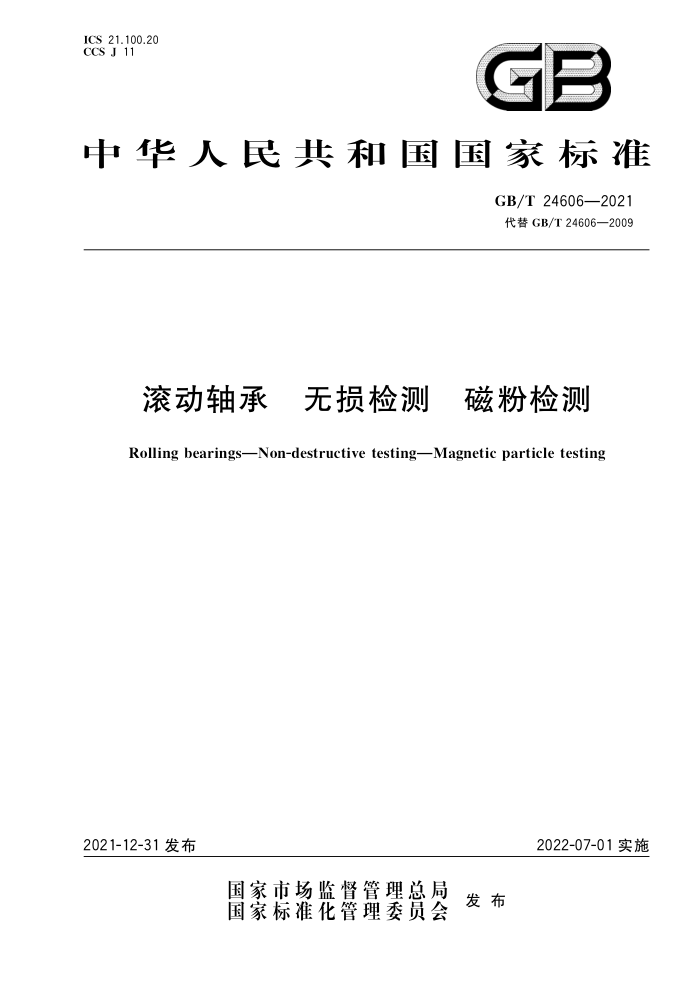
ICS 21.100.20 CCS J 11
GB
中华人民共和国国家标准
GB/T 24606—2021 代替GB/T24606—2009
滚动轴承 无损检测 磁粉检测
Rolling bearingsNon-destructive testingMagnetic particle testing
2021-12-31发布
2022-07-01实施
国家市场监督管理总局
国家标准化管理委员会 发布
GB/T24606—2021
前言
本文件按照GB/T1.1一2020《标准化工作导则 第1部分:标准化文件的结构和起草规则》的规定起草。
本文件代替GB/T24606—2009《滚动轴承 无损检测 磁粉检测》,与GB/T24606—2009相比,除编辑性改动外,主要技术变化如下:
a)增加了部分术语和定义(见第3章); b) 修改了对检测人员的要求(见第5章,2009年版的第5章); c) 增加对辅助器材的要求(见6.2); d) 增加了对磁粉颗粒尺寸的要求(见6.3.1); e) 删除了磁悬液配方,增加了对载液的要求(见6.3.2,2009年版的6.3.2); f) 增加对磁悬液污染物的要求、磁悬液的配制以及污染物的检测方法和水断实验(见6.3.3); g) 修改和细化了对标准试片和标准试块的要求(见6.4,2009年版的6.4); h) 修改了磁化方法(见第7章,2009年版的第8章)。 请注意本文件的某些内容可能涉及专利。本文件的发布机构不承担识别专利的责任。 本文件由中国机械工业联合会提出。 本文件由全国滚动轴承标准化技术委员会(SAC/TC98)归口。 本文件起草单位:洛阳轴承研究所有限公司、瓦房店轴承集团有限责任公司、舍弗勒(中国)有限公
司、张家港市逸洋精密轴承有限公司、合肥市远大轴承锻造有限公司、洛阳LYC轴承有限公司、浙江五洲新春集团股份有限公司、宁波慈兴轴承有限公司、无锡华洋滚动轴承有限公司、浙江德美轴承有限公司、射阳县翔盛检测装备制造有限公司、福建省永安轴承有限责任公司、重庆长江轴承股份有限公司、台州市永宁轴承制造有限公司、大连冶金轴承股份有限公司、江苏赛福探伤设备制造有限公司。
本文件主要起草人:高元安、李慎华、赵普民、李祎文、罗志钢、马桢明、陈翠丽、王明舟、徐林燕、李开元、 唐奇东、吴盛亮、杨俊生、陈正彬、赵兴新、王敬美、杜勇、杨标、林庄
本文件及其所代替文件的历次版本发布情况为: —GB/T24606—2009; 一本次为第一次修订。
I
GB/T24606—2021
滚动轴承无损检测 磁粉检测
1范围
本文件规定了滚动轴承零件(以下简称“零件”)湿法磁粉检测的规程。 本文件适用于铁磁性材料制造的轴承零件(包括原材料、毛坏、半成品、成品、在役检修件)表面和近
表面缺陷的磁粉检测。
2 规范性引用文件
下列文件中的内容通过文中的规范性引用而构成本文件必不可少的条款。其中,注日期的引用文
件,仅该日期对应的版本适用于本文件;不注日期的引用文件,其最新版本(包括所有的修改单)适用于本文件。
GB/T261一2008闪点的测定宾斯基-马丁闭口杯法 GB/T265一1988石油产品运动粘度测定方法和动力粘度计算法 GB/T9445一2015无损检测人员资格鉴定与认证 GB/T12604.5—2020无损检测术语磁粉检测 GB/T15822.2一2005无损检测磁粉检测第2部分:检测介质 GB/T23907—2009 无损检测磁粉检测用试片 JB/T6641—2017滚动轴承残磁及其评定方法 JB/T8290—2011 无损检测仪器 磁粉探伤机
术语和定义
3
GB/T12604.5一2020界定的以及下列术语和定义适用于本文件。
3.1
当量直径 equivalentdiameter Deff 与该零件的周长相同的圆柱体的直径为该零件的当量直径,
3.2
缺陷defect 尺寸、取向、位置或性质对零件的有效使用会造成损害或不满足规定验收要求的不连续性。
3.3
中心导体法 centralconductor 导电体穿过被检件孔径中心,通电后,在被检件内部及其周围形成周向磁场的磁化方法,[来源:GB/T12604.5—2020,2.5,有修改
3.4
偏心导体法 non-central conductor 如果空心被检件直径太大,探伤机所提供的磁化电流不足以使被检件表面达到所要求的磁场强度
时,可将芯棒偏置,即将导体穿入被检件,并贴近被检件内表面放置,电流从导体上通过形成周向磁场的
1
GB/T24606—2021
定周期为一年。 6.3磁悬液 6.3.1磁粉
6.3.1.1磁粉的最大粒度应不大于45m(筛网目数约320目)。荧光磁粉或非荧光磁粉均应在经制造厂主管部门批准使用的具有自然缺陷(或人工缺陷)的试片(块)上进行校验,缺陷磁痕显示清晰时方可采用。 6.3.1.2 磁粉的其他技术要求应符合GB/T15822.2一2005的规定。
6.3.2载液 6.3.2.1油基载液
油基载液应符合表1的规定。
表1油基载液
项目闪点(闭口)
质量指标 ≥94℃ ≤3.0 N5.0 ≤1.5
试验方法 GB/T 261—2008
40 ℃ 20 ℃
运动黏度 mm/s
GB/T 265—1988
本底荧光 cd/m2
荧光系数测试仪
适于荧光磁粉检测用油基载液
6.3.2.2 2水基载液
水基载液是在水中加入润湿剂和防锈剂制成的,需要时可加入消泡剂。水基载液应具有良好的湿
5ZC润性和防锈性。
6.3.3磁悬液体积分数
非荧光磁粉磁悬液的体积分数应为1.2mL/100mL~3.0mL/100mL;荧光磁粉磁悬液的体积分数应为0.1mL/100mL~0.6mL/100mL。 6.3.4磁悬液污染物要求
在白光或黑光(用于荧光磁悬液)照射下观察,测量管沉积物若明显分层时,上层污染物体积不应超过磁悬液体积的30%。 6.3.5磁悬液配制
采用磁粉检测专用的载液、浓缩液或磁膏,按照产品说明书的要求进行配制。配制后用具有自然缺陷或人工缺陷的试片(块)进行验证,缺陷磁痕显示清晰,方可使用。 6.3.6磁悬液体积分数和污染物的判定 6.3.6.1 磁悬液体积分数使用最小刻度为0.05mL(非荧光磁粉可使用最小刻度为0.1mL)的梨形沉淀
3
GB/T24606—2021
管或锥形瓶进行测试。测量前应使磁悬液充分搅拌均匀,测量时将磁悬液喷淋头持续喷淋1min后,从磁悬液喷头直接接取100mL磁悬液,水基载液静止沉淀30min,油基载液静止沉淀40min~45min,再读取沉淀在管底的磁粉刻度值。 6.3.6.2磁悬液污染物达到以下要求时,应更换磁悬液:
在白光和黑光(用于荧光磁悬液)下观察,测定管中沉积物若明显分成两层且上层污染物体积超过磁悬液体积的30%;
一在黑光下用未使用过的标准磁悬液与使用过的磁悬液比较观察,荧光磁粉的亮度和颜色明显
降低或磁悬液沉积物之上的载液发荧光,以及出现磁悬液变色、结团等现象。
6.3.7水断试验
对于小型零件,将表面干净的待检零件浸人磁悬液中,并在浸没结束后观察工件表面。磁悬液所形
成的薄膜能够连续均匀覆盖整个零件表面,则视为合格。如薄膜破裂,暴露出零件表面,则润湿剂浓度过低,需进行调整。
对于大型零件,将表面于净的待检零件采用单股水流流下,用手抹断,如能续流,则视为合格。如不
能续流,则需调整润湿剂浓度。 6.4标准试片及试块
零件检测时根据零件的形状可选择符合GB/T23907一2009规定的不低于A1-15/50、A1-30/100
和D-15/50的中灵敏度标准试片,或经客户认可的其他标准试片或试块。
7磁化方法
7.1零件磁化时,至少应对零件的同一受检部位在互相垂直或接近垂直的两个方向上实施磁化, 7.2连续法检测时,可采用周向磁化或纵向磁化,也可采用复合磁化对零件进行检测。
注:复合磁化是对零件同时进行周向磁化和纵向磁化,在零件上产生一个随时间变化的复合磁场,可检出各个方向
上的缺陷。复合磁化仅适用于连续法。
7.3剩磁法检测时,应顺序采用周向磁化和纵向磁化,观察完磁痕后的零件需经退磁才可更换磁化方式。周向磁化和纵向磁化的顺序可自行确定 7.4经用户和制造厂协商确定后,也可采用其他磁化方法
8磁化规范
8.1总则
磁化后零件表面的切向磁通密度应≥1T。通常轴承零件表面磁场为2kA/m~6kA/m时,可获
得超过1T切向磁通密度。采用特斯拉计检测零件表面磁场强度来确定磁化电流,也可通过标准试片上的人工刻槽显示完全且清晰来确定磁化电流。轴承零件采用通电法、导体法、感应电流法、环形件绕电缆法、线圈法磁化时,按9.2~9.6的规定选择磁化规范
SAG
8.2通电法
通电法磁化规范按表2的规定。
4
GB/T24606—2021
表2通电法磁化规范
方法剩磁法连续法
直流电 I=35D~60D I=10D~20D
交流电 I=25D~40D I=8D~15D
半波整流电 I=12D~20D I=4D~8D
全波整流电 I=20D~40D I=7D~15D
8.3导体法
8.3.1中心导体法
采用中心导体法时,中心导体的轴线应与零件的中心轴近于重合并应采用表2规定的磁化规范。 8.3.2偏心导体法 8.3.2.1采用偏心导体法时,中心导体贴紧零件内壁并应采用表2规定的磁化规范,其中,D=中心导体直径十2倍零件壁厚。 8.3.2.2偏心导体磁化时,沿零件周长的有效磁化区为中心导体直径的4倍,绕中心导体转动零件检测其全部周长,每次应有约10%的有效磁化重叠区。 8.4 感应电流法
感应电流法磁化规范为:
连续法:NI=(8~15)Df;剩磁法:NI=(25~40)Df。
S
8.5环形件绕电缆法
环形件绕电缆法磁化时,应采用表2规定的磁化规范,并应以NI代替I。 8.6 线圈法 8.6.1采用连续法磁化 8.6.1.1对于偏心放置的零件,且磁化线圈横截面面积不小于10×零件横截面面积(低填充系数)时的磁化规范按公式(1):
45 000 L/D
NI :
.(1)
8.6.1.2 :当磁化线圈横截面面积小于2×零件横截面面积(高填充系数)时,零件的长径比L/D≥3时的磁化规范按公式(2):
35 000 L/D+2
NI :
·(2)
8.6.1.3当磁化线圈横截面面积介于2×零件横截面面积和10×零件横截面面积之间(中填充系数)时,其磁化规范根据实际应用情况在公式(1)和公式(2)计算结果之间选择 8.6.2采用剩磁法磁化
剩磁法纵向磁化规范如下: a)零件的长径比L/D≥10时,空载线圈的中心磁场强度应大于12000A/m; b)零件的长径比2
5
GB/T24606—2021
c)零件的长径比L/D≤2时,应将多个零件连接在一起,连接后应L/D>5。空载线圈的中心磁
场强度应根据实际L/D值按a)或b)选取。
8.7磁轭法
当使用磁轭检测时,磁极与零件表面间隙应不超过0.5mm。交流电磁轭至少应有45N的提升力;直流电(包括整流电)磁轭或永久性磁轭至少应有177N的提升力;交叉磁轭至少应有118N的提升力。
9退磁
9.1检测合格的零件应进行退磁。检测后尚有加热至700℃以上的热处理工序的零件可不退磁。 9.2多个零件同时退磁时,应将零件之间留有一定的间隔,摆放于非金属的料盘或料筐中进行退磁 9.3退磁时所使用的电流值不应小于磁化时所使用的电流值。一般情况下,交流电磁化用交流电退磁,直流电磁化用直流电退磁。 9.4零件退磁后,应进行残磁测定,其要求及方法应符合JB/T6641一2017的规定。 9.5 5已退磁的零件,应远离磁化设备及退磁设备1.5m以外。
磁粉检测程序及操作注意事项
10
10.1磁粉检测程序
磁粉检测程序如下。 a) 检测前的准备工作:
1) 检测场地检查,消除不安全因素; 2) 磁粉探伤机(照度及紫外辐照度、相关设备、器材)检查; 3) 零件表面预清洗,清除纤维、油污、氧化皮、铁锈、金属屑等杂物; 4) 磁悬液体积分数及污染物检测; 5) 水断试验(仅限水基磁悬液); 6) 系统灵敏度测试; 7) 零件内部存在有可能影响探伤效果的残磁时,检验前应对零件进行退磁
b) 选择并确定磁化规范。 c) 按以下两种方法进行充磁及施加磁悬液:
1)连续法:施加磁悬液,同时充磁,充磁时间为1s~3s,停止施加磁悬液后再连续充磁1次
-
2次,每次0.5s~1s; 2)剩磁法:充磁后,采用浸泡法施加磁悬液,浸泡时间不少于30s。
d) 观察、评定及缺陷记录:对零件上形成的磁痕应及时观察,并评定是否为缺陷磁痕。采用照相
法、透明胶带粘印法、书面描述等方法对缺陷进行记录, e) 对合格零件和不合格零件进行区分标识。 f) 退磁。 g) 如有疑问可重复b)~f)。 h) 检测后的合格零件应及时清洗,如有需要进行防锈处理。
SAC
10.2 磁粉检测操作注意事项
磁粉检测操作应注意: a)零件夹持在探伤机磁化夹头之间时,夹持力要适当,不应使零件产生变形; 6