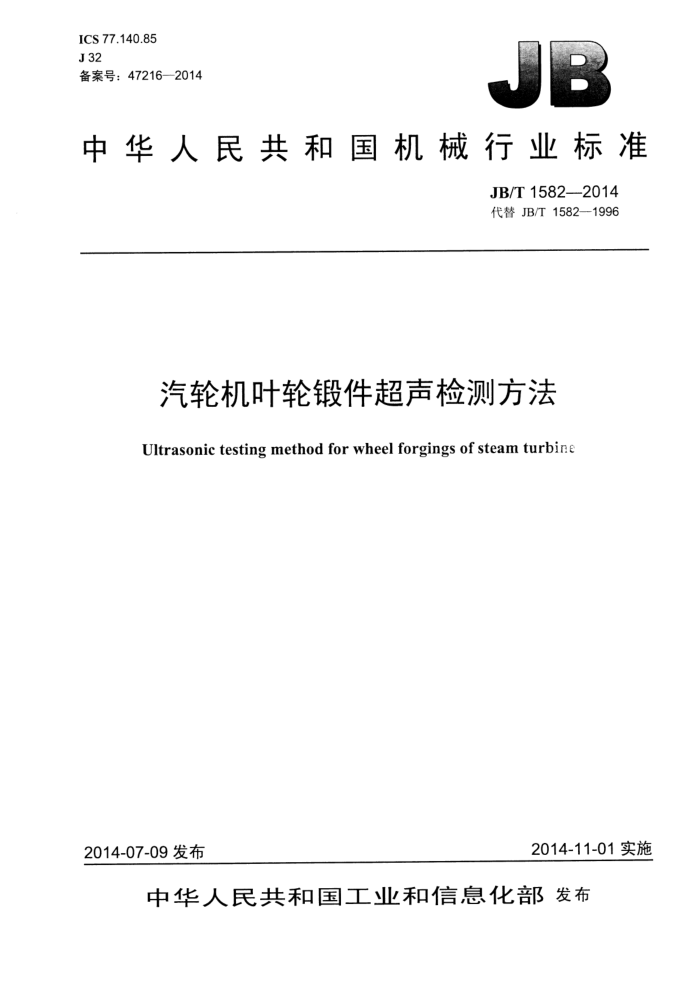
ICS 77.140.85 J32 备案号:47216—2014
中华人民共和国机械行业标准
JB/T 1582—-2014 代替 JB/T 1582—1996
汽轮机叶轮锻件超声检测方法
Ultrasonic testing method for wheel forgings of steam turbine
2014-11-01实施
2014-07-09 发布
中华人民共和国工业和信息化部发布
JB/T 1582-—2014
目 次
I1
前言
.......................
范围 2规范性引用文件 3术语和定义, 4人员资格..… 一般要求.
1
5
6检测器材.. 6.1超声检测仪.. 6.2探头... 6.3 试块. 6.4 系统组合性能.…. 耦合剂
..............................
7
8 超声检测前锻件的准备 9 检测时机, 10 超声检测方法. 10.1 检测总则. 10.2 灵敏度.
..........
10.3 材质声衰减系数的测定 10.4 远场区声束直径的计算 10.5 缺陷当量大小的确定..…. 10.6 检测灵敏度重新校正. 11缺陷的测量与记录
11.1 一般要求 11.2 密集缺陷信号的测量. 11.3 单个缺陷的测量, 11.4 连续缺陷信号的测量.… 11.5 游动缺陷信号 11.6缺陷性质的判定. 11.7 记录 12 检测报告
........
6 6
....................
6
5
JB/T 1582-—2014
前 言
本标准按照GB/T1.1—2009给出的规则起草。 本标准代替JB/T1582—1996《汽轮机叶轮锻件超声波探伤方法》,与JB/T1582-1996相比主要技术
变化如下:
-对缺陷信号重新进行了定义(见第3章);一修改了灵敏度调整的内容(见10.2,1996年版的5.2);一增加了声束直径计算公式(见10.4);一增加了缺陷定量计算公式(见10.5);
一增加了灵敏度重新校正的要求(见10.6);一修改了试块的要求,删除了附录A(见6.3,1996年版的5.2.4、附录A)。
本标准由中国机械工业联合会提出。 本标准由全国大型铸锻件标准化技术委员会(SAC/TC506)归口。 本标准起草单位:二重集团(德阳)重型装备股份有限公司。 本标准主要起草人:范吕慧、陈冲。 本标准所代替标准的历次版本发布情况为:
JB/T1582—1985,JB/T1582-1996。
II
JB/T 1582—2014
汽轮机叶轮锻件超声检测方法
1范围
本标准规定了用直射法对叶轮锻件进行接触式脉冲反射超声检测的各种检测程序、缺陷信号的分类、缺陷的测量与记录、检测报告等内容。
本标准适用于JB/T1266和JB/T7028中各类叶轮锻件的超声检测,其他轮盘锻件可参考使用。
2规范性引用文件
下列文件对于本文件的应用是必不可少的。凡是注日期的引用文件,仅注日期的版本适用于本文件。凡是不注日期的引用文件,其最新版本(包括所有的修改单)适用于本文件。
GB/T 9445无损检测人员资格鉴定与认证 GB/T11259无损检测超声检测用钢参考试块的制作与检验方法 GB/T12604.1无损检测术语超声检测 JB/T126625MW~200MW汽轮机轮盘及叶轮锻件技术条件 JB/T702825MW以下汽轮机轮盘及叶轮锻件技术条件 JB/T9214无损检测A型脉冲反射式超声检测系统工作性能测试方法 JB/T10061A型脉冲反射式超声探伤仪通用技术条件 JB/T10062超声探伤用探头性能测试方法
3术语和定义
GB/T12604.1界定的以及下列术语和定义适用于本文件。
3.1
单个分散缺陷信号individual indication 最小缺陷当量符合锻件技术条件规定的记录限,当探头从缺陷最大信号反射位置向任一方向移动
时,信号幅度出现正常的下降而无此起彼伏的现象,相邻两缺陷之间的距离大于其中较大缺陷当量直径的倍数达到相应技术条件中的规定值的缺陷信号。除非另有规定,单个分散缺陷信号是指除密集缺陷信号、连续(条状)缺陷信号和游动缺陷信号之外的缺陷信号。 3.2
密集缺陷信号 cluster indication 在边长为50mm的立方体内,数量不少于5个、当量直径不小于锻件技术条件规定值的记录限的缺
陷信号。 3.3
连续(条状)缺陷信号extended indication 缺陷回波高度至少在一个方向上非均匀下降,其延伸长度大于缺陷允许的最大当量直径的缺陷信
号。连续(条状)缺陷信号的延伸尺寸采用半波高度法(-6dB法)测定。在测定延伸尺寸时应考虑探头的声场特性进行修正。
距离扫查面声程为S(mm)处的远场区直探头6dB声束直径按公式(1)计算。
1
JB/T 1582-2014
as Ts
2
(1)
式中: Ts-探头晶片直径,单位为毫米(mm); a一一波长,单位为毫米(mm); d6 dB 声束直径,单位为毫米(mm)。
3.4
缺陷引起的底波降低量loss of backreflection causedbyflaws 在缺陷附近完好区内第一次底波幅度Bc与缺陷处第一次底波幅度B之比(Bc/Br),用声压级(dB)
表示。 3.5
游动缺陷信号 traveling indication 在技术条件规定的灵敏度下,当探头在被检测部位移动时,信号前沿位置的移动距离相当于25mm
或25mm以上金属深度的缺陷信号。
4 人员资格
4.1锻件超声检测人员应按照GE:T9445或其他同等标准的规定,经国家有关部门考核鉴定并取得相应资格证书。 4.2超声检测人员资格等级分为I、IⅡI和II级。各资格等级的人员只能从事与该等级相对应的超声检测工作,并负相应的技术责任
5 一般要求
对叶轮锻件超声检测的方法、部位及质量等级要求应在图样、技术文件和订货技术条件中注明。
6检测器材
6.1超声检测仪 6.1.1采用A型超声检测仪,且检测仪应符合JB/T10061的要求。 6.1.2垂直线性至少在屏高80%内呈线性显示,其误差不大于土5%,水平线性误差不大于土2%。检测仪的线性误差应按JB/T10061的要求进行测试。 6.1.3灵敏度余量应在30dB以上,其测定方法按JB/T10061的要求进行。 6.2探头 6.2.1应采用符合JB/T10062规定的直探头。 6.2.2探头的公称频率为1MHz~5 MHz。 6.2.3直探头的有效晶片直径为10mm~40mm。 6.2.4如果要求检测近表面,应采用双晶探头。 6.2.5对于叶轮锻件,本标准推荐优先采用频率为2MHz~2.5MHz、晶片直径为20mm~25mm的直探头。也可以采用其他探头来评定缺陷和对缺陷进行定位,或者进行特殊部位的超声检测。
2
JB/T 1582--2014
6.3试块 6.3.1试块应采用与被检工件相同或声学特性相近的材料制成。该材料用直探头检测时,不得有影响检测灵敏度调节的缺陷。 6.3.2试块的制作应符合GB/T11259的规定 6.4系统组合性能
系统组合性能的测试按JB/T9214的规定进行。
7耦合剂
7.1耦合剂应具有良好的润湿性。可使用机油、甘油、浆糊或水作为耦合剂。对于成品锻件推荐使用 20#~40#机油作为耦合剂。 7.2不同的耦合剂不能进行对比。因此,超声检测系统性能测试、灵敏度调节和校正时所用的耦合剂应与超声检测时的耦合剂相同。
8超声检测前锻件的准备
8.1叶轮锻件应尽可能加工成简单的扁圆形状,避免出现妨碍超声检测操作的锥体、沟槽等几何形状,表面不得有刀具划痕、氧化皮、机械加工后残留的细屑、油漆或其他外来物。 8.2锻件检测面的表面粗糙度Ra不大于6.3μm。
9检测时机
应在性能热处理后进行。如果性能热处理后锻件外形妨碍全面检测,则允许在性能热处理之前进行超声检测。在这种情况下,热处理后要尽可能全面地对锻件再进行一次超声检测。
10超声检测方法
10.1检测总则 10.1.1叶轮超声检测应符合标准或订货协议的规定。叶轮应从端部和周向两个方向进行扫查,由于锻件几何形状原因导致锻件的某些部位不能进行检测时,可采用其他方法进行检测,应在超声检测报告中注明。 10.1.2为了保证扫查范围完全覆盖整个锻件体积,探头相邻两次扫查至少应有15%的重叠。 10.1.3探头扫查速度不应超过150mm/s。 10.1.4供方或需方对锻件进行复核或重新评定时,应使用有可比性的检测仪、探头和耦合剂。 10.2灵敏度 10.2.1检测灵敏度是指有效地发现技术条件中规定的最小缺陷当量。在扫查过程中可适当提高灵敏度,以便发现缺陷。但当发现缺陷需要进行各种测量工作时,则应恢复到基准灵敏度。 10.2.2缺陷检测灵敏度的基准高度,应在扫描线与满屏高的40%~80%范围内选定。 10.2.3AVG曲线法适用于探头的近场区和远场区,本标准推荐优先选用AVG曲线法。对于工件本身不能采用AVG曲线法时,允许用同类材质的其他工件进行AVG曲线法调节灵敏度。必要时应作相应
3
JB/T 1582—2014
的修正。 10.2.4计算法仅适用于大于或等于3倍探头近场区的情况,计算方法详见10.2.6。 10.2.5试块法也适用于探头的近场区和远场区,但应修正试块与工件的差异。 10.2.6当声程大于或等于3倍近场时,按公式(2)计算所需增加的dB值以调整缺陷检测灵敏度。
4dB = 20lg 2aS
(2)
元g2
式中: △dB—需提高增益分贝数; 超声波波长,单位为毫米(mm); S-—锻件被检测部位厚度,单位为毫米(mm); 元一 一 -圆周率(取值为3.14159); Φ一平底孔当量直径,单位为毫米(mm)。
10.2.7当检测灵敏度确定之后,以检测灵敏度为基准,若信噪比大于或等于6dB,则认为该锻件具有足够的可检测性,否则由供需双方协商处理。 10.3材质声衰减系数的测定 10.3.1当声程大于或等于3倍近场时,在锻件无缺陷区域内,至少选取三处具有代表性的部位检测出 BE:篇,第-一次底波高度B,与第二次底波高度B2之间的dB差值。
":()计算材质声衰减系数α。
(B - B2)- 6 dB
α
(3)
2
读减系数,单位为分贝每毫米(dB/mm); --声程,单位为毫米(mm)。
10.3.2当材质衰减系数α超过0.004dB/mm时,应对超声检测结果给予修正并在报告中记录相应的衰减系数。 10.4远场区声束直径的计算
按公式(1)计算6dB声束直径。 10.5缺陷当量大小的确定 10.5.1AVG曲线法定量
当缺陷位于近场和远场时,都可使用AVG曲线法进行定量,具体使用方法按相应探头的AVG曲线使用规定。 10.5.2计算法定量
当声程大于或等于3倍近场时,按公式(4)计算缺陷当量直径的大小。
2x+2α(x -S) 元Sd
B/B=20lg
(4)
式中: B/B一底波与缺陷回波的 dB 差,单位为分贝(dB);
-波长,单位为毫米(mm); xf—缺陷深度,单位为毫米(mm);
2一
4
JB/T 1582-—2014
S一声程,单位为毫米(mm); Φ缺陷当量直径,单位为毫米(mm); α一材质声衰减系数,单位为分贝每毫米(dB/mm)。
10.5.3试块法定量 10.5.3.1当声程大于或等于3倍近场时,按公式(5)计算缺陷当量直径的大小。
x+2αx-2α
(5)
4= 401g
xr
式中: △——缺陷与试块平底孔之dB 差值,单位为分贝(dB); d——缺陷当量直径,单位为毫米(mm);
-试块平底孔的深度,单位为毫米(mm); xf—缺陷深度,单位为毫米(mm); α -材质声衰减系数(对比试块),单位为分贝每毫米(dB/mm); α———缺陷处材质衰减系数,单位为分贝每毫米(dB/mm)。
x
10.5.3.2当声程小于3倍近场时,应用试块直接比较或用DAC曲线来确定缺陷当量直径的大小 10.6检测灵敏度重新校正 10.6.1除每次进行超声检测前应校正缺陷检测灵敏度外,遇到下列情况时,应对缺陷检测灵敏度进行重新校正:
a)校正后的探头、合剂和仪器状态发生任何改变; b)外部电源电压波动较大或操作者怀疑灵敏度有改动; c)工作结束及使用模拟机连续工作达4h以上。
10.6.2当缺陷检测灵敏度变化且降低2dB以上时,应对上一次校正后所检测的锻件进行全面复检;当缺陷检测灵敏度变化且提高2dB以上时,应对所有的记录信号进行重新评定。
11缺陷的测量与记录
11.1般要求
检测中遇到缺陷信号之后,应根据缺陷信号的类别采用不同的方法对缺陷进行测量。 11.2密集缺陷信号的测量
密集缺陷信号的测量包括: a)根据缺陷信号在扫描线上的位置,测量缺陷的深度分布范围; b)根据探头中心扫查到缺陷的移动范围,测量缺陷的平面分布范围; c)缺陷的当量直径; d)缺陷密集区在锻件上的位置。
11.3单个缺陷的测量
单个缺陷的测量包括: a)用AVG曲线法、计算法或试块比较法测量缺陷的当量直径; b)缺陷在锻件上的位置。
5