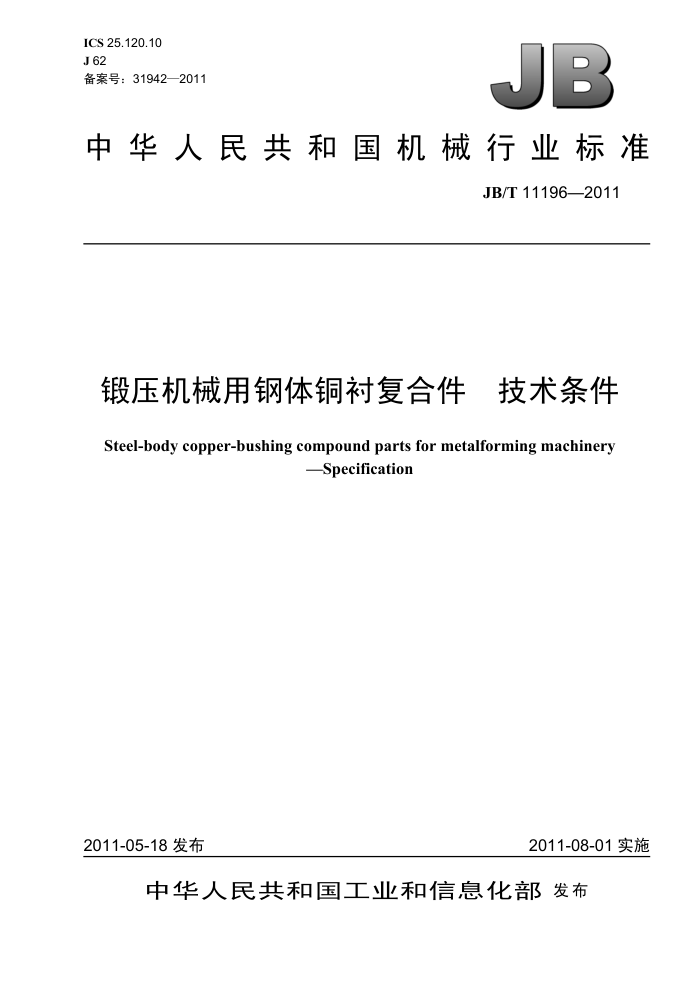
ICS25.120.10 J 62 备案号:31942—2011
JB
中华人民共和国机械行业标准
JB/T 11196—2011
锻压机械用钢体铜衬复合件 技术条件
Steel-body copper-bushing compound parts for metalforming machinery
-Specification
2011-05-18 发布
2011-08-01实施
中华人民共和国工业和信息化部发布
JB/T11196—2011
目 次
前言范围..
I11
1
规范性引用文件. 3 复合件分类.. 4 技术要求.... 4.1 化学成分及力学性能 4.2 尺寸公差及公差带. 4.3 加工余量, 4.4 计算示例毛坏尺寸 4.5 几何形状、尺寸 4.6 表面质量要求.. 4.7 缺陷的修整. 4.8 钢体铜衬结合面.
2
试验方法. 6 验收规则 6.1 复合件检验权利和检验地点, 6.2 试样 6.3 试验次数、试验结果的评定和复验, 6.4复合件几何形状、尺寸和表面质量的验收
5
标志与证明... 图1 复合件分类示意图图2 圆环件. 图3复合件结合面压力试验试件,表1 复合件分类.. 表2复合件尺寸公差表3加工余量.. 表4示例毛坏尺寸表5 加工表面的浇冒口残留量
7
JB/T11196—2011
前言
本标准按照GB/T1.1一2009给出的规则起草。 请注意本文件的某些内容可能涉及专利,本文件的发布机构不承担识别这些专利的责任,本标准由中国机械工业联合会提出。 本标准由全国锻压机械标准化技术委员会(SAC/TC220)归口。 本标准负责起草单位:青岛正大铸造有限公司、中国海洋大学材料科学与工程研究院、深圳市华测
检测有限公司。
本标准主要起草人:宋敬清、宋鲲鹏、王昕、郭冰、孙华山。 本标准为首次发布。
III
JB/T11196—2011
锻压机械用钢体铜衬复合件 技术条件
1范围
本标准规定了锻压机械用钢体铜衬复合件的分类、技术要求、试验方法、验收规则、标志与证明本标准适用于锻压机械中用离心铸造方法生产的钢体铜衬复合件(以下简称复合件)。
2规范性引用文件
下列文件对于本文件的应用是必不可少的。凡是注日期的引用文件,仅所注日期的版本适用于本文件。凡是不注日期的引用文件,其最新版本(包括所有的修改单)适用于本文件。
GB/T699优质碳素结构钢 GB/T1176一1987铸造铜合金技术条件 GB/T6060.1表面粗糙度比较样块铸造表面 GB/T6414一1999铸件尺寸公差与机械加工余量 GB/T11352—2009 一 一般工程用铸造碳钢件
3复合件分类 3.1根据工作条件和用途将复合件分为两类,即螺母类和轴套(瓦)类。如图1和表1所示。
钢体 a)螺母类
铜衬
钢体 铜衬 b)轴套(瓦)类
图1复合件分类示意图
表1复合件分类
类别螺母类
检验项目
工作条件和用途
承受重载荷,工作条件复杂,用于传递打击力,如:主螺母承受中等载荷,要求耐磨性能好,如:轴套、轴 尺寸、表面质量、化学成分、力学性能及补瓦等
尺寸、表面质量、化学成分、力学性能及特殊要求
轴套(瓦)类
充要求
3.2铸件类别由需方在图样或技术文件中规定,或供需双方协商规定。
1
JB/T11196—2011
技术要求 4.1化学成分及力学性能 4.1.1复合件铜衬的化学成分及力学性能应符合GB/T1176的规定。 4.1.2 2对于两类复合件,以力学性能为主要验收依据。化学成分允许略有偏差,允许偏差值为各主要成分含量上、下限的10%。 4.1.3 3复合件钢体的化学成分及力学性能应符合GB/T699及GB/T11352的规定。 4.2尺寸公差及公差带 4.2.1尺寸公差应符合GB/T6414一1999的规定,常用等级代号与公差等级见表2。同一复合件选用同公差等级,公差等级按复合件坏件最大尺寸选取。
4
表2 复合件尺寸公差
单位为毫米
公差等级
公称尺寸 ≥40~63 >63~100 >100~160 >160~250 >250~400 >400~630 >630~1000 >1000~1600
CT10 2.8 3.2 3.6 4.0 4.4 5.0 6.0 7.0
CT11 4.0 4.4 5.0 5.6 6.2 7.0 8.0 9.0
4.2.2 公差带一般对称于坏件公称尺寸配置,并应符合GB/T6414一1999的规定。坏件公称尺寸指:
图样中标注的两个非加工面之间的尺寸;一图样中标注的非加工内、外径,圆角和圆弧。
4.3加工余量 4.3.1坏件的加工余量是指一个面的加工余量。旋转体或两个面需加工的表面加工余量应按两倍计算。 4.3.2 加工余量按毛坏最大尺寸从表3中选取。
表3 加工余量
单位为毫米
加工余量(≥)
毛坏最大尺寸
孔 2.0 3.0 3.5 4.0 4.5 5.0 6.0
外圆、端面
≤100 >100~160 >160~250 >250~400 >400~630 >630~1000 >1000~1600
4.0
6.0
4.4计算示例毛坏尺寸 4.4.1 示例毛坏要求如下:
2