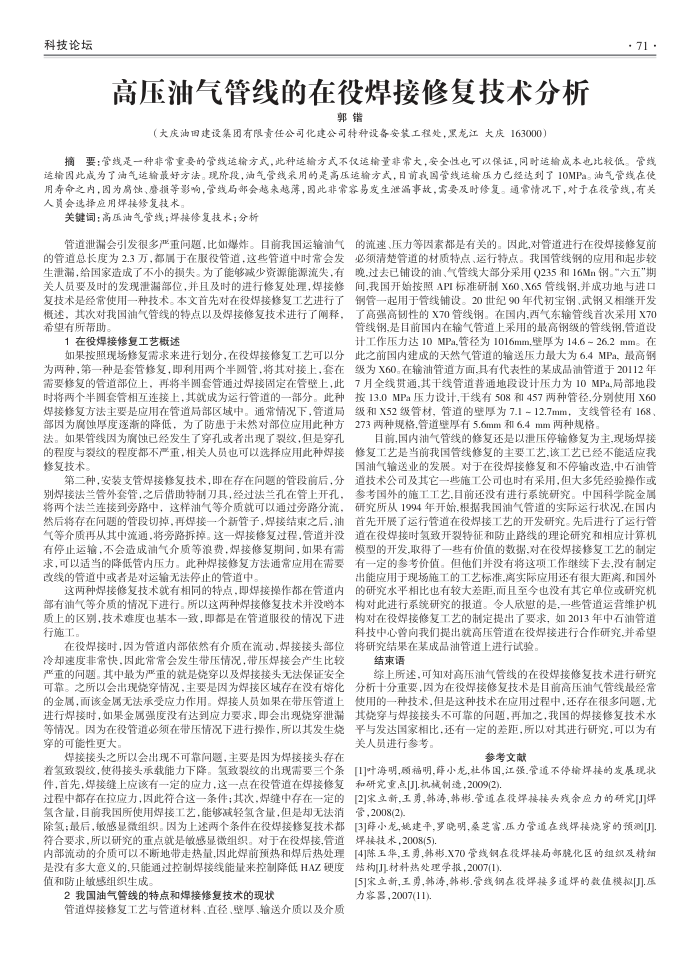
科技论坛
高压油气管线的在役焊接修复技术分析
郭错
(大庆油图建设集因有限责任公司化建公司特种设备安装工程处,黑龙江大庆163000)
· 71 -
摘要:管线是一种非常重要的管线运输方式,此种适输方式不仅运输量非常大,安全性也可以保证,同时适输成本电比较低。管线运输因此成为了油气运输最好方法。现阶段,油气管线采用的是高压运输方式,目前我国管线运输压力已经达到了10MPa。油气管线在使用寿命之内,因为离蚀、亮损等影响,管线局部会越来越薄,固此非常客易发生泄漏事故,需要及时修复。通常情况下,对于在役管线,有关人奠会选择应用焊接修复技术
关键词:高压油气管线:焊接修复技术;分析
管道泄漏会引发很多严重间题,比如煤炸。目前我国运输油气的流速、压力等因素都是有关的。因此对管道进行在役焊接修复前
的管道总长度为2.3万,都属于在服役管道.这些管道中时常会发生泄蒲,给国家造成了不小的损失。为了能够减少资源能源流失,有关人员要及时的发现泄漏部位,并且及时的进行修复处理,焊接修复技术是经常使用一种技术。本文首先对在役焊接修复工艺进行了概述,其次对我国油气管线的特点以及焊接修复技术进行了阐释,希望有所帮助,
1在役焊接修复工艺概述
如果按照现场修复需求来进行划分,在役焊接修复工艺可以分为两种,第一种是套管修复,即利用两个半圆管,将其对接上,套在需要修复的管道部位上,再将半圆套管通过焊接固定在管壁上,此时将两个半圆套管相互连接上,其就成为运行管道的一部分。此种焊接修复方法主要是应用在管道局部区域中。通常情况下,管道局部因为质蚀厚度逐渐的降低,为了防患于未然对部位应用此种方法。如果管线因为腐蚀已经发生了穿孔或者出现了裂纹,但是穿孔的程度与裂纹的程度都不严重,相关人员也可以选择应用此种焊接修复技术。
第二种,安装支管焊接修复技术,即在存在间题的管段前后,分别焊接法兰管外套管,之后借助特制刀其,经过法兰孔在管上开孔,将两个法兰连接到旁路中,这样油气等介质就可以通过旁路分流。然后将存在间题的管段切掉,再焊接一个新管子,焊接结束之后,油气等介质再从其中流通.将旁路拆掉。这一焊接修复过程,管道并没有停止运输,不会造成油气介质等浪费,焊接修复期间,如果有需求,可以适当的降低管内压力。此种焊接修复方法通常应用在需要改线的管道中或者是对运输无法停止的管道中。
这两种焊接修复技术就有相同的特点,即焊接操作都在管道内部有油气等介质的情况下进行。所以这两种焊接修复技术并没哟本质上的区别,技术难度也基本一致,即都是在管道服役的情况下进行施工
在役焊接时,因为管道内部依然有介质在流动,焊接接头部位冷却速度非常快.因此常常会发生带压情况,带压焊接会产生比较
必须清楚管道的材质特点、运行特点。我国管线钢的应用和起步较晚,过去已铺设的油、气管线大部分采用Q235和16Mn钢。“六五"期间,我国开始接照API标准研制X60、X65管线钢,并成功地与进口钢管一起用于管线铺设。20世纪90年代初宝钢、武钢文相继开发了高强高韧性的X70管线钢。在国内,西气东输管线首次采用X70 管线钢,是目前国内在输气管道上采用的最高钢级的管线钢,管道设计工作压力达10MPa,管径为1016mm,壁厚为14.6~26.2mm。在此之前国内建成的天然气管道的输送压力最大为6.4MPa,最高钢级为X60。在输油管道方面.具有代表性的某成品油管道于20112年 7月全线贯通,其干线管道普通地段设计压力为10MPa局部地段按13.0MPa压力设计,干线有508和457两种管径.分别使用X60 级和X52级管材,管道的壁厚为7.1~12.7mm,支线管径有168, 273两种规格,管道壁厚有5.6mm和6.4mm两种规格
目前,国内油气管线的修复还是以泄压停输修复为主,现场焊接修复工艺是当前我国管线修复的主要工艺该工艺已经不能适应我国油气输送业的发展。对于在役焊接修复和不停输改造,中石油管道技术公司及其它一些施工公司也时有采用,但大多凭经验操作或参考国外的施工工艺,目前还没有进行系统研究。中国科学院金属研究所从1994年开始根据我国油气管道的实际运行状况.在国内首先开展了运行管道在役焊接工艺的开发研究。先后进行了运行管道在役焊接时氢致开裂特征和防止路线的理论研究和相应计算机模型的开发,取得了一些有价值的数据,对在役焊接修复工艺的制定有一定的参考价值。但他们并没有将这项工作继续下去,没有制定出能应用于现场施工的工艺标准,离实际应用还有很大距离,和国外的研究水平相比也有较大差距而且至今也没有其它单位或研究机构对此进行系统研究的报道。令人欣慰的是,一些管道运营维护机构对在役焊接修复工艺的制定提出了要求,如2013年中石油管道科技中心曾向我们提出就高压管道在役焊接进行合作研究,并希望将研究结果在某成晶油管道上进行试验。
结束语
综上所述,可知对高压油气管线的在役焊接修复技术进行研究
严重的间题。其中最为严重的就是烧穿以及焊接接头无法保证安全
分析十分重要,因为在役焊接修复技术是目前高压油气管线最经常
可靠。之所以会出现烧穿情况,主要是因为焊接区域存在没有熔化
的金属,而该金属无法承受应力作用。焊接人员如果在带压管道上进行焊接时,如果金属强度没有达到应力要求,即会出现烧穿泄蒲等情况。因为在役管道必须在带压情况下进行操作,所以其发生烧穿的可能性更大。
焊接接头之所以会出现不可靠间题,主要是因为焊接接头存在着氢致裂纹,使得接头承载能力下降。氢致裂纹的出现需要三个条件,首先,焊接缝上应该有一定的应力这一点在役管道在焊接修复过程中都存在拉应力,因此符合这一条件;其次,焊缝中存在一定的氢含量,目前我国所使用焊接工艺,能够减轻氢含量,但是却无法消除氢;最后,撤感显微组织。因为上述两个条件在役焊接修复技术都符合要求,所以研究的重点就是缴感显微组织。对于在役焊接,管道内部流动的介质可以不断地带走热量,因此焊前预热和焊后热处理是没有多大意义的,只能通过控制焊接线能量来控制降低HAZ硬度值和防止敏感组织生成。
2我国油气管线的特点和焊接修复技术的现状
管道焊接修复工艺与管道材料、直径、壁厚、输送介质以及介质
使用的一种技术,但是这种技术在应用过程中,还存在很多间题,尤其烧穿与焊接接头不可靠的间题,再加之,我国的焊接修复技术水平与发达国家相比,还有一定的差距,所以对其进行研究,可以为有关人员进行参考。
参考文献
[1]叶海明,顾福明,薛小龙,壮伟国,江强.管道不停输焊接的发展现状和研究重点[]机械制造,2009(2)。
[2立新,王勇,韩涛,韩彬.管道在役焊接接头残余应力的研究[J焊管,2008(2)
[3]薛小龙,姚建平,罗晓明桑芝富,压力管道在线焊接烧穿的预测[] 烊接技术,2008(5)
[4]陈玉华,王勇,韩彬.X70管线钢在役焊接局部晚化区的组织及精细结构[J]材料热处理学报,2007(1).
[5]宋立新,主勇,韩涛,韩彬.管线钢在役焊接多道焊的数值模拟[].压力容器,2007(11)