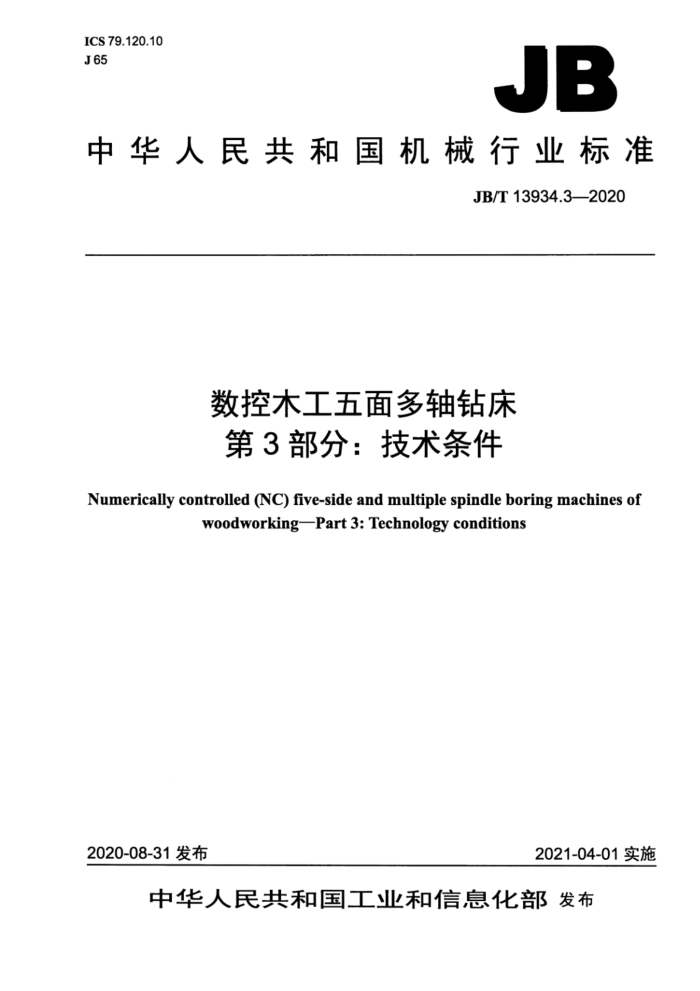
JB
中华人民共和国机械行业标准
JB/T13934.3—2020
数控木工五面多轴钻床第3部分:技术条件
Numerically controlled (NC) five-side and multiple spindle boring machines of
woodworkingPart 3: Technology conditions
2020-08-31发布
2021-04-01实施
目 次
前言 1范围. 2规范性引用文件 3 参数 4要求,
I
4.1 一般要求 4.2 关键零部件加工要求. 4.3 气动和润滑系统要求. 4.4 电气设备及数控系统要求 4.5 装配要求. 4.6 温升及空运转功率 4.7 精度要求. 4.8 安全要求. 4.9 外观要求 5试验方法 5.1 试验条件 5.2 外观检验. 5.3 润滑系统检验.. 5.4 气动系统检验· 5.5 电气设备检验. 5.6 参数检验.. 5.7 装配检验 5.8 基本性能检验. 5.9 安全检验.. 5.10 精度检验. 5.11 空运转试验 5.12 负载试验.. 6检验规则 6.1 检验分类.. 6.2 出厂检验. 6.3 型式检验 7标志、包装、随机文件、运输和贮存 7.1 标志. 7.2 包装. 7.3 随机文件 7.4运输
云上
6
6 E
前言
JB/T13934《数控木工五面多轴钻床》分为三个部分:
一第1部分:参数;一第2部分:精度;一第3部分:技术条件。 本部分为JB/T13934的第3部分本部分按照GB/T1.1一2009给出的规则起草。 本部分由中国机械工业联合会提出。 本部分由全国木工机床与刀具标准化技术委员会(SAC/TC84)归口。 本部分起草单位:南兴装备股份有限公司、福州木工机床研究所、顺德职业技术学院、广东产品质
量监督检验研究院、佛山市豪伟德机械有限公司、佛山市顺德区迈盛达自动化机械有限公司。
本部分主要起草人:韦国平、肖晓晖、丁红珍、成绵龙、刘敬盛、方德明。 本部分为首次发布。
数控木工五面多轴钻床第3部分:技术条件
1范围
JB/T13934的本部分规定了数控木工五面多轴钻床的参数、要求、试验方法、检验规则、标志,包装、随机文件、运输和贮存。
本部分适用于数控木工五面多轴钻床(以下简称机床)。
2规范性引用文件
下列文件对于本文件的应用是必不可少的。凡是注日期的引用文件,仅注日期的版本适用于本文件。凡是不注日期的引用文件,其最新版本(包括所有的修改单)适用于本文件。
GB/T191包装储运图示标志 GB2893安全色 GB2894安全标志及其使用导则 GB/T3077合金结构钢 GB/T5226.1机械电气安全机械电气设备第1部分:通用技术条件 GB/T6414一2017铸件尺寸公差、几何公差与机械加工余量 GB/T6576机床润滑系统 GB/T7932气动对系统及其元件的一般规则和安全要求 GB/T9239.1-2006机械振动恒态(刚性)转子平衡品质要求 第1部分:规范与平衡允差的
检验
GB/T9969工业产品使用说明书总则 GB/T10961木工机床操作指示形象化符号 GB12557木工机床安全通则 GB/T14384木工机床通用技术条件 GB22659木工机床安全数控钻床和数控镂铣机 GB/T26220工业自动化系统与集成机床数值控制数控系统通用技术条件 JB/T8356机床包装技术条件 JB/T9953木工机床噪声声压级测量方法 JB/T13934.1--2020数控木工五面多轴钻床 第1部分:参数 JB/T13934.2—2020数控木工五面多轴钻床 第2部分:精度
3参数
机床的主要参数应符合JB/T13934.1一2020的规定。
4要求
4.1一般要求
4.1.1机床除应符合本部分的规定外,还应符合GB/T14384的规定。在按本部分验收机床时,同时对 GB/T14384中未经本部分具体化的其余验收项目进行检验。 4.1.2机床应按经规定程序批准的图样和技术文件制造。 4.1.3机床出厂时应保证其完整性,并备有正常使用和维修所需的专用附件及备用易损件,特殊附件由用户和制造厂共同商定,随机供应或单独订货。 4.1.4机床出厂应保证配套的外购件(包括电气、气动元件等)符合现行标准并取得合格证,同时须与主机同时进行运转试验。 4.2关键零部件加工要求 4.2.1主轴应采用GB/T3077规定的40Cr合金钢或力学性能相当的其他钢材制造。 4.2.2铸件精度不应低于GB/T6414-2017规定的DCTG11级。 4.2.3机床的刀具主轴电动机带轮和与之传动的带轮应按GB/T9239.1一2006的规定进行动平衡检查,平衡品质等级不应低于G6.3级要求。 4.2.4机床的直线移动导轨、齿条、滚动丝杠,以及纵向滑动导轨、横向滑动导轨等所有滑动导轨的工作表面应经耐磨、耐腐蚀处理,表面硬度应不低于60HRC。 4.3气动和润滑系统要求 4.3.1机床的气动系统应符合GB/T7932的规定。 4.3.2气动系统密封应可靠,不应有渗漏和冲击现象。 4.3.3机床的润滑系统应符合GB/T6576的规定。 4.4电气设备及数控系统要求 4.4.1机床的电气设备应符合GB/T5226.1的规定。 4.4.2机床应集成有CAD/CAM软件并能与数控系统相兼容 4.4.3机床的数控系统应符合GB/T26220的规定,数控装置的平均无故障工作时间应不少于5000h,且数控系统应具有以下基本功能:
应具备单项定位功能应限制数控轴可以运行的范围。 应具有补偿数据、修正误差的功能。 应具有自动退让的控制功能。 应具有自动寻参考点的功能,寻参考点速度应采用低速。 应提供示教功能代替寻参考点操作。 一应具备计数控制功能。 应至少具备手动、自动操作模式。 断电后,应能保存加工相关数据。 应提供监控数字量I/O端口状态的方法。 至少应为下述系统部件提供诊断的方法: ·输入端口;
·显示部件: ·数据存储器。
4.5装配要求
4.5.1机床装配前所有零件均应进行防锈和清洁处理。 4.5.2机床不应安装图样未规定的垫片调整螺钉等。 4.5.3机床的移动导轨副、滚珠丝杠副、滑动导轨副等组装后应运动轻便、灵活,无阻滞现象。 4.5.4机床的直线移动导轨、纵向滑动导轨(X轴方向)、齿条与床身的结合面,横向滑动导轨(Y轴方向横向滚动丝杠、升降导轨座体与移动横梁的结合面等重要固定结合面应紧密贴合,允许塞入塞尺的厚度不应大于0.04mm,塞尺塞入深度不应大于接触面宽的1/4,接触面间可塞入部位累计长度不应大于周长的1/10。 4.6温升及空运转功率 4.6.1机床主轴轴承达到稳定温度后,其最高温度应不超过70℃,温升应不超过40℃。 4.6.2机床主传动系统空运转功率(不包括电动机空运转功率)应不超过主轴电动机额定功率的30%。 4.7精度要求
机床的精度应符合JB/T13934.2一2020的规定。 4.8安全要求 4.8.1机床的电气和结构安全应符合GB/T5226.1、GB12557、GB22659的规定。 4.8.2凡能触及运动部件的部位均应设置防护装置,防护隔离装置打开时,运动部件应不能启动。 4.8.3机床应设置危险区域,当有人员进入危险区域时应自动停机。 4.8.4在靠近操作者位置的地方应配有急停按钮,并在机身或操作台上有明显的安全提示标志。 4.8.5排钻盒在纵向、横向、垂直方面三个方向移动(X轴、Y轴、Z轴)至导轨两端极限位置时,应有限位保护装置。 4.8.6换刀机构运转到换刀区并进行上升、下降换刀动作时,各极限位置应有缓冲装置。 4.8.7 当气压系统工作压力小于规定值时,机床应不能启动或应自动停机。 4.8.8 机床空运转噪声最大声压级不应超过85dB(A)。 4.8.97 机床应具备有效收集、排放木屑和粉尘的措施,并在使用说明书中说明所需配备吸尘装置的最小风量。 4.9外观要求 4.9.17 机床外观表面平整,不应出现粗糙不平和其他凹凸缺陷及损伤。 4.9.2 机床的防护罩应平整匀称,不应翘曲、凹陷。 4.9.3 机床零部件内外结合面的边缘应平整、焊接牢固,焊缝应修整平直、均匀。 4.9.4 机床外露零部件表面不应有磕碰、锈蚀,外露标准件应做镀锌、发黑等表面处理。 4.9.5 机床的镀锌、发黑应色调一致,防护层不应有褪色、脱落现象。 4.9.6 机床涂漆层应无明显色差,漆膜外观应无明显流挂、起泡及发白现象。 4.9.7 机床上的各种标识应清晰耐久,铭牌应固定在明显位置。
5试验方法
5.1试验条件
机床在试验前应按4.5的要求完成装配并调整好水平,工作台面纵横向水平度误差在1000mm测量长度上不大于0.10mm。机床数控系统应按有关标准的规定进行开机前的调试、检测等试运行工作。 5.2外观检验
采用目测及通用量具进行检验。 5.3润滑系统检验
按GB/T6576的规定进行。 5.4气动系统检验
按GB/T7932的规定进行。 5.5电气设备检验
按GB/T5226.1的规定进行。 5.6参数检验
机床参数按JB/T13934.1一2020的规定执行。在空运转条件下,采用通用量具进行测量,参数偏差不应超过公称值的士10%。 5.7装配检验
采用水平仪等水平检测器具,塞尺及目测方法进行检验。 5.8基本性能检验
机床在空运转试验前或空运转试验过程中,应检查以下基本性能: a)检查机床各项防护装置是否安全可靠; b)检查机床刀具主轴运行动作是否平稳、可靠,其运动行程到达限位位置时能否自动回程: c)检查机床工件夹紧装置动作是否灵活、可靠; d)检查机床换刀机构进行换刀动作时是否灵活、准确、可靠,在换刀行程的进给、回程两端位置
是否具有限位装置: e)检查机床刀具定位起始点及刀具加工开始点的运行动作是否灵活、可靠,位置准确: f)检查机床数控系统各项功能是否运行正常: g)检查机床集成的CAD/CAM软件各项功能是否运行正常。
5.9安全检验
采用目测方法并在空运转试验中进行检验。 5.10精度检验
机床精度检验按JB/T13934.2一2020的规定,在空运转试验后进行。
5.11空运转试验 5.11.1试验目的和一般要求 5.11.1.1空运转试验是在无负荷状态下运转机床,检验各机构的运转状态、安全性、温度变化、空运转功率、噪声以及操纵机构动作是否灵活、平稳、可靠。 5.11.1.2试验时,机床的主传动机构应按技术文件规定的速度范围,从最低转速起依次运转,应做包括低,中、高速在内的不少于10种转速的运转,各种转速的运转时间不应少于2mi,最高转速运转时间不应少于1h,使主轴轴承达到稳定温度。 5.11.2试验方法 5.11.2.1在靠近主轴定心轴承处测量温度和温升,结果应满足4.6.1的要求。 5.11.2.2采用1级功率表测量空运转功率,结果应满足4.6.2的要求。 5.11.2.3噪声按JB/T9953的规定进行测定。 5.11.2.4按GB/T14384规定的检验方法检查安全防护装置、操纵机构、制动机构的功能和动作是否可靠。 5.11.2.5采用目测检查气动和润滑系统是否工作正常,是否无渗漏,控制系统和指示仪表是否准确、 可靠。 5.11.2.6采用目测检查机床的数控系统各功能是否稳定、可靠。 5.11.2.7反复启动、停止主机和各运转机构10次,检查机床运转的平稳性,灵活性。 5.12负载试验 5.12.1负载试验是检验机床在负载状态下运转时的工作性能及安全性,检验其加工能力、承载能力及运转状态是否符合要求。 5.12.2机床负载试验应在空运转试验合格后进行。 5.12.3机床负载试验应在规定的额定工作条件下,使用含水率不超过10%的中密度纤维板进行,改变进给速度和切削深度,使机床达到主电动机的额定功率。 5.12.4机床负载试验时各机构应运行平稳,气动和润滑系统无渗漏。
6检验规则
6.1检验分类
机床的检验分为出厂检验和型式检验。 6.2出厂检验 6.2.1每台机床均应经制造厂质量检验部门进行出厂检验,检查合格并签发质量检验合格证后方能出厂。 6.2.2出厂检验项目包括:
a)外观检验 b)参数检验; c》装配检验; d)安全检验;