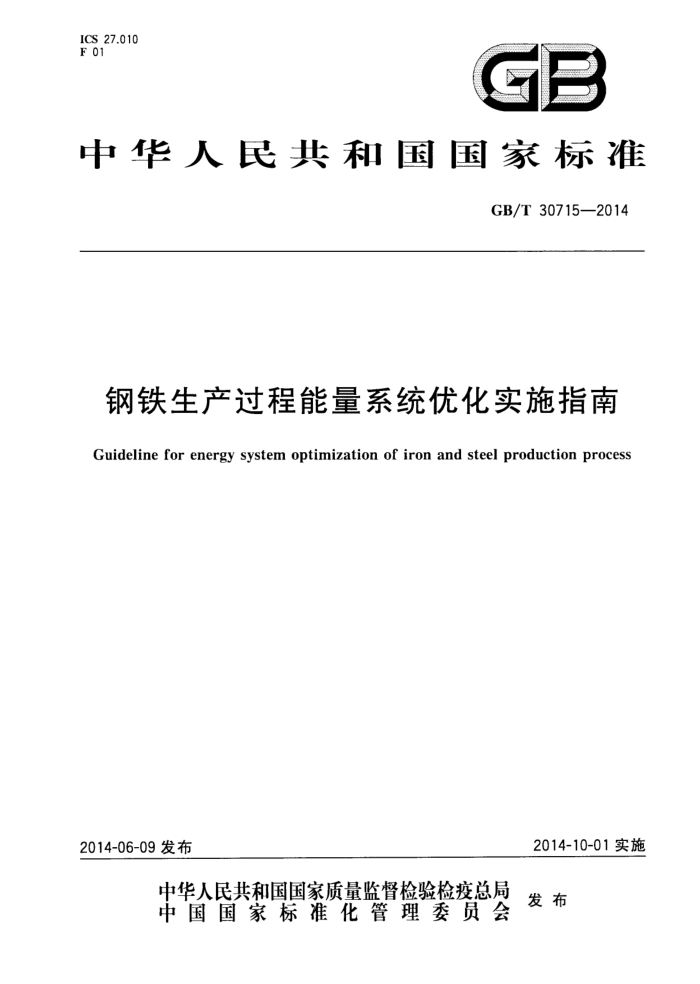
ICS 27.010 F 01
g2
中华人民共和国国家标准
GB/T30715—2014
钢铁生产过程能量系统优化实施指南
Guideline for energy system optimization of iron and steel production process
2014-10-01实施
2014-06-09发布
中华人民共和国国家质量监督检验检疫总局
中国国家标准化管理委员会 发布
GB/T 30715—2014
前言
本标准按照GB/T1.1一2009给出的规则起草
:
本标准由全国能量系统标准化技术委员会(SAC/TC459)提出并归口。 本标准起草单位:中国标准化研究院、钢铁研究总院、山东钢铁集团有限公司、唐山钢铁集团有限责
任公司、太原钢铁(集团)有限公司、北京首钢股份有限公司、宝钢集团有限公司、冶金工业信息标准研究院、南京钢铁股份有限公司、济钢集团有限公司、四川省节能技术服务中心。
本标准主要起草人:刘猛、邮秀萍、梁凯丽、王宝军、闫振武、姚红、戴坚、于永森、白雪、冯凉、仇金辉、 陈飚、杨勇。
-
GB/T307152014
钢铁生产过程能量系统优化实施指南
1范围
本标准给出了实施钢铁生产过程能量系统优化的原则、步骤及其主要内容。 本标准适用于现有钢铁生产过程能量系统优化工作,新建或改扩建钢铁生产过程项目的能量系统
优化可参照本标准执行。
2规范性引用文件
下列文件对于本文件的应用是必不可少的。凡是注日期的引用文件,仅注日期的版本适用于本文件。凡是不注日期的引用文件,其最新版本(包括所有的修改单)适用于本文件。
GB/T2589 综合能耗计算通则 GB/T3484 企业能量平衡通则 GB/T13234 企业节能量计算方法 GB/T 28749 企业能量平衡网络图绘制方法 GB/T28750 节能量测量和验证技术通则 GB/T28751 企业能量平衡表编制方法 GB/T28924一2012钢铁企业能效指数计算导则
3术语和定义
GB/T28924一2012界定的以及下列术语和定义适用于本文件
3.1
钢铁生产过程ironandsteelproductionprocess 以铁矿石或废钢为原料,包括炼铁、炼钢和轧钢等主工序,原料处理、动力系统、运输系统等辅助工
序的钢铁产品制造过程。 3.2
钢铁生产过程能量系统energysystemofironandsteelproductionprocess 钢铁生产过程中能量转换、输送、分配、储存、使用和回收等一个或若干个环节组成的系统。
3.3
钢铁生产过程能量系统优化energysystemoptimizationofironandsteelproductionprocess 以钢铁生产过程能量系统为研究对象,通过系统分析,结合先进工艺和节能技术的应用,找出提升
系统整体能源利用效率的机会,在满足生产需求的前提下,提出并实施系统优化方案,并对优化效果进行持续评估和改进的过程。 3.4
载能体energycarrier 在制备或生产过程中消耗了能源的物质,或本身可产生能量的物质。
1
GB/T30715—2014
4基本原则
钢铁生产过程能量系统优化应遵循以下基本原则: a) 重视能源和非能源物质等载能体的节约; b) 进行全生产过程的能耗分析,包括直接能耗和间接能耗;
充分考虑安全生产和环境保护等约束条件;
c) d)
充分考虑成本控制和经济效益等因素; e) 充分考虑各类影响因素,如产品品种结构、能源结构、原料品质、产品深加工程度等;
充分考虑与周边社区、企业的能源优化;
f
g)确保能量系统优化实施效果的稳定持续。
5
基本实施步骤
开展钢铁生产过程能量系统优化工作包括但不限于以下基本实施步骤: a)系统边界划分; b)系统现状调研; c)系统总体用能分析; d) 优化方案的制定; e) 优化方案的实施; f) 效果评估。
6 系统边界划分
6.1 边界类别
边界划分主要包括以下类别: a)工序边界,以原材料或中间产品的输人确定每个工序的起点,以中间产品或最终产品的输出确
定每个工序的终点; b) 管理边界,边界内包括企业内的钢铁主工序和辅助工序;
关联企业边界,边界内包括相关联的不同企业;
c):
d)地理边界,边界内包括主要生产设施所处的地理区域。 6.2 划分原则
边界划分主要遵循以下原则: a) 边界划分应以管理边界为主,确保边界内能量系统优化工作的可控性; b) 当与钢铁生产过程相关联的不同企业均参与到同一能量系统优化工程中时,可按照关联企业
边界划分系统;应通过描述系统的工艺流程图,明确系统和各工序的边界,示例参见附录A;明确上述边界后,确定相应的地理边界。
c) d)
2
GB/T30715—2014
7系统现状调研
7.1内容
现状调研包括但不限于以下内容: a)钢铁生产流程和工艺生产装置、重点耗能设备设计能力、实际生产能力、工艺及产品方案、全厂
总平面布置及主要物流、原料和产品类别、品种结构、数量、质量、价格等; b) 生产控制数据,包括操作参数、原料和产品质量控制指标、产品深加工程度、生产装置、系统生
产负荷等; c) 能源及耗能工质消耗类别、数量、质量、价格等; d) 重点耗能设备能源利用效率; e) 钢铁生产过程二次能源回收利用情况,如副产煤气、余热蒸汽、余热余压等二次能源产生利用
数据; f) 生产装置、公辅系统生产瓶颈以及用能存在的主要问题; g) 与厂外生活区、邻近工业园区及周边企业能源互供的现状及未来互供的可能性及可靠性; h)环境保护执行的标准; i) 环境温度、气压和湿度等气象数据; j) 企业发展规划,包括新建装置、扩能及重大技改等。
7.2数据资料收集与分析
现状调研过程中数据资料收集与分析包括但不限于以下要点: a)收集一定时期内企业稳定生产情况下用能分析评价及优化方案制定等所需的相关资料和
数据; b)对所收集数据和资料的完整性和准确性进行分析,可依据物料平衡、能量平衡和相互间关联关
系,对数据进行校正及核实,必要时应对存有疑问或不足的重要数据进行实测。
8系统总体用能分析
8.1概述
通过分析与能量系统生产和用能直接相关的各种因素对系统能源消耗总量的影响,找出能量系统优化的重点环节。 8.2基本分析内容 8.2.1利用第7章的调研结果,分别按照GB/T3484、GB/T28751和GB/T28749的要求绘制钢铁生产过程能量系统能量平衡表和能量平衡网络图,可根据系统实际情况构建钢铁生产过程能量系统优化模型。 8.2.2针对铁矿石或废钢等原料物质流,分析各工序用能情况(包括主要耗能设备能效情况),分析方法可采用能耗限额对标与e-P分析相结合的方法;其中能耗限额对标是与相关标准的能耗限额指标进行对比,无具体标准对应的应与国内外先进企业进行对标分析;e-P分析法可参照参考文献[1]、[2]。 8.2.3针对主要能源介质,对煤气系统、蒸汽系统、电力系统、气体系统、水系统等进行分析,从能源的产生、转换、输送、分配、储存、使用、回收等环节评价能量利用的合理性;分析二次能源回收利用情况,包
3
GB/T30715—2014 括二次能源富裕量、梯级利用或降质使用情况及损失率、二次能源发电装机容量、发电能耗等,评价二次能源利用的合理性。 8.2.4分析各主要耗能设备能效,并与相关的能效指标进行对比,无具体能效标准对应的应与国内外先进企业相关指标进行对标分析。 8.3分析结果输出
说明现有能量系统存在的问题、找出提升系统整体能效的机会及对应的节能技术,钢铁生产过程能量系统优化常见节能技术可参见但不限于附录B
优化方案的制定
9
9.1以本系统用能现状为基础,参照第4章的基本原则,充分考虑相关节能技术实施对系统整体节能效果和经济效益的综合影响,分别形成不同节能技术各自对应的优化方案。 9.2优化方案包括以下主要内容:
a)现状分析及存在的主要问题; b)优化方案设计; c)节能效果和经济效益估算; d) 实施建议。
10 优化方案的实施
优化方案的实施主要包括以下要点:
综合考虑不同的优化方案对系统能效、经济性的影响、对其他方案的影响、方案实施的技术经
a)
济可行性等因素进行优选排序,组合形成实施方案;优化方案实施后,持续跟踪方案的节能增效效果。对可持续采用的方案,适时改进工艺操作规程;对不能持续采用的方案分析原因,进行必要的调整。
b)
11 效果评估
11.1优化工作全部完成或阶段完成后,对钢铁生产过程能量系统用能情况进行后评价,以评估优化结果,相关评价计算结果记录备案作为今后优化工作的依据或参考。 11.2钢铁生产过程能量系统综合能耗计算可按照GB/T2589进行计算。 11.3钢铁生产过程能量系统优化实现的节能量可按照GB/T28750进行测量和验证。 11.4钢铁生产过程能量系统优化实现的节能量可按照GB/T13234进行计算。 11.5 5钢铁生产过程能量系统综合能效指数可按照GB/T28924一2012进行计算。
4
GB/T 30715—2014
附录A (资料性附录)
钢铁生产过程能量系统典型流程及边界示例
图A.1给出了钢铁生产过程能量系统典型流程及边界示例,
能源输入
外购焦炭
燃料油等
外购矿石
烧结
电炉
模铸
上游产品输入
球团
外购废钢
钢材
焦炉
高炉
转炉
连铸
轧钢
外购钢坏
中
外购熔剂
煤气加工输送
其他(石灰密、氧气厂、物流运输等)
外购铁合
自备电厂(锅炉等公辅设备)
外购其他
外销燃气
焦油苯等
系统边界
外销能源或与周边企业、社会共享
图A.1钢铁生产过程能量系统典型流程及边界示例
GB/T 30715—2014
附录B (资料性附录)
钢铁生产过程能量系统优化常见节能技术
B.1 优化工艺结构和产品结构
B.1.1 高炉、转炉流程的优化技术:
a) 铁、钢界面的衔接匹配技术,减少铁水转兑热损失和混铁炉保温的能源消耗: b)2 炼钢、连铸机的界面技术,高效连铸改造,提高运行速度,缩短运行时间
连铸、轧钢界面,提高连铸坏热送比例,提高热装温度。
c)
B.1.2电炉短流程,采用超高功率电炉技术,包括优化供电制度、煤氧强化冶炼、电炉汽化冷却等综合节能技术。 B.1.3 熔融还原技术,直接使用粉矿、煤粉,取消了造块、焦化工序。 B.1.4 提高工序能源利用效率:
a) 焦化工序:采用大型贮煤筒仓、大型机械焦炉和捣固炼焦炉、高效塔氨水蒸馏、负压蒸氨、负压
脱苯等工艺技术; b) 烧结工序:采用厚料层操作和低硅、低温烧结技术;回收烧结过程的余热余能,进行热风烧结、
热风点火和余热发电等; c) 炼铁工序:采用高风温、富氧大喷煤技术;利用热风炉烟气预热煤气和助燃空气;采用顶燃式热
风炉;高炉大型化及强化冶炼技术,提高大高炉冶炼强度和利用系数等; d)炼钢工序:采用一罐到底,完善转炉烟气净化回收系统;利用转炉余热蒸汽发电技术;干式机械
真空技术等; e) 轧钢工序:加热炉蓄热燃烧技术;热送热装技术。
B.1.5提高钢铁材料产品性能,提高钢材强度,延长其生命周期。
B.2 优化能源结构、提高能源效率、促进余热余能高效利用 B.2.1 高温高压燃气锅炉热电技术、燃气蒸汽联合循环发电技术,在可能条件下实现共同火力联合发电。 B.2.2 2煤化工优化技术,在生产焦炭的同时,完善焦油深加工工艺,提高焦化工序综合效益。 B.2.3采用高温高压锅炉的干熄焦技术、焦化人炉煤调湿技术、上升管余热回收技术、初冷器余热回收技术、导热油蒸氨节能技术、焦炉烟气余热回收利用技术。 B.2.4高炉炉顶余压发电技术、炉体软水闭路循环技术、高炉专家系统、高炉冲渣水余热回收利用技术等。 B.2.5蓄热式轧钢加热炉、蓄热式钢包烘烤技术、工业炉窑黑体节能技术、加热炉利用烟气进行空气、 煤气预热技术。 B.2.6优化煤气管网、蒸汽管网、氧气管网、氮气管网、压缩空气管网系统技术。 B.2.7变频调速、高效电机、绿色照明、干式变压器、无功补偿等节电技术。 B.2.8 3高炉煤气干法除尘、转炉煤气干法除尘等技术。 B.2.9 9副产煤气高附加值开发利用技术。 6