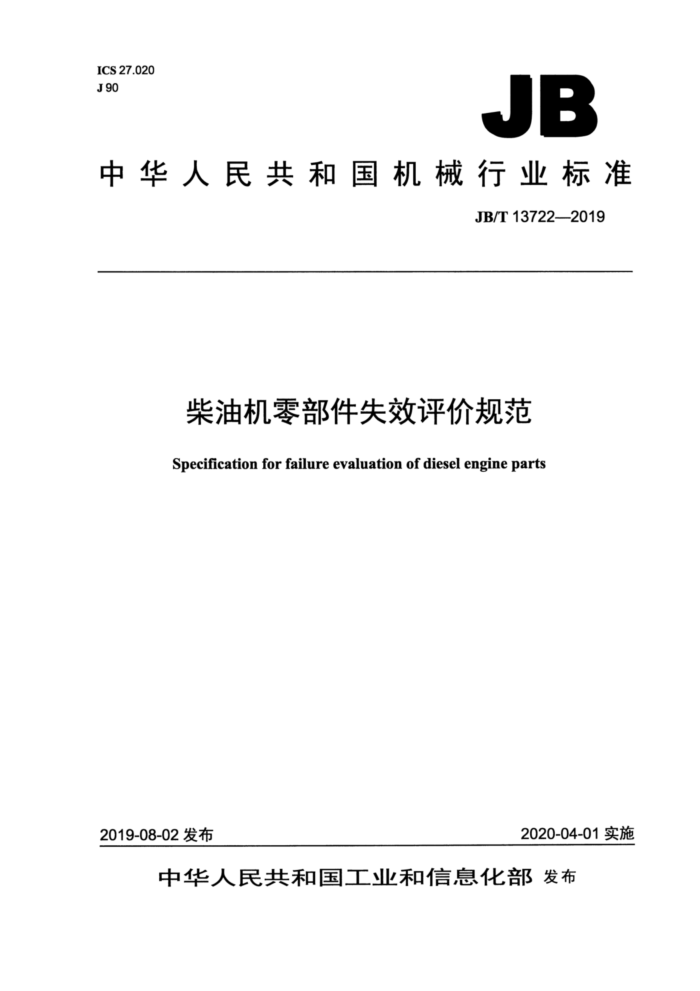
ICS 27.020 J 90
JB
中华人民共和国机械行业标准
JB/T 13722—2019
柴油机零部件失效评价规范
Specification for failure evaluation of diesel engine part
2020-04-01实施
2019-08-02 发布
中华人民共和国工业和信息化部发布
JB/T 13722—2019
目 次
前言。 1范围. 2规范性引用文件 3术语和定义… 4失效分析方法..
Ⅱ
4.1总则... 4.2柴油机故障分析.. 4.3零部件失效分析.. 5失效评价 5.1零部件失效判定 5.2柴油机故障检测结果的记录 5.3零部件失效检测结果的记录附录A(规范性附录)柴油机主要故障现象附录 B (资料性附录) 四类损伤细分表, B.1机械损伤 B.2腐蚀损伤 B.3 热损伤. B.4摩擦损伤附录C(规范性附录)部分零部件失效评价规则..
o
图 1 柴油机零部件失效分析流程
表 1 柴油机故障分类. 表 2故障类型与 FMEA 严重度的对应关系及评分表表3零部件损伤分类.. 表4零部件的主要失效模式表 5 柴油机故障记录表. 表 6 零部件失效记录表. 表 A.1 柴油机故障现象. 表 B.1 机械损伤分类.. 表 B.2 腐蚀损伤分类表 B.3 热损伤分类表 B.4 摩擦损伤分类表 C.1 部分零部件失效评价规则
10 11
JB/T 13722—2019
前言
本标准按照GB/T1.1一2009给出的规则起草。 本标准由中国机械工业联合会提出。 本标准由全国内燃机标准化技术委员会 (SAC/TC177)归口。 本标准起草单位:广西玉柴机器股份有限公司、云南西仪工业股份有限公司、潍柴动力股份有限公
司、上海内燃机研究所、上海汽车集团股份有限公司商用车技术中心、昆明理工大学、宁波鑫达杰电器有限公司、同济大学。
本标准主要起草人:赵添常、邓伟、计维斌、杨维沛、郭圣刚、邓斌、罗志坚、谢亚平、陈云清、 雷基林、荣超、胡惠祥、倪计民。
本标准为首次发布。
II
JB/T 13722—2019
柴油机零部件失效评价规范
1范围
本标准规定了柴油机零部件故障和失效的术语和定义、失效分析方法、失效评价。 本标准适用于柴油机零部件失效模式的评定,柴油机整机故障的分析与评价也可参考采用。
2规范性引用文件
下列文件对于本文件的应用是必不可少的。凡是注日期的引用文件,仅注日期的版本适用于本文
件。凡是不注日期的引用文件,其最新版本(包括所有的修改单)适用于本文件。
GB/T23339—2018内燃机曲轴技术条件 GB/T23341.2一2018涡轮增压器第2部分:试验方法 JB/T5239.4一2011柴油机柴油滤清器第4部分:试验方法 JB/T 9753.2--2008 3内燃机气缸盖与机体第2部分:铸铁气缸盖技术条件 JB/T 11323—2013 中小功率柴油机可靠性评定方法 JB/T 11414—2013 合成式喷油泵总成可靠性考核评定方法、台架试验方法、故障分类及判定
规则
JB/T 11416—2013 喷油器总成可靠性考核评定方法、试验方法、故障分类及判定规则 JB/T11876—2014行 往复式内燃机缸套活塞环组件拉伤试验方法 JB/T12034—2015 喷油嘴偶件可靠性考核评定方法、试验方法及失效判定
3术语和定义
下列术语和定义适用于本文件。
3.1
失效failure 产品执行规定功能能力的终止。
3.2
故障fault 产品不能执行规定功能的状态,预防性维修及其他计划性活动或缺乏外部资源的情况除外。 注:故障通常是产品自身失效后的状态,但也可能在失效前就存在。
3.3
零部件失效 component failure 零部件损伤现象不断地发展,造成应有的功能损害,达到某一规定功能能力的丧失。
3.4
失效模式failure mode 失效的外在表现形式和过程规律,一般可理解为失效的性质和类型。
1
JB/T 13722—2019
4失效分析方法
4.1总则
柴油机零部件失效分析需结合柴油机故障分析开展。柴油机故障分析需锁定与故障相关的子系统,然后分析确定与柴油机故障相关的失效或损伤零部件,对照失效或损伤零部件找出失效模式以及引起失效的原因。对根据柴油机故障就能确定失效的零部件进行分析,找出失效模式以及引起失效的原因。柴油机零部件失效分析流程如图1所示。
柴油机故障
柴油机故障分析
零部件失效分析
锁定与故障相关的子系统
找出失效模式以及引起失效的原因
分析确定与柴油机故障相关的失效或损伤零部件
图1 柴油机零部件失效分析流程
4.2柴油机故障分析 4.2.1故障分类
根据柴油机发生故障造成的危害程度或损坏严重程度和修复难易程度,将故障分为I类故障(致命故障)、Ⅱ类故障(严重故障)、Ⅲ类故障(一般故障)和IV类故障(轻度故障),其定义和分类原则见表1。
表1柴油机故障分类定义
类别 名称 I
分类原则
重要零部件严重损坏导致的危害人员安 危及行驶安全,导致人身伤亡,引起重要零部全或造成重大经济损失的故障
致命故障
件报废,或对周围环境造成严重危害的故障
主要性能超过规定限值、主要零部件损伤 影响行驶安全,导致主要总成、零部件损坏,
严重故障
II
需要解体才能排除或造成柴油机性能显著下降的故障
或失效导致的故障需要停机检修、不需要更换主要零部件并 造成停机或性能下降,但一般不会导致重要总
II
一般故障
成、零部件损坏,并可用随机工具和易损备件或价值很低的零件在短时间内修复的故障
可用随机工具排除的故障
IV 轻度故障 一般不导致停机、不需要更换零件并可用 一般不会导致停机或性能下降,不需更换零
随机工具在短时间内排除的故障
件,用随机工具在短时间内能轻易排除的故障
4.2.2故障类型与FMIEA严重度的关系及评分表
故障类型与FMEA(失效模式与影响分析)严重度的对应关系及评分见表2,评估依据是根据对产品的影响严重性或对用户的影响程度而定。 2
JB/T 13722—2019
表2故障类型与FMEA严重度的对应关系及评分表
故障类型
故障影响
评估依据
严重度数
潜在失效模式影响了发动机的安全运行,或包含不符合政府法规
10
致命故障(I类故障) 或法规要求
不符合安全性 的情形,失效发生时无预警
潜在失效模式影响了发动机的安全运行,或包含不符合政府法规的情形,失效发生时有预警
9
严重故障(Ⅱ类故障) 或功能降低
基本功能丧失 基本功能丧失(发动机无法正常运行,不影响发动机安全运行)
8 7 6 5 4
基本功能降低(发动机可以运行,但性能下降)
次要功能丧失 次要功能丧失(发动机可以运行,但舒适、便捷功能不可实施)
一般故障 或功能降低(Ⅲ类故障)
次要功能降低(发动机可以运行,但舒适、便捷性能下降)有外观、可听噪声、发动机操作项目上的问题,并且被绝大多数
用户(>75%)察觉有外观、可听噪声、发动机操作项目上的问题,并且被许多用户(50%)察觉有外观、可听噪声、发动机操作项目上的问题,但只被少数识别能力敏锐的用户(<25%)察觉没有可识别的影响
干扰
3
轻度故障(IV类故障)
2
没有影响
1
4.2.3故障现象
柴油机主要故障现象见附录A。 4.2.4故障检测方法
针对柴油机故障现象,目前主要有三种检测方法: a)基于数据库的方法:在长期故障分析的基础上,总结形成FMEA数据库,当再次出现同类的异
常故障时,可借鉴故障经验数据库开展分析检测的方法; b)基于试验的方法:根据相关试验标准或试验规范来进行分析检测的方法; c)基于故障特征码的方法:当柴油机工作不正常时,通过查看电控系统的故障码来进行分析检测
的方法。
4.2.5故障解体分析
针对柴油机故障现象,对故障机解体分析中应遵循以下原则: a)故障码先行; b)由外到内; c)由简到繁; d)依据结构和原理; e)掌握数据; f)经验判断。
4.3零部件失效分析 4.3.1损伤分类
独立于损伤原因、损伤过程、损伤形态,以及受损部件的类型、功能和机械结构,柴油机零部件中出现的所有损伤都可以通过一系列物理、化学和电化学过程来解释,并可以分为由机械载荷引起的损
3
JB/T13722—2019
伤、由于在潮湿介质中造成的腐蚀所产生的损伤、由热载荷产生的损伤以及由摩擦载荷引起的损伤四类,零部件损伤分类见表3。更进一步的损伤分类可参见附录B。
表3零部件损伤分类
损伤分类机械损伤腐蚀损伤热损伤摩擦损伤
情况说明
外力断裂、疲劳断裂无机械负荷的腐蚀、机械作用(应力腐蚀)、氢腐蚀热断裂、内部组织热载荷变化形成裂纹、热变形、高温腐蚀、沉积物造成的功能损伤,扩散过程造成的损伤滑动磨损、滚动磨损、表面疲劳磨损、磨粒磨损、流动磨损(冲蚀)
4.3.2失效模式
常见失效模式可分为以下六类: a)损坏型失效模式:包括断裂、开裂、碎裂、裂纹、点蚀、烧蚀、击穿、变形、拉伤、龟裂和压
痕等; b)退化型失效模式:包括老化、变质、剥落、异常磨损等; c)松脱型失效模式:包括松脱、脱落等; d)失调型失效模式:包括压力过高或过低、行程失调、间隙过大或过小、干涉和卡滞等; e)堵塞与渗漏型失效模式:包括堵塞、气阻、漏水、漏油、渗油等; f)性能衰退或功能失效型失效模式:包括功能失效、性能衰退、排放超标、异响等。 柴油机零部件的主要失效模式见表4。
表4零部件的主要失效模式
失效模式断裂崩缺 零部件部分材料脱离本体,如齿轮崩缺(崩齿)、气门崩块等开裂 零部件表面产生明显裂缝龟裂
概念定义及情况说明
零部件有限面积的几何表面分离,如轴类、杆类、支架、传动带、齿轮等零件的断裂
零部件表面产生网状裂纹,如主轴瓦的龟裂等零部件变成许多不规则形状的碎块,如轴承、摩擦片、衬套、塑料壳罩等零部件的碎裂
碎裂脆裂 材料受力后没有发生明显的塑性变形就突然发生的断裂爆裂 储存液体或气体的容器,或传输管路受到高压,造成突然破裂烧蚀 零部件表面因产生局部熔化而发生的损坏,如气缸体、缸盖、活塞顶、轴瓦的烧蚀烧损 零部件表面因高温或其他原因造成大面积损坏烧死 零部件连接后由于高温作用造成无法拆卸,如排气管螺栓螺纹高温变形,而导致螺栓无法拆卸
接触液体的零部件表面,因空泡爆炸、共振、电化学等腐蚀原因而造成麻点状和针状小孔,如气缸套、 水泵等的穴蚀腐蚀局限在零部件金属表面各个很小区域,向金属内部扩展,形成点状孔穴,如齿轮齿面、凸轮表面、 挺杆等零部件点蚀物体表面相对运动时工作表面物质损失,并且损伤程度超过可接受的范围
穴蚀
点蚀磨损干磨 机油、润滑油不良,造成零部件间的摩擦
零部件局部磨损,如缸套、轴瓦等产生的非均匀性磨损,气门与座圈之间的非均匀性磨损等
偏磨
4
JB/T 13722—2019
表4零部件的主要失效模式(续)
失效模式碰伤 零部件之间相互碰撞或者异物与零部件发生碰撞,造成零部件表面损伤划伤
概念定义及情况说明
在摩擦表面滑动方向上形成宽而深的犁痕式破坏
拉伤 摩擦副相对运动时,沿摩擦表面滑动方向形成片状伤痕,如缸筒、轴瓦等的拉伤变形 物体在外来因素作用下产生的形状和尺寸的改变压痕 零部件表面产生的凹状痕迹拉缸 缸内壁被拉成很深的沟纹,活塞、活塞环与气缸壁摩擦副丧失密封性而影响内燃机正常运转抱死 两个相对运动的部件(如轴颈与轴瓦、缸套与活塞等)相互粘结和咬住剥落 疲劳磨损时,从摩擦表面以鳞片形式分离出磨屑脱落
附着物丧失连接而造成的零部件分离,主要指油漆、涂层等附着物
变色 由于高温造成零部件表面颜色的变化积炭
由各种原因造成的燃油不完全燃烧,致使一部分炭粒和杂质沉积在燃烧室壁面和活塞等零部件上通常在天然水中都溶解有一部分矿物盐类,当水在密闭容器内受热时,碳酸盐会在密闭容器的壁面上形成一层固态附着物
结垢结胶 机油受高温焦化并与炭粒、灰分等胶结成胶状物,通常是指燃烧室及其周围高温零部件的结胶腐蚀 金属与环境间的化学作用,使金属性能发生变化,导致金属、环境及其构成体系功能受到损伤锈蚀
金属在大气中由于氧、水分及其他杂质而引起的腐蚀或变色非金属零件随使用时间的增长或周围环境的影响,性能衰退,如密封胶圈等橡胶类零件的老化
老化氧化 零部件表面物质与氧元素产生化学反应,影响性能或使用变质 流体介质随使用时间或环境变化,导致化学成分的变化,如燃油、机油、防冻液等物质的变质
零部件间的接触表面由于过热、化学变化等原因,致使接触表面处材料分子的转移,产生局部吸附、 粘在一起,如离合器与飞轮之间的粘连
粘连
4.3.3失效分析步骤与检测方法 4.3.3.1 失效分析步骤
失效分析一般由以下三个步骤构成: a)查清失效对象的状态; b)分析并确定失效原因和机理; c)做出分析结论,提出改进措施。
4.3.3.2 :失效检测方法
对失效零部件进行分析检测时,应关注其主要失效模式,现象特征,宏观、微观及表面性能。在柴油机零部件失效分析中主要有以下八类检测方法:
a)宏观、低倍检测:通过肉眼、放大镜和体视显微镜等直接观察失效零部件或整个部件,了解失
效零部件的功能,对失效系统和失效零部件之间的关系有一全面的了解;得到宏观或低倍形貌、颜色、位置、表面缺陷、尺寸信息。
b)金相组织分析:采用光学显微镜对金属类产品的金相显微组织进行检查,获得显微组织、晶粒
度、第二相的分布,夹杂物的类型、尺寸、分布、数量等检测数据。 c)电子显微检测:用透射电镜、扫描电镜进行分析。根据断口谱形特征,确定材料或构件的失效
5