表面清洁度的目视测定第1部分未涂覆过的钢材表
面和全面清除原有涂层后的钢材表面的锈蚀等级和处理等级
GB/T18570.3涂覆涂料前钢材表面处理表面清洁度的评定试验 第3部分:涂覆涂料前钢材表
面的灰尘评定(压敏粘带法)
GB/T18570.9 涂覆涂料前钢材表面处理表面清洁度的评定试验 第9部分:水溶性盐的现场电导率测定法
GB/T23257-2009 埋地钢质管道聚乙烯防腐层 SY/T0315-2005 钢质管道单层熔结环氧粉末外涂层技术规范 SY/T0457-2010
钢质管道液体环氧涂料内防腐层技术标准
CDP-G0GP-OP-034-2011-1 埋地钢质管道液体聚氨酯补口防腐层技术规定
3原材料验收与储存
3.1一般规定 3.1.1补口涂敷商应对采购的双组分液体聚氨酯涂料依据补口防腐层工程设计、技术规格书及产品说明书进行检验和验收,检查内容包括涂料产品信息、质量证明文件、产品包装、涂料抽样检查。 3.1.2双组份液体聚氨酯涂料供应商应提供的涂料产品信息包括:产品名称、厂名、批号、生产日期、 保质期限等内容完整的商品标志,安全数据单、产品使用说明书、质量证明书、性能检测报告及出厂合格证。
1
Q/SYGDJ03342012
3.1.3 双组分液体聚氨酯涂料均应包装完好,产品使用说明书内容至少应包括涂料技术指标、涂料的涂敷施工温度、两个组分的配合比例、涂刷型涂料配制后的适用期、涂敷方法、参考用量、运输及储存的注意事项等。 3.1.4对每种牌(型)号的双组分液体聚氨酯涂料,在使用前均应由国家计量认证的第三方检测机构或国外独立实验室出具质量检测报告,检测结果应符合表3.1和表3.2规定的技术要求,报告出具日期应在两年之内。性能达不到规定要求的,不能使用。 3.1.5双组分液体聚氨酯涂料的两个组分应由同一生产商生产或配套提供。对每一生产批次进行抽样检查,同一批次涂料数量超过20吨的批次,每20吨抽查一次。应对首批涂料产品按照表3.1和表3.2 中除第9项常温绝缘电阻之外的性能项目逐项检查;如不合格,则应重新抽查,取样数目加倍,如仍有不合格项,则该批涂料为不合格。以后的每批涂料应按表3.1的全部内容和表3.2中的第2、3、4、5 和8①项进行检查,如不合格,则应重新抽查,取样数目加倍,如仍有不合格项,则该批涂料为不合格。 抽样的检测应在经国家计量认证的实验室进行。
表3.1液体聚氨酯涂料性能指标
序号 1 2
项目细度(μm) 固体含量(%) 喷涂型
指标 ≤100 ≥98 ≤30 ≤2 ≤1.5 ≤6
测试方法 GB/T 1724
SY/T0457-2010附录A
表干(min) 实干(h) 表干(h) 实干(h)
干燥时间 (23±1)℃
GB/T 1728
3
刷涂型
表3.2液体聚氨酯补口防腐层性能指标、b 项目
序号
指标平整、光滑、 无漏涂、无流挂、无气泡、 无色斑
测试方法
外观
目视检查
1
(23±2)℃(J/mm) (-5+3) ℃(J/mm) (23±2) ℃(mm) 设计最高温度(%)°
≥5 ≥3 ≤0.2 30
GB/T23257-2009附录K
抗冲击
2
(8kv检漏无漏点)
压痕
GB/T23257-2009附录G
3
≥70且符合生产厂要求
硬度(邵氏D)
GB/T 2411
4
对钢管对管体聚烯烃涂层对管体环氧类涂层
≥10.0 ≥3.5 ≥5.0 ≥7.0
(20+2)℃ (MPa)
CDP-G-OGP-OP-034-2011-1
附着力
5
附录A
附若力
(20±2)℃
对钢管
CDP-G-OGP-OP-034-2011-1
6
2
Q/SYGDJ03342012
1.2 m 热收缩带
1.2m
XX
埋深1.6m
图1喷涂补口作业坑尺寸要求a
X 2.2m
交
@1.016m
1.0m
0.6m
0.85m
0.85m
图2喷涂补口作业坑尺寸要求b
4.1.4当存在下列情况之一,且无有效防护措施及加热设备时,不应进行露天补口施工:
雨天、雪天、风沙天;风力超过4级(7.9m/s);相对湿度大于85%;管体表面温度在露点温度以上3℃之内,或者低于涂料生产商推荐的温度。
4.2表面处理程序 4.2.1设备预热 4.2.1.1空压机预热启动。先启动空压机的柴油发动机进行预热,启动前应检查发动机机油、冷却液、 燃油是否达到正常标准。待发动机水温上升后,再启动加载空压机。 4.2.1.2发电机预热启动。中频感应加热可采用中频发电机或工频发电机配中频转换电源供电,涂料预热可采用工频发电机供电启动发电机前检查燃油、冷却液、机油是否满足启动要求。待发动机水温上升后,再运行发电机。
4
Q/SYGDJ03342012
4.2.2中频加热 4.2.2.1将电缆连接到配电柜的相应位置,注意电缆连接必须接触良好。利用车载吊吊起线圈安放到补口部位。 4.2.2.2启动线圈加热,加热温度以工艺试验确定的参数为准。加热停止后将线圈吊离管口。 4.2.3补口部位清理
应清除钢管表面的焊瘤、毛刺等,应将补口部位裸露钢管表面和管体防腐层搭接表面的油污、泥土
等污物清理干净;并应将焊缝表面处理平滑。管体防腐层端部如有翘边、开裂等缺陷时,应对缺陷进行清理,直至防腐层粘接完好处。应对防腐层端部不规则部位进行修磨,使得边沿规整;管体聚烯烃防腐层端面坡面应修磨至低于30°。
4.2.4喷砂前准备 4.2.4.1喷砂罐管路连接加砂。连接喷枪管路时,在满足作业的距离内,砂罐及设备应尽量远离作业面。在气管路和喷砂管路都安装完毕后,再加入干燥的砂子磨料,加砂时应通过滤筛网把砂子倒入砂罐直至砂子加满为止。 4.2.4.2试喷并调整砂阀。准备工作完毕后,打开空气进气阀门,操作手启动开关、开始试喷砂,同时调节砂阀控制出砂量,操作手观察砂子喷射到钢管表面的力度、速度及洁净度来调整适合的出砂量。 4.2.4.3喷砂除锈应采用干燥、清洁的磨料。磨料不应被铁锈、盐分和其它杂质污染。应采用电厂或高炉炉渣(主要成分为硅酸铝或硅酸铁)、棕刚玉或金刚砂等砂料,砂粒应均匀,粒径在0.2mm~2.0mm 之间。 4.2.4.4压缩空气应干燥、洁净。喷砂设备中应包含有脱水、脱油等的净化装置。在每班作业之前,应对压缩空气质量进行测试,朝一张白色的纸垫喷气约一分钟,纸面无可见油、水痕迹, 4.2.5喷砂作业 4.2.5.1补口部位钢管表面应进行喷砂除锈,除锈等级应达到GB/T8923.1规定的Sa2.5级,表面锚纹深度应达到50um~110μm。 4.2.5.2焊口两边管体防腐层搭接面也应进行喷砂处理。首先快速扫射一遍,然后观察管体防腐层表面状态的合格程度才能再次喷射,避免管体防腐层产生细小毛刺。观察管体聚烯烃防腐层表面的喷砂处理应均匀,形成粗糙表面,无可见的光滑部位,无毛渣、毛刺,搭接面的处理宽度宜超出搭接宽度20mr 以上;对管体环氧粉末防腐层表面的喷砂处理应均匀,无可见的光滑部位,并应避免管体环氧粉末防腐层过度减薄,甚至出现漏点。 4.2.5.3表面处理后,应采用压缩空气将补口部位钢管表面和管体防腐层搭接面上的砂粒、尘埃、锈粉等清除干净,补口部位钢管表面灰尘等级不应超过GB/T18570.3规定的2级:管体防腐层搭接面清洁,呈现防腐层本体颜色。 4.2.5.4喷砂处理后,可对聚烯烃搭接表面采用火焰加热或其它方式处理,加热温度控制在90℃~110 ℃,提高补口涂料对聚烯烃防腐层的润湿能力。 4.2.5.5定向钻穿越段补口涂装作业时,宜对聚烯烃搭接面采用火焰极化、电晕极化或氧化性气体极化处理,提高补口涂料对聚乙烯防腐层的润湿能力。 4.2.5.6表面处理后应随即进行补口涂装,间隔时间应不超过2h。表面处理后至喷涂前不应出现浮锈如出现返锈或表面污染时,应重新进行表面处理。
5