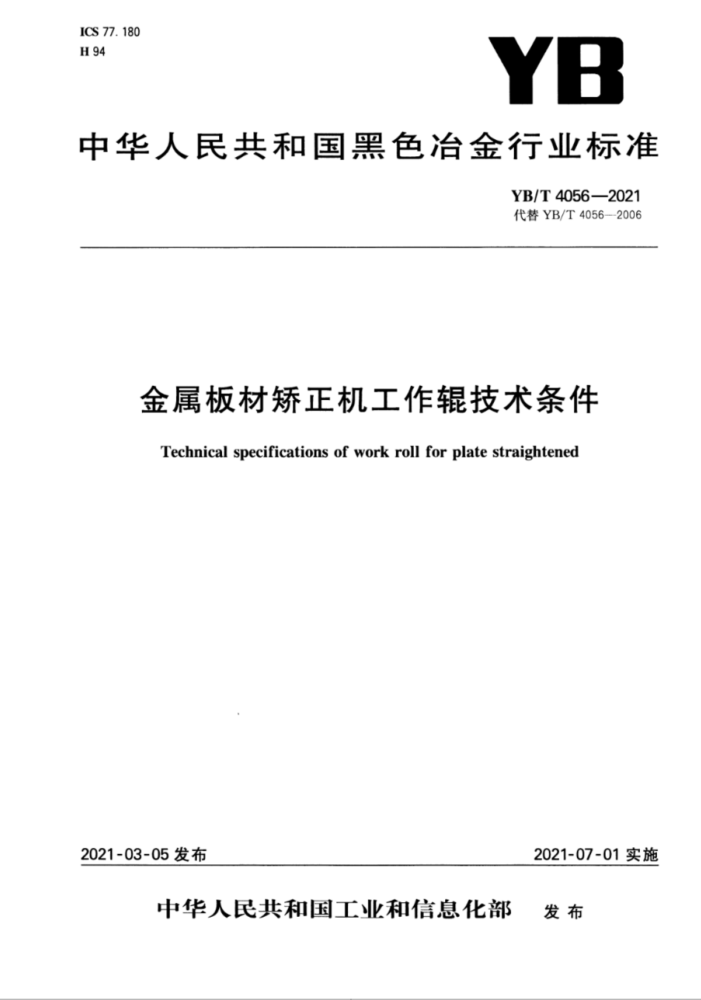
ICS 77. 180 H 94
YB
中华人民共和国黑色冶金行业标准
YB/T 4056—2021 代替YB/T4056—2006
金属板材矫正机工作辊技术条件
Technical specificationsof workrollforplate straightened
2021-07-01实施
2021-03-05发布
中华人民共和国工业和信息化部 发布
0e
育
本# T0-TYT0
Y
NPHTD TMoUMMMwMoT r ST1a 大
H44
Tas&.4 T电经牌正机工作想及有装体证体家由供健取方协内服年成膜 B 家直格 x404 T4500a44 T正工保泰水M品 -TEThAaTa-4T TT4 电511 TETC6A2N 美& t单 TTO-大本大中国工业金商本标术有口工本A品红内# 本营水本 --7T4036-11/T00-000
YB/T4056—2021
金属板材矫正机工作辑技术条件
1范围
本标准规定了辊式金属板材矫正机工作辊的技术要求、试验方法、检验规则、标记、包装、运输和贮存等。 本标准适用于辊式金属板材矫正机用整体锻造合金钢工作辊(以下简称:矫正机工作辊),也适用于
技术要求相同的金属板材矫正机用整体锻造合金钢中间辑。
2规范性引用文件
2
下列文件对于本文件的应用是必不可少的。凡是注日期的引用文件,仅注日期的版本适用于本文
件。凡是不注日期的引用文件,其最新版本(包括所有的修改单)适用于本文件。
GB/T222钢的成品化学成分允许偏差 GB/T223.5钢铁酸溶硅和全硅含量的测定还原型硅钼酸盐分光光度法(GB/T223.5-
-
2008,ISO4829-1:1986、ISO4829-2:1988,MOD)
GB/T223.11 钢铁及合金铬含量的测定可视滴定或电位滴定法(GB/T223.11一2008,ISO 4937:1986,MOD)
GB/T 223.13 钢铁及合金化学分析方法 硫酸亚铁铵滴定法测定钒含量 GB/T223.14 钢铁及合金化学分析方法 钼试剂萃取光度法测定钒含量 GB/T223.18 钢铁及合金化学分析方法 硫代硫酸钠分离-碘量法测定铜量 GB/T223.23 钢铁及合金镍含量的测定 丁二酮分光光度法 GB/T223.26 钢铁及合金钼含量的测定 硫氰酸盐分光光度法 GB/T223.59 钢铁及合金磷含量的测定 铋磷钼蓝分光光度法和锑磷钼蓝分光光度法 GB/T223.60 钢铁及合金化学分析方法 高氯酸脱水重量法测定硅含量 GB/T 223.63 钢铁及合金化学分析方法 高碘酸钠(钾)光度法测定锰量 GB/T223.68 钢铁及合金化学分析方法 管式炉内燃烧后碘酸钾滴定法测定硫含量 GB/T223.69 钢铁及合金碳含量的测定 管式炉内燃烧后气体容量法 GB/T226 钢的低倍组织及缺陷酸蚀检验法 GB/T230.1 金属材料洛氏硬度试验第1部分:试验方法(GB/T230.1一2018,ISO6508-1:
2016,MOD)
GB/T1184—1996 形状和位置公差 未注公差值 GB/T1299--2014 4工模具钢 GB/T1804—2000 一般公差未注公差的线性和角度尺寸的公差 GB/T4340.1 金属材料维氏硬度试验第1部分:试验方法(GB/T4340.1一2009,ISO6507-1:
2005,MOD
GB/T4879—2016防锈包装 GB/T5617 钢的感应率火或火焰率火后有效硬化层深度的测定 GB/T13298 金属显微组织检验方法 GB/T13313 3轧辊肖氏、里氏硬度试验方法
1
YB/T4056—2021
GB/T13314一2008锻钢冷轧工作辊通用技术条件 GB/T15822.1无损检测 磁粉检测 第1部分:总则(GB/T15822.1—2005,ISO9934-1:2001,
IDT)
GB/T23904 :无损检测 超声表面波检测方法 JB/T9218无损检测渗透检测方法
3技术要求
3.1矫正机工作辊应按供需双方认可的图样制造,并符合本标准规定。如有特殊要求,由供需双方协商确定。 3.2 矫正机工作辊材质 3.2.1 矫正机工作辑用钢的牌号和化学成分推荐按表1规定,也可采用供需双方商定的其他牌号或化学成分,辊坏或成品分析的化学成分允许偏差应符合GB/T222的规定。
表1 矫正机工作辊用钢及化学成分
化学成分(质量分数)/%
牌号
推荐用途
c
V Cu Ni
Si
Mn Cr Mo
P
S
0.50~
60CrMo
0.55~ 0. 17~ 0.50~ 0. 80 0.30~
0. 65 0. 37 0.80 0.90~ 0. 40 0.15~ ≤0.25
60CrMoV
0. 35
1. 20
0.32~ 0.80~ 0.20~ 4.75~ 1.10~ 0.80~ 0. 45 1. 20 0. 50 5. 50 1. 70 1. 20 0.33~ 0.80~ 0.20~ 4.75~ 1.10~ 0.30~ 0. 43 1. 20 0. 50 5. 50 1. 60 0. 60 0.60~ 0.80~ 0.30~ 4. 80~ 1.10~ 0.30~ 0. 65 1. 20 0. 50 5. 20 1. 40 0. 50 0.95~ 0.15~ 0. 25~ 1.40~
热矫正机工作辊
≤0.30 ≤0.25
4Cr5MoSiV1
≤0.30 ≤0.25
4Cr5MoSiV
≤0.30 ≤0.25 ≤0.25 ≤0.30 ≤0.020 ≤0.010
6Cr5MoSiV
GCr15
-
1. 05 0. 35 0. 45 1. 65 0.80~ 0.15~ 0.30~ 1. 80~ 0.20~ 0.05~
8Cr2MoV
0. 90 0. 40 0. 50 2. 40 0. 40 0. 15 ≤0.25 0. 85~ 0.25~ 0.20~ 1. 70~ 0.20~
≤0.25
9Cr2Mo
0. 95 0. 45 0. 35 2.10 0. 40 0.85~ 0.25~ 0.20~ 2.50~ 0.20~ 0. 95 0. 45 0. 35 3. 50 0. 40 0.78~ 0. 40~ 0.20~ 4.80~ 0.20~ 0.10~ 0. 90 1. 10 0. 50 5. 50 0. 60 0. 20 1.40~
冷矫正机工作辊
≤0.25
9Cr3Mo
≤0.25 ≤0.80
8Cr5MoV
≤0.60 ≤0.60 11.0~ 0.70~ 0.90~
13. 0 1. 20 1. 00 ≤0.30 ≤0.25
Cr12Mo1V1
1. 60
注:冷矫正机工作辑辊适用于常温矫直,热矫正机工作辊适用于带温矫直。 3.2.2 矫正机工作辊用辑坏的冶炼方法宜采用“电炉(或转炉)冶炼十炉外精炼十电渣重熔”,也可采用 2
YB/T4056—2021
供需双方商定的其他方法,具体冶炼方式在合同中注明。 3.3矫正机工作辊锻件的锻比
矫正机工作辑锻件采用模铸锭锻造时,辊身锻比应不小于3,采用电渣锭锻造时辊身锻比应不小于 2,采用钢坏锻造时,辊身锻比不小于1.5。 3.4矫正机工作辊的热处理要求 3.4.1矫正机工作辊应进行热处理,辊身、辊颈表面的硬度应符合图样和技术文件或有关协议的规定。 3.4.2矫正机工作辊辊身表面硬度应根据使用条件确定,一般推荐冷矫75HSD~95HSD、热矫 50HSD~85HSD,在8HSD硬度单位范围内选取。 3.4.3矫正机工作辊辊身表面硬度应均匀,其硬度均匀度应不大于4HSD硬度单位。 3.4.4矫正机工作辊辊身的有效淬硬层深度,一般应符合表2规定。
表2矫正机工作辊辊身的有效淬硬层深度 <20
单位为毫米 >150 5~15
辊身直径有效率硬深度
≥20~60 1.5~4
>60~150 3~6
双方协商
3.4.5要求进行表面淬火的辊颈,有效淬硬层深度一般为1.5mm~4mm。 3.4.6矫正机工作辑辊身边缘允许有低于图样硬度要求的软带存在,辊身直径≤100mm允许5mm~ 15mm,辊身直径>100mm按表3规定。软带宽度也可由供需双方商定。
表3矫正机工作辊辊身两边缘允许软带宽度 ≤300
单位为毫米 ≥2001 ≤65
辊身长度允许软带宽度
301~600 ≤45
601~1000 ≤50
1001~2000 ≤55
≤25
3.5矫正机工作辊的机械加工要求 3.5.1 矫正机工作辊的尺寸公差、形状和位置公差、表面粗糙度等均应符合图样要求。 3.5.2 图样上未注公差尺寸的极限偏差应执行GB/T1804一2000m级。 3.5.3 图样上未注形状和位置公差:
对于要求遵循包容原则的圆柱表面,其圆柱度公差值为尺寸公差的一半。对于从功能要求不需
a)
要遵循包容原则的圆柱表面,由圆度、素线直线度(或相对两条素线的平行度)的未注公差值和尺寸公差分别控制;
b)辊身轴线对辊颈公共基准轴线的同轴度公差值应执行GB/T1184一1996H级; c) 键槽中心面对通过基准轴线的基准中心平面的对称度公差值应执行GB/T1184一1996K级。
3.5.4对于成组使用的矫正机工作辊,成组辊身直径差一般不大于0.05mm。 3.6矫正机工作辊的表面质量 3.6.1 辊身和辊颈的工作表面不允许有裂纹及肉眼可见的凹坑、非金属夹杂、气孔和其他影响使用的表面缺陷。 3.6.2按供需双方商定,对工作辊表面可进行磁粉探伤或渗透探伤检查,对于辊身直径≥60mm的工作辊可采用超声表面波探伤方法检查,不允许有微裂纹等缺陷存在。 3.6.3矫正机工作辊辊身表面有镀铬要求的,镀层厚度达到0.05mm~0.10mm,镀铬层硬度达到 58HRC~62HRC。
3
YB/T 40562021
3.7矫正机工作辊的内部质量 3.7.1矫正机工作辊试样的低倍组织,不允许有白点、内裂、缩孔、气泡、翻皮和目视可见的非金属夹杂物等冶金缺陷。 3.7.2矫正机工作辊(锻件切片)显微组织网状碳化物不大于2级(按GB/T1299一2014第三级别图评定)。 3.7.3 3矫正机工作辊内部超声波探伤按GB/T13314一2008执行,质量等级满足表A.2中的A级规定。
4试验方法
4.19 矫正机工作辊的化学成分检验方法按GB/T222及GB/T223相关标准规定执行。 4.2矫正机工作辊硬度试验一般用肖氏硬度计或里氏硬度计测定,试验方法按GB/T13313执行。特殊条件也可采用洛氏硬度计或维氏硬度计测定,试验方法分别按GB/T230.1、GB/T4340.1规定执行。 4.3矫正机工作辊有效率硬层深度的测试方法按GB/T5617规定执行。 4.4矫正机工作辊磁粉探伤方法按GB/T15822.1规定执行,也可用渗透探伤方法,按JB/T9218的规定执行。辊身直径≥60mm的工作辊超声表面波探伤方法按GB/T23904规定执行。 4.5 矫正机工作辊低倍组织检验按GB/T226规定执行 4.6 矫正机工作辊网状碳化物检验按GB/T13298规定执行。 4.7 矫正机工作辑超声波探伤检验按GB/T133142008附录A规定执行。
5检验规则
5.1矫正机工作辑化学成分应于每炉钢水浇注前取样检验,电渣钢应于电渣锭补缩端取样检验 5.2矫正机工作辊的几何尺寸、形位公差、表面质量应由制造厂质量检验部门按本标准和图样的要求逐件进行检查和验收。 5.3矫正机工作辊表面硬度应按图样规定逐支进行检验,辊身表面硬度均匀度及辊身表面两端的软带宽度应分别符合3.4.3和3.4.6的规定。 5.4矫正机工作辊有效淬硬层深度一般由工艺保证,不作常规检查。必要时可由用同材质、同直径、经相同工艺规范热处理的试样或实物解剖测试。 5.5按供需双方的商定,工作辊应逐支进行磁粉探伤或渗透探伤,辊身直径≥60mm的工作辊可以进行超声表面波探伤。
6标记、包装、运输和贮存
6.1经检验合格的矫正机工作辊,应在其非传动端端面的适当部位(轴向对称的任选一端)标明厂标,端面直径小于20mm的可用其他方法进行标记。 6.2矫正机工作辊防锈包装应按GB/T4879一2016表1中的1级执行,防锈期2年。 6.3矫正机工作辊外包装用包装箱包装或栅板包装,质量应符合运输部门对包装的要求;对于包装有特殊要求的,可由供需双方协商。 6.4包装箱内应随附下列文件
a)装箱单应注明矫正机工作辊名称、型号及规格、合同号、数量、装箱日期;
4
YB/T4056—2021
b) 产品质量合格证。 6.5包装箱外表面的标志一般包括:
a)合同号、工作辊型号或名称、数量; b)重量; c) 发站(港)及发货单位; d) 到站(港)及收货单位; e) 有关包装贮运指示标志。
6.6矫正机工作辊应存放在通风、干燥的仓库或车间内。
5
YB/T4056—2021
参考文献
[1] GB/T1299—2014 4工模具钢 [2] GB/T 30772015 合金结构钢 [3] GB/T18254—2016 高碳铬轴承钢 [4] JB/T6401—2017 大型轧辊锻件用钢技术条件
6