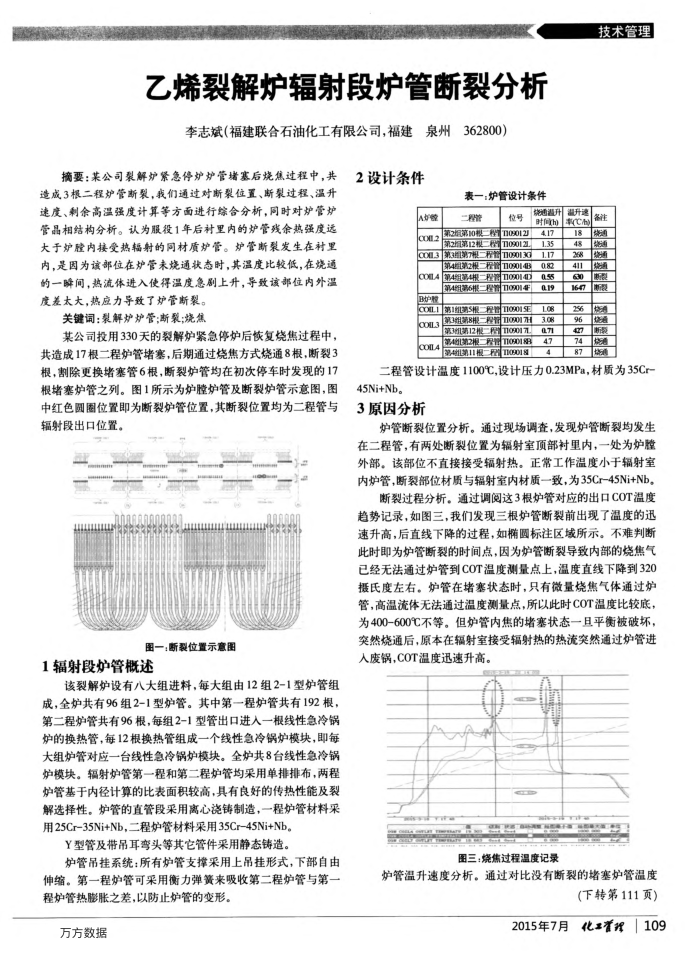
乙烯裂解炉辐射段炉管断裂分析
李志斌(福建联合石油化工有限公司,福建泉州362800)
摘要:某公司裂解炉崇急停炉炉管堵塞后烧焦过程中,共造成3根二程炉管断裂,我们通过对断裂位置、断裂过程、温升速度、剩余高温强度计算等方面进行综合分析,同时对炉管炉管晶相结构分析。认为服役1年后村里内的炉管残余热强度远大于炉腔内接受热辐射的同材质炉管。炉管断裂发生在衬里内,是因为该部位在炉管未烧通状态时,其温度比较低,在烧通的一解间,热流体进入使得温度急剧上升,导致该部位内外温度差太大,热应力导致了炉管断裂。
关键词:裂解炉炉管;断裂;烧焦
某公司投用330天的裂解炉紧急停炉后恢复烧焦过程中,共造成17根二程炉管堵塞,后期通过烧焦方式烧通8根,断裂3 根,割除更换堵塞管6根,断裂炉管均在初次停车时发现的17 根堵塞炉管之列。图1所示为炉炉管及断裂炉管示意图,图中红色圆圈位置即为断裂炉管位置,其断裂位置均为二程管与辐射段出口位置。
图一:断裂位置示意图
1辐射段炉管概述
该裂解炉设有八大组进料,每大组由12组2-1型炉管组成,全炉共有96组2-1型炉管。其中第一程炉管共有192根,第二程炉管共有96根,每组2-1型管出口进人一根线性急冷锅炉的换热管,每12根换热管组成一个线性急冷锅炉模块,即每大组炉管对应一台线性急冷锅炉模块。全炉共8台线性急冷锅炉模块。辐射炉管第一程和第二程炉管均采用单排排布,两程炉管基于内径计算的比表面积较高,具有良好的传热性能及裂解选择性。炉管的直管段采用离心浇铸制造,一程炉管材料采用25Cr-35Ni+Nb,二程炉管材料采用35Cr-45Ni+Nb。
Y型管及带吊耳弯头等其它管件采用静态铸造。
炉管吊挂系统:所有炉管支撑采用上吊挂形式,下部自由伸缩。第一程炉管可采用衡力弹簧来吸收第二程炉管与第一程炉管热膨胀之差,以防止炉管的变形。
万方数据
2设计条件
表一:炉管设计条件
A炉
二程管
第2相第10根
002
第2组第12楼二程
位号 TH09012J T109012
能通温升温升速时间h)
$(C/h)
18
1.35
CO3第3组第程二程管
T109013G
第4附第2楼二程2附1090143
T109014D
第4期
4H
第4组等6报二月
TIOX014
B护膜
IL1第1组第S报二程
HIOOSE
第3m第8根二程001元
OOL
第38第12楼二程T109017L 第481382HPWTI09018B
COILA
38483811报二T109018
1.17 0.82 0.5 On
10 3.0 0.71
48 既
630 1647
26
技术管理
各注资通
通给通
您通
96
烧通 427新
燃通
87
绿
二程管设计温度1100℃,设计压力0.23MPa,材质为35Cr 45Ni+Nb。
3原因分析
炉管断裂位置分析。通过现场调查,发现炉管断裂均发生在二程管,有两处断裂位置为辐射室顶部衬里内,一处为炉膛外部。该部位不直接接受辐射热。正常工作温度小于辐射室内炉管,断裂部位材质与辐射室内材质一致,为35Cr-45Ni+Nb,
断裂过程分析。通过调阅这3根炉管对应的出口COT温度趋势记录,如图三,我们发现三根炉管断裂前出现了温度的迅速升高,后直线下降的过程,如椭四标注区域所示。不难判断此时即为炉管断裂的时间点,因为炉管断裂导致内部的烧焦气已经无法通过炉管到COT温度测量点上,温度直线下降到320 摄氏度左右。炉管在堵塞状态时,只有微量烧焦气体通过炉管,高温流体无法通过温度测量点,所以此时COT温度比较底,为400-600℃不等。但炉管内焦的堵塞状态一且平衡被破坏,突然烧通后,原本在辐射室接受辐射热的热流突然通过炉管进人废锅,COT温度迅速升高。
图三:烧焦过程温度记录
炉管温升速度分析。通过对比没有断裂的堵塞炉管温度
(下转第111页)
2015年7月
化置理109