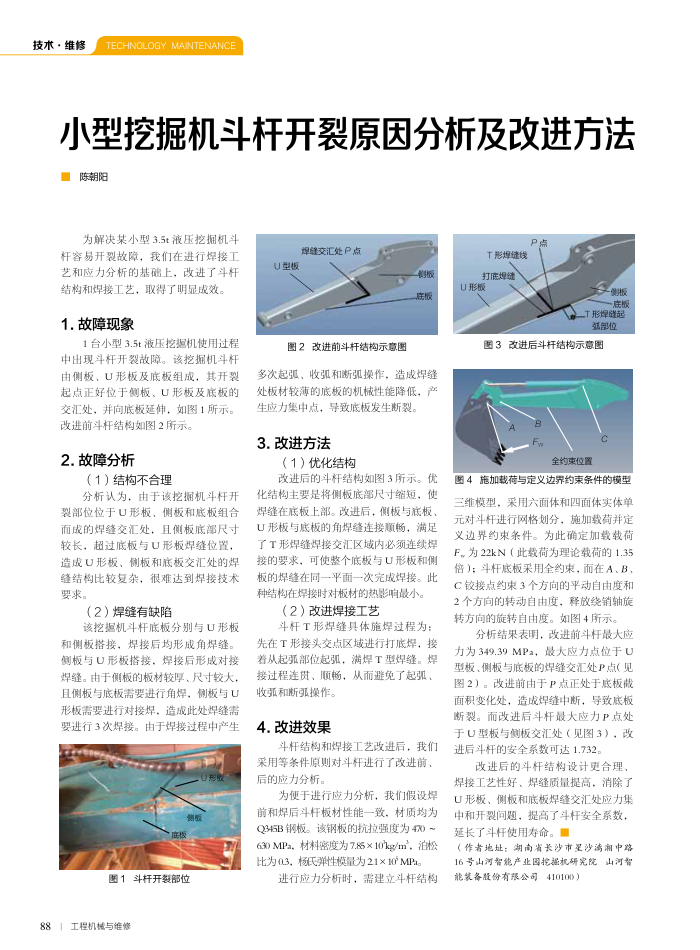
技术·维修
TECHNOLOGY MAINTENANCE
小型挖掘机斗杆开裂原因分析及改进方法陈朝阳
为解决某小型3.5t液压挖掘机斗
杆容易开裂故障,我们在进行焊接工艺和应力分析的基础上,改进了斗杆
结构和焊接工艺,取得了明显成效。 1.故障现象
1台小型3.5t液压挖损机使用过程中出现斗杆开裂故障。该挖掘机斗杆由侧板、U形板及底板组成,其开裂起点正好位于侧板、U形板及底板的交汇处,并向底板延伸,如图1所示。
改进前斗杆结构如图2所示。 2.故障分析
(1)结构不合理
分析认为,由于该挖掘机斗杆开裂部位位于U形板、侧板和底板组合而成的焊缝交汇处,且侧板底部尺寸较长,超过底板与U形板焊缝位置造成U形板、侧板和底板交汇处的焊缝结构比较复杂,很难达到焊接技术要求。
(2)焊缝有缺陷
该挖揭机斗杆底板分别与U形板和侧板搭接,焊接后均形成角焊缝。侧板与U形板搭接,焊接后形成对接焊缝。由于侧板的板材较厚、尺寸较大,且侧板与底板需要进行角焊,侧板与U 形板需要进行对接焊,造成此处焊缝需要进行3次焊接。由于焊接过程中产生
侧版
图1斗杆开裂部位
881工程机械与维修
U型板
焊缝交汇处P点
图2改进前斗杆结构示意围
板底板
多次起弧、收弧和断弧操作,造成焊缝处板材较薄的底板的机械性能降低,产
生应力集中点,导致底板发生断裂。 3.改进方法
(1)优化结构
改进后的斗杆结构如图3所示。优化结构主要是将侧板底部尺寸缩短,使焊缝在底板上部。改进后,侧板与底板 U形板与底板的角焊缝连接顺畅,满足了T形焊缝焊接交汇区域内必须连续焊接的要求,可使整个底板与U形板和侧板的焊缝在同一平面一次完成焊接。此种结构在焊接时对板材的热影响最小。
(2)改进焊接工艺
斗杆T形焊缝具体施焊过程为:先在T形接头交点区域进行打底焊,接着从起弧部位起弧,满焊T型焊缝。焊接过程连贯、顺畅,从而避免了起弧,
收和断弧操作。 4.改进效果
斗杆结构和焊接工艺改进后,我们采用等条件原则对斗杆进行了改进前、后的应力分析。
为便于进行应力分析,我们假设焊前和焊后斗杆板材性能一致。材质均为 Q345B钢板。该钢板的抗拉强度为470~ 630MPa,材料密度为7.85×10kg/m,泊松比为03,杨氏弹性模量为21×10°MPa
进行应力分析时,需建立斗杆结构
T形焊缝线打底焊缝
U形板
P点
文测版底板
T形焊缝起
弧部位
图3改进后斗杆结构示意图
全约束位置
图4施加载与定义边界约束条件的模型三维模型,采用六面体和四面体实体单元对斗杆进行网格划分,施加载荷并定义边界约束条件。为此确定加载载荷 F为22kN(此数荷为理论载荷的1.35 倍);斗杆底板采用全约束,而在A、B、 C铰接点约束3个方向的平动自由度和 2个方向的转动自由度,释放绕销轴旋转方向的旋转自由度。如图4所示。
分析结果表明:改进前斗杆最大应力为349.39MPa,最大应力点位于U 型板、侧板与底板的焊缝交汇处P点(见图2)。改进前由于P点正处于底板截面积变化处,造成焊缝中断,导致底板断裂。而改进后斗杆最大应力P点处于U型板与侧板交汇处(见图3),改进后斗杆的安全系数可达1.732。
改进后的斗杆结构设计更合理、焊接工艺性好、焊缝质量提高,消除了 U形板、侧板和底板焊缝交汇处应力集中和开裂问题,提高了斗杆安全系数,延长了斗杆使用寿命。
(作者地址:湖南省长沙市星沙涛湘中路 16号山河智能产业图挖据机研完院山河智能策备股份有限公司410100)