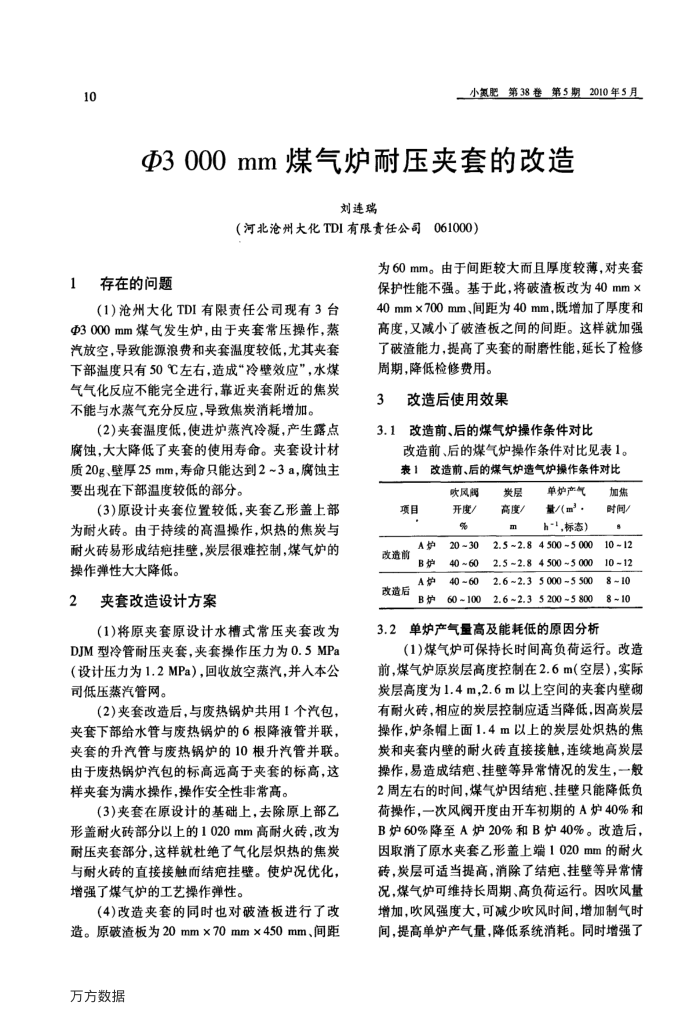
10
小氮肥第38卷第5期2010年5月
Φ3000mm煤气炉耐压夹套的改造
刘连瑞
(河北沧州大化TDI有限责任公司061000)
为60mm。由于间距较大而且厚度较薄,对夹套
存在的问题
1
(1)沧州大化TDI有限责任公司现有3台 Φ3000mm煤气发生炉,由于夹套常压操作,蒸汽放空,导致能源浪费和夹套温度较低,尤其夹套下部温度只有50℃左右,造成“冷壁效应”,水煤气气化反应不能完全进行,靠近夹套附近的焦炭不能与水蒸气充分反应,导致焦炭消耗增加。
(2)夹套温度低,使进炉蒸汽冷凝,产生露点腐蚀,大大降低了夹套的使用寿命。夹套设计材质20g、壁厚25mm,寿命只能达到2~3a,腐蚀主要出现在下部温度较低的部分。
(3)原设计夹套位置较低,夹套乙形盖上部为耐火砖。由于持续的高温操作,炽热的焦炭与耐火砖易形成结疤挂壁,炭层很难控制,煤气炉的
操作弹性大大降低。 2
夹套改造设计方案
(1)将原夹套原设计水槽式常压夹套改为 DJM型冷管耐压夹套,夹套操作压力为0.5MPa(设计压力为1.2MPa),回收放空蒸汽,并人本公司低压蒸汽管网。
(2)夹套改造后,与废热锅炉共用1个汽包,夹套下部给水管与废热锅炉的6根降液管并联,夹套的升汽管与废热锅炉的10根升汽管并联。由于废热锅炉汽包的标高远高于夹套的标高,这样夹套为满水操作,操作安全性非常高。
(3)夹套在原设计的基础上,去除原上部乙形盖耐火砖部分以上的1020mm高耐火砖,改为耐压夹套部分,这样就杜绝了气化层炽热的焦炭与耐火砖的直接接触而结疤挂壁。使炉况优化,增强了煤气炉的工艺操作弹性。
(4)改造夹套的同时也对破渣板进行了改造。原破渣板为20mm×70mm×450mm、间距万方数据
保护性能不强。基于此,将破渣板改为40mm× 40mm×700mm、间距为40mm,既增加了厚度和高度,又减小了破渣板之间的间距。这样就加强了破渣能力,提高了夹套的耐磨性能,延长了检修
周期,降低检修费用。 3
改造后使用效果
改造前、后的煤气炉操作条件对比
3.1
改造前、后的煤气炉操作条件对比见表1。表1改造前、后的煤气炉造气炉操作条件对比
吹风阔开度/
项目
%
改造前改造后
A炉 B炉
20 ~30 40 ~60
A炉
40~60
B炉
60~100
炭层高度/ m
单炉产气量(m, h"",标态)
加焦时间/ 8
10~12
2.5 ~2.84500 ~5 000
2. 5 ~2.8 4 500 ~ 5 000
10 ~12
8~10
2. 6 ~2.3 5 000 ~5 500 2. 6 ~ 2. 3 5 200 ~ 5 800
8-10
3.2单炉产气量高及能耗低的原因分析
(1)煤气炉可保持长时间高负荷运行。改造前,煤气炉原炭层高度控制在2.6m(空层),实际炭层高度为1.4m,2.6m以上空间的夹套内壁砌有耐火砖,相应的炭层控制应适当降低,因高炭层操作,炉条帽上面1.4m以上的炭层处热的焦炭和夹套内壁的耐火砖直接接触,连续地高炭层操作,易造成结疤、挂壁等异常情况的发生,一般 2周左右的时间,煤气炉因结疤、挂壁只能降低负荷操作,一次风阀开度由开车初期的A炉40%和 B炉60%降至A炉20%和B炉40%。改造后因取消了原水夹套乙形盖上端1020mm的耐火砖,炭层可适当提高,消除了结疤、挂壁等异常情况,煤气炉可维持长周期、高负荷运行。因吹风量增加,吹风强度大,可减少吹风时间,增加制气时间,提高单炉产气量,降低系统消耗。同时增强了