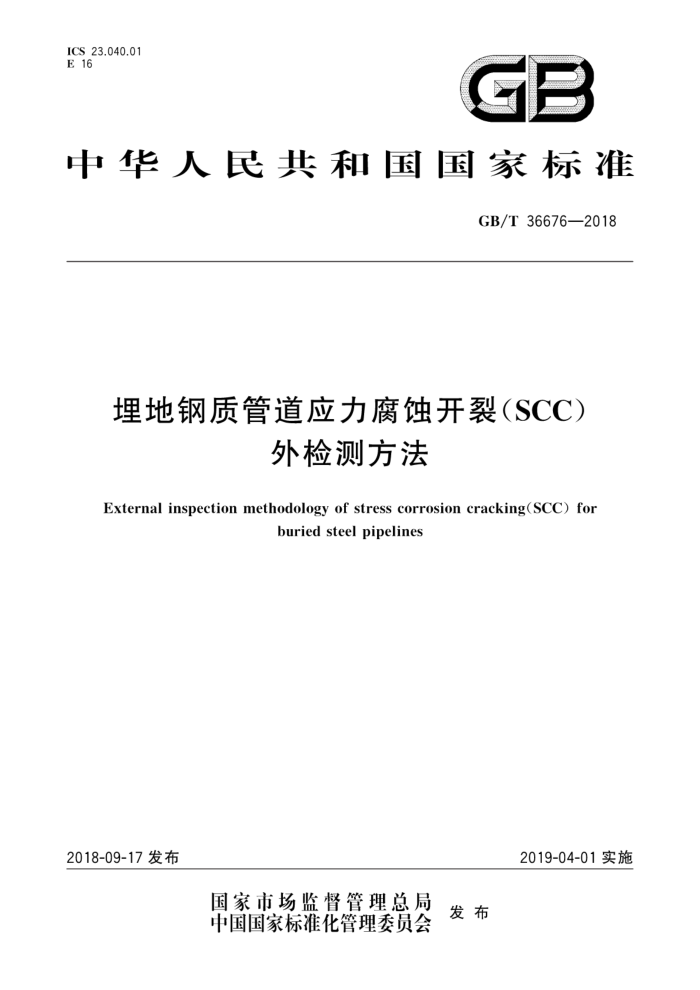
ICS 23.040.01 E 16
GB
中华人民共和国国家标准
GB/T36676—2018
埋地钢质管道应力腐蚀开裂(SCC)
外检测方法
External inspection methodology of stress corrosion cracking(SCC)for
buried steel pipelines
2019-04-01实施
2018-09-17 发布
国家市场监督管理总局
中国国家标准化管理委员会 发布
GB/T36676—2018
目 次
前言范围规范性引用文件
2
术语和定义总则 5 数据收集 SCC敏感因素分析
3
4
6
SCC位置预测 8 开挖检测
评估与处置 10记录和报告· 附录A(资料性附录) 数据收集附录B(规范性附录) SCC敏感性分析和评估附录C(资料性附录) 土壤环境下SCC敏感电位区间确定方法附录D(资料性附录) 含SCC管段裂纹扩展速率实验测定方法附录E(资料性附录) 交变载荷作用下含SCC管段裂纹扩展速率预测方法参考文献
15
17
1.9
GB/T36676—2018
前言
本标准按照GB/T1.1一2009给出的规则起草。 本标准由全国锅炉压力容器标准化技术委员会(SAC/TC262)提出并归口。 本标准起草单位:中国特种设备检测研究院、北京科技大学、中国石油大学(北京)、中国石化销售有
限公司、中国石油天然气股份有限公司管道分公司、中国石油化工股份有限公司天然气分公司、中石化长输油气管道检测有限公司、重庆市特种设备检测研究院、中国石化销售有限公司华南分公司、中国石油工程建设有限公司西南分公司、中国石油天然气股份有限公司长庆油田分公司、中国石油天然气股份有限公司塔里木油田分公司、深圳市燃气集团股份有限公司、福建省特种设备检验研究院、广东大鹏液化天然气有限公司、上海金艺检测技术有限公司、中石油东部管道有限公司。
本标准主要起草人:修长征、王俊强、王海涛、李晓刚、刘智勇、帅健、邵珊珊、卜文平、冯庆善、 宗照峰、薛正林、吴晓阳、王卫东、姜放、陈钒、卢宏伟、李先明、周德敏、安成名、吴林军、李曙华、梁强、 万欣、刘晴、李岩。
1
GB/T36676—2018
埋地钢质管道应力腐蚀开裂(SCC)
外检测方法
1范围
本标准规定了埋地钢质管道应力腐蚀开裂(SCC)的外检测方法,包括数据收集、SCC敏感因素分析、SCC位置预测、开挖检测、评估与处置、记录和报告
本标准适用于陆上长输管道、集输管道以及公用管道中的埋地钢质管道,其他埋地钢质管道可参照本标准的相关规定执行。
本标准仅适用于埋地钢质管道由外部环境引起的应力腐蚀开裂,不适用于输送介质引起的应力腐蚀开裂。
规范性引用文件
2
下列文件对于本文件的应用是必不可少的。凡是注日期的引用文件,仅注日期的版本适用于本文件。凡是不注日期的引用文件,其最新版本(包括所有的修改单)适用于本文件
GB/T19285 埋地管道腐蚀防护工程检验 GB/T 19624 在用含缺陷压力容器安全评定 GB/T 24196 金属和合金的腐蚀电化学试验方法恒电位和动电位极化测量导则 GB/T 27699 钢制管道内检测技术规范 GB/T 27921 风险管理风险评估技术 GB/T 30582 基于风险的理地钢质管道外损伤检验与评价 GB 32167 油气输送管道完整性管理规范 NB/T 47013 承压设备无损检测 TSG D7003 压力管道定期检验规则-长输管道 TSG D7004 压力管道定期检验规则-公用管道
3术语和定义
下列术语和定义适用于本文件。
3.1
应力腐蚀开裂 stresscorrosioncracking;SCC 金属材料在拉应力和腐蚀环境联合作用下引起的开裂现象。
3.2
高pH SCChighpH stresscorrosioncracking 埋地管道的一种由外部碱性电解质环境引起的应力腐蚀开裂形式注:裂纹表现为沿晶开裂,并有明显分叉。
3.3
近中性pHSCC near neutral pH stress corrosion cracking 埋地管道的一种由外部近中性PH电解质环境引起的应力腐蚀开裂形式注:裂纹一般表现为穿晶开裂,分叉较少,裂纹处或管道表面有腐蚀现象
1
GB/T36676—2018
4总则
4.1应力腐蚀开裂外检测工作应满足TSGD7003、TSGD7004等国家相关法规标准的规定。 4.2本方法用于评估陆上埋地钢质管道由外部环境引起的应力腐蚀开裂,包括近中性pHSCC和高 pHSCC两种形式。 4.3应力腐蚀开裂外检测工作包含六个步骤:数据收集、SCC敏感因素分析、SCC位置预测、开挖检测、评估与处置、记录和报告,流程如图1所示。
确定工作范围
雷要时,应通过检验检测
对于未能收集到的数据可以进行保守假设
数据收集
补充数据
SCC敏感因素分析
SCC位置预测
开挖检测
评估与处置
记录和报告
图1 应力腐蚀开裂外检测流程图
5数据收集
5.1收集管道基本信息、历史和当前有效数据,至少应包括管道设计资料、安装资料、内外环境、腐蚀防护系统、运行维护资料等五类数据,参见附录A表A.1。 5.2当收集到的数据不足时,应通过检验检测补充表A,1所需数据,其中腐蚀防护系统检测按照 GB/T19285执行,内检测按照GB/T27699执行。 5.3当数据未能收集到且又无法进行补充检验检测时,评估人员可以基于类似情况的经验和信息进行保守假设,假设数据以及相应的措施应予以记录。
2
GB/T36676—2018
6SCC敏感因素分析
6.1SCC敏感因素分析是在数据收集的基础上,确定SCC的发生条件、损伤类型和形成原因,用于准确确定SCC检测范围。 6.2SCC的发生需要同时满足三个条件,即敏感金属材料、足够大拉应力和特定腐蚀环境。埋地钢质管道SCC的具体发生条件见附录B。 6.3影响SCC裂纹萌生和扩展的因素众多,关系复杂且具有不确定性,可按照附录B对影响SCC的因素进行敏感性分析。 6.4高pHSCC和近中性pHSCC发生的腐蚀环境有所差别,其特征和敏感因素对比见表1。
表1两种SCC类型的特定腐蚀环境
SCC类型
因素对比位置温度
高pHSCC
近中性pHSCC 防腐层剥离或破损处
防腐层破损点处,干湿交替的土壤环境
>32 ℃
无影响
特定土壤腐蚀溶液
浓的CO/HCO;溶液·pH>9.3 -600mV~750mV相对饱和Cu/CuSO
稀的CO-/HCO,溶液.pH介于5.5~7.5
管道表面电位
阴极保护被屏蔽,自然腐蚀电位
参比电极(CSE) 裂纹处无腐蚀
管道表面腐蚀情况
裂纹处有腐蚀,裂纹萌生与蚀坑相关
7 SCC位置预测
7.1SCC敏感管段筛选 7.1.1 满足下列条件的管段应确定为SCC敏感管段:
a) 曾发生过SCC的邻近管段; b) 与以往发生SCC具有相同或相近特征的管段,特征包括地形特征、土壤类型、含水率、排水状
况以及防腐层异常等; c) 操作条件下,应力超过管材规定最低屈服强度的60%、在压气站或泵站下游操作压力较大且
波动频繁、局部残余应力较大或应力集中等的管段,操作温度高于38℃的管段; d) 使用年限大于10年的长期服役老旧管段; e) 检测发现防腐层存在剥离、破损、老化等异常,尤其防腐层为非熔结环氧粉末(FBE)的管段; f) 检测发现管体存在腐蚀、凹陷、裂纹等缺陷的管段; g) 阴极保护不达标或异常管段,或参考附录C确定的SCC敏感电位区间处于I区的管段; h) 检测人员认定的可能发生SCC的其他敏感管段,如穿越、跨越管段的出入土位置、地质灾害引
起的变形管段、车辆碾压管段、投产后埋深发生变化且土壤具有腐蚀特性的管段等
7.1.2 :按照附录B对筛选出的管段进行SCC敏感性评估,依据评估结果对敏感管段进行开挖排序。 7.2SCC敏感管段开挖位置确定 7.2.1 开挖位置确定的原则如下:
a) 优先开挖已发生过SCC的位置,或按照GB32167要求开挖由内检测发现的裂纹缺陷位置:
3
GB/T36676—2018
b)如果已确认之前发生SCC的位置具有某些相同特征,应考虑在相同特征的其他地点进行
开挖; c) 如果没有发生过SCC,应考虑开挖防腐层异常、管体缺陷的位置; d)除上述情况外,应考虑开挖应力、压力波动以及温度最高的位置。
7.2.2对开挖位置进行现场勘察、预评估,确定是否具备开挖条件。
8开挖检测
8.1 开挖原则 8.1.1SCC敏感管段的开挖可结合管道定期检验进行,开挖点数量和比例按照TSGD7003中开挖检测的相关要求执行。 8.1.2优先开挖排序靠前的SCC敏感管段。当开挖过程中,发现存在SCC时,优先开挖具有同类特征的管段。 8.1.3开挖前,应制定详细的开挖计划,做好开挖准备工作,包括土地赔偿、开挖范围、安全措施等,开挖作业遵守相关安全操作规程。 8.2开挖检测和数据采集 8.2.1管道开挖、检测及回填过程中,应遵守相关法规及标准,防止管道失稳。 8.2.2并挖前,应明确数据采集的最低要求,包括历史数据的有效性、采集的数据类型及用途等,并准备好所有相关记录表格,参见表A.2。 8.2.3开挖后,应对管道及防腐层进行宏观检查,应采用磁粉、渗透等方法对管道外表面进行检测,应采用超声、电磁、射线等方法对管体和焊缝进行检测。无损检测工作应按照NB/T47013等相关标准执行。SCC缺陷尺寸的确定,可采用磁粉或渗透检测方法确定裂纹宏观形状和路径,结合超声检测、打磨或抛光方法确定裂纹的最大深度。打磨或抛光的深度和长度应遵守操作规程对最大允许打磨量的要求,可参照相关管道缺陷修复标准执行。 8.2.4在开挖检测过程中应详细记录管道和防腐层的各类缺陷特征、尺寸、相对位置等,以图片和文字形式保存。 8.2.5对开挖检测过程发现的除SCC之外的外腐蚀、内腐蚀、机械损伤等缺陷,应按照GB/T30582选择相应的方法进行检测和评估。 8.2.6发现的SCC裂纹分布范围超出开挖区域时,应对检测位置进行扩挖;检测人员认为必要时,可增加开挖位置进行验证性检测。 8.3SCC开裂分析 8.3.1依据开挖检测发现的裂纹宏观形貌和尺寸,区分开裂类型,包括高pHSCC、近中性pHSCC或其他类型缺陷;分析开裂形成原因,包括机械损伤、腐蚀、安装焊接缺陷等;针对裂纹群,分析裂纹之间的相互作用,确定损伤程度,包括最大长度和宽度,参见表A.2。 8.3.2如果宏观无法区分SCC类型,可采用原位金相分析方法,检验SCC微观形貌。
9评估与处置
9.1SCC裂纹评估与处置流程 9.1.1SCC裂纹评估与处置包含四个方面:SCC裂纹评估、处置与减缓控制措施、裂纹扩展速率预测和 4
ICS 23.040.01 E 16
GB
中华人民共和国国家标准
GB/T36676—2018
埋地钢质管道应力腐蚀开裂(SCC)
外检测方法
External inspection methodology of stress corrosion cracking(SCC)for
buried steel pipelines
2019-04-01实施
2018-09-17 发布
国家市场监督管理总局
中国国家标准化管理委员会 发布
GB/T36676—2018
目 次
前言范围规范性引用文件
2
术语和定义总则 5 数据收集 SCC敏感因素分析
3
4
6
SCC位置预测 8 开挖检测
评估与处置 10记录和报告· 附录A(资料性附录) 数据收集附录B(规范性附录) SCC敏感性分析和评估附录C(资料性附录) 土壤环境下SCC敏感电位区间确定方法附录D(资料性附录) 含SCC管段裂纹扩展速率实验测定方法附录E(资料性附录) 交变载荷作用下含SCC管段裂纹扩展速率预测方法参考文献
15
17
1.9
GB/T36676—2018
前言
本标准按照GB/T1.1一2009给出的规则起草。 本标准由全国锅炉压力容器标准化技术委员会(SAC/TC262)提出并归口。 本标准起草单位:中国特种设备检测研究院、北京科技大学、中国石油大学(北京)、中国石化销售有
限公司、中国石油天然气股份有限公司管道分公司、中国石油化工股份有限公司天然气分公司、中石化长输油气管道检测有限公司、重庆市特种设备检测研究院、中国石化销售有限公司华南分公司、中国石油工程建设有限公司西南分公司、中国石油天然气股份有限公司长庆油田分公司、中国石油天然气股份有限公司塔里木油田分公司、深圳市燃气集团股份有限公司、福建省特种设备检验研究院、广东大鹏液化天然气有限公司、上海金艺检测技术有限公司、中石油东部管道有限公司。
本标准主要起草人:修长征、王俊强、王海涛、李晓刚、刘智勇、帅健、邵珊珊、卜文平、冯庆善、 宗照峰、薛正林、吴晓阳、王卫东、姜放、陈钒、卢宏伟、李先明、周德敏、安成名、吴林军、李曙华、梁强、 万欣、刘晴、李岩。
1
GB/T36676—2018
埋地钢质管道应力腐蚀开裂(SCC)
外检测方法
1范围
本标准规定了埋地钢质管道应力腐蚀开裂(SCC)的外检测方法,包括数据收集、SCC敏感因素分析、SCC位置预测、开挖检测、评估与处置、记录和报告
本标准适用于陆上长输管道、集输管道以及公用管道中的埋地钢质管道,其他埋地钢质管道可参照本标准的相关规定执行。
本标准仅适用于埋地钢质管道由外部环境引起的应力腐蚀开裂,不适用于输送介质引起的应力腐蚀开裂。
规范性引用文件
2
下列文件对于本文件的应用是必不可少的。凡是注日期的引用文件,仅注日期的版本适用于本文件。凡是不注日期的引用文件,其最新版本(包括所有的修改单)适用于本文件
GB/T19285 埋地管道腐蚀防护工程检验 GB/T 19624 在用含缺陷压力容器安全评定 GB/T 24196 金属和合金的腐蚀电化学试验方法恒电位和动电位极化测量导则 GB/T 27699 钢制管道内检测技术规范 GB/T 27921 风险管理风险评估技术 GB/T 30582 基于风险的理地钢质管道外损伤检验与评价 GB 32167 油气输送管道完整性管理规范 NB/T 47013 承压设备无损检测 TSG D7003 压力管道定期检验规则-长输管道 TSG D7004 压力管道定期检验规则-公用管道
3术语和定义
下列术语和定义适用于本文件。
3.1
应力腐蚀开裂 stresscorrosioncracking;SCC 金属材料在拉应力和腐蚀环境联合作用下引起的开裂现象。
3.2
高pH SCChighpH stresscorrosioncracking 埋地管道的一种由外部碱性电解质环境引起的应力腐蚀开裂形式注:裂纹表现为沿晶开裂,并有明显分叉。
3.3
近中性pHSCC near neutral pH stress corrosion cracking 埋地管道的一种由外部近中性PH电解质环境引起的应力腐蚀开裂形式注:裂纹一般表现为穿晶开裂,分叉较少,裂纹处或管道表面有腐蚀现象
1
GB/T36676—2018
4总则
4.1应力腐蚀开裂外检测工作应满足TSGD7003、TSGD7004等国家相关法规标准的规定。 4.2本方法用于评估陆上埋地钢质管道由外部环境引起的应力腐蚀开裂,包括近中性pHSCC和高 pHSCC两种形式。 4.3应力腐蚀开裂外检测工作包含六个步骤:数据收集、SCC敏感因素分析、SCC位置预测、开挖检测、评估与处置、记录和报告,流程如图1所示。
确定工作范围
雷要时,应通过检验检测
对于未能收集到的数据可以进行保守假设
数据收集
补充数据
SCC敏感因素分析
SCC位置预测
开挖检测
评估与处置
记录和报告
图1 应力腐蚀开裂外检测流程图
5数据收集
5.1收集管道基本信息、历史和当前有效数据,至少应包括管道设计资料、安装资料、内外环境、腐蚀防护系统、运行维护资料等五类数据,参见附录A表A.1。 5.2当收集到的数据不足时,应通过检验检测补充表A,1所需数据,其中腐蚀防护系统检测按照 GB/T19285执行,内检测按照GB/T27699执行。 5.3当数据未能收集到且又无法进行补充检验检测时,评估人员可以基于类似情况的经验和信息进行保守假设,假设数据以及相应的措施应予以记录。
2
GB/T36676—2018
6SCC敏感因素分析
6.1SCC敏感因素分析是在数据收集的基础上,确定SCC的发生条件、损伤类型和形成原因,用于准确确定SCC检测范围。 6.2SCC的发生需要同时满足三个条件,即敏感金属材料、足够大拉应力和特定腐蚀环境。埋地钢质管道SCC的具体发生条件见附录B。 6.3影响SCC裂纹萌生和扩展的因素众多,关系复杂且具有不确定性,可按照附录B对影响SCC的因素进行敏感性分析。 6.4高pHSCC和近中性pHSCC发生的腐蚀环境有所差别,其特征和敏感因素对比见表1。
表1两种SCC类型的特定腐蚀环境
SCC类型
因素对比位置温度
高pHSCC
近中性pHSCC 防腐层剥离或破损处
防腐层破损点处,干湿交替的土壤环境
>32 ℃
无影响
特定土壤腐蚀溶液
浓的CO/HCO;溶液·pH>9.3 -600mV~750mV相对饱和Cu/CuSO
稀的CO-/HCO,溶液.pH介于5.5~7.5
管道表面电位
阴极保护被屏蔽,自然腐蚀电位
参比电极(CSE) 裂纹处无腐蚀
管道表面腐蚀情况
裂纹处有腐蚀,裂纹萌生与蚀坑相关
7 SCC位置预测
7.1SCC敏感管段筛选 7.1.1 满足下列条件的管段应确定为SCC敏感管段:
a) 曾发生过SCC的邻近管段; b) 与以往发生SCC具有相同或相近特征的管段,特征包括地形特征、土壤类型、含水率、排水状
况以及防腐层异常等; c) 操作条件下,应力超过管材规定最低屈服强度的60%、在压气站或泵站下游操作压力较大且
波动频繁、局部残余应力较大或应力集中等的管段,操作温度高于38℃的管段; d) 使用年限大于10年的长期服役老旧管段; e) 检测发现防腐层存在剥离、破损、老化等异常,尤其防腐层为非熔结环氧粉末(FBE)的管段; f) 检测发现管体存在腐蚀、凹陷、裂纹等缺陷的管段; g) 阴极保护不达标或异常管段,或参考附录C确定的SCC敏感电位区间处于I区的管段; h) 检测人员认定的可能发生SCC的其他敏感管段,如穿越、跨越管段的出入土位置、地质灾害引
起的变形管段、车辆碾压管段、投产后埋深发生变化且土壤具有腐蚀特性的管段等
7.1.2 :按照附录B对筛选出的管段进行SCC敏感性评估,依据评估结果对敏感管段进行开挖排序。 7.2SCC敏感管段开挖位置确定 7.2.1 开挖位置确定的原则如下:
a) 优先开挖已发生过SCC的位置,或按照GB32167要求开挖由内检测发现的裂纹缺陷位置:
3
GB/T36676—2018
b)如果已确认之前发生SCC的位置具有某些相同特征,应考虑在相同特征的其他地点进行
开挖; c) 如果没有发生过SCC,应考虑开挖防腐层异常、管体缺陷的位置; d)除上述情况外,应考虑开挖应力、压力波动以及温度最高的位置。
7.2.2对开挖位置进行现场勘察、预评估,确定是否具备开挖条件。
8开挖检测
8.1 开挖原则 8.1.1SCC敏感管段的开挖可结合管道定期检验进行,开挖点数量和比例按照TSGD7003中开挖检测的相关要求执行。 8.1.2优先开挖排序靠前的SCC敏感管段。当开挖过程中,发现存在SCC时,优先开挖具有同类特征的管段。 8.1.3开挖前,应制定详细的开挖计划,做好开挖准备工作,包括土地赔偿、开挖范围、安全措施等,开挖作业遵守相关安全操作规程。 8.2开挖检测和数据采集 8.2.1管道开挖、检测及回填过程中,应遵守相关法规及标准,防止管道失稳。 8.2.2并挖前,应明确数据采集的最低要求,包括历史数据的有效性、采集的数据类型及用途等,并准备好所有相关记录表格,参见表A.2。 8.2.3开挖后,应对管道及防腐层进行宏观检查,应采用磁粉、渗透等方法对管道外表面进行检测,应采用超声、电磁、射线等方法对管体和焊缝进行检测。无损检测工作应按照NB/T47013等相关标准执行。SCC缺陷尺寸的确定,可采用磁粉或渗透检测方法确定裂纹宏观形状和路径,结合超声检测、打磨或抛光方法确定裂纹的最大深度。打磨或抛光的深度和长度应遵守操作规程对最大允许打磨量的要求,可参照相关管道缺陷修复标准执行。 8.2.4在开挖检测过程中应详细记录管道和防腐层的各类缺陷特征、尺寸、相对位置等,以图片和文字形式保存。 8.2.5对开挖检测过程发现的除SCC之外的外腐蚀、内腐蚀、机械损伤等缺陷,应按照GB/T30582选择相应的方法进行检测和评估。 8.2.6发现的SCC裂纹分布范围超出开挖区域时,应对检测位置进行扩挖;检测人员认为必要时,可增加开挖位置进行验证性检测。 8.3SCC开裂分析 8.3.1依据开挖检测发现的裂纹宏观形貌和尺寸,区分开裂类型,包括高pHSCC、近中性pHSCC或其他类型缺陷;分析开裂形成原因,包括机械损伤、腐蚀、安装焊接缺陷等;针对裂纹群,分析裂纹之间的相互作用,确定损伤程度,包括最大长度和宽度,参见表A.2。 8.3.2如果宏观无法区分SCC类型,可采用原位金相分析方法,检验SCC微观形貌。
9评估与处置
9.1SCC裂纹评估与处置流程 9.1.1SCC裂纹评估与处置包含四个方面:SCC裂纹评估、处置与减缓控制措施、裂纹扩展速率预测和 4