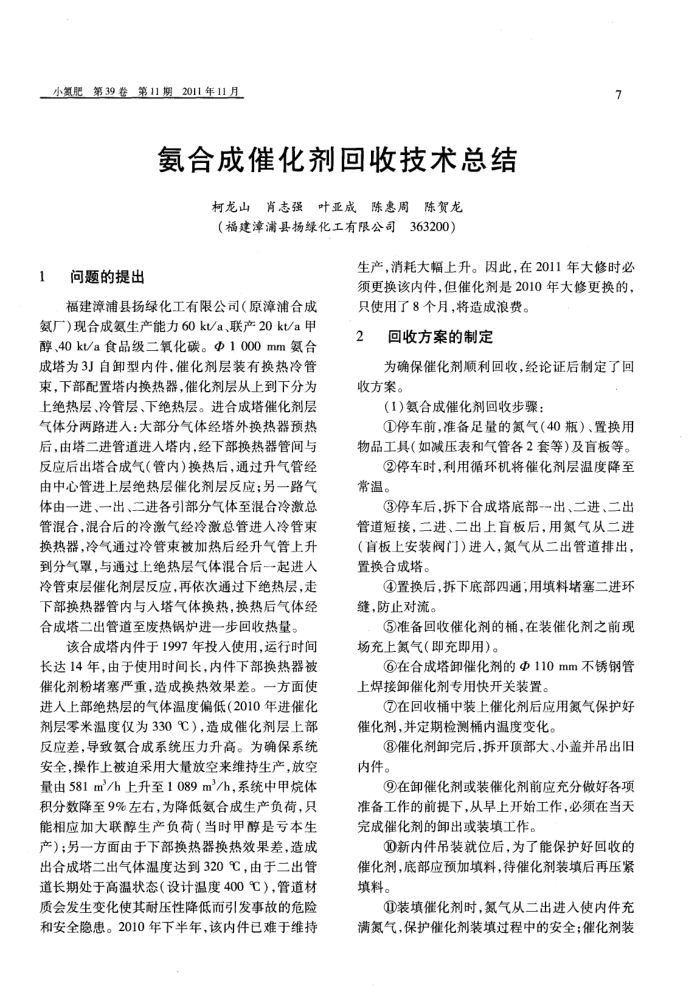
小氮肥第39卷第11期2011年11月
氨合成催化剂回收技术总结
柯龙山肖志强叶亚成陈惠周陈贺龙(福建漳浦县扬绿化工有限公司363200)
问题的提出
1
福建漳浦县扬绿化工有限公司(原漳浦合成氨厂)现合成氨生产能力60kt/a、联产20k/a甲醇、40kt/a食品级二氧化碳。Φ1000mm氨合成塔为3J自卸型内件,催化剂层装有换热冷管束,下部配置塔内换热器,催化剂层从上到下分为上绝热层、冷管层、下绝热层。进合成塔催化剂层气体分两路进入:大部分气体经塔外换热器预热后,由塔二进管道进入塔内,经下部换热器管间与反应后出塔合成气(管内)换热后,通过升气管经由中心管进上层绝热层催化剂层反应:另一路气体由一进、一出、二进各引部分气体至混合冷激总管混合,混合后的冷激气经冷激总管进人冷管束换热器,冷气通过冷管束被加热后经升气管上升到分气罩,与通过上绝热层气体混合后一起进人冷管束层催化剂层反应,再依次通过下绝热层,走下部换热器管内与人塔气体换热:换热后气体经合成塔二出管道至废热锅炉进一步回收热量
该合成塔内件于1997年投人使用,运行时间长达14年,由于使用时间长,内件下部换热器被催化剂粉堵塞严重,造成换热效果差。一方面使进人上部绝热层的气体温度偏低(2010年进催化剂层零米温度仅为330℃),造成催化剂层上部反应差,导致氨合成系统压力升高。为确保系统安全,操作上被迫采用大量放空来维持生产,放空量由581m/h上升至1089m/h,系统中甲烷体积分数降至9%左右,为降低氨合成生产负荷,只能相应加大联醇生产负荷(当时甲醇是亏本生产):另一方面由于下部换热器换热效果差,造成出合成塔二出气体温度达到320℃,由于二出管道长期处于高温状态(设计温度400℃),管道材质会发生变化使其耐压性降低而引发事故的危险和安全隐患。2010年下半年,该内件已难于维持
7
生产,消耗大幅上升。因此,在2011年大修时必须更换该内件,但催化剂是2010年大修更换的,
只使用了8个月,将造成浪费。 2
回收方案的制定
为确保催化剂顺利回收,经论证后制定了回收方案。
(1)氨合成催化剂回收步骤:
①停车前,准备足量的氮气(40瓶)、置换用物品工具(如减压表和气管各2套等)及盲板等。
②停车时,利用循环机将催化剂层温度降至常温。
③停车后,拆下合成塔底部-出、二进、二出管道短接,二进、二出上盲板后,用氮气从二进(盲板上安装阀门)进入,氮气从二出管道排出,置换合成塔。
④置换后,拆下底部四通:用填料堵塞二进环缝,防止对流。
③准备回收催化剂的桶,在装催化剂之前现场充上氮气(即充即用)。
@在合成塔卸催化剂的Φ110mm不锈钢管上焊接卸催化剂专用快开关装置。
②在回收桶中装上催化剂后应用氮气保护好催化剂,并定期检测桶内温度变化。
8催化剂卸完后.拆开顶部大、小盖并吊出旧内件。
③在卸催化剂或装催化剂前应充分做好各项准备工作的前提下,从早上开始工作,必须在当天完成催化剂的卸出或装填工作。
新内件吊装就位后,为了能保护好回收的催化剂,底部应预加填料,待催化剂装填后再压紧填料。
①装填催化剂时,氮气从二出进人使内件充满氮气,保护催化剂装填过程中的安全;催化剂装