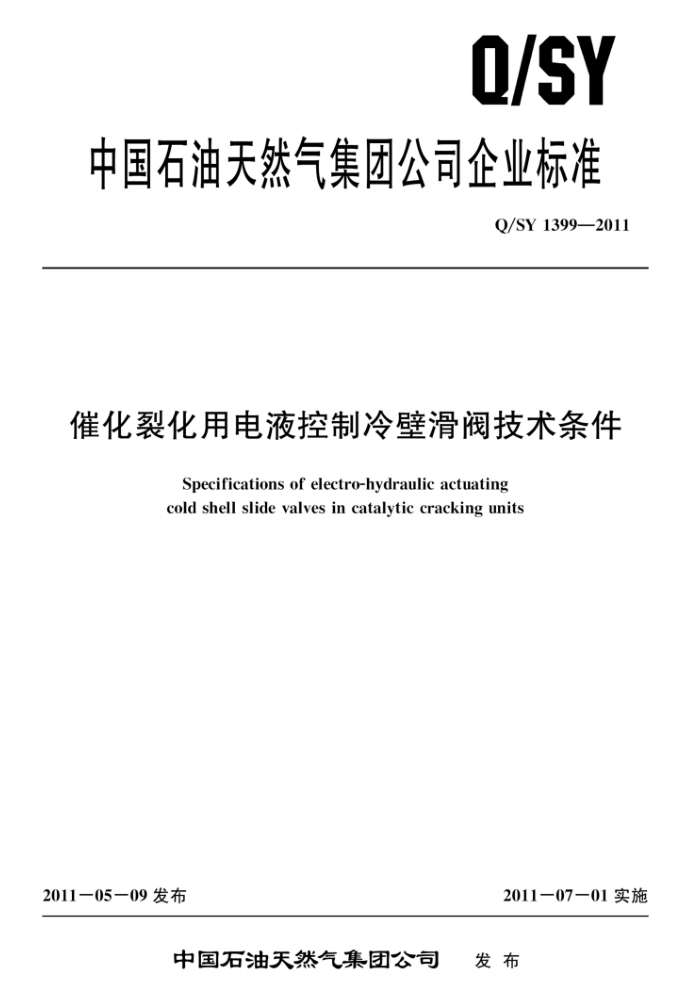
Q/SY
中国石油天然气集团公司企业标准
Q/SY 1399—2011
催化裂化用电液控制冷壁滑阀技术条件
Specifications of electro-hydraulic actuating cold shell slide valves in catalytic cracking units
2011一05一09 发布
2011一07一01实施
中国石油天然气集团公司 发布
Q/SY 1399—2011
目 次
前言
范围 2 规范性引用文件 3 术语和定义 4 型式、分类及型号 5 要求 6 试验及试验方法 7 检验规则
N
涂饰、标志、包装、贮运附录A(规范性附录) 滑阀耐磨零件表面堆焊钻铬钨硬质合金的表面质量技术条件参考文献
8
10
12 13
Q/SY 1399—2011
前言
本标准依据GB/T 1.1一2009给出的规则起草本标准由中国石油天然气集团公司标准化委员会石油化工设备与材料专业标准化技术委员会提出
并归口。
本标准起草单位:渤海石油装备制造有限公司本标准主要起草人:张玉峰、刘晓东、戚达强、冉文浩、张银、梁宗辉、赵凯维、胡安铎、邓
纯萍。
II
Q/SY 1399—2011
3. 1
线性度linearity 在全行程范围内,某一试验点上输入信号对应的实际位移与理论位移的最大差值与全行程之比,
用相对误差表示。 3. 2
灵敏度sensitivity 在全行程范围内引起输出位移最小变化的输入信号最大变化值与理论输入信号全量程之比,用相
对值表示。 3.3
分辨率resolution 引起信号最小变化的最大位移变化值与理论全行程之比,用相对值表示。
4型式、分类及型号
4.1 分类
电液控制冷壁滑阀由阀体部分及电液执行机构组成。根据电液滑阀阀板数量的不同,分为单动滑阀和双动滑阀两类,如图1和图2所示。
4.2型式
单动滑阀为上进气下排气;双动滑阀有上进气下排气和下进气上排气两种结构。 4.3型号 4.3.1 型号表示方法
D s
D
F
/
滑阀公称尺寸同一公称尺寸滑阀不同开口面积(按罗马数字顺序排) D代表单动滑阀,S 代表双动滑阀滑阀冷壁电液控制
4.3.2型号示例
规格为 Φ1000mm、开口面积为第 3种尺寸的单动滑阀:DLFDⅢ1000。规格为Φ1500mm、开口面积为第2种尺寸的双动滑阀:DLFSⅡ1500。
5要求
5.1 设计要求 5.1.1环境条件如下: 2
Q/SY 1399—2011
动操作机构
8
5
6
1一阀体:2一节流锥:3一阀座圈:4一导轨:5一阀板:6一阀杆:7一阀盖:8一手动机构:9一油缸
图 1 单动滑阀简图
国国
9
18
6
1一阀体;2—节流锥;3一阀座圈;4一导轨;5一阀板;6一阀杆;7一阀盖;8一手动机构;9一油缸
图2双动滑阀简图
a)单动滑阀安装在催化剂的循环管线上,管线应是垂直的或最大倾斜度不应大于 40°。双动滑
阀应安装在末级分离器出口的垂直管线上。 b) 滑阀的进入及排出口的管线直径应与滑阀相同,直径≥300 mm口径的滑阀与管线应用焊接
连接。 电液执行机构要求周围环境无腐蚀性介质存在,温度-40℃~60℃,相对湿度90%以下 (25℃时)。适用于炼油I 区的Ⅱ B级 Ti~T3组爆炸性气体混合物可能存在的爆炸性危险场所。
c)
5.1.2性能要求如下:
a) 阀体部分设计参数见表1。 b) 电液执行机构性能:
3
Q/SY 1399—2011
1) 线性度:不低于1/1000。 2) 灵敏度:不低于1/1000。 3) 分辨率:不低于1/1000。 4) 行程速度:正常 25mm/s,最大 100mm/s 5) 有效行程:应比所配滑阀的行程大20mm~30mm。 6) 在最低油压下,输出力(推力或拉力)应满足滑阀所需的驱动力。
表1阀体部分设计参数
类型
单位 MPa MPa ℃
参数设计压力设计压差
单动滑阀 ≤0.5 0. 2~0. 35 ≤350 720~900 100~150
双动滑阀 ≤0.5 0. 2~0. 35 ≤350 720~900 100~150
壳体内件
设计温度
℃ mm mm
双层衬里厚度耐磨层衬里厚度
20 催化剂
20 再生烟气
通过介质
5.1.3阀体部分与电液执行机构的连接:
阀体部分与电液执行机构、支架的连接应采用带凸缘对中的刚性连接,阀杆与活塞杆的连接应采用带有锁紧的螺纹和法兰连接。 5.1.4每台单动滑阀的流道阀口面积应根据介质的操作参数进行单独的专门设计计算,并从调节性能、抗冲刷、寿命等方面综合比较以确定阀口的形状。 5.1.5阀体的要求如下:
a) 阀体进口的上游应设计有节流锥,保证介质的最小流动阻力。节流锥的内表面应衬有龟甲网
加固的单层耐磨衬里,壳体的其余内表面应衬有龟甲网锚固的耐磨、隔热的双层衬里。 b) 壳体应用钢板焊接,钢板应用Q345R,Q245R等材料。壳体为三通或四通结构,两侧筒
体可采用圆形或长方形,圆形侧筒体应采用标准法兰,PN应不小于2.5MPa,长方形侧筒体下端应为30°倾斜,筒体的大小应保证内部零件方便地取出。阀体的两侧应设计有吊耳。
5.1.6阀盖应能与阀体侧筒体法兰匹配,为圆形或长方形。填料函应用串联式的双填料结构,设有带阀门的液体填料注入口,填料函前端应设有蒸汽吹扫入口,内设有阀杆保护套。长方形阀盖法兰每端应设有两个定位销,以保证对中定位,法兰的上方必须设计有吊耳。 5.1.7阀杆为整体锻造,T型头部,带有45°倒角的倒密封和限位台。阀杆主体部分表面应喷焊硬质合金,加工后厚度≥0.5mm,硬度≥HRC50。阀杆材料根据设计温度不同,可选用NS112, 4Cr14Ni14W2Mo, 0Cr18Ni12Mo2Ti。 5.1.8导轨应为L型或 U型。与阀板接触的滑动表面和迎介质冲刷面应堆焊钻钴铬钨硬质合金,堆焊层加工后厚度≥3mm,硬度≥HRC40。导轨材料根据设计温度不同可选用NS112,06Cr19Ni10。 5.1.9阀板为平板状,上平面应带有龟甲网加固的耐磨衬里,前端衬里应有隔板加固。阀板两侧及与导轨的滑动接触面必须堆焊钻钴铬钨硬质合金,堆焊层加工后厚度≥3mm,硬度≥HRC40。在设计最大压差下,阀板的挠度不应大于0.13mm。 5.1.10阀座圈:双动滑阀阀座圈的流道口应为长方形;单动滑阀阀座圈的流道口应为梯形或矩形, N
Q/SY 1399—2011
前沿应为半圆形。流道口的所有角应为圆形,R30mm~50mm。流道口的周边及底面应衬有隔板加固的耐磨衬里。 5.1.11高温螺栓:阀座圈与阀体、导轨与阀座圈连接螺栓材料,双头螺柱可选用NS112(使用温度<900℃),0Cr18Ni12Mo2Ti(使用温度<720℃);螺母可选用06Cr19Ni10等。 5.1.125.1.5a)的要求也适合热壁滑阀,但应把双层衬里改为以龟甲网锚固的单层衬里。阀盖、阀杆、导轨、阀板、阀座圈、高温螺栓的要求也适合热壁滑阀。 5.1.13电液执行机构的要求如下:
a)电液执行机构应为分离式,即伺服油缸和手动机构组装在滑阀阀体上,压力油源及电液控制
部分为一独立单元,与伺服油缸之间用耐压管线连接。 b)电液执行机构应配置一个带离合器的手轮蜗轮蜗杆式手动机构,手动机构设计应保证在不
影响手轮操作的情况下,能把伺服油缸或执行机构从阀上拆卸。 c)[ 电液控制系统应接收4mA~20mA输人控制信号和输出4mA~20mA的阀位信号,具有正
反作用的选择和行程大小的调整、零位的调整、行程速度的调整。 d)电液执行机构应具备自动锁位功能:信号丢失、反馈丢失或跟踪丢失等电气控制系统任一
故障时,执行机构应立即自动锁位。 e) 电液执行机构应具备装置事故时的自保联锁功能。 f) 自动报警及显示:信号丢失、反馈丢失、跟踪丢失、液压油压低、备用蓄能器压力低、油箱
油温高、油箱油位低、自保投用、推力极限等报警及显示,输入信号、实际阀位等显示。 g)操作功能:中央控制室自控操作、遥控操作、装置紧急自保操作、本地操作、手动机械操
作和快速开关操作。 h)电液执行机构的电气控制系统防爆等级:dⅡBT3,如采用非防爆元件,应安装在防爆等级
dIⅡBT3 的控制箱内。 i)手动机构的支架端部和电液控制柜的上方应设有吊环。
5.1.14对于DN500以下口径的调节流量滑阀或切断用单动滑阀也可以采用气动执行机构。气动执行机构的性能必须保证滑阀所需的驱动力,灵敏度不低于1/200,精度不低于1/100,回差不低于1/100。
5.2制造要求 5.2.1 技术依据
电液滑阀的制造除应符合本标准的规定外,还应符合经规定程序批准的产品图样和工艺技术文件的规定。
5.2.2材料和外购件
5.2.2.1电液滑阀主要零件用材料应符合如下规定:
板材、管材、棒材应分别符合GB/T 699,GB/T 700,GB/T710,GB/T 711,GB/T 713,GB/ T1220,GB/T1221,GB/T3077和GB/T3280的规定。在保证产品性能的条件下,允许用其他材料代替。 5.2.2.2电液滑阀主要外购件应符合如下规定:
a)外购的电子电气元件应符合GB5226.1的规定。 b)外购的液压元件应符合GB/T 7935 的规定
5.2.2.3电液滑阀所用板材、管材、棒材、外购的机械零件和部件、电子电气元件、液压元件等,均应有生产厂的检验合格证和质量证明书。
5