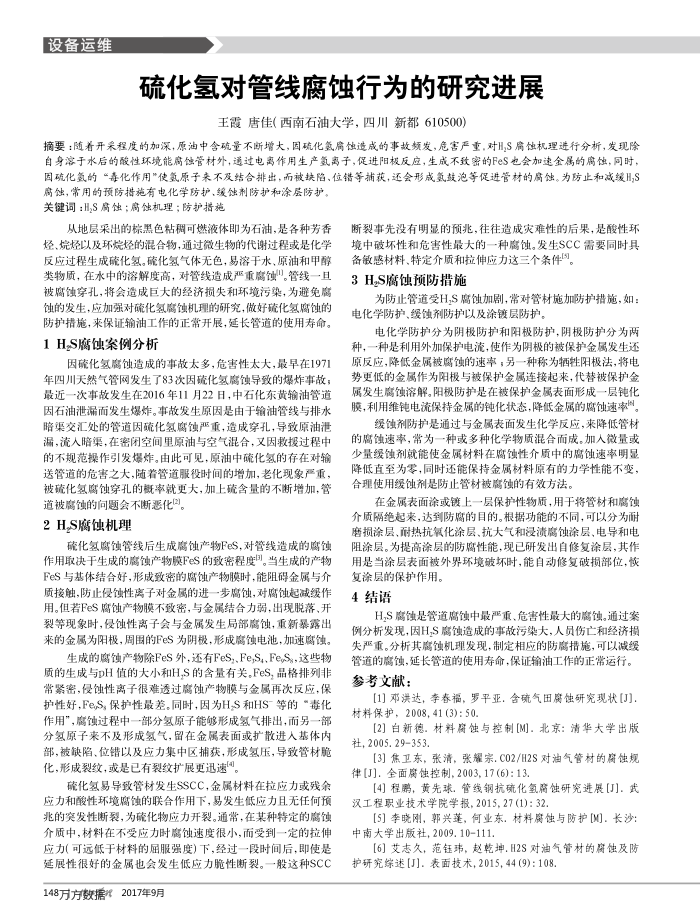
设备运维
硫化氢对管线腐蚀行为的研究进展
王霞唐佳(西南石油大学,四川新都610500)
摘要:随着开采程度的加深,原油中含硫量不断增大,固硫化氢扁蚀造成的事故频发,危害严重,对H,S扁蚀机理进行分析,发现除自身溶于水后的酸性环境能离蚀管材外,通过电离作用生产氨离子,促进阳极反应,生成不致密的FeS电会加速金属的腐蚀,同时,固硫化氢的“毒化作用"使氢原子来不及结合排出,而被块陷、位错等捕获,还会形成氢鼓泡等促进管材的腐蚀。为防止和减缓H,S
离蚀,常用的预防持施有电化学防护、缓蚀剂防护和涂层防护。关键词:H,S腐蚀;离蚀机理;防护措施
从地层采出的棕黑色粘可燃液体即为石油,是各种芳香烃、烷烃以及环烷烃的混合物,通过微生物的代谢过程或是化学反应过程生成硫化氢。硫化氢气体无色,易溶于水、原油和甲醇类物质,在水中的溶解度高,对管线造成严重需蚀"。管线一且被腐蚀穿孔,将会造成巨大的经济损失和环境污染,为避免离蚀的发生,应加强对化氢离蚀机理的研究,做好硫化氢腐蚀的防护措施,来保证输油工作的正常开展,延长管道的使用寿命。 1H,S腐蚀案例分析
因化氢离蚀造成的事故太多,危害性太大,最早在1971 年四川天然气管网发生了83次固硫化氢需蚀导致的爆炸事故:最近一次事故发生在2016年11月22日,中石化东黄输油管道因石油泄漏面发生爆炸。事故发生原因是由于输油管线与排水略渠交汇处的管道因化氢腐蚀严重,造成穿孔,导致原油漏,流人略渠,在密闭空间里原油与空气混合,又因救援过程中的不规范操作引发爆炸。由此可见,原油中硫化氢的存在对输送管道的危害之大,随著管道服役时间的增加,老化现象产重,被硫化氢腐蚀穿孔的概率就更大,加上硫含量的不断增加,管
道被离蚀的问题会不断恶化。 2H.S腐蚀机理
碰化氢腐蚀管线后生成需蚀产物FeS,对管线造成的腐蚀作用取决于生成的离蚀产物膜FeS的致密程度"。当生成的产物 FeS与基体结合好,形成致密的腐蚀产物膜时,能阻碍金属与介质接触,防止侵蚀性离子对金属的进一步岛蚀,对腐蚀起减缓作用。但者FeS腐蚀产物膜不致密,与金属结合力竭,出现脱落、开裂等现象时,侵蚀性离子会与金属发生局部离蚀,重新暴露出来的金属为阳极,周围的FeS为阴极,形成离蚀电池,加速腐蚀。
产物除FeS外,还有FeS,Fe,S4,FeS,这些物
生成的硬
H值的大小和H,S的含量有关,FeS,晶格排列非
质的生成与
金属再次反应,保
常紧密,侵蚀性离子很难透过离蚀产物膜与
等的“毒化
护性好,FeS
保护性最差,同时,因为HS和HS
作用”,需蚀过程中一
一部分氢原子能够形成氢气排出,而另一部
分氢原子来不及形成氢气,留在金属表面或扩散进人基体内部,被缺陷、位错以及应力集中区捕获,形成氢压,导致管材脆化,形成裂纹,或是已有裂纹扩展更迅速
碰化氢易导致管材发生SSCC,金属材料在拉应力或残余应力和酸性环境腐蚀的联合作用下,易发生低应力且无任何预兆的突发性断裂,为硫化物应力开裂。通常,在某种特定的离蚀介质中,材料在不受应力时离蚀速度很小,而受到一定的拉伸应力(可远低于材料的届服强度)下,经过一段时间后,即使是延展性很好的金属也会发生低应力脆性断裂。一般这种SCC
148万方数据2017年9月
断裂事先没有明显的预兆,往往造成灾难性的后果,是酸性环境中破坏性和危害性最大的一种离蚀。发生SCC需要同时具
备敏感材料、特定介质和拉伸应力这三个条件。 3H,S腐蚀预防措施
为防止管道受H,S离蚀加剧,常对管材施加防护措施,如:电化学防护、缓蚀剂防护以及涂镀层防护
电化学防护分为阴极防护和阳极防护,阴极防护分为两种,一种是利用外加保护电流,使作为阴极的被保护金属发生还原反应,降低金属被腐蚀的速率;另一种称为栖性阳极法,将电势更低的金属作为阳极与被保护金属连接起来,代替被保护金属发生离蚀溶解。阳极防护是在被保护金属表面形成一层钝化膜,利用维钝电流保持金属的钝化状态,降低金属的腐蚀速率国。
缓蚀剂防护是通过与金属表面发生化学反应,来降低管材的离蚀速率,常为一种或多种化学物质混合面成。加人微量或少量缓蚀剂就能使金属材料在腐蚀性介质中的腐蚀速率明显降低直至为零,同时还能保持金属材料原有的力学性能不变,合理使用缓蚀剂是防止管材被离蚀的有效方法。
在金属表面涂或镀上一层保护性物质,用于将管材和离蚀介质隔绝起来,达到防腐的目的。根据功能的不同,可以分为耐磨损涂层、耐热抗氧化涂层、抗大气和浸渍离蚀涂层、电导和电阻涂层。为提高涂层的防腐性能,现已研发出自修复涂层,其作用是当涂层表面被外界环境破坏时,能自动修复破损部位,恢
复涂层的保护作用。 4结语
H,S离蚀是管道离蚀中最严重、危害性最大的离蚀。通过案例分析发现,因H,S离蚀造成的事故污染大,人员伤亡和经济损失严重。分析其离蚀机理发现,制定相应的防离措施,可以减缓管道的离蚀,延长管道的使用寿命,保证输油工作的正常运行。参考文献:
[1]邓洪达,李春福,罗平亚,含硫气田离蚀研究现状[J]. 材料保护,2008,41(3):50.
[2]白新德.材料腐蚀与控制[M].北京:清华大学出版社,2005.29353.
[3】焦卫东,张清,张耀宗,C02/H2S对油气管材的腐蚀规律[J].全面离蚀控制,2003,17(6):13.
[4]】程鹏,黄先球,管线钢抗硫化氢商蚀研究进展[J].式汉工程职业技术学院学报,2015,27(1):32.
[5】李晓刚,郭兴蓬,何业东,材料离蚀与防护[M].长沙:中南大学出版社,2009.10-111.
[6]】艾志久,范钰玮,赵乾坤.H2S对油气管材的离蚀及防护研究综述[J].表面技术,2015,44(9):108