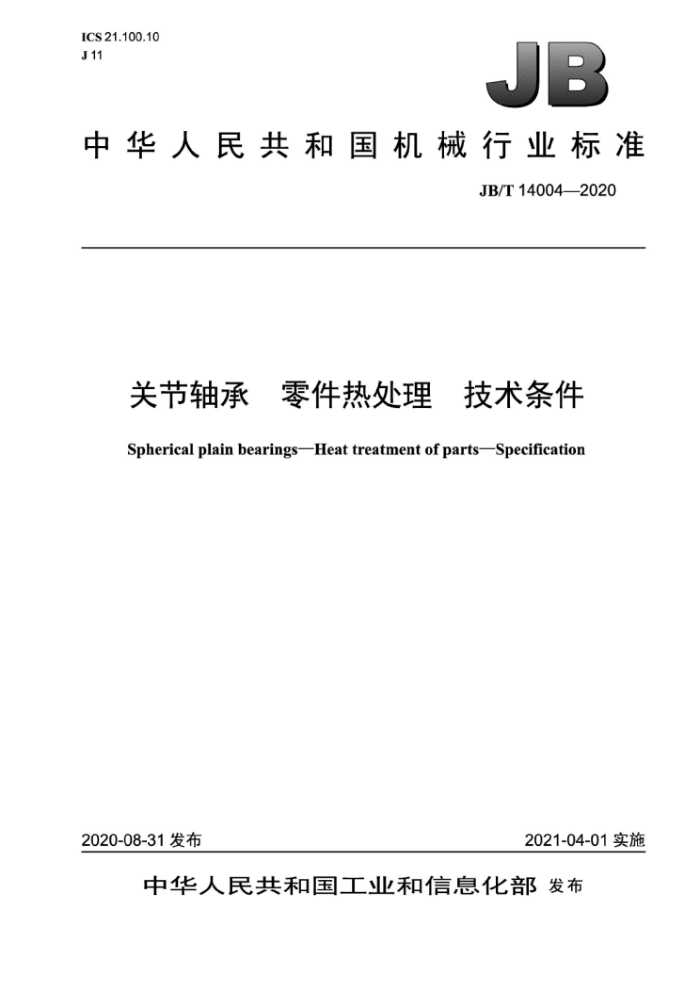
ICS 21.100.10 J11
JB
中华人民共和国机械行业标准
JB/T14004—2020
关节轴承 零件热处理 技术条件 SphericalplainbearingsHeattreatmentofpartsSpecification
2021-04-01实施
2020-08-31发布
中华人民共和国工业和信息化部发布
JB/T14004—2020
目 次
前言 1范围 2规范性引用文件 3术语和定义 4技术要求
1
4.1高碳铬轴承钢关节轴承零件, 4.2不锈钢关节轴承零件 4.3 渗碳钢关节轴承零件. 4.4 调质钢关节轴承杆端体和挤压型套圈 5检测方法附录A(资料性附录) 套圈有效壁厚附录B (资料性附录) 关节轴承套圈率回火后允许的变形量附录C (规范性附录) 关节轴承零件萍回火后显微组织,附录D (规范性附录) 40Cr13钢制关节轴承零件淬回火后的脱碳层深度参考文献
6
A
11
12 .13
图A.1 关节轴承套围有效壁厚示意图图C.1 第一级别图(40Cr13中碳铬不锈钢关节轴承零件率回火后显微组织)图C.2第二级别图(渗碳钢关节轴承零件渗碳淬回火后心部显微组织)
5
.11 11
表1高碳铬轴承钢关节轴承零件球化退火后的技术要求表2高碳铬轴承钢关节轴承零件马氏体淬回火后的硬度表3高碳铬轴承钢关节轴承零件马氏体萍回火后同一零件的表面硬度差表4高碳铬轴承钢关节轴承零件马氏体萍回火后的显微组织表5高碳铬轴承钢关节轴承零件率回火后的其他技术要求,表6不锈钢关节轴承零件球化退火后的技术要求。 表7不锈钢关节轴承零件萍回火后硬度和同一零件硬度差表8不锈钢关节轴承零件率回火后其他技术要求.. 表9 渗碳钢关节轴承零件正火后技术要求表10 渗碳钢关节轴承零件率硬层深度表11 渗碳钢关节轴承零件表面硬度和心部硬度表12 杆端体和挤压型套圈调质处理后技术要求,表13 检测方法表B.1 外圈萍回火后外径变动量... 表B.2 内圈回火后内径变动量... 表B.3 渗碳热处理后允许的变形量表D.1 40Cr13钢制关节轴承零件淬回火后的脱碳层深度
4
2
10 12
I
JB/T14004—2020
前 言
本标准按照GB/T1.1一2009给出的规则起草。 本标准由中国机械工业联合会提出。 本标准由全国滚动轴承标准化技术委员会(SAC/TC98)归口。 本标准起草单位:福建龙溪轴承(集团)股份有限公司、洛阳轴承研究所有限公司。 本标准主要起草人:陈浩、雷建中、林振元、林庄、陈志雄、黄秀东、王珊珊、李夏青、黄阿德。 本标准为首次发布。
I
JB/T14004—2020
关节轴承 零件热处理 技术条件
1范围
本标准规定了采用符合GB/T18254规定的GCr15、GCr15SiMn;GB/T3086规定的G95Cr18、 G102Cr18Mo;GB/T1220规定的40Cr13;GB/T699规定的45;GB/T33161规定的G20CrMo、G20CrNiMo 及GB/T3077规定的20Cr、20CrMo、20CrMnTi、20CrMnMo、20CrNiMo、35CrMo、40Cr、40CrNiMoA、 42CrMo钢制关节轴承零件的热处理技术要求和检验方法等。
本标准适用于上述关节轴承零件工序间与成品零件的热处理质量检验,也适用于其他高碳铬轴承钢、 中碳铬不锈钢、高碳铬不锈轴承钢、渗碳钢、调质钢关节轴承零件热处理质量检验,对有特殊要求的关节轴承零件按相应产品图样的规定。
2规范性引用文件
2
下列文件对于本文件的应用是必不可少的。凡是注日期的引用文件,仅注日期的版本适用于本文件。凡是不注日期的引用文件,其最新版本(包括所有的修改单)适用于本文件。
GB/T230.1—2018 金属材料洛氏硬度试验第1部分:试验方法 GB/T231.1—2018 金属材料布氏硬度试验第1部分:试验方法 GB/T1172—1999 黑色金属硬度及强度换算值 GB/T3944—2002 关节轴承词汇 GB/T4340.1—2009 金属材料维氏硬度试验 第1部分:试验方法 GB/T6394—2017 金属平均晶粒度测定方法 GB/T7232—2012 金属热处理工艺术语 GB/T13320—2007 钢质模锻件金相组织评级图及评定方法 GB/T17394.1—2014 金属材料 里氏硬度试验第1部分:试验方法 GB/T24606—2009 滚动轴承无损检测磁粉检测 GB/T34891—2017 滚动轴承 高碳铬轴承钢零件热处理技术条件 JB/T1460—2011 滚动轴承 高碳铬不锈钢轴承零件热处理技术条件 JB/T7361—2007 滚动轴承 零件硬度试验方法 JB/T7362—2007 滚动轴承 零件脱碳层深度测定法 JB/T8881—2020 滚动轴承 渗碳轴承钢零件热处理技术条件 JB/T14006—2020 滚动轴承高碳铬轴承钢零件残留奥氏体检测规程
3术语和定义
GB/T3944和GB/T7232界定的术语和定义适用于本文件。
1
JB/T140042020
4 技术要求
4.1 高碳铬轴承钢关节轴承零件 4.1.1 关节轴承零件球化退火后的技术要求
关节轴承零件球化退火后的技术要求应按表1的规定。
表1 高碳铬轴承钢关节轴承零件球化退火后的技术要求
检查项目硬度
技术要求
GCr15钢
GCr15SiMn钢
179HBW~207HBW或88HRB~94HRB 179HBW~217HBW或88HRB~97HRB 细小、均匀分布的球化组织,应符合GB/T34891一2017第一级别图的第2级~第4级,允许有细点状球化组织,不允许有第1级和第5级所示的组织存在应符合GB/T34891一2017第四级别图的第1级~第2.5级不大于单边最小加工余量的2/3
显微组织网状碳化物脱碳层深度
4.1.2 关节轴承零件马氏体淬回火后的技术要求 4.1.2.1 硬度
关节轴承零件马氏体淬回火后硬度及同一零件的表面硬度差应分别按表2和表3的规定。
表2 高碳铬轴承钢关节轴承零件马氏体回火后的硬度
套圈有效壁厚
萍火后硬度 HRC
常规回火后硬度
高温回火后硬度HRC 250℃
零件名称单缝外圈
HRC
mm
300℃ 54~58
56~60 56~61
≥60
<25 ≥25b
其余套圈
58~64
套圈有效壁厚的规定参见附录A,以下同。 有效壁厚≥25mm的套图,其心部硬度应≥54HRC
表3 高碳铬轴承钢关节轴承零件马氏体淬回火后同一零件的表面硬度差
零件名称
外圈或座圈(外径)
内圈或轴圈(球面直径)
100 400 2
325 一 3
成品尺寸 mm
400 一 3
100 325 2
> M
-
100 1
100 I
便度差HRC
4.1.2.2 显微组织
关节轴承零件马氏体淬回火后显微组织应由隐晶、细小结晶或小针状马氏体、均匀分布的细小残留碳化物、 少量残留奥氏体组成,充许存在少量届氏体。 淬回火后的显微组织要求应按表4的规定。
2
JB/T14004—2020
表4 高碳铬轴承钢关节轴承零件马氏体淬回火后的显微组织
套圈有效壁厚 mm
显微组织级别
屈氏体(第三级别图)
零件材料
马氏体(第二级别图)
≤
≤
>
距工作面3mm以内 距工作面3mm以外
12 25 35
第1级
GCr15钢
12
第2级第1级第2级
不予控制第2级不予控制
第1级~第4级
GCr15SiMn钢
35
注:套圈有效壁厚≥50mm,车 轴承内圈的高径比(高度/内径)≥3时,淬回火后硬度和显微组织要求由制造厂和
用户双方商定。 显微组织级别图谱按照GB/T34891的规定。
-
4.1.2.3 其他技术要求
关节轴承零件淬回火后的其他技术要求应按表5的规定。
表5 高碳铬轴承钢关节轴承零件淬回火后的其他技术要求
检查项目裂纹回火稳定性脱碳层深度及表面软点套圈变形量残留奥氏体含量外观质量不锈钢关节轴承零件
技术要求
关节轴承零件回火后不允许有裂纹关节轴承零件第二次回火前后相应点的硬度差不应大于1HRC 工序间脱碳层深度要求按照GB/T34891一2017中附录C的规定或按制造厂与用户双方协商的规定。成品零件工作面不允许有脱碳和表面软点淬回火后允许的变形量参见本标准附录B或按制造厂与用户双方协商的规定率回火后的残留奥氏体含量按照GB/T34891一2017中附录E的规定或按制造厂与用户双方协商的规定痒回火后应无磕碰伤、 锈蚀及污物附着,整体外观颜色应均匀
4.2
4.2.1 关节轴承零件球化退火后的技术要求
关节轴承零件球化退火后的技术要求应按表6的规定。
表6 不锈钢关节轴承零件球化退火后的技术要求
技术要求
检查项目硬度
40Cr13钢 ≤229HBW
G95Cr18、G102Cr18Mo钢
197HBW~255HBW
均匀分布的细粒状珠光体,允许存在分散的一次碳化物,不允许有李晶状碳化物组织存在,李晶状碳化物显微组织按照JB/T1460一2011规定的第一级别图
显微组织
3
JB/T14004—2020
4.2.2 关节轴承零件淬回火后技术要求 4.2.2.1 硬度
关节轴承零件淬回火后的硬度和同一零件硬度差应按表7的规定。
表7 不锈钢关节轴承零件回火后硬度和同一零件硬度差
40Cr13钢
G95Cr18、G102Cr18Mo钢
零件名称
内圈或轴圈(球面
外圈或座圈(外径) 内圈或轴圈(球面直径) 外圈或座圈(外径)
直径)
成品尺寸 mm 硬度 HRC
160 290
120 200
100 一
100
/
≤ 160 290
120 200
100
100
一
一
50~55 53~ 50~ 50~55 ≥54
53~ 50~ 58 55
≥55
58 55
不予控制
不予控制
2
2
硬度差 HRC I
2
1
2
1
1
4.2.2.2 显微组织
40Cr13钢制关节轴承零件淬回火后显微组织由马氏体、适量的残留碳化物和少量残留奥氏体组成,按本标准附录C规定的第一级别图,平均晶粒度不应小于8级或更细。
G95Cr18、G102Cr18Mo钢制关节轴承零件率回火后显微组织按照JB/T1460的规定。
4.2.2.3 其他技术要求
关节轴承零件淬回火后的其他技术要求应按表8的规定。
表8 不锈钢关节轴承零件回火后其他技术要求
检查项目裂纹回火稳定性脱碳层深度及表面软点套圈变形量外观质量
技术要求
关节轴承零件淬回火后不允许有裂纹关节轴承零件第二次回火前后相应点的硬度差不应大于1HRC 40Cr13钢制关节轴承零件工序间脱碳层深度要求按本标准附录D的规定,G95Cr18、 G102Cr18Mo钢制关节轴承零件工序间脱碳层深度要求按照JB/T1460的规定,或按制造厂与用户双方协商的规定。成品零件工作面不允许有脱碳和表面软点关节轴承零件淬回火后允许的变形量参见本标准附录B或按制造厂与用户双方协商的规定应无碴碰伤、锈蚀及污物附着,整体外观颜色应均匀
4.3 渗碳钢关节轴承零件 4.3.1 关节轴承零件预备热处理技术要求
关节轴承零件正火后的技术要求应按表9的规定。
表9 渗碳钢关节轴承零件正火后技术要求
检查项目硬度显微组织“ 平均晶粒度对正火显微组织的评定有特殊要求时,评定方法按制造厂与用户双方协商的规定。
技术要求 ≤229HBW
按照GB/T13320—2007中图2规定的1级~4级应符合GB/T6394一2017规定的5级或更细的晶粒度级别
a
4
JB/T14004—2020
4.3.2 关节轴承零件渗碳热处理技术要求
4.3.2.1 淬硬层深度
经渗碳热处理后的成品零件淬硬层深度应符合表10的规定。
表10渗碳钢关节轴承零件硬层深度套圈有效壁厚
单位为毫米
淬硬层深度 0.5~0.9 0.9~1.4 ≥1.2 ≥1.6 >2 ≥2.5 >3
> 3.5 6 12 20 30 50 80
≤ 6 12 20 30 50 80
注:对于有特殊要求的成品零件,淬硬层深度按产品图样的规定。 4.3.2.2 硬度
关节轴承零件经渗碳一次率回火或二次率回火后的表面硬度和心部硬度应符合表11的规定。
表11 渗碳钢关节轴承零件表面硬度和心部硬度
表面硬度 HRC
硬化层深度
心部硬度 HRC 30~45 26~45
钢号
mm <2 ≥2
回火后 58~64 56~64
渗碳泽火后
20Cr、20CrMo、20CrMnTi、20CrMnMo、 20CrNiMo、G20CrMo、G20CrNiMo
≥61
注:有特殊要求的轴承零件按产品图样的规定。
4.3.2.3 表面硬度差
当硬化层深度<2mm时,经渗碳热处理的同一零件的表面硬度差应≤2HRC。 4.3.2.4 表面含碳量
经渗碳热处理后的成品零件硬层深度<2mm时,零件表面的含碳量(质量分数)应为0.7%~ 1%;当淬硬层深度≥2mm时,零件表面含碳量(质量分数)不应低于0.7%。若有特殊要求,在表面硬度合格的情况下可另行规定。 4.3.2.5碳化物
经渗碳热处理后的关节轴承零件渗碳层碳化物要求应符合JB/T8881一2020中4.2.3的规定。 4.3.2.6 渗碳表层显微组织及心部显微组织
关节轴承零件经渗碳、淬回火后渗碳表层显微组织应符合JB/T8881的规定;心部显微组织由板条马氏体和一定量的铁素体组成,铁素体含量不应超过附录C的第二级别图。
5