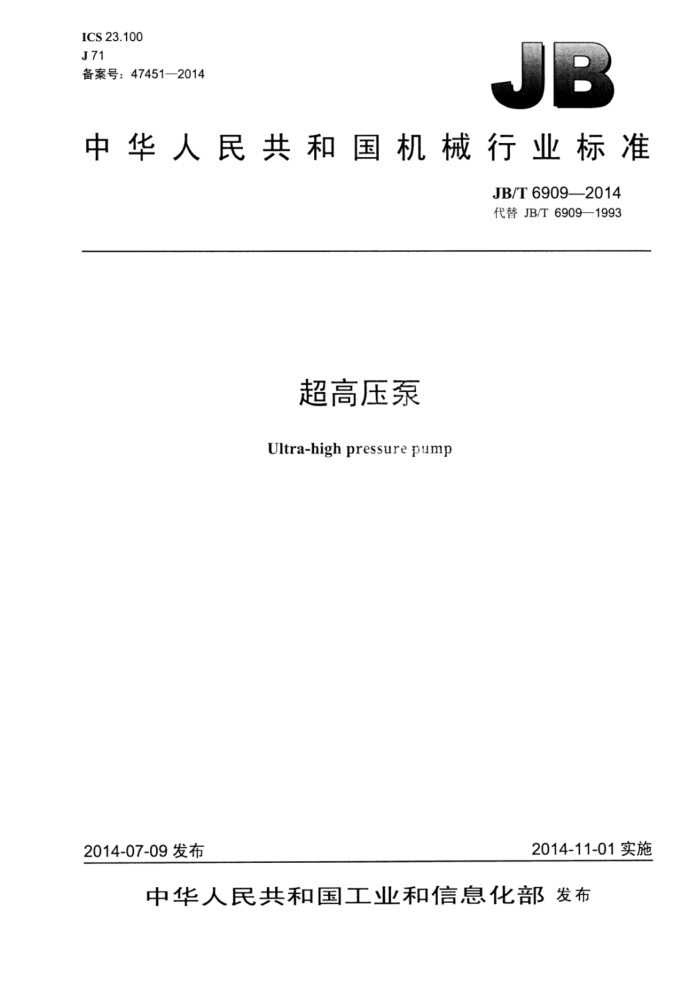
ICS 23.100 J71 备案号:47451—2014
中华人民共和国机械行业标准
JB/T 6909—2014 代替JB/T6909—1993
超高压泵 Ultra-highpressurepump
2014-11-01实施
2014-07-09发布
中华人民共和国工业和信息化部发布
JB/T6909—2014
目 次
前言.
1
范围. 2 规范性引用文件 3型式与基本参数, 3.1型式. 3.2 基本参数 4技术要求. 4.1 一般要求. 4.2 性能要求 4.3 噪声.. 4.4 安全阀、溢流阀 4.5 易损件寿命 4.6 材料要求.. 4.7 制造技术要求 5试验方法 5.1 试验装置 5.2 试运转.. 5.3 性能试验 5.4 压力 5.5 流量. 5.6 泵速... 5.7 功率. 5.8 温度. 5.9 安全阀或超压保护装置 5.10 累积运转试验 5.11 噪声测量 6 检验规则
1
6.1 检验类别, 6.2 检验项目. 6.3 检验报告... 7标志、包装和贮存 7.1标志.. 7.2 包装和贮存. 附录A(资料性附录)基本参数
10
JB/T6909—2014
前言
本标准按照GB/T1.1一2009给出的规则起草。 本标准代替JB/T6909—1993《超高压泵》,与JB/T6909—1993相比主要技术变化如下:
删除了型号编制要求(见3.1,1993年版的第3章);一增加并修订了基本参数(见3.2,1993年版的第4章);一增加并修订了噪声规定(见4.3,1993年版的5.5)。 本标准由中国机械工业联合会提出。 本标准由全国泵标准化技术委员会(SAC/TC211)归口。 本标准起草单位:合肥通用机械研究院、天津市通洁高压泵制造有限公司、合肥通用环境控制技术
有限责任公司、四川杰特机器有限公司、无锡高压清洗设备有限公司。
本标准主要起草人:薛胜雄、齐永健、武子全、任启乐、李文、易李力、张丽闵。 本标准所代替标准的历次版本发布情况为:
JB/T 6909—1993。
II
JB/T6909—2014
超高压泵
1范围
本标准规定了超高压泵的型式与基本参数、技术要求、试验方法、检验规则、标志、包装和贮存。 本标准适用于额定排出压力为100MPa~1000MPa的机动往复泵和液动超高压增压器(以下简称
泵),输送介质为常温清水或油品,工作环境温度为常温、相对湿度不大于85%的场合。
规范性引用文件
2
下列文件对于本文件的应用是必不可少的。凡是注日期的引用文件,仅注日期的版本适用于本文件。 凡是不注日期的引用文件,其最新版本(包括所有的修改单)适用于本文件。
GB/T 222 钢的成品化学成分允许偏差 GB/T 226 钢的低倍组织及缺陷酸蚀检验法 GB/T 229 金属材料 夏比摆锤冲击试验方法 GB/T 230.1 金属材料 洛氏硬度试验第1部分:试验方法(A、B、C、D、E、F、G、H、K、N、
T标尺)
GB/T 231.1 金属材料 布氏硬度试验第!部分:试验方法 GB/T 699 优选碳素结构钢 GB/T 700 碳素结构钢 GB/T 1029 三相同步电机试验方法 GB/T 1032 三相异步电动机试验方法 GB/T 1220 不锈钢棒 GB/T 1311 直流电机试验方法 GB/T 1348 球墨铸铁件 GB/T 1979 结构钢低倍组织缺陷评级图 GB/T 2975 钢及钢产品 力学性能试验取样位置及试样制备 GB/T3077 合金结构钢 GB 3836.1 爆炸性环境第1部分:设备 通用要求 GB/T 6394 金属平均晶粒度测定方法 GB/T 7784 机动往复泵试验方法 GB/T 9439 灰铸铁件 GB/T 10561 钢中非金属夹杂物含量的测定 标准评级图显微检验法 GB/T 13306 标牌 GB/T13384 机电产品包装通用技术条件 JB/T 9090 容积泵零部件液压与渗漏试验
3 型式与基本参数
3.1 1型式
泵的驱动型式可以分为以下几种:电动、柴油机驱动、液动、手动。
1
JB/T6909—2014
3.2 2基本参数 3.2.1 泵的基本参数选取参见附录A。 3.2.2 泵的额定排出压力超出附录A范围的应在表1中选取。
表1
单位为兆帕 1 000
400
500
630
710
800
3.2.3 泵的柱(活)塞直径应在表2中选取。
表 2 10 12 14 16 18 20 22
单位为毫米
柱赛直径活塞直径 50 60
6
7
8 65
9 70 75 80 85 90 98 100
技术要求 4.1 一般要求 4.1.1 泵应按经规定程序批准的图样及技术文件制造。 4.1.2按非连续工作制设计制造的泵可连续工作时间不得小于1h,且应在铭牌上特别标明。 4.1.3 泵应能在额定排出压力及额定泵速下安全运转。 4.1.4 泵在运行时应符合下列条件:
4
a)泵应在常压下起动: b)各静密封面无泄漏; c)润滑油油压及油位在规定范围内,油温不超过75℃; d)轴承、传动端运动副温度不超过75℃; e)泵应有过载保护装置。
4.1.5 超高压螺栓、螺母及液力端与动力端螺纹连接处,应规定装配扭矩。 4.1.6 联轴器、传动带和其他可能对人体造成伤害的运动零件周围,应有防护罩。 4.1.7 泵用于易燃易爆环境时,电动机和电气设备的防爆型式类别、级别和温度按GB3836.1的规定。 4.1.8 成套供应的泵应包括:
a)完整泵1台; b)安全阀或超压保护装置,泵的吸入、排出接头; c)原动机1台; d)易损件和备件不少于1台套; e)专用工具1台套; f)随带文件。
4.2性能要求 4.2.1泵的额定压力或流量指标,保证其在一值下,第二个值的初始值不得比前一值下降10%以上。 4.2.2额定排出压力在400MPa压力以下的泵,其容积系数不得低于80%。 4.3噪声
电动机驱动的泵在额定工况下运行时,噪声应符合表3的规定。压力和功率超过表3范围则不规定噪声指标。柴油机驱动的泵不执行表3的规定,当泵噪声超过表3的规定时,应采用降噪方式使之符合。
2
JB/T69092014
表3
单位为分贝
额定排出压力MPa
额定输入功率
kw ≤7.5 >7.5~22 >22~75 >75~250
≥400 85 90
≤200 80 85
200~400 83 88 95 105
4.4 安全阀、溢流阀 4.4.1 泵或其系统应配备安全阀或其他超压保护装置,其正常开启压力应符合表4的规定。
表4 ≤400
>400 (1.02~1.05)Par
泵额定排出压力Pa MPa
安全阀开启压力
(1.05~1.1) Pdr
4.4.2 液压传动的低压溢流阀的开启压力为工作压力的1.05倍1.10倍;压缩空气传动的低压安全阀的开启压力为工作压力的1.0倍~1.1倍。 4.5 易损件寿命 4.5.1 泵的主要易损件负荷下的累积运转时间应不低于表5的要求。
表 5
单位为小时
额定排出压力MPa >250~400
项目
输送介质清水油品清水油品
≤250 250 400
≥400~630
≥630 50 80
200 250 250(允许修复) 400(允许修复)
100 150
柱塞密封副
阀组
4.5.2 压力不大于320MPa的泵在额定工况下无故障累积运行时间应不低于50h。 4.5.3 泵的所有承压零部件都应进行液压试验,试验按照JB/T9090规定进行。 4.6 材料要求 4.6.1 零件的材料应按图样规定,但经试验鉴定确能保证设计要求的材料允许代用。 4.6.2 所有承受超高压零件的材料必须具备表6规定的力学性能 4.6.3 材料应有化学成分和力学性能的证明书,无证明书时,应按照GB/T699、GB/T700、GB/T1220 和GB/T3077的规定,进行化学和力学性能检验。 4.6.4 材料化学分析和力学性能检验,按照GB/T222、GB/T229、GB/T230.1和GB/T231.1的规定进行。 4.6.5 钢锭或直径大于80mm的型材(需经锻造或直接进行机械加工)应按GB/T226、GB/T1979的规定做低倍组织的微观组织检验。中心疏松和一般疏松不超过1.5级。偏析不大于1.5级,不应有白点、 缩孔、气泡、蜂窝等缺陷。非金属夹杂物中的氧化物、硫化物各不超过1.5级,总重量不超过2.5级。 4.6.6 重要承压零件的锻件中非金属夹杂物按GB/T10561的规定评定。 4.6.7 如材料已经过热处理,力学性能又符合要求时,可直接投料加工,但在材料合格证上要特别说明。 4.6.8 锻件坏料应铲除或磨净其表面的缺陷。采用钢锭锻造时,必须切除两端不坚实部分。
3
JB/T6909—2014
表6 抗拉试验
冲击试验
试验 夏比冲击吸收功
极限强度 屈服极限
伸长率
断面收缩率 olo
类别 等级
V ) 平均值 最小值
> MPa
温度
>
轴向 切向 轴向 切向 17 14 45
600 750
700~850
40 30 20 20.6 14.7 22 40 40
A
锻件 B 850~1000
16 13 35 14
c 1000~1200 900
12 25
800~900
700 800 900
17 14 50 16 13 50 15 12 45
e
管子 b 900~1000
20
14.7
20.6
c 1000~1100
35
注:在泵的最低使用温度比耐压试验温度20℃低的情况下,! 以较低的温度进行冲击试验,则要同时满足表中平
均值和最小值的规定。
4.6.9锻件不应有过烧和严重脱碳现象,外表面不应有裂纹、折迭、锻伤、斑疤、夹渣等缺陷,应按锻件订货商和材料制造商之间的协定标准及检查方法进行检查。对需要机械加工的表面,如有上述缺陷但经加工后能完全去除,可以使用。 4.6.10 锻件的缺陷不应补焊。 4.6.11锻件应有适当的锻造比。如按主体断面积计算,当用钢锭锻造时,其锻造比不小于3;当用直径不小于80mm的型材锻造时,其锻造比不小于2.5, 4.6.12 2最终热处理后锻件的晶粒度应按GB/T6394的规定检查,且不低于5级。 4.6.13 管子应通过显微组织试验确认不存在脱碳等异常组织。 4.6.14 4在同一炉号、同一工艺条件下,热处理的同批锻件或直接投料的零件,应按下列规定进行力学性能检验:
a)螺柱、螺母:可抽零件批量总数的20%做硬度试验,有1件不合格时应100%进行检验。对螺
柱抽检1%做力学性能试验,但不小于2件,每项试验取不小于2个拉伸试样、2个冲击试样。 b)超高压缸体:抽取1个锻件进行拉伸和冲击试验,取样位置自端部热处理厚度2/3以上。表面
取样位置:拉伸试验在实心材料热处理厚度1/4处;冲击试验在实心材料热处理厚度1/2处。 c)其他零件:力学性能试件数量为零件批量总数的10%,但不小于2件,在每个试件上取1个拉
伸试样、2个冲击试样。对单件质量超过20kg、批量总数不超过10个的零件,试件数量可取 1件,在试件中取1个拉伸试样、2个冲击试样。
4.6.15 当在试验中发现有1个试样不合格时,应以加倍数量的试样重新试验。 4.6.16 力学性能试样的取样方法,按GB/T2975的规定。 4.6.17 承压零件应进行无损检验,并出具检验报告。 4.6.18 泵的铸件技术要求和试验方法应符合GB/T9439和GB/T1348的规定。 4.7 制造技术要求 4.7.1 零件应无影响强度和损伤外观的缺陷。 4.7.2 有疲劳强度要求的零件表面,加工后表面粗糙度在轴向及周向均不大于3.2μum。 4.7.3 密封表面不应有划伤、凹陷等缺陷。 4.7.4 承压零件的内层应进行自增强处理,处理方法可采用打压、滚压和热套等多种工艺。 4.7.5 承受超高压循环压力作用的零件不应焊接。 4.7.6 高、低压缸体、曲轴、连杆、柱塞、接头变截面处的圆角应光滑过渡。 4
JB/T6909—2014
4.7.7 高压连接螺纹的精度不低于6H/6h。 4.7.8泵阀组配研后应做煤油渗透试验,5min中内不得渗漏。 4.7.9 柱塞与密封套应偶配研磨。 4.7.10 主要零部件加工检验合格后,应打上标记。 4.7.11 检验合格的零部件、外购件、外协件应有合格证方可装配。 4.7.12 装配前,与润滑油接触的零件的非加工表面应涂耐油防锈漆底漆。各零件应清除毛刺,逐一清洗后,再用压缩空气吹干。 4.7.13 螺纹连接装配应采用指示式扭力扳手装配。 4.7.14 试验完毕后,盘车检查装配质量,柱塞往复不少于5次,不应卡阻。 4.7.15 泵的表面漆层应光洁平整,超高压管路应涂红色油漆。
5 试验方法
5.1 试验装置 5.1.1 泵的排出管路上应设置压力仪表、调压阀、安全阀或其他超压保护装置及稳压装置。 5.1.2 排出管路和负载容器允许承受的压力与被试泵额定排出压力相适应。 5.1.3吸入管路的各连接处不应泄漏,以免空气进入。 5.1.4排出管路上设置的稳压装置应保证压力表指示值的变动范围符合测量要求。 5.1.5试验时,试验人员不应正对调压阀轴向调压,泵及装置隔离区不应进人。 5.1.6试验装置不应采用热弯管。 5.1.7 采用爆破膜式安全阀,应通过试验标注爆破压力。 5.1.8 试验应在额定工况下进行,试验工况各参数的测量值对额定值的允许偏差应符合表7的规定。
表7
要 求 >320~630 MPa
工况项目
≥630 MPa
≤320 MPa
排出压力允许下降度%
0
5 额定值的5%
8
泵速允许偏差
表8
允许误差 %
测定值转速压力流量噪声泵输入功率
1.0 2.5
2.0
5.1.9 9测量泵压力的仪表指示值,允许波动范围应小于10%,用于流程的泵其排出压力允许波动范围应符合流程的要求。 5.1.10试验时,泵运行达到稳定工况后所有仪表读数应同步读出并记录,每个被测参数的测量次数对型式检验和抽样检验应不少于3次,对出厂试验则不少于1次,取算术平均值为测量值。 5.1.11测量用仪器、仪表的测量误差应不大于表8规定,且所有测量仪器、仪表应有计量部门或有关部门的检验合格证明,并在有效使用期内。
5