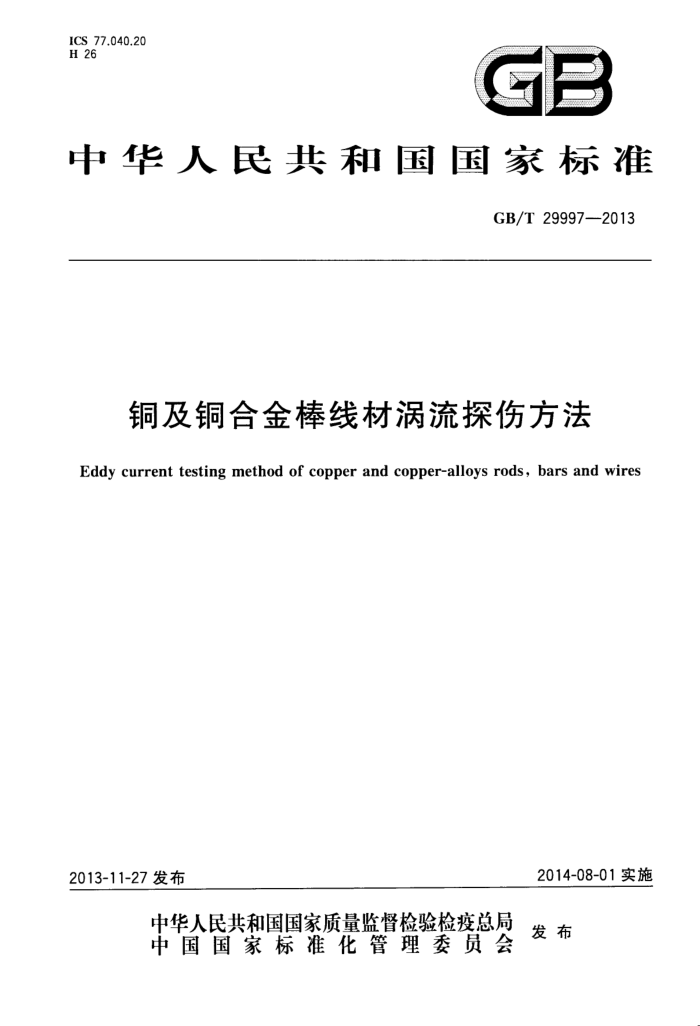
ICS 77.040.20 H 26
GB
中华人民共和国国家标准
GB/T 299972013
铜及铜合金棒线材涡流探伤方法
Eddy current testing method of copper and copper-alloys rods,bars and wires
2014-08-01实施
2013-11-27发布
中华人民共和国国家质量监督检验检疫总局
中国国家标准化管理委员会 发布
GB/T 29997—2013
前言
本标准按照GB/T1.1—2009给出的规则起草本标准参考采用ASTME1606-2009《电工用重拉铜棒的电磁(涡流)检测方法》。 本标准由全国有色金属标准化技术委员会(SAC/TC243)归口。 本标准负责起草单位:中国有色金属工业无损检测中心、佛山市华鸿铜管有限公司、中铝洛阳铜业
-
有限公司、中铝上海铜业有限公司。
本标准主要起草人:张光济、林国良、李湘海、黎晓桃、奚国平、施海青、张熹、蒋杰、张小青。
-
GB/T29997-2013
铜及铜合金棒线材涡流探伤方法
1范围
本标准规定了铜及铜合金棒线材进行穿过式和点式涡流探伤的方法、对比试样、仪器设备、操作步骤和结果的评定。
本标准适用于外径Φ2mm~Φ100mm棒线材表面及近表面缺陷的涡流探伤,其他规格的棒线材可参照本标准执行。
注:棒线材涡流探伤应在传动装置上自动进行,如需采用手动涡流探伤,可由供需双方协商确定。
2规范性引用文件
下列文件对于本文件的应用是必不可少的。凡是注日期的引用文件,仅注日期的版本适用于本文
件。凡是不注日期的引用文件,其最新版本(包括所有的修改单)适用于本文件。
GB/T5248—2008铜及铜合金无缝管涡流探伤方法 GB/T9445一2005无损检测人员资格鉴定与认证 GB/T12604.6—2008无损检测术语涡流检测
3术语及定义
下列术语及定义适用于本文件。
3.1
(铜棒线)在线涡流探伤方法 on-lineeddycurrenttestingmethodofcopperrods,barsandwires 利用电磁感应在铜棒线材表面和近表面产生涡流的原理,对生产过程中的成品和半成品棒线材进
行整盘或整卷的探伤方法。 3.2
(铜棒线)离线涡流探伤方法off-lineeddycurrenttestingmethodofcopperrods,barsandwires 利用电磁感应在铜棒线材表面和近表面产生涡流的原理,对生产过程中的成品和半成品棒线材进
行逐根或逐条探伤的方法。 3.3
信噪比signaltonoiseratio 在涡流探伤仪器输出端缺陷信号幅度与最大噪声信号幅度之比。
3.4
零电势differenceofinduced-potential 检测线圈采用差动连接而在绕组之间形成的感应电压之差。检测线圈内有试件时为有载零电势
检测线圈内无试件时为空载零电势。 3.5
穿过式涡流探伤方法feed-througheddycurrenttestingmethod 采用穿过式涡流检测线圈进行涡流探伤的方法。
1
GB/T29997—2013
3.14
相位分析phaseanalysis 对涡流检测信号的相位角实施测量和分析的技术。 【GB/T12604.6-2008,定义7.3。】
3.15
调制分析modulationanalysis 对检波后的涡流信号进行频率分析的技术。 【GB/T12604.6—2008,定义7.5。】
4方法原理
涡流探伤是金属材料的一种无损检测方法。涡流探伤的灵敏度是以标准样棒(线)上人工缺陷当量的大小来衡量的。但人工缺陷的尺寸不应解释为涡流探伤可以检测到缺陷的最小尺寸。由于探伤灵敏度与涡流密度有关,而涡流密度随着棒线材外表面距离的增加而呈指数曲线下降,探伤灵敏度也随之下降。当表面有缺陷的导电试件通过由交流电流激励线圈时,则试件表层感应出的涡流会发生畸变,这一变化使线圈的阻抗发生变化,导致在检测线圈内产生的电信号发生变化。经信号处理可得到缺陷信号的显示图像、电信号、声光报警、记录等。从缺陷信号的幅值和相位可对缺陷进行判断。
注1:若含有磁性的棒线材(如铜镍合金材)因其所固有的磁导率不均匀性,可能导致检测结果的不正确,通常可以
采用饱和磁化技术加以消除。 注2:对于棒线材中存在的连续而深度缓慢变化的纵向缺陷,用穿过式自比差动线圈检测,其信号可能总是达不到
报警电平。
5仪器和设备
5.1涡流探伤系统主要包括涡流探伤仪器、检测线圈和传动装置。还包括记录装置、电气控制、磁饱和等辅助装置。 5.2涡流探伤仪器:涡流探伤仪器应具有激励、放大、信号处理(包括相位分析、调制分析和幅度分析等)、信号显示、声、光报警、端部信号消除、分选、标记、打印信号输出等单元或功能。探伤仪应具良好的稳定性和抗干扰能力。 5.2.1信号显示可以是阻抗平面的矢量显示,也可以是单向或双向幅度显示。 5.2.2增益器对于相应的标准人工缺陷信号而言,应有不小于10dB的余量。 5.3检测线圈:穿过式线圈一般由单个或多个测量线圈和激励线圈构成的差动式线圈组成,以单一频率激励,检测线圈内径与被检棒线材外径匹配,其填充系数不小于0.70。点式线圈探头可采用绝对式、 差动式等方式,应与仪器有良好的匹配,采用铜棒线与线圈作相对匀速旋转运动和匀速直线运动的方式进行检验。点式线圈探头与探伤仪配合,应有间隙补偿功能,以便克服由提离效应引起的检测误差。 5.4传动装置:主要包括进、出料架、传动辊道、驱动压轮、成品分选等部分,各机构的动作应平稳,并且在最小振动条件下同心地使被检棒线材通过检测线圈。 5.4.1传动装置的传送速度应匀速,其波动范围应不大于士5%。 5.4.2棒线材在线检验应配有收放线装置,并且收放线装置有可靠的同心度,能确保工件同心地通过探头。并要安装打标或剪切装置。 5.5磁饱和装置:饱和磁化装置应能在棒线材的被检区域产生足够的饱和磁化能力,能消除其磁导率不均匀所引起的干扰信号。 5.6涡流探伤设备在实际探伤过程中,不允许对被检棒线材造成机械损伤。
3
GB/T29997-2013
5.7 涡流探伤仪器与装置应定期检测,按本标准进行综合性能测试。涡流探伤系统的综合性能指标应符合表1的规定。各指标测试方法按附录A进行。
表1 涡流探伤综合性能指标
周向灵敏度差Z ≤3 dB
信噪比 S/N ≥10 dB
端部不可检 人工缺陷大小 人工缺陷漏测(盲区)
人工缺陷误报率Kz
长时间稳定性(波动值)
分辨率 ≤0.2mm
报率K,
≤3.0%
≤2 dB
≤100mm
≤1.0%
标准人工缺陷样棒(线)
6
6.1 标准人工缺陷样棒(线),是经人工加工的有标准伤的棒线材,用于调节探伤灵敏度、测定探伤设备的综合性能及在探伤过程中校验设备。 6.2标准人工缺陷样棒(线)的材质,必须与被检棒线材的牌号、规格、表面状态、热处理状态相同,并且无自然缺陷的低噪声棒线材。 6.3标准人工缺陷的形状:钻孔和纵向刻槽(U型)。可采用电火花或机械加工制作。 6.4 标准人工缺陷样棒(线)的孔径、纵长刻槽尺寸,与被检棒线材的外径的对应关系见表2和表3。
表2标准人工缺陷纵长刻槽尺寸等级
棒(线)直径D
人工缺陷等级代号 N-3% N-4% N-1% N-2 % N-3% N-4% N-0.2 N-0.3 N-0.4 N-0.5 N-0.6 N-0.8 N-1.0 N-1.2 N-1.5
槽深h mm 3%D 4%D 1%D 2%D 3%D 4%D 0.2 0.3 0.4 0.5 0.6 0.8 1.0 1.2 1.5
槽宽W mm
槽长L mm ≤20
槽深允许偏差
mm
mm
2~8
±10%h
≤0.3
士10%h但不得超过士0.05
>8~30
≤0.3
≤20
>30~100
±0.05
≤0.5
≤20
注1:等级的选择由供需双方决定,应考虑被检棒线材表面粗糙度、平直度和加工状态的因素;注2:槽长的选择可根据探伤速度及探头个数确定;注3:槽深应由供需双方选定,槽深最小不能小于产品直径公差之半
4
GB/T29997—2013
表3标准人工缺陷钻孔尺寸
棒(线)直径D
孔径Φ mm 0.6 0.7 0.8 1.0 1.2 1.4 1.6 1.8 2.0 2.2 3.0
允许偏差 mm
孔深h mm 0.5 1.0 1.5 2.0
人工缺陷等级代号
mm
N-0.6 N-0.7 N-0.8 N-1.0 N-1.2 N-1.4 N-1.6 N-1.8 N-2.0 N-2.2 N-3.0
2~30
±0.05
1.0 1.5 2.0 2.5 3.0
>30~100
±0.05
6.5离线检测的标准人工缺陷样棒(线)长度应大于2000mm,直度不大于1.5mm/m,轴向5个相同钻孔,2个钻孔分别距离棒(线)端100mm,中间3个孔之间的距离为500mm,并沿圆周方向相隔120° 分布,可按照图1a)、图1b)或图1c)制作。
单位为毫米
od,
100
0
a)
11
500
500
b)
图1标准人工缺陷样棒(线)图
5
GB/T29997—2013
单位为毫米
100
od,
V
/
0
1 e)
说明: d,标准人工缺陷孔径; d- 棒线材外径。
图1(续)
7操作步骤
7.1 棒线材在进行涡流探伤之前应进行外形尺寸和表面质量的检查。 7.2 :涡流探伤仪器和设备应在预热稳定后,方可进行调试、探伤。 7.3 根据被检棒线材的规格,选择同牌号、同状态、同规格的有标准人工缺陷的样棒(线)。 7.4选择合适的检测线圈和导套,并安装固定好。 7.5调整设备的主机与工件的同心度。 7.6调整仪器的参数:选择合适的频率、相位、滤波,确定灵敏度(即增益)。 7.6.1 确定灵敏度时,连续走5次,使5个人工缺陷都报警。 7.6.2确定灵敏度时,中间三个人工缺陷的周向灵敏度差不大于3dB,信噪比不小于10dB。 7.7 正常探伤:在确定灵敏度基础上,再提高2dB灵敏度值,方可对棒线材进行涡流探伤。 7.8材质含磁性时,可以采用饱和磁化装置,使其被检区域达到磁饱和。 7.9离线检测:每隔2h~4h应对7.6.2调整的仪器参数进行校验。若发现灵敏度的波动值大于2dB 时,应对上一次至本次检验之间的棒线材进行复检。 7.10棒线材的在线检测:没有传动装置时可用手动方法参照离线检测确定灵敏度。在正常探伤时,应开启打标对应装置(或剪切装置)。
8探伤结果的评定
8.1 没有警报信号的棒线材均为涡流探伤合格。 8.2对于直状棒线材,有报警信号的均为涡流探伤不合格。如对缺陷信号有疑问,应进行复探。 8.3对于盘状棒线材,有缺陷信号报警的部位均为涡流探伤不合格部位。可通过打标装置直接在有缺陷的区域上打印标记或进行剪切。标记长度由供需双方协商确定,一般为300mm~600mm,伤点应在标记范围内,并作好缺陷数量的记录。
6