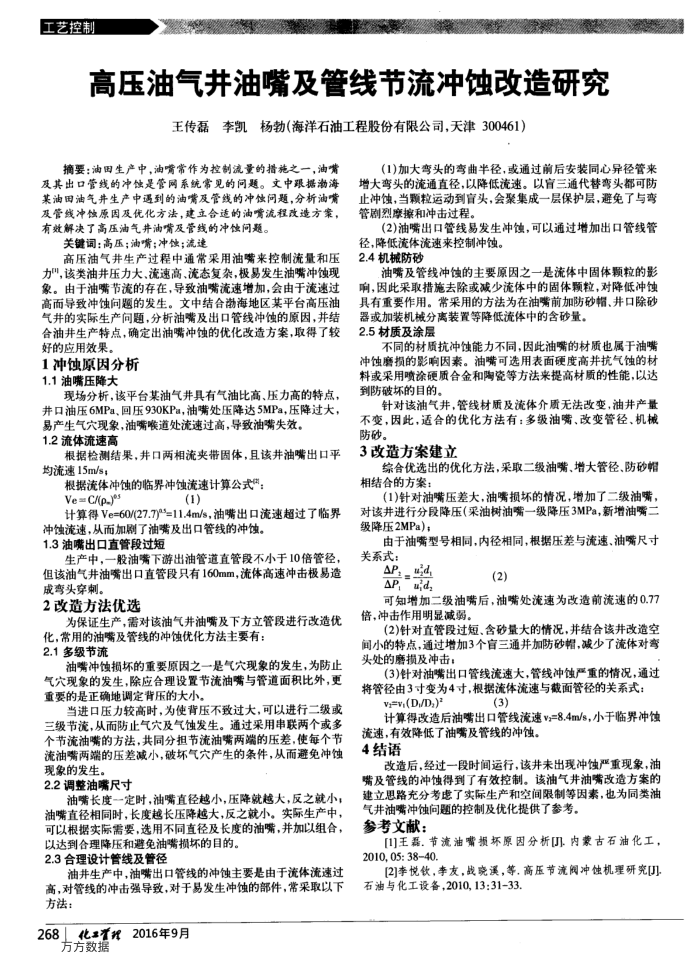
工艺控制
高压油气井油嘴及管线节流冲蚀改造研究
王传磊李凯杨勃(海洋石油工程股份有限公司,天津300461)
摘要:油图生产中,油嘴常作为拉制流量的指施之一,油嘴及其出口管线的冲蚀是管网系统常见的同题。文中跟据激海
(1)加大弯头的弯曲半径,或通过前后安装同心异径管来增大弯头的流通直径,以降低流速。以盲三通代替弯头都可防
某油田油气井生产中遇到的油嘴及管线的冲蚀问题,分析油嘴
止冲蚀,当颗粒运动到盲头,会聚集成一层保护层,避免了与弯
及管线冲蚀原因及优化方法,建立合造的油嘴流程改造方案,
管剧烈摩擦和冲击过程。
有效解决了高压油气井油嘴及管线的冲蚀问题。
关键词:高压;油嘴;冲蚀;流速
高压油气井生产过程中通常果用油嘴来控制流量和压力,该类油井压力大、流速高、流态复杂,极易发生油嘴冲蚀现象。由于油嘴节流的存在,导致油嘴流速增加,会由于流速过高而导致冲蚀向题的发生。文中结合勘海地区某平台高压油气井的实际生产问题,分析油嘴及出口管线冲蚀的原因,并结合油井生产特点,确定出油嘴冲蚀的优化改造方案,取得了较好的应用效果。
1冲蚀原因分析 1.1油嘴压隆大
现场分析,该平台某油气井具有气油比高、压力高的特点,井口油压6MPa、回压930KPa,油嘴处压降达5MPa,压降过大,
易产生气穴现象,油嘴喉道处流速过高,导致油嘴失效。 1.2流体流速高
根据检测结果,并口两相流夹带固体,且该并油嘴出口平均流速15m/s
根据流体冲蚀的临界冲蚀流速计算公式:
Ve C/(p-)es
(1)
计算得Ve=60/(27.7)=11.4m/s,油嘴出口流速超过了临界
冲蚀流速,从而加剧了油嘴及出口管线的冲蚀。 1.3油嘴出口直管段过短
生产中,一股油嘴下游出油管道直管段不小于10倍管径,但该油气井油嘴出口直管段只有160mm,流体高速冲击极易造成弯头穿刺。
2改造方法优选
为保证生产,需对该油气并油嘴及下方立管段进行改造优
化,常用的油嘴及管线的冲蚀优化方法主要有: 2.1多级节流
油嘴冲蚀损坏的重要原因之一是气穴现象的发生,为防止气穴现象的发生,除应合理设置节流油嘴与管道面积比外,更重要的是正确地调定背压的大小,
当进口压力较高时,为使背压不致过大,可以进行二级或三级节流,从而防止气穴及气蚀发生。通过采用串联两个或多个节流油嘴的方法,共同分担节流油嘴两端的压差,使每个节流油嘴两端的压差减小,破坏气穴产生的条件,从而避免冲蚀现象的发生。
2.2调整油嘴尺寸
油嘴长度一定时,油嘴直径越小,压降就越大,反之就小;油嘴直径相同时,长度越长压降越大,反之就小。实际生产中,可以根据实际需要,选用不同直径及长度的油嘴,并加以组合,
以达到合理降压和避免油嘴损坏的目的。 2.3合理设计管线及管径
油井生产中,油嘴出口管线的冲蚀主要是由于流体流速过高,对管线的冲击强导致,对于易发生冲蚀的部件,常采取以下方法:
268化置纪2016年9月
方方数据
(2)油嘴出口管线易发生冲馋,可以通过增加出口管线管
径,降低流体流速来控制冲蚀。 2.4机械防砂
油嘴及管线冲蚀的主要原因之一是流体中固体颗粒的影响,因此采取措施去除或减少流体中的固体颗粒,对降低冲蚀具有重要作用。常采用的方法为在油嘴前加防砂帽、井口除砂
器或加装机械分离装置等降低流体中的含砂量。 2.5材质及涂层
不同的材质抗冲蚀能力不同,因此油嘴的材质也属于油嘴冲蚀磨损的影响因素。油嘴可选用表面硬度高并抗气蚀的材料或采用喷途硬质合金和陶资等方法来提高材质的性能,以达到防破坏的目的。
针对该油气井,管线材质及流体介质无法改变,油井产量不变,因此,适合的优化方法有;多级油嘴、改变管径、机械防砂。
3改造方案建立
综合优选出的优化方法,采取二级油嘴、增大管径、防砂帽相结合的方案:
(1)针对油嘴压差大,油嘴损坏的情况,增加了二级油嘴,对该井进行分段降压(采油树油嘴一级降压3MPa,新增油嘴二级降压2MPa);
由于油嘴型号相同,内径相同,根据压差与流速、油嘴尺寸关系式:
AP,d, AP"ad
(2)
可知增加二级油嘴后,油嘴处流速为改造前流速的0.77 倍,冲击作用明显减弱。
(2)针对直管段过短、含砂量大的情况,并结合该井改造空间小的特点,通过增加3个盲三通并加防砂帽,减少了流体对弯头处的磨损及冲击:
(3)针对油嘴出口管线流速大,管线冲蚀严重的情况,通过将管径由3寸变为4寸,根据流体流速与截面管径的关系式:
vi=v(D/D,)2
(3)
计算得改造后油嘴出口管线流速v=8.4m/s,小于临界冲蚀
流速,有效降低了油嘴及管线的冲蚀。 4结语
改造后,经过一段时间运行,该井未出现冲蚀严重现象,油嘴及管线的冲蚀得到了有效控制。该油气井油嘴改造方案的建立思路充分考虑了实际生产和空间限制等因素,也为同类油
气井油嘴冲蚀问题的控制及优化提供了参考。参考文献:
[1]王磊.节流油嘴损坏原因分析[]内蒙古石油化工, 2010,05:3840.
[2]李悦钦,李友,战晓溪,等.高压节流阅冲蚀机理研究[1] 石油与化工设备,2010,13:31-33