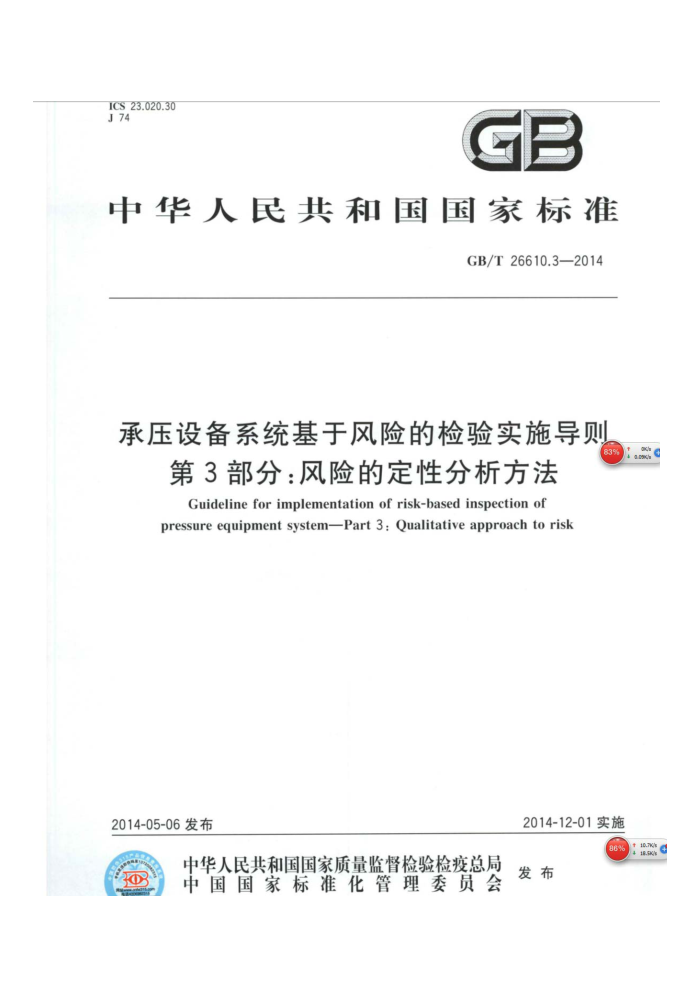
ICS23.020.30 J 74
GB
中华人民共和国国家标准
GB/T26610.3—2014
承压设备系统基于风险的检验实施导则
OK
第3部分:风险的定性分析方法 Guidelinefor implementationof risk-based inspection of pressure equipment system-Part 3:Qualitative approach to risk
2014-12-01实施
2014-05-06发布
R
69
中华人民共和国国家质量监督检验检疫总局
中国国家标准化管理委员会 发布
GB/T26610.3—2014
前 言
GB/T26610《承压设备系统基于风险的检验实施导则》分为5个部分:
第1部分:基本要求和实施程序;第2部分:基于风险的检验策略;第3部分:风险的定性分析方法;第4部分:失效可能性定量分析方法;第5部分:失效后果定量分析方法。
本部分为GB/T26610的第3部分。 本部分按照GB/T1.1一2009给出的规则起草。 本部分参考了APIRP581《基于风险的检验》,并结合我国的实际情况制定。 本部分由全国锅炉压力容器标准化技术委员会(SAC/TC262)提出并归口。 本部分起草单位:合肥通用机械研究院、中国特种设备检测研究院、福建特种设备检测研究院、中国
石油化工股份有限公司、中国石油天然气股份有限公司、中国石油化工股份有限公司茂名分公司、大连西太平洋石油化工有限公司。
.o
本部分主要起草人:陈学东、艾志斌、杨铁成、胡久韶、顾望平、贾国栋、王辉、李光海、谢国山、王笑梅张志超、何承厚、李信伟、韩建宇、曲豫。
0
GB/T26610.3—2014
承压设备系统基于风险的检验实施导则
第3部分:风险的定性分析方法
1范围
GB/T26610的本部分给出了针对石油化工装置承压设备系统进行风险定性分析的方法,其他工业承压设备系统实施的风险定性分析也可参照采用。
本部分适用于GB/T26610.1所指的承压设备系统。
2规范性引用文件
下列文件对于本文件的应用是必不可少的。凡是注日期的引用文件,仅注日期的版本适用于本文件。凡是不注日期的引用文件,其最新版本(包括所有的修改单)适用于本文件。
GB/T26610.1 承压设备系统基于风险的检验实施导则 第1部分:基本要求和实施程序
e
3术语和定义
GB/T26610.1界定的以及下列术语和定义适用于本文件。
3.1
设备因子 equipment factor EF 与装置(单元或工段)中可能发生失效的设备总数相关的表征数值。
3.2
损伤因子 damage factor
DF 装置(单元或工段)中潜在的损伤机理种类的量化表征。
3.3
检验因子 inspectionfactor IF 当前检验程序的有效性及其对识别装置(单元或工段)中潜在损伤机理的能力的量化表征。
3.4
维护状态因子 maintenance condition factor MCF 被评估装置(单元或工段)的设计制造水平、企业管理和维护程序运行的有效性的量化表征。
3.5
工艺因子 processfactor PF 装置(单元或工段)运行连续性、工艺稳定性和安全保护装置可靠性的量化表征。
Oe
GB/T 26610.3—2014
3.6
机械设计因子mechanicaldesignfactor MDF 装置(单元或工段)设计规范的先进性及与现行标准的符合性的量化表征。
3.7
燃烧与爆炸后果 damageconsequence 可燃性介质泄放到环境中引起着火与爆炸造成的各种损失的量化表征。
3.8
燃烧与爆炸后果等级 damage consequence category 根据化学因子、破坏量值因子、状态因子、自燃因子、压力因子和安全防护因子的组合所确定的后果
等级类别。 3.9
化学因子 chemical factor CF 介质发生燃烧的可能性的量化表征,由可燃因子和反应因子组成。
3.10
可燃因子 flashfactor FF 介质固有的可然性的量化表征
0.5kt
3.11
反应因子 reaction facto RF 介质暴露于 点火源时发生反应的可能性
童化
3.12
损伤量值因子 damage quantity factor DQF 失效事件发生后,装置中的可燃介质最大程度泄放导致的破坏程度的量化表征。
3.13
状态因子 statefactor SF 介质泄放到大气中被闪蒸成汽的难易度程度的量化表征。
3.14
自燃因子 auto-ignition factor AF 介质泄漏后自行燃烧的可能性的量化表征。
3.15
压力因子 pressurefactor PRF 失效事件发生后,介质泄放到环境中的快慢程度的量化表征。
3.16
安全防护因子 credit factor CRF 装置在设计、制造过程所赋予的安全特性的量化表征。
2
GB/T26610.3—2014
3.17
中毒后果 toxicconsequence 有毒介质泄放到环境中引起的中毒造成的各种损失的量化表征。
3.18
中毒后果类别等级 toxic consequence category 根据中毒量值因子、扩散因子、安全防护因子以及人口因子的组合所确定的后果等级类别。
3.19
中毒量值因子 toxic quantity factor TQF 失效事件发生后,装置中的有毒介质最大程度的泄放导致的破坏程度的量化表征。
3.20
扩散因子 dispersibilityfactor DLF 介质扩散能力的量化表征
3.21
人口因子 population factor PPF 失效事件发生后,可能受到某 有市介质泄放影响的天数的量化表征
OKs 0.4K/s
4总则 4.1 定性分析的程序
分析前应首先确定被评估装置(单元或工段)的物理边界和介质特性:然后按第5童确定其失效可能性,按第6章确定其失效后果, 具,按第章确定其风险等级 4.2 一般原则 4.2.1当装置(单元或工段)中有若干种主要的介质时,应根据介质种类分别计算该装置的失效后果,并确定风险级别,以风险级别最高的结果作为该装置最终的风险级别 4.2.2在进行风险的定性务析时,为保证评估结果的一致性,当某一问题有多种可选答案时,应选择其中的一种,而不是使用插值、 4.3 定性分析的应用 4.3.1风险的定性分析方法可以单独应用,也可以和定量方法结合起案使用。在受条件限制无法进行全部定量风险分析时,可通过定性分析方法筛选出定性风险相对较高的部分进行定量风险分析,再依据定量风险分析的结果制定基于风险的检验策略。 4.3.2进行不同装置(单元或工段)定性风险对比时需要考虑装置(单元或工段)中的设备数量,只有设备数量相近的装置(单元或工段)才能进行对比。
5失效可能性评估 5.1失效可能性的评估步骤 5.1.1 根据被评估装置(单元或工段)的具体情况,分别对下列6个因子进行赋值或计算:
Ke
GB/T 26610.3—2014
a) 设备因子(EF); b) 损伤因子(DF); c) 检验因子(IF); d) 维护状态因子(MCF) e)工艺因子(PF);
机械设计因子(MDF)。
D
5.1.2将上述6个因子的值相加,计算失效可能性因子,按表1确定失效可能性等级(即图1风险矩阵图的纵轴)。
表 1 失效可能性等级
失效可能性等级
失效可能性因子
1 2 3
0~15 16~25 26~35 36~50 51~75
5
5.2 各因子的赋值或计算方法
Ok
5.2.1 设备因子(EF)
根据被评估装置(单元或工段)中可能发生失效的设备总数对设备因子(EF)进行赋值,其最大值为15:
a) 对完整的装置进行评估(可能发生失效设备数量大于150台),取EF=15; b) 对装置中的某个单元进行评估(可能发生失效设备数量为20台~150台),取EF=5; c) 对装置中的某个工段进行评估(可能发生失效设备数量小于20台设备),取EF=2。
5.2.2 损伤因子(DF)
判断装置(单元或工段)中是否存在发生某种损伤机理的可能性,并分别赋值: a) 存在导致碳钢或低合金钢发生腐蚀开裂的可能性,取DF1=5; b) 存在因低温、回火脆化或其他原因可能引起碳钢发生脆性断裂的可能性,取DF2=4;
存在发生热疲劳或机械疲劳的可能性,取DF3=4; d) 存在发生高温氢腐蚀的可能性,取DF4=3; e) 存在由于工艺原因引发奥氏体不锈钢应力腐蚀开裂的可能性,取DF5=3; f) 存在发生局部腐蚀的可能性,取DF6=3; g) 存在发生全面腐蚀的可能性,取DF7=2: h) 存在发生螨变损伤的可能性,取DF8=1:
c)
存在材料退化(如α相析出、渗碳、珠光体球化等)的可能性,取DF9=1;存在已经识别的其他损伤机理的可能性,取DF10=1。
i) i) 将DF1~DF10相加,计算损伤因子(DF),其最大值为20。
5.2.3 检验因子(IF) 5.2.3.1 根据容器检验历史对IF1进行赋值:
e
4
GB/T26610.3—2014
按要求进行定期检验,检验方案符合有关规范要求,有现场监控装置(如泄漏报警、视频监控等),取IF1=—5;
a)
b) 仅进行过部分宏观(肉眼)检查和超声测厚等,取IF1=一2; c) 未进行过有效检验,取IF1=0。
2
5.2.3.2 根据管道检验历史对IF2进行赋值:
a) 按要求进行定期检验,检验方案符合有关规范要求,有现场监控装置,取IF2=一5; b) 仅进行过部分宏观(肉眼)检查和超声测厚等,取IF2=一2; c) 未进行过有效检验,取IF2=0。
5.2.3.3 根据检验方案对IF3进行赋值:
a) 已识别出设备的全部损伤机理,并全部制定了有针对性的检验方案,取IF3=一5;
仅对部分已识别的损伤机理制定了针对性的检验方案,取IF3=一2; c) 检验方案不满足上述各项要求,取IF3=0。
b)
5.2.3.4 将IF1~IF3相加,计算检验因子(IF),其最小值为一15,但其绝对值不得超过损伤因子(DF)。 5.2.4 维护状态因子(MCF) 5.2.4.1 根据企业的管理水平对MCF1进行赋值:
a) 企业管理水平明显优于现行有关工业标准、规范,取MCF1=0; b) 企业管理水平接近现行有关工业标准、规范,取MCF1=2; c) 企业管理水平明显低于现行有关工业标准、规范,取MCF1=5。
1ke
5.2.4.2 根据装置设计与制造水平对MCF2进行赋值:
a) 装置的设计与制造水平明显优于现行有关工业标准、规范,同时业主提出了更严格的要求,取
MCF2=0; b) 装置的设计与制造水平接近现行有关工业标准、规范,取MCF2=2; c) 装置的设计与制造水平明显低于现行有关工业标准、规范,取MCF2=5。
5.2.4.3 根据装置维修方案的有效性对MCF3进行赋值:
a) 装置的维修方案明显优于现行有关工业标准、规范,同时业主提出了更严格的要求,取
MCF3=0; b) 装置的维修方案接近现行有关工业标准、规范,取MCF3=2; c) 装置的维修方案水平明显低于现行有关工业标准、规范,取MC3=5。
5.2.4.4 将MCF1MCF3相加,计算检验因子(MCF),其最大值为15。 5.2.5 工艺因子(PF) 5.2.5.1 根据平均每年的计划或非计划停工次数对PF1进行赋值:
a) 0次1次,取PF1=0; b) 2次~4次,取PF1=1;
5次~8次,取PF1=3; d) 9次~12次,取PF1=4; e) 多于12次,取PF1=5。
c)
5.2.5.2 根据工艺稳定性对PF2进行赋值:
a) 工艺非常稳定,不存在造成反应失控的可能性或其他不安全因素,取PF2=0; b) 存在一定的操作异常的可能性,取PF2=1; c) 存在导致设备损伤加速的可能性或其他不安全因素,取PF2=3;
工艺本身非常不稳定,极易失控,取PF2=5。
d)
e
GB/T26610.3—2014 5.2.5.3 根据保护装置可靠性,如是否会因为介质结垢或堵塞导致安全阀等失效,对PF3进行赋值:
a) 运行状况清洁,发生堵塞的可能极小,取PF3=0; b) 有轻微结垢或堵塞的可能,取PF3=1;
有明显结垢或堵塞的可能,取PF3=3; d) 在使用过程中,发现过保护装置损坏的情况,取PF3=5。
c)
5.2.5.4 将PF1~PF3相加,计算工艺因子(PF),其最大值为15。 5.2.6 机械设计因子(MDF) 5.2.6.1 根据设备设计、制造、维护与现行标准、规范的符合性对MDF1进行赋值:
a) 所有设备均按现行标准、规范进行设计与维护,取MDE1=0; b) 所有设备均按其建造时的有效标准、规范进行设计与维护,取MDF1=2; c) 设备未按现行标准、规范进行设计,取MDF1=5。
5.2.6.2 根据工艺对MDF2进行赋值:
工艺是通用的且符合现行标准与规范设计条件,取MDF2=0; b) 工艺独特 或所有工艺设计条件均为极端条件,取MDF2=5。
a)
5.2.6.3 将MDF 1和MDF2相加,机械设计因(MDF其最大值为10
6失效后果评估
C
6.1 失效后果的分类
失效后果分为 a)燃烧与爆后果; b) 中毒后果。
6.2失效后果评估原则
当某一介质泄漏仅产生燃烧与爆炸后果或中毒后果,仅需要针对实际存在的失效后果进行评估,作为最终的失效后果等级图1风险矩阵图的水平轴);当介质泄漏产生两种失效后果时,如果其中一种后果带来的风险占明显主导地位时,只需确定主导风险的后果而不必考虑另一种后果,否则应对两种失效后果分别进行评估,并以其中较严重的失效后果等级作为最继的失效后果等级。 6.3 燃烧与爆炸后果等级的评估方法 6.3.1 评估步骤 6.3.1.1 根据被评估装置(单元或工段)的具体情况,分别对下列6个因子进行赋值或计算:
a) 化学因子(CF); b) 损伤量值因子(DQF); c) 状态因子(SF); d) 自燃因子(AF); e) 压力因子(PRF); f) 安全防护因子(CRF)。
e
6.3.1.2 将上述6个因子的值相加,计算燃烧与爆炸后果因子,按表2确定燃烧与爆炸后果等级。
0