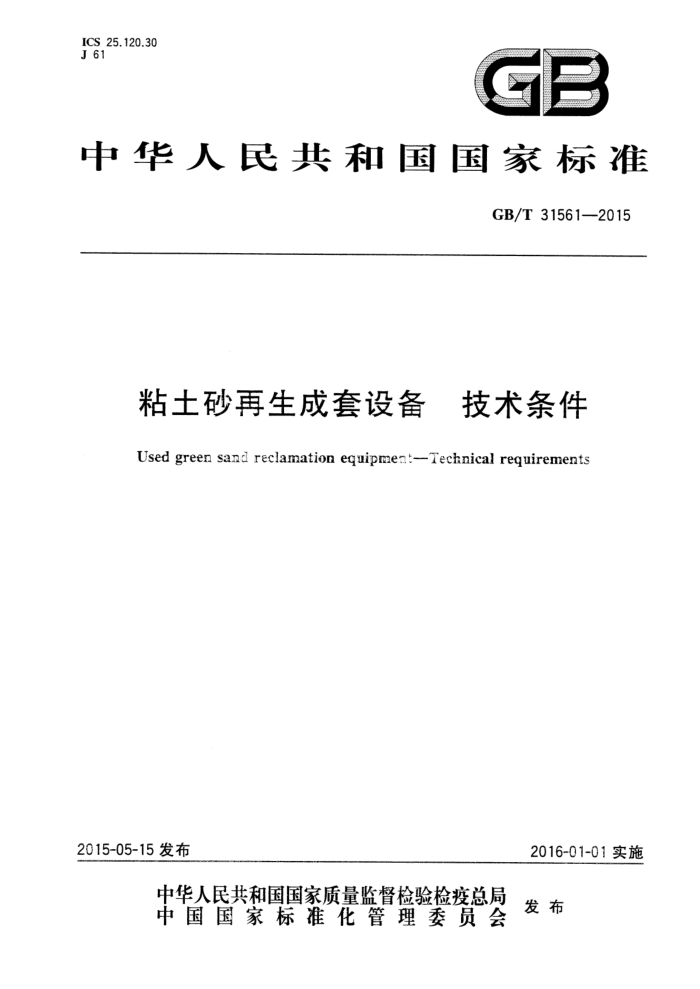
ICS 25.120.30 J 61
GB
中华人民共和国国家标准
GB/T31561—2015
粘土砂再生成套设备 技术条件 Used green sand reclamation equipment--Technical requirements
2015-05-15发布
2016-01-01实施
中华人民共和国国家质量监督检验检疫总局
中国国家标准化管理委员会 发布
GB/T 31561—2015
前言
本标准按照GB/T1.1一2009给出的规则起草。 本标准由中国机械工业联合会提出。 本标准由全国铸造机械标准化技术委员会(SAC/TC186)归口。 本标准起草单位:保定维尔铸造机械股份有限公司、济南铸造锻压机械研究所有限公司。 本标准主要起草人:侯若先、董志合、卢军、王学军、常信平、赵凤堂。
M
GB/T31561—2015
粘土砂再生成套设备技术条件
1范围
本标准规定了粘土砂再生成套设备的术语和定义、技术要求、试验方法、检验规则、包装、标志和储运。
本标准适用于采用干法再生和热法再生的粘土砂再生成套设备(以下简称成套设备)。
2规范性引用文件
下列文件对于本文件的应用是必不可少的。凡是注日期的引用文件,仅注日期的版本适用于本文件。凡是不注日期的引用文件,其最新版本(包括所有的修改单)适用于本文件。
GBZ2.1工作场所有害因素职业接触限值第1部分:化学有害因素 GB150.1 压力容器 第1部分:通用要求 GB150.2 压力容器 第2部分:材料 GB150.3 压力容器 第3部分:设计 GB150.4 压力容器 第4部分:制造、检验和验妆 GB/T1184-1996 6形状和位置公差未注公差值 GB/T1804—20CC )一般公差未注公差的线性和角度尺寸的公差 GB/T2584铸造用砂及混合料试验方法 GB/T3093.1-201) 紧宣件机械性能 螺检、螺钉和螺栏 GB/T3098.2—2CCC 紧回件机械性能 螺母粗牙螺纹 GB/T3766 液压系统通用技术条件 GB 4053.1 固定式钢梯及平台安全要求 第1部分:钢直梯 GB 4053.2 回定式钢梯及平台安全要求 第2部分:钢斜梯 GB4053.3 固定式钢梯及平台安全要求 第3部分:工业防护栏杆及钢平台 GB5226.1 机械电气安全机械电气设备 第1部分:通用技术条件 GB/T 6576 机尿润滑系统 GB/T 7932 气动系统通用技术条件 GB 8959 铸造防尘技术规程 GB/T 9442 铸造用殖砂 GB/T 9969 工业产品使用说明书总则 GB/T10595 带式输送机 GB 12348 工业企业厂界环境噪声排放标准 GB/T13306标牌 GB/T16157 固定污染源排气中颗粒物测定与气态污染物采样方法 GB 18452 破碎设备安全要求 GB20426 煤炭工业污染物排放标准 GB20905 铸造机械安全要求 GB/T23570 金属切削机床焊接件 通用技术条件
1
GB/T31561—2015
GB/T25370 铸造机械术语 GB/T25371 铸造机械噪声声压级测量方法 GB/T25711—2010铸造机械通用技术条件 GB50050工业循环冷却水处理设计规范 GB50235—2010工业金属管道工程施工规范 GB50277 铸造设备安装工程施工及验收规范 JB/T3926 垂直斗式提升机 JB/T5548.2 电动激振器 第2部分:技术条件 JB/T 9985 筛砂机 JB/T10788 铸造用除尘器 器通用技术条件
3术语和定义
GB/T25370界定的以及下列术语和定义适用于本文件。
3.1
旧砂再生sandreclamation 通过物理和化学的方法,去除旧砂砂粒表面包裹着的残留粘结剂膜及杂物,使旧砂恢复或接近恢复
于新砂的物理和化学性能代替新砂使用。 3.2
干法再生 dryattrition regeneration 利用机械或空气的方法使旧砂流加速,靠砂粒之间和砂粒与设备零件之间的摩擦、碰撞作用再生
旧砂。 3.3
热法再生thermalregeneration 利用加热氧化或燃烧的方法再生旧砂。
3.4
含泥量claycontent 旧砂中含有直径小于0.02mm的粒子的质量分数。
3.5
脱膜率binderremovalrate 去除粘结在旧砂粒表面惰性膜的能力。
3.6
成套设备工作区 reclamationequipmentsarea 安装成套设备的区域和操作人员的工作区域,不包括单一设备的防护性结构和设计用于起各种防
范作用的隔离区域。 3.7
散落砂spillsand 散落在设备以外的旧砂。
3.8
再生砂reclaimedsand 经过再生处理后的旧砂。
2
GB/T 31561—2015
3.9
再生单元 regenerationunit 再生机和周围辅助设备组成的设备单元。
3.10
结露condensationofmoisture 除尘器内部和除尘管道内部温度低于附近空气露点温度时除尘器内表面和管道内壁出现冷凝水
现象。
4技术要求
4.1一般要求 4.1.1成套设备应符合GB/T25711一2010的规定,并按照经过规定程序批准的图样及技术文件制造。 4.1.2成套设备的安全应符合GB20905的有关规定。 4.1.3各种零件的材质、机械性能和物理性能应符合技术文件的规定。 4.1.4金属结构件的焊接应符合GB/T23570的规定。 4.1.5 机械加工零件的未注公差尺寸极限偏差不应低于GB/T1804一2000规定的m级公差要求。 4.1.6电气系统应符合GB5226.1的规定。 4.1.7气动系统应符合GB/T7932的规定。 4.1.8液压系统应符合GB/T3766的规定。 4.1.9 单机润滑系统应符合GB/T6576的规定。 4.1.10 单机设备应保证维修方便,各个设备间应有足够的维修空间。 4.1.11 成套设备的安装除应符合技术文件规定的要求外,还应符合GB50277的规定。 4.1.12 成套设备的涂装应符合技术文件的规定。 4.1.13 成套设备的各种标牌应符合GB/T13306的要求。 4.1.14 4设备说明书中应附有易损件的型号,并应注明易损件的寿命。 4.1.15 成套设备的使用说明书中应规定在正常使用条件下该成套设备生产的再生砂的用途。 4.1.16 随机技术文件应包括产品说明书、产品合格证和装箱单。随机文件的编制应符合GB/T9969 的规定。 4.1.17 随机附件、备件应齐全。 4.2 破碎设备 4.2.1破碎机除符合本标准外还应符合GB18452的规定。 4.2.2振动破碎再生机体组焊后应进行去残留应力处理。 4.2.3振动破碎再生机安装激振器的底脚螺栓孔及激振器安装面的表面粗糙度和形位公差应符合 JB/T5548.2的规定,侧振式破碎再生机激振器底座安装面间平行度和对称度应符GB/T1184-1996 中附表B3、B4规定的9级公差要求。 4.2.4振动破碎再生机所有螺栓紧固件均应采用高强度螺栓,其螺栓的强度级别不应低于GB/T3098.1一 2010中8.8级的规定,其螺母的强度级别不应低于GB/T3098.2一2000中8.0级的规定,并应采取防松措施,在正常使用条件下不应松动和断裂。 4.2.5正常使用条件下,破碎设备的机体在9000h内不应开裂。 4.2.6正常使用条件下,破碎设备的耐磨件和易损件的寿命不应小于3000h。
3
GB/T 31561—2015
4.3加热设备 4.3.1 加热设备应符合粘土砂再生工艺要求。 4.3.2加热设备炉体的外表面温度不应大于80℃。 4.4再生机 4.4.1脱膜率应符合技术文件的规定。 4.4.2回用率应符合技术文件的规定。 4.4.3再生机中使用的叶轮、转盘等高速旋转的零件应进行静平衡试验和校正,其不平衡力矩不应大于0.015N·m。 4.4.4正常使用条件下,再生机中耐磨件的寿命不应小于2000h。 4.5 5筛砂机 4.5.1 筛砂机应符合JB/T9985的规定。 4.5.2 过筛效率应符合技术文件的规定。 4.6 6冷却器 4.6.1 冷却器的水管应进行耐压试验,应在0.5MPa下保压30min无渗漏。 4.6.2 冷却器的循环水管路系统应符合GB50050的规定。 4.7磁选机 4.7.1 磁选机应符合相关标准的规定。 4.7.2磁选旧砂中的磁性物质宜采用二级磁选或二级以上磁选,相邻两级磁选机的安装距离应大于 1.5 m。 4.8气力输送 4.8.1 压送罐的罐体应符合GB150.1~150.4的规定。 4.8.2气力输送管道应采用无缝钢管制作。管子切口质量应符合GB50235一2010中4.1.5的规定。 4.8.3管道法兰面与管子中心的垂直度应符合GB50235一2010中6.2.4的规定。 4.8.4 管道的安装应符合GB50235—2010中6.3.2~6.3.6的规定。 4.8.5管道安装后水平偏差不应大于长度的0.5%,最大不超过30mm;垂直偏差不应大于高度的1%,最大不超过15mm。 4.8.6 管道安装时应设管道支架,管道支架安装应牢固。 4.9 垂直斗提机 4.9.1 垂直斗提机应符合JB/T3926的规定。 4.9.2 提升水分含量较大的旧砂时,料斗和斗提机底部应做防粘砂处理。 4.10 带式输送机 4.10.1 带式输送机应符合GB/T10595的规定。 4.10.2 带式输送机应采用槽型托辊。 4.10.3 带式输送机的输送带的长度小于6m时宜采用整条无接缝皮带。 4.10.4 带式机的支腿间距不应大于3m。
4
GB/T 31561—2015
4.11振动输送机 4.11.1输送水分含量较大的旧砂时,输送槽应做防粘砂处理。 4.11.2振动输送机出砂口上部安装磁选机时,应使用抗磁材料制造出砂口处槽体。 4.12除尘系统 4.12.1 除尘系统设计应符合GB8959的规定。 4.12.2 除尘器应符合JB/T10788的规定。 4.12.3 除尘系统设计合理,除尘器应尽量靠近污染源布置,管道应尽量简短。 4.12.4 除尘管道直径小于或等于400mm时,壁厚不应小于3mm,管道直径大于400mm小于 1500mm时,壁厚不应小于4mm,管道直径大于或等于1500mm时,壁厚不应小于6mm。 4.12.5 除尘管道与风机的进出口应采用柔性连接,管道的设计应易于人工清理管道中的沉积物。 4.12.6 除尘罩的形式应能满足工艺要求,不应影响设备的操作和设备的维修。 4.12.7 管路系统主要吸尘口应安装风量调节阀。 4.12.8 除尘管道应设置测量孔。 4.12.9 在粉尘湿度较大,易结露的工况下,除尘系统应有防结露措施。 4.13 砂仓及平台 4.13.1 砂仓的结构应符合粘土砂的特性。 4.13.2 砂仓壁板的厚度应根据砂斗的容量及结构而定,不应小于5mm。 4.13.3 各种平台顶面宜采用花纹钢板焊接,钢板厚度不应小于4mm。 4.13.4 砂仓的防护栏杆、梯子和平台应符合GB4053.1~4053.3的规定。 4.14 空运转、负荷运转 4.14.1 各单机设备的空运转应在制造厂进行,空运转时间不应少于4h;负荷运转可在用户进行,运转时间不应少于2h。 4.14.2成套设备整机空运转可在用户进行,连续空运转时间不应少于4h;在空运转之后按额定生产率进行负荷运转,负荷运转时间不应少于2h。 4.14.3各单机应能在技术文件规定的额定生产率状态下正常工作,无异常现象。 4.14.4 水路系统不应漏水,各阀门启闭应灵活可靠。 4.14.5 各单机及连接部位均不应漏砂及冒灰现象。 4.14.6 5 振动破碎再生机的空载振幅不应小于1mm,并可根据工艺要求进行调整。 4.14.7 振动输送机正常工作的条件下,机体的侧向偏摆量不应大于2mm。 4.14.8 振动输送机机体工作时进料口和出料口两端振幅差值不应大于10%。 4.14.9 振动输送机正常工作的条件下,机体两侧板对称点振动方向的双振幅差值不应大于在此两点所测双振幅的平均值的20%。 4.14.10除尘器工作时,除尘器和除尘管路各部位不应出现漏尘现象。 4.14.11垂直斗提机卸料情况良好,无显著回料现象。 4.14.12 2气力输送装置的加砂阀、进排气系统应开关灵活,密封可靠,工作过程中不允许有漏气和漏砂现象发生。 4.14.13再生砂含泥量的范围应符合技术文件的规定。 4.14.14 再生砂的回用率不应小于90%。 4.14.15再生砂的粒度分布与原新砂(或上一轮再生砂)的粒度分布相差不应大于一个筛号。
5
GB/T31561—2015
4.14.16 再生砂的砂温应符合技术文件的规定。 4.14.17 散落砂量应小于成套设备额定生产率的万分之五。 4.14.18 成套设备工作区的粉尘浓度应符合GBZ2.1的规定。 4.14.19 成套设备工作区的噪声不应大于75dB(A)。 4.14.20 成套设备在生产过程中的气体排放应符合GB20426的规定和当地环保部门的规定。 4.14.21 成套设备产生的噪声对环境的影响应符合GB12348的规定。
5试验方法
5.1成套设备的噪声测定
按GB/T25371的规定测定。 5.2粉尘排放量的测定
按GB/T16157的规定测定。
5.3成套设备生产率的测定
在成套设备正常生产且再生砂质量合格时,每隔1h分别测量每台单机设备的生产率,依次进行 3次,取3次称量值的平均值,即为单机设备的生产率,从计算结果中取单机设备生产率的最小值,即为成套设备的生产率。 5.4总含泥量的测定
按GB/T2684规定的方法测定再生砂的含泥量。 5.5脱膜率的测定 5.5.1脱膜率应在旧砂含水量不大于1%的条件下进行测定。 5.5.2从再生单元进口部位与再生单元出口部位,分别取处于同一次再生循环内的旧砂和再生砂各 1000g,烘干后,分别随机地取旧砂和再生砂各五份,每份50g,精确至0.001g,测定含泥量。 5.5.3分别测出旧砂和再生砂各自的含泥量,并取其算术平均值。 5.5.4按式(1)进行计算,计算结果即为设备的脱膜率。
M.-M3
R,=-
X100%
..*.(1 )
M2
式中: R.脱膜率; M2— -旧砂含泥量,单位为克(g); Ms—再生砂含泥量,单位为克(g)。
5.6再生砂温度测定
在成套设备正常工作过程中,用分辨率为0.2℃的温度计在再生砂储砂斗入口处每隔30min测量一次再生砂温度,测3次,取算术平均值,即为再生砂温度。 5.7再生砂回用率的测定
称量再生前的一定质量的旧砂W1,将这部分旧砂经成套设备再生后再进行称量,质量为W?,连续称量3次,取其平均值并按式(2)进行计算,计算结果即为再生砂回用率。
6
ICS 25.120.30 J 61
GB
中华人民共和国国家标准
GB/T31561—2015
粘土砂再生成套设备 技术条件 Used green sand reclamation equipment--Technical requirements
2015-05-15发布
2016-01-01实施
中华人民共和国国家质量监督检验检疫总局
中国国家标准化管理委员会 发布
GB/T 31561—2015
前言
本标准按照GB/T1.1一2009给出的规则起草。 本标准由中国机械工业联合会提出。 本标准由全国铸造机械标准化技术委员会(SAC/TC186)归口。 本标准起草单位:保定维尔铸造机械股份有限公司、济南铸造锻压机械研究所有限公司。 本标准主要起草人:侯若先、董志合、卢军、王学军、常信平、赵凤堂。
M
GB/T31561—2015
粘土砂再生成套设备技术条件
1范围
本标准规定了粘土砂再生成套设备的术语和定义、技术要求、试验方法、检验规则、包装、标志和储运。
本标准适用于采用干法再生和热法再生的粘土砂再生成套设备(以下简称成套设备)。
2规范性引用文件
下列文件对于本文件的应用是必不可少的。凡是注日期的引用文件,仅注日期的版本适用于本文件。凡是不注日期的引用文件,其最新版本(包括所有的修改单)适用于本文件。
GBZ2.1工作场所有害因素职业接触限值第1部分:化学有害因素 GB150.1 压力容器 第1部分:通用要求 GB150.2 压力容器 第2部分:材料 GB150.3 压力容器 第3部分:设计 GB150.4 压力容器 第4部分:制造、检验和验妆 GB/T1184-1996 6形状和位置公差未注公差值 GB/T1804—20CC )一般公差未注公差的线性和角度尺寸的公差 GB/T2584铸造用砂及混合料试验方法 GB/T3093.1-201) 紧宣件机械性能 螺检、螺钉和螺栏 GB/T3098.2—2CCC 紧回件机械性能 螺母粗牙螺纹 GB/T3766 液压系统通用技术条件 GB 4053.1 固定式钢梯及平台安全要求 第1部分:钢直梯 GB 4053.2 回定式钢梯及平台安全要求 第2部分:钢斜梯 GB4053.3 固定式钢梯及平台安全要求 第3部分:工业防护栏杆及钢平台 GB5226.1 机械电气安全机械电气设备 第1部分:通用技术条件 GB/T 6576 机尿润滑系统 GB/T 7932 气动系统通用技术条件 GB 8959 铸造防尘技术规程 GB/T 9442 铸造用殖砂 GB/T 9969 工业产品使用说明书总则 GB/T10595 带式输送机 GB 12348 工业企业厂界环境噪声排放标准 GB/T13306标牌 GB/T16157 固定污染源排气中颗粒物测定与气态污染物采样方法 GB 18452 破碎设备安全要求 GB20426 煤炭工业污染物排放标准 GB20905 铸造机械安全要求 GB/T23570 金属切削机床焊接件 通用技术条件
1
GB/T31561—2015
GB/T25370 铸造机械术语 GB/T25371 铸造机械噪声声压级测量方法 GB/T25711—2010铸造机械通用技术条件 GB50050工业循环冷却水处理设计规范 GB50235—2010工业金属管道工程施工规范 GB50277 铸造设备安装工程施工及验收规范 JB/T3926 垂直斗式提升机 JB/T5548.2 电动激振器 第2部分:技术条件 JB/T 9985 筛砂机 JB/T10788 铸造用除尘器 器通用技术条件
3术语和定义
GB/T25370界定的以及下列术语和定义适用于本文件。
3.1
旧砂再生sandreclamation 通过物理和化学的方法,去除旧砂砂粒表面包裹着的残留粘结剂膜及杂物,使旧砂恢复或接近恢复
于新砂的物理和化学性能代替新砂使用。 3.2
干法再生 dryattrition regeneration 利用机械或空气的方法使旧砂流加速,靠砂粒之间和砂粒与设备零件之间的摩擦、碰撞作用再生
旧砂。 3.3
热法再生thermalregeneration 利用加热氧化或燃烧的方法再生旧砂。
3.4
含泥量claycontent 旧砂中含有直径小于0.02mm的粒子的质量分数。
3.5
脱膜率binderremovalrate 去除粘结在旧砂粒表面惰性膜的能力。
3.6
成套设备工作区 reclamationequipmentsarea 安装成套设备的区域和操作人员的工作区域,不包括单一设备的防护性结构和设计用于起各种防
范作用的隔离区域。 3.7
散落砂spillsand 散落在设备以外的旧砂。
3.8
再生砂reclaimedsand 经过再生处理后的旧砂。
2
GB/T 31561—2015
3.9
再生单元 regenerationunit 再生机和周围辅助设备组成的设备单元。
3.10
结露condensationofmoisture 除尘器内部和除尘管道内部温度低于附近空气露点温度时除尘器内表面和管道内壁出现冷凝水
现象。
4技术要求
4.1一般要求 4.1.1成套设备应符合GB/T25711一2010的规定,并按照经过规定程序批准的图样及技术文件制造。 4.1.2成套设备的安全应符合GB20905的有关规定。 4.1.3各种零件的材质、机械性能和物理性能应符合技术文件的规定。 4.1.4金属结构件的焊接应符合GB/T23570的规定。 4.1.5 机械加工零件的未注公差尺寸极限偏差不应低于GB/T1804一2000规定的m级公差要求。 4.1.6电气系统应符合GB5226.1的规定。 4.1.7气动系统应符合GB/T7932的规定。 4.1.8液压系统应符合GB/T3766的规定。 4.1.9 单机润滑系统应符合GB/T6576的规定。 4.1.10 单机设备应保证维修方便,各个设备间应有足够的维修空间。 4.1.11 成套设备的安装除应符合技术文件规定的要求外,还应符合GB50277的规定。 4.1.12 成套设备的涂装应符合技术文件的规定。 4.1.13 成套设备的各种标牌应符合GB/T13306的要求。 4.1.14 4设备说明书中应附有易损件的型号,并应注明易损件的寿命。 4.1.15 成套设备的使用说明书中应规定在正常使用条件下该成套设备生产的再生砂的用途。 4.1.16 随机技术文件应包括产品说明书、产品合格证和装箱单。随机文件的编制应符合GB/T9969 的规定。 4.1.17 随机附件、备件应齐全。 4.2 破碎设备 4.2.1破碎机除符合本标准外还应符合GB18452的规定。 4.2.2振动破碎再生机体组焊后应进行去残留应力处理。 4.2.3振动破碎再生机安装激振器的底脚螺栓孔及激振器安装面的表面粗糙度和形位公差应符合 JB/T5548.2的规定,侧振式破碎再生机激振器底座安装面间平行度和对称度应符GB/T1184-1996 中附表B3、B4规定的9级公差要求。 4.2.4振动破碎再生机所有螺栓紧固件均应采用高强度螺栓,其螺栓的强度级别不应低于GB/T3098.1一 2010中8.8级的规定,其螺母的强度级别不应低于GB/T3098.2一2000中8.0级的规定,并应采取防松措施,在正常使用条件下不应松动和断裂。 4.2.5正常使用条件下,破碎设备的机体在9000h内不应开裂。 4.2.6正常使用条件下,破碎设备的耐磨件和易损件的寿命不应小于3000h。
3
GB/T 31561—2015
4.3加热设备 4.3.1 加热设备应符合粘土砂再生工艺要求。 4.3.2加热设备炉体的外表面温度不应大于80℃。 4.4再生机 4.4.1脱膜率应符合技术文件的规定。 4.4.2回用率应符合技术文件的规定。 4.4.3再生机中使用的叶轮、转盘等高速旋转的零件应进行静平衡试验和校正,其不平衡力矩不应大于0.015N·m。 4.4.4正常使用条件下,再生机中耐磨件的寿命不应小于2000h。 4.5 5筛砂机 4.5.1 筛砂机应符合JB/T9985的规定。 4.5.2 过筛效率应符合技术文件的规定。 4.6 6冷却器 4.6.1 冷却器的水管应进行耐压试验,应在0.5MPa下保压30min无渗漏。 4.6.2 冷却器的循环水管路系统应符合GB50050的规定。 4.7磁选机 4.7.1 磁选机应符合相关标准的规定。 4.7.2磁选旧砂中的磁性物质宜采用二级磁选或二级以上磁选,相邻两级磁选机的安装距离应大于 1.5 m。 4.8气力输送 4.8.1 压送罐的罐体应符合GB150.1~150.4的规定。 4.8.2气力输送管道应采用无缝钢管制作。管子切口质量应符合GB50235一2010中4.1.5的规定。 4.8.3管道法兰面与管子中心的垂直度应符合GB50235一2010中6.2.4的规定。 4.8.4 管道的安装应符合GB50235—2010中6.3.2~6.3.6的规定。 4.8.5管道安装后水平偏差不应大于长度的0.5%,最大不超过30mm;垂直偏差不应大于高度的1%,最大不超过15mm。 4.8.6 管道安装时应设管道支架,管道支架安装应牢固。 4.9 垂直斗提机 4.9.1 垂直斗提机应符合JB/T3926的规定。 4.9.2 提升水分含量较大的旧砂时,料斗和斗提机底部应做防粘砂处理。 4.10 带式输送机 4.10.1 带式输送机应符合GB/T10595的规定。 4.10.2 带式输送机应采用槽型托辊。 4.10.3 带式输送机的输送带的长度小于6m时宜采用整条无接缝皮带。 4.10.4 带式机的支腿间距不应大于3m。
4
GB/T 31561—2015
4.11振动输送机 4.11.1输送水分含量较大的旧砂时,输送槽应做防粘砂处理。 4.11.2振动输送机出砂口上部安装磁选机时,应使用抗磁材料制造出砂口处槽体。 4.12除尘系统 4.12.1 除尘系统设计应符合GB8959的规定。 4.12.2 除尘器应符合JB/T10788的规定。 4.12.3 除尘系统设计合理,除尘器应尽量靠近污染源布置,管道应尽量简短。 4.12.4 除尘管道直径小于或等于400mm时,壁厚不应小于3mm,管道直径大于400mm小于 1500mm时,壁厚不应小于4mm,管道直径大于或等于1500mm时,壁厚不应小于6mm。 4.12.5 除尘管道与风机的进出口应采用柔性连接,管道的设计应易于人工清理管道中的沉积物。 4.12.6 除尘罩的形式应能满足工艺要求,不应影响设备的操作和设备的维修。 4.12.7 管路系统主要吸尘口应安装风量调节阀。 4.12.8 除尘管道应设置测量孔。 4.12.9 在粉尘湿度较大,易结露的工况下,除尘系统应有防结露措施。 4.13 砂仓及平台 4.13.1 砂仓的结构应符合粘土砂的特性。 4.13.2 砂仓壁板的厚度应根据砂斗的容量及结构而定,不应小于5mm。 4.13.3 各种平台顶面宜采用花纹钢板焊接,钢板厚度不应小于4mm。 4.13.4 砂仓的防护栏杆、梯子和平台应符合GB4053.1~4053.3的规定。 4.14 空运转、负荷运转 4.14.1 各单机设备的空运转应在制造厂进行,空运转时间不应少于4h;负荷运转可在用户进行,运转时间不应少于2h。 4.14.2成套设备整机空运转可在用户进行,连续空运转时间不应少于4h;在空运转之后按额定生产率进行负荷运转,负荷运转时间不应少于2h。 4.14.3各单机应能在技术文件规定的额定生产率状态下正常工作,无异常现象。 4.14.4 水路系统不应漏水,各阀门启闭应灵活可靠。 4.14.5 各单机及连接部位均不应漏砂及冒灰现象。 4.14.6 5 振动破碎再生机的空载振幅不应小于1mm,并可根据工艺要求进行调整。 4.14.7 振动输送机正常工作的条件下,机体的侧向偏摆量不应大于2mm。 4.14.8 振动输送机机体工作时进料口和出料口两端振幅差值不应大于10%。 4.14.9 振动输送机正常工作的条件下,机体两侧板对称点振动方向的双振幅差值不应大于在此两点所测双振幅的平均值的20%。 4.14.10除尘器工作时,除尘器和除尘管路各部位不应出现漏尘现象。 4.14.11垂直斗提机卸料情况良好,无显著回料现象。 4.14.12 2气力输送装置的加砂阀、进排气系统应开关灵活,密封可靠,工作过程中不允许有漏气和漏砂现象发生。 4.14.13再生砂含泥量的范围应符合技术文件的规定。 4.14.14 再生砂的回用率不应小于90%。 4.14.15再生砂的粒度分布与原新砂(或上一轮再生砂)的粒度分布相差不应大于一个筛号。
5
GB/T31561—2015
4.14.16 再生砂的砂温应符合技术文件的规定。 4.14.17 散落砂量应小于成套设备额定生产率的万分之五。 4.14.18 成套设备工作区的粉尘浓度应符合GBZ2.1的规定。 4.14.19 成套设备工作区的噪声不应大于75dB(A)。 4.14.20 成套设备在生产过程中的气体排放应符合GB20426的规定和当地环保部门的规定。 4.14.21 成套设备产生的噪声对环境的影响应符合GB12348的规定。
5试验方法
5.1成套设备的噪声测定
按GB/T25371的规定测定。 5.2粉尘排放量的测定
按GB/T16157的规定测定。
5.3成套设备生产率的测定
在成套设备正常生产且再生砂质量合格时,每隔1h分别测量每台单机设备的生产率,依次进行 3次,取3次称量值的平均值,即为单机设备的生产率,从计算结果中取单机设备生产率的最小值,即为成套设备的生产率。 5.4总含泥量的测定
按GB/T2684规定的方法测定再生砂的含泥量。 5.5脱膜率的测定 5.5.1脱膜率应在旧砂含水量不大于1%的条件下进行测定。 5.5.2从再生单元进口部位与再生单元出口部位,分别取处于同一次再生循环内的旧砂和再生砂各 1000g,烘干后,分别随机地取旧砂和再生砂各五份,每份50g,精确至0.001g,测定含泥量。 5.5.3分别测出旧砂和再生砂各自的含泥量,并取其算术平均值。 5.5.4按式(1)进行计算,计算结果即为设备的脱膜率。
M.-M3
R,=-
X100%
..*.(1 )
M2
式中: R.脱膜率; M2— -旧砂含泥量,单位为克(g); Ms—再生砂含泥量,单位为克(g)。
5.6再生砂温度测定
在成套设备正常工作过程中,用分辨率为0.2℃的温度计在再生砂储砂斗入口处每隔30min测量一次再生砂温度,测3次,取算术平均值,即为再生砂温度。 5.7再生砂回用率的测定
称量再生前的一定质量的旧砂W1,将这部分旧砂经成套设备再生后再进行称量,质量为W?,连续称量3次,取其平均值并按式(2)进行计算,计算结果即为再生砂回用率。
6