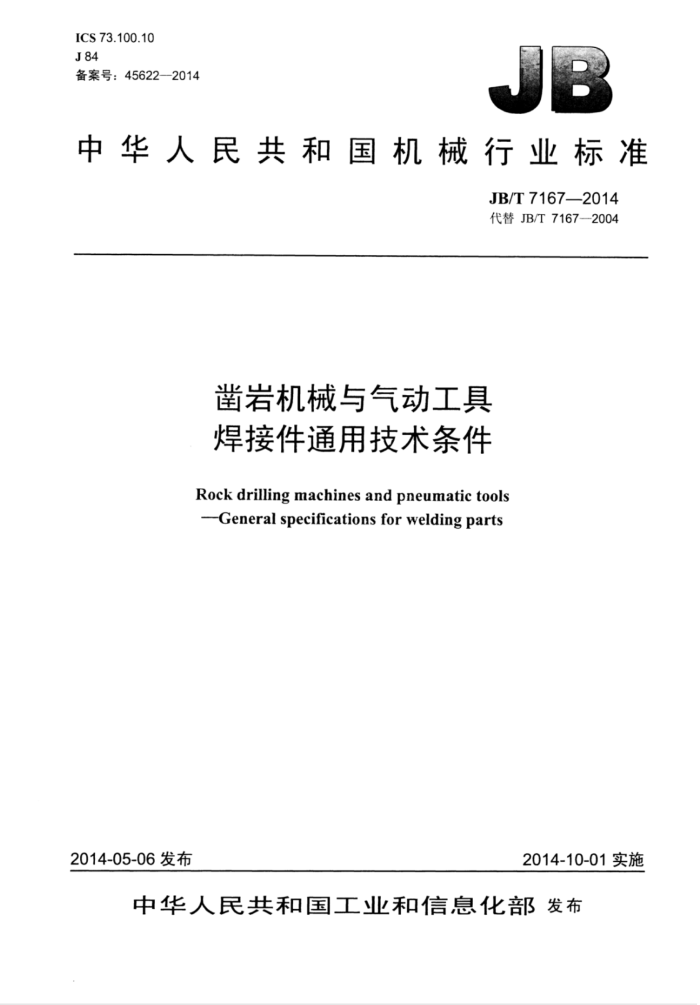
ICS73.100.10 J84 备案号:45622—2014
中华人民共和国机械行业标准
JB/T7167—2014 代替JB/T7167—2004
凿岩机械与气动工具焊接件通用技术条件 Rock drilling machines and pneumatic tools General specifications for welding parts
2014-10-01实施
2014-05-06发布
中华人民共和国工业和信息化部发布
JB/T7167-2014
目 次
前言 1范围.. 2 规范性引用文件材料..
I
3
4焊前准备 4.1 下料... 4.2 下料后的矫正 4.3 弯曲成型定位焊.
5 6
接 6.1 焊前. 6.2 焊接 7焊后要求. 7.1 一般要求 7.2 焊接变形矫正, 7.3 焊接件的形状偏差、尺寸偏差与焊缝缺陷 8检查与验收. 8.1 焊接件的检查项目和检查方法 8.2 焊缝严密性试验. 8.3 焊缝的压力试验, 8.4 焊缝的钻孔试验.. 8.5 焊缝力学性能试验 8.6 无损检测, 8.7 般规则.
#EE9
.9
9
.10 10 .10
JB/T7167-2014
前言
本标准按照GB/T1.1—2009给出的规则起草。 本标准代替JB/T7167—2004《凿岩机械与气动工具 焊接件通用技术条件》,与JB/T7167一2004
相比主要技术变化如下:
增加了目次: —增加了GB/T699、GB/T700、GB/T1591、GB/T3077; 一删除了已废止的GB/T2649、GB/T2655、GB/T2656、GB/T14958(2004年版第2章)
-将4.1.1焊前准备项目中的厚度大于16mm调整为大于8mm 将4.1.2焊前准备项目中的厚度小于5mm调整为小于6mm;一删除了8.5.2中的e)项和f)项(2004年版8.5.2)。
本标准由中国机械工业联合会提出。 本标准由全国凿岩机械与气动工具标准化技术委员会(SAC/TC173)归口。 本标准起草单位:天水风动机械有限责任公司、天水凿岩机械气动工具研究所。 本标准主要起草人:程延军、李衍斌、马文瑾。 本标准所代替标准的历次版本发布情况为:
JB7167—1993JB/T7167-2004。
II
JB/T7167—2014
凿岩机械与气动工具焊接件通用技术条件
1范围
本标准规定了焊接材料和原材料的使用条件,下料焊接,焊后等方面的要求及检查与验收方法本标准适用于由碳素结构钢、低合金结构钢采用手工电弧焊、半自动焊、自动焊、气体保护焊等方
法制造的凿岩机械与气动工具的焊接件。
2规范性引用文件
下列文件对于本文件的应用是必不可少的。凡是注日期的引用文件,仅注日期的版本适用于本文
件。凡是不注日期的引用文件,其最新版本(包括所有的修改单)适用于本文件。
GB/T 699 优质碳素结构钢 GB/T700 碳素结构钢 GB/T1591 低合金高强度结构钢 GB/T2650 焊接接头冲击试验方法 GB/T2651 焊接接头拉伸试验方法 GB/T2653 焊接接头弯曲试验方法 GB/T2654 焊接接头硬度试验方法 GB/T3077 合金结构钢 GB/T3323 金属熔化焊焊接接头射线照相 GB/T5117 非合金钢及细晶粒钢焊条 GB/T5118 热强钢焊条 GB/T8110 气体保护电弧焊用碳钢、低合金钢焊丝 GB/T11345 焊缝无损检测超声检测技术检测等级和评定 GB/T14957 熔化焊用钢丝 JB/T6046碳钢、低合金钢焊接构件焊后热处理方法 JB/T10045.3一1999热切割气割质量和尺寸偏差
3材料
3.1用于焊接结构件的原材料,其化学成分、力学性能应符合GB/T699、GB/T700、GB/T1591、GB/T 3077的规定。规格、表面质量应符合图样或工艺文件的要求。 3.2碳钢和低合金钢焊条应符合GB/T5117和GB/T5118的规定。 3.3焊接用钢丝应符合GB/T8110和GB/T14957的规定。 3.4用于焊接件的原材料(如板材、型材等)和焊接材料(如焊条、焊丝、焊剂等)进厂时应经质量检验部门检查验收合格后方可使用。 3.5原材料、焊接材料的代用应经技术主管部门批准后方可使用。
1
JB/T71672014
4焊前准备
4.1下料 4.1.1 厚度大于8mm的金属板材应优先采用气割下料。 4.1.2 厚度小于6mm的金属板材不应采用火焰切割。 4.1.3 金属材料剪切后,边棱与表面的垂直度误差应不大于1/10,切口边缘不应有裂纹及超过1mm的缺棱,并应清除飞边毛刺。 4.1.4 金属材料气割后,应清除熔渣,并修圆棱角。 4.1.5 剪切下料尺寸偏差应符合表1的规定。 4.1.6 气割下料尺寸偏差应符合表2的规定。
表1
单位为毫米
用于不切削加工
用于切削加工
板 材 厚 度 >8~14
切口长度
≤3
>3~8
≤3
>3~8
>8~14
极 限 偏 差
+3:8 9 18 2.8 19.9
+1: +1. +2:4 +9.3 2
≤500 >500~1000 >1 000~1600 >1600~2500 >2500~4000
+2.3 +3:8 153 +8:9 单位为毫米
±0.8 ±1 ± 1.2 ± 1.4 ± 1.8
±1 ± 1.3 ± 1.5 ± 1.7 ± 2.1
± 1.4 ± 1.7 ± 1.9 ± 2.1 ± 2.5
表2
用于不切削加工
用于切削加工
板 材 厚 度
割口长度
≤12 >12~20>20~40 >40~60 ≤12 >12~20 >20~40 >40~60
极 限 偏 差 ±2
≤500
2:8 +2.2 +2.9 129
± 1.0 ± 1.2
± 1.5
>500~1000 ±1.5 ± 1.7 ±2.0 ± 2.5 12.9 +9: +2.9 +8:8 >1 000~1 600 ±1.8 ± 2.1 ±2.3 ±2.8 +2.4 +3:8 13.1 39
± 2.2 ±2.5 ± 2.7 ± 3.2 +9: 3.4 19. 3.6 ±2.7 ±2.9 ± 3.2 ±3.7 +19.4 9.2 4: 12.2 ± 3.3 ±3.5 ±3.8 ±4.3 14.3 +13.5 143 48
≥>1600~2500 >2500~4000 ≥40006300
14.s *16.8 1ts 1.
>6300 4.1.7 金属材料气割下料的零件不切削加工时,按JB/T10045.3一1999的规定检查验收, 切割面质量
±4
±4.5 ±5.0
±4.2
为IⅡI级、切割面平面度为2等、割纹深度为2等。 4.1.8 优先采用数控、光电、仿形等自动或半自动气割下料。 4.1.9 气割下料后板材边棱之间的垂直度误差与平行度误差不应大于相应尺寸公差的一半。 4.1.10 气割下料后的型材切割断面对其表面的垂直度误差与平行度误差不应大于相应尺寸公差的一半。 2
JB/T71672014
4.2 下料后的矫正
4.2.1下料后的板材经矫正后的平面度公差应符合表3的规定。 4.2.2 下料后的各种型钢经矫正后的直线度公差应符合表4的规定。
表3
单位为毫米
板材长度 500~1000
≤500 Lmax
≥1000 L=1000
板材厚度
简 图
L=500 平面度公差
≤4 >4~12 >12
≤1.0 ≤0.8 ≤0.5
≤1.5 ≤1.0 ≤0.6
≤2.0 ≤1.5 ≤1.0
→
最大范围:t 最大距离。
广
表4
单位为毫米
项目
公差 L≤100时≤1.0 L>1000时≤L/1000
简 图
L
直线度公差t
各种型钢直线度公差不应大于5
4.3 弯曲成型 4.3.1 管子弯曲成型应装砂热弯,加热温度在800℃一950℃,弯山过程中温度不应低于700℃,冷弯应在专门的弯管机上进行。 4.3.2 管子的弯曲半径应大于管子外径的3倍。 4.3.3 管子弯曲半径偏差、圆度、波纹深度应符合表5的规定。
单位为毫米
表5
M
子 外径
类别 R>75~125 2
示意图
30≤38 ≤51 ≤60 ≤70≤83 ≤102 ≤108 ≤125 ≤150 ≤200
2
3
4
弯曲半径
2 2 3
R的极限 R>125~300
- 5 4 3
1
R>300~400 R>400~1000 R>1000
5 4 4 4 3 3
5
5
5
偏差 (±)
4 3
5
R≤75 3.0 R>75~100 2.5 3.1 R>100~125 2.3
在弯曲半径处的
2.6 3.6
1.7 2.1 3.2
圆度 R>125~160
R>160~200 R>200~300 R>300~400
1.7 2.8 3.6 1.6 2.6 3.0 4.6 5.8
a或b
2.4 3.8 5.0 7.2 8.1
3
JB/T71672014
表5(续)管子外径
单位为毫米
类别
示意图
≤30≤38 ≤51≤60 ≤70≤83 ≤102 ≤108≤125≤150|≤200
在弯曲 R>400~500 半径处的
5
1.8 3.1 4.2 6.2 7.0 7.6 1.5 2.3 3.4 5.1 5.9 6.5 7.5 1.2 1.9 2.5 3.6 4.4 5.0 6.0 7.0
R>500~600
圆度 a或b
a/2
R>600 弯曲处的波纹深度
-
一
1.0 1.5 1.5 2.0 3.0 4.0 5.0 6.0 7.0 8.0
J
4.3.4 弯曲成型的筒体偏差应符合表6的规定。 4.3.5 弯曲件弯曲成型后,弯曲部位不应有裂纹、较严重拉薄、明显锤击和冲压的痕迹。 4.3.6 弯曲件不应有严重脱碳现象。
表6
单位为毫米
外径DH
偏 差
主简体壁厚 >16~30
表面凸凹量
直径极限偏差 ADH(±)
≤16
>30
公称尺寸
c 1.2 1.5 2.0 2.5 3.0 3.5 4.0 4.0 5.0 5.0
圆度t (t=b-a)
1.5 2.0 2.5 3.0 4.0 5.0 6.0 7.0 8.0 9.5
1.2 1.5 2.0 2.5 3.0 4.0 5.0 6.0 7.0 8.0
≤400 >400~500 >500~630 >630~800 >800~1000 >1000~1250 >1250~1600 >1600~2000 >2000~2500 >2500~3 150
2.0 2.5 3.0 4.0 5.0 6.0 7.5 9.0 11.0 13.0
1.0 1.2 1.5 2.0 2.5 3.5 4.0 5.0 6.0 7.0
C aV+H
5定位焊
5.1 定位焊的零件应是检查合格的零件。 5.2 定位焊时,不应采用强力、锤击变形等措施,应保证各被焊件之问的弱应力连接。 5.3 定位焊时,使用的焊条和焊丝应与常规焊接时所用的型号相同。 5.4 定位焊时,焊接电流宜比常规焊接时的电流大10%~15%。 5.5 定位焊的焊缝尺寸应符合表7的规定。
4
JB/T71672014
5.6 起重要作用的定位焊焊缝,可适当增加定位焊缝的尺寸和数量,但不应大于最终焊缝的高度。 5.7 为了减小焊接变形,定位焊时要预留反变形量,其数值根据试验和生产经验而定。
表7
单位为毫米
焊件厚度 ≤4 >4~12 >12
焊缝高度 <4 3~6 >6
焊缝长度 7~15 10~20 15~20
焊缝间距 50~100 100~200 200300
5.8定位焊时,焊件的相对位置应符合5.8.1~5.8.5的要求。 5.8.1 搭接接头时,其尺寸公差应符合表8的规定。
表8
单位为毫米
板 厚搭边宽度极限偏差L
6 ot2 02 ot2 0 10 ot o -5
>6~10 >10~18
>18
简 图
S
T
L AL
ot
搭边装配间隙Ar1
A/
5.8.2 型钢(角钢、工字钢、槽钢)定位焊时,其偏差应符合表9的规定。
表9 偏差t
单位为毫米
型钢高度
简 图
h
B>1000 ≤0.020h ≤0.015h ≤0.010h
B≤1000
≤100
≤0.015h
>100~240
≤0.010h
>240
≤0.008h
5.8.3 钢板等厚对接时,其对口错边量e应符合表10的规定,但最大不应超过2mm。
表10
单位为毫米
板厚S ≤6 >6~12 >12
简 图
对口错边量e
≤&5 ≤88 ≤12
5.8.4对接不同厚度钢板的受力接头时,如两板厚度差(S-6)不超过表11的规定时,则焊接接头的基本形式与尺寸按较厚的尺寸数据选取:否则应将较厚的板削薄,其削薄长度L≥3(S)。 5.8.5型钢对接时,其对口错边量e应符合表12的规定。 5.8.6 定位焊后的结构件,经检验人员检验合格后方可焊接。
5