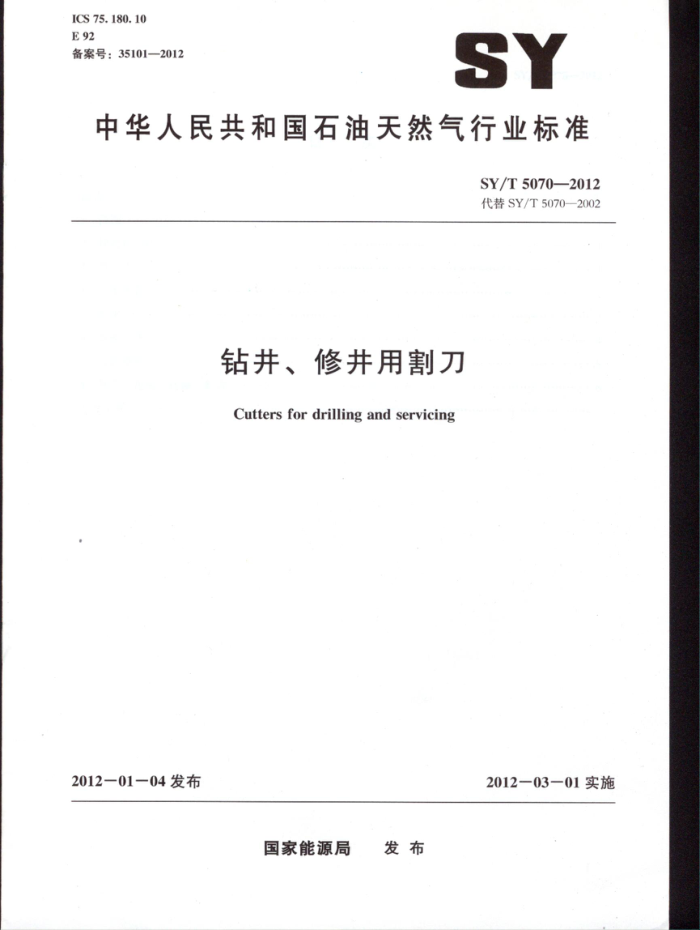
ICS75.180.10 E92 备案号:35101—2012
SY
中华人民共和国石油天然气行业标准
SY/T5070—2012 代替SY/T5070—2002
钻井、修井用割刀 Cutters for drilling and servicing
201201-04发布
2012一03一01实施
国家能源局 发布
SY/T 5070—2012
目 次
前言 1 范围 2 规范性引用文件 3 型号表示方法
基本参数 5 要求试验方法
4
6
检验规则标志、包装、运输、贮存
V
5
8
6
参考文献
SY/T5070—2012
前言
本标准按照GB/T1.1一2009《标准化工作导则第1部分:标准的结构和编写》给出的规则起草。
本标准代替SY/T5070—2002《钻修井用割刀》。本标准与SY/T5070—2002相比,主要变化如下:
增加了割刀的规格,修改了2002年版的表1、表2的内容(见表1、表2);修改了探伤要求(见5.4);修改了力学性能符号;修改了力学性能要求(见5.1);修改了刀头的要求(见5.3);修改了出厂检验项目和型式检验项目(见第7章)。
本标准由全国石油钻采设备和工具标准化技术委员会(SAC/TC96)提出并归口。 本标准起草单位:石油工业井下工具质量监督检验中心、贵州高峰石油机械股份有限公司、通化
石油工具股份有限公司、丹诺(北京)石油技术服务有限公司。
本标准主要起草人:蒲玲霞、万文财、史利强、罗涛、刘晓晓、姜永奎、明祥贵、张虎林。 本标准代替了SY/T5070—2002。 SY/T5070—2002的历次版本发布情况为
SY5070—1985,SY/T5070—1991; -SY5424—1991; -SY/T5688—1995。
ⅡI
SY/T5070—2012
钻井、修井用割刀
1范围
本标准规定了割刀的型号表示方法、基本参数、要求、试验方法、检验规则、标志、包装、运输和贮存等。
本标准适用于石油钻修井作业中切割油管、套管和钻杆本体等管材所用水力式和机械式内、外割刀的设计、制造和检验。
2规范性引用文件
下列文件对于本文件的应用是必不可少的。凡是注日期的引用文件,仅注日期的版本适用于本文件。凡是不注日期的引用文件,其最新版本(包括所有的修改单)适用于本文件。
GB/T228.1金属材料拉伸试验第1部分:室温试验方法(GB/T228.1—2010,ISO6892 -1:2009,MOD)
GB/T229金属材料夏比摆锤冲击试验方法(GB/T229—2007,ISO148-1:2006,MOD) GB/T230.1金属材料洛氏硬度试验第1部分:试验方法(A、B、C、D、E、F、G、H、
K、N、T标尺)(GB/T 230.1—2009,ISO6508-1:2005,MOD)
GB/T231.1金属材料布氏硬度试验第1部分:试验方法(GB/T231.1—2009,ISO6506 -1:2005,MOD)
GB/T9253.2石油天然气工业套管、油管和管线管螺纹的加工、测量和检验(GB/T 9253.2—1999,API Spec 5B: 1996, IDT)
GB/T22512.2石油天然气工业旋转钻井设备第2部分:旋转台肩式螺纹连接的加工与测量 (GB/T 22512.2—2008,ISO10424-2:2007,MOD)
SY/T5029抽油杆(SY/T5029—2006,APISpec11B:1998,MOD) JB/T4730.3承压设备无损检测第3部分超声检测(JB/T4730.3—2005,ASME第V卷,
NEQ)
JB/T4730.4承压设备无损检测第4部分磁粉检测(JB/T4730.4—2005,ASME第V卷,NEQ)
3型号表示方法
OD-OOXO
副参数代号,工具公称外径,以工具外径的毫米数表示主参数代号,以切割落鱼外径的毫米数表示型式代号,S代表“水力式”,J代表“机械式” 名称代号,D代表“割刀” 类型代号,N代表“内”,W代表“外”
SY/T5070—2012
示例1: ND-J127×102表示切割落鱼外径为127mm,工具外径为102mm的机械式内割刀。 示例2: WD-S89×143表示切割落鱼外径为89mm,工具外径为143mm的水力式外割刀。
基本参数
4.1 内割刀的基本参数见表1。
表1 内割刀的基本参数
切割落鱼外径,mm
接头螺纹
轴向推刀力
型号 ND-J(S)60× ND-J(S)73× ND- (S)89×
kN
允许用
套管
推荐 1°/16油杆螺纹
油管 60. 3 73.0 88.9 101.6 114.3
钻杆 60.3 73.0 88.9
3~6
1.900TBG 23% TBC 2%TBG NC26 NC31 NC31 NC38
1.900TBG
(S) 102×□
ND
114.3
114.3 127.0 127.0 139.7 139.7 168.3
ND- (S)114×口 ND- (S)127X
2VREG 2%REG
S) 140×
ND-
4~10
ND- (S)168×
4%FH 3REG NC50 5MFH 6REG
NC46
177.8
ND- (S)178×
NC46 NC50 NC50 6%REG 6%REG 6%REG 6%REG 6%REG 6%REG 7REG 75AREG 6%REG
193.7 219.1 244.5 273.0 298
ND- (S)193X
ND- (S)219X ND- (S)245X ND- (S)273×
(S)298×
ND
10~30
ND- (S)340X ND- 1 (S) 406×
9
406.4
ND- (S)473× ND- (S)508× ND- J(S)762X ND-J (S)914× ND-J(S)1524×
508.0 762.0
20~50
14
1524.0
注1:J(S)表示机械式(或水力式)。 注2:口表示由制造厂自行确定的工具外径
4.2外割刀的基本参数见表2。
2
SY/T5070—2012
表2外割刀的基本参数
提升落鱼能力
剪销剪断力
轴向推刀力
型号
推荐接头螺纹
切割落鱼 33.3油管 60.3油管
kN 5 10 16 14 10 21 21 16 14 10 10 20 28 21 21 41 41 28 20 20
kN
kN
WD-J(S)33× WD-J (S)60× 4CSG
4%CSG
6~10
WD-J(S)73× 5VLCS
73.0油管
3~8
WD-J(S)89×
5%LCSG
88.9油管
8~15
WD-J(S)102× 7LCSG
101.6油管
WD-J(S)114× 7LCSG
114钻杆或油管
10~20
10~30
WD-J(S)127×
7LCSG
127.0钻杆
WD-J(S)140× 8% LCSG
139.7
注1:J(S)表示机械式(或水力式)注2:口表示由制造厂自行确定的工具外径。 注3:接头螺纹可采用套铣管的双级螺纹或偏梯形螺纹。
5要求
5.1 内割刀的心轴和外割刀的上接头,外筒等主要零件热处理后材料的力学性能应符合表3的规定。
表3主要零件力学性能下屈服强度Rel
割刀外径 mm <178 ≥178
抗拉强度Rm
伸长率A
冲击功Ak
硬度 HBW10/3000
MPa ≥965 ≥931
%
MPa ≥760 ≥690
J
≥285 ≥277
≥13
≥54
5.2 内割刀的锚定卡瓦应进行表面处理,卡瓦牙表面硬度为50HRC~65HRC。
刀头采用高速工具钢制作的,刀头热处理后的刃部硬度应为55HRC~65HRC。刀头采用碳化
5.3
3
SY/T5070—2012
钨硬质合金焊条堆敷焊的,堆焊层不得有未熔透、裂纹等缺陷。焊料与硬质合金、刀体须结合良好。 5.4主要零件应进行无损探伤检验。超声探伤不应有超过JB/T4730.3锻件超声检测规定的ⅡI级缺陷,磁粉探伤不应有超过JB/T4730.4锻件磁粉检测规定的Ⅱ级缺陷。 5.5内割刀的连接螺纹应符合GB/T22512.2,GB/T9253.2或SY/T5029的要求。外割刀的连接螺纹应符合GB/T9253.2或相应套铣管的连接螺纹的要求。 5.6各相对转动或相对移动零部件应运动灵活,不得有卡滞现象。刀头完全伸出时,内割刀的刀尖直径应大于落鱼外径8mm以上,外割刀的刀尖直径应小于落鱼的最小内径8mm以上。刀头复位时应无卡阻。 5.7机械式内割刀卡瓦产生的锚定力应大于表1所规定的轴向推刀力。 5.8外割刀如有剪销控制,其剪销剪断力应符合表2的规定。 5.9切割试验时,割刀应能在20min内割断落鱼,刀体不应产生断裂或影响刀体收回的变形,刀尖不得有崩刃或显著磨钝,落鱼切口应平整。 5.10能够从井内起出切割点以上落鱼的外割刀,其提升落鱼能力应不低于表2的规定。
6 试验方法
6.1材料的力学性能检验
主要零件的拉伸试样和冲击试样均沿纵向截取,试样中心线应距外表面25mm,或者在零件壁厚中间处截取。试验按GB/T228.1和GB/T229的有关规定执行。洛氏硬度和布氏硬度的试验方法分别按GB/T230.1和GB/T231.1中的有关规定执行。刀刃硬度的检验部位应在距刀尖不大于10mm 的范围内。 6.2无损探伤
无损探伤时应按JB/T4730.3和JB/T4730.4规定的检测方法执行。 6.3连接螺纹检验
割刀采用的钻杆接头螺纹按GB/T22512.2规定的方法进行,油管和套管螺纹的检验按GB/T 9253.2规定的方法进行,割刀采用的抽油杆螺纹应进行松动试验,试验方法按SY/T5029规定的方法进行。 6.4运动灵活性
转动或移动各相对运动部件,检查是否有卡滞现象;拨动刀体,检查其伸出和复位。 6.5切割性能试验 6.5.1切割前的准备
选取与割刀切割范围相适应的管柱作为落鱼,将其竖直固定。把割刀连接于切割管柱上,缓慢下放割刀进人落鱼至预定切割位置。 6.5.2切割条件
切割条件包括: a)冷却液连续冷却。 b)转速:20r/min~60r/min。
4
SY/T5070—2012
6.5.3切割试验 6.5.3.1机械式内割刀
割刀转动数圈后,下压心轴,锚定卡瓦,按5.7检查卡瓦的锚定能力。转动割刀,同时按表1的规定施加轴向推刀力,直至割断落鱼,并记录切割时间。上提割刀,卡瓦应能顺利收回。起出割刀,检查刀体、刀尖和落鱼切口。 6.5.3.2水力式内割刀
转动割刀,同时开泵循环,使活塞产生的推力与表1中规定的轴向推刀力相符合,直至割断落鱼,并记录切割时间。起出割刀,检查刀体、刀尖和落鱼切口。 6.5.3.3机械式外割刀
割刀如有剪销控制,需先剪断剪销,记录剪断力。然后正转割刀,按表2的规定施加轴向推刀力,直至割断落鱼,并记录切割时间。起出割刀,检查刀体、刀尖和落鱼切口。 6.5.3.4水力式外割刀
割刀如有剪销控制,需先剪断剪销,记录剪销剪断压差或剪断力。然后正转割刀,开泵循环,使活塞产生的推力与表2中规定的轴向推刀力相符合,直至割断落鱼,并记录切割时间。起出割刀,检查刀体、刀尖和落鱼切口。 6.6外割刀提升落鱼能力
将落鱼固定,使割刀套入相应的落鱼,缓慢施加轴向拉力,直至负荷增加至表2所规定的提升落鱼能力的1.5倍,保持5min,在用人力沿径向敲击落鱼产生振动的情况下不得滑脱,然后卸载检查,各零件不得有变形或损坏。
检验规则
7
7.1 检验分类 7.1.1出厂检验
产品经制造厂检验部门检验合格后,并附有产品合格证明文件方可出厂。 7.1.2 型式检验
有下列情况之一时,应进行型式检验。
样机试制。 正式生产的产品在结构、材料和工艺方面有较大改变,可能影响产品性能时。 国家或行业质量监督机构提出型式检验要求时。
7.2检验项目 7.2.1出厂检验按照以下项目进行:
a)结构参数。 b) 热处理零件硬度。 c) 接头螺纹。