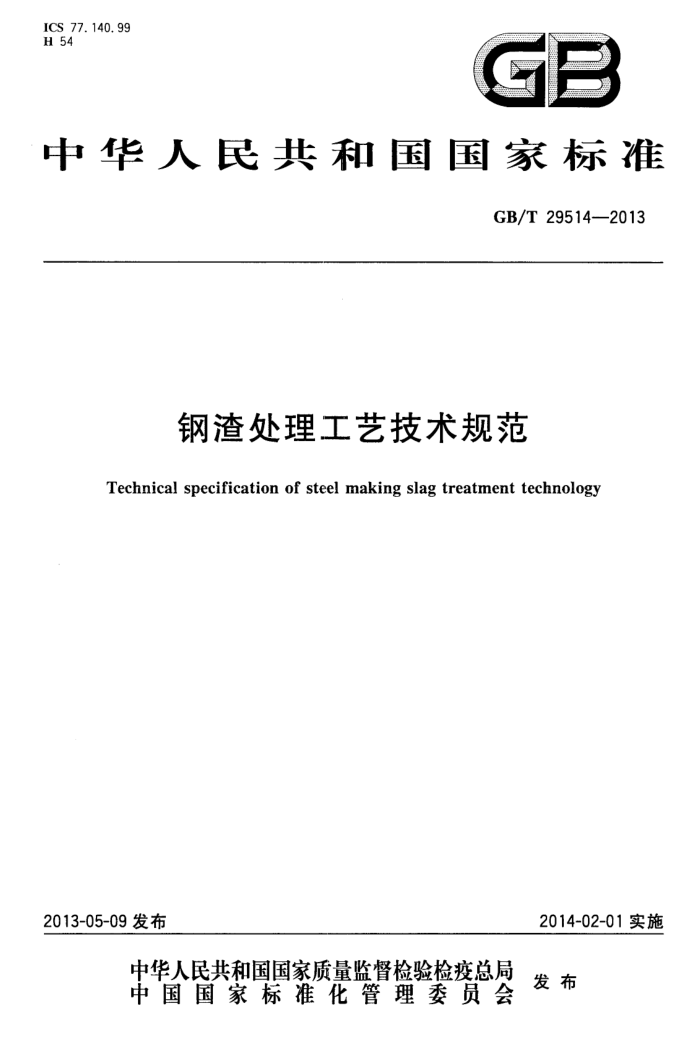
ICS 77.140.99 H 54
GB
中华人民共和国国家标准
GB/T29514-—2013
钢渣处理工艺技术规范
Technical specification of steel making slag treatment technology
2014-02-01实施
2013-05-09发布
中华人民共和国国家质量监督检验检疫总局
中国国家标准化管理委员会 发布
GB/T 29514—2013
前言
本标准按照GB/T1.1一2009给出的规则起草。 本标准由中国钢铁工业协会提出。 本标准由全国钢标准化技术委员会(SAC/TC183)归口。 本标准起草单位:济钢国际工程技术有限公司、鞍山钢铁集团公司矿渣开发公司、冶金工业信息标
准研究院、马鞍山钢铁股份有限公司、宝山钢铁股份有限公司、湖南华菱湘潭钢铁有限公司、浙江宏驰机械仪器制造有限公司。
本标准主要起草人:姜进强、苏兴文、陈树国、仇金辉、陈广言、高建平、肖永力、井广敏、李永谦、 李晓阳、唐奇山、刘茵、王姜维、丁陈来、张东力、李小莉、张萍、张关来。
I
GB/T29514—2013
钢渣处理工艺技术规范
1范围
本标准规定了钢渣处理工艺的术语和定义、技术要求、环境保护、操作与维护和安生要求。 本标准适用于热问、滚筒、风碎、水淬等钢渣处理工艺技术,主要用于处理炼钢过程产生的热态
钢渣。
2规范性引用文件
下列文件对于本文件的应用是必不可少的。凡是注日期的引用文件,仅注日期的版本适用于本文件。凡是不注日期的引用文件,其最新版本(包括所有的修改单)适用于本文件。
GB12348工业企业厂界环境噪声排放标准 GB/T20801压力管道规范(所有部分) GB50010混凝土结构设计规范 GB50016建筑设计防火规范 GB50046工业建筑防腐蚀设计规范 GB/T50265泵站设计规范 GB50316 工业金属管道设计规范 AQ2001炼钢安全规程 YB/T804钢铁渣及处理利用术语
3术语和定义
YB/T804确定的以及下列术语和定义适用于本文件。
3. 1
热闷装置equipmentof self-disintegratingby steam 以水蒸气为工艺介质,对热态钢渣进行热闷自解处理的容器。
3. 2
滚筒装置 equipmentof rotarycylinderprocess 以钢球为工艺介质,对热态钢渣急速冷却和碎化的可回转设备。
3.3
风碎装置equipmentofair-granulating 通过压缩空气对液态钢渣进行粒化处理的设备。
3. 4
水淬装置equipment of water-granulating 通过高速水幕对液态钢渣进行粒化处理的设备。
1
GB/T29514—2013
4热阀工艺技术
4.1原理
将热态钢渣倒入热闷罐内,利用喷人水产生的蒸汽在罐内进行钢渣裂解,使钢渣自解粉化、渣铁分离。 4.2流程
工艺流程见图1。
加盖
蒸汽回收或有组织排放
热问罐
钢渣
出渣
(回流水)
喷水
集水池
沉淀池
循环水泵组
图1热闷流程示意图
4.3热闷装置 4.3.1一般要求
热闷装置应符合设计图纸要求。 4.3.2热闷盖 4.3.2.1热闷盖由盖体、底座、喷淋管路、锁紧装置等组成。 4.3.2.2 热闷盖盖体材质应考虑环境温度、腐蚀、压力影响。 4.3.2.3 热闷盖和热闷罐之间应设置密封装置,保证热闷过程的密封性良好。 4.3.2.4 热闷盖应设计安装有安全防爆装置及保护装置,在热闷罐内压力超过设定值时及时泄爆,保证安全。 4.3.3热闷罐 4.3.3.1 热闷罐罐体材料应耐高温、耐压、耐腐蚀。 4.3.3.2 热闷罐混凝土部分的设计应符合GB50010的规定。 4.3.3.3 热闷罐底部应设计回水装置,使回水及时排出。 4.3.3.4 热闷罐应具备良好的隔热保温性能。 4.3.4循环供水系统 4.3.4.1 循环水系统由泵站、沉淀池、集水池和供水管路组成。 2
GB/T29514—2013
4.3.4.2水系统应设计为全循环系统,供水压力要保证喷水压力的要求。 4.3.4.3泵站设计应符合本标准规定,同时应符合GB/T50265的规定。 4.3.4.4供水泵选型要适合介质温度、水质特点、启动迅速的要求。 4.3.4.5供水管路设计应符合GB50316的规定。 4.3.5 蒸汽排放 4.3.5.1热闷罐产生的蒸汽应回收利用或有组织排放。 4.3.5.2蒸汽管路应按GB/T20801进行设计。 4.3.6检测和控制系统 4.3.6.1蒸汽管路应设温度和压力检测装置。 4.3.6.2水管路应设压力、流量检测装置。 4.3.6.3集水池应设液位检测装置。 4.3.6.4热区域电缆应采用阻燃或耐高温电缆。
5滚筒工艺技术
5.1原理
高温熔渣在一个回转的滚筒中,通过多种介质的共同冷却和机械力协同作用将钢渣急速冷却和碎化。 5.2流程
滚筒工艺流程见图2。
蒸汽回收或有组织排放
扒渣等辅助倒渣
熔渣
滚筒
钢渣
出渣
回流水
循环水泵组
集水池
沉淀池
图2 滚筒流程示意图
5.3滚筒装置 5.3.1一般要求
滚筒装置应符合设计图纸要求。
3
GB/T29514—2013
5.3.2受渣漏斗 5.3.2.1漏斗为钢结构,应设有内衬。 5.3.2.2漏斗应单独进行支撑,设有操作平台,并符合安全标准。 5.3.3滚筒本体
滚筒本体为钢结构,与渣相接触的衬板、钢球及其他零件应耐磨及耐急冷急热;应采用具有防松功能的螺栓连接副。 5.3.4传动装置
滚简的传动装置应设有防尘罩并考虑易更换。 5.3.5滚筒支撑装置
滚筒支撑装置应考虑可调整、易更换、易润滑及防尘。 5.3.6喷水装置
喷水装置由喷嘴和管道等组成,喷嘴的角度应可调。
6风碎工艺技术
6.1原理
液态钢渣在高速气流的剪切作用下,分散成的细小颗粒,颗粒渣随即落入水池中快速冷却,得到风碎渣。 6.2流程
风碎工艺流程见图3。
蒸汽回收或有组织排放
翻渣入中间包
钢渣
锅渣渣口
渣池
出渣
压缩空气
粒化器
补充水
图3风碎流程示意图
6.3风碎设备 6.3.1一般要求
风碎设备应符合设计图纸要求。 6.3.2风碎设备主要由中间包、渣口、粒化器、水池等组成。 6.3.3中间包材质一般为铸钢。
4
GB/T29514—2013
6.3.4渣口横截面一般采用U型,材质一般为普碳钢,可为焊接件或铸造件,其流出端一般比粒化器出口端长10cm以上。 6.3.5水池应耐冲刷、耐腐蚀,用于收集风碎渣。 6.3.6粒化器为风碎工艺的核心设备。材质一般为普碳钢,也可用不锈钢,中间孔与侧孔呈H型分布,也可皇U型分布。压缩空气压力和流量视液态渣的流动性进行调节。视场地落渣区域的长短,粒化器的仰角可做调整。
7水淬工艺技术
7.1原理
液态钢渣由中间包均匀流入粒化器形成的高速水幕,钢渣在高速水幕的急冷、剪切作用和水池壁的撞击下,淬成细小颗粒,使钢渣粒化。 7.2流程
水淬工艺流程见图4。
循环水泵组
沉淀池
事故水
(回流水)
粒化器
水淬池
出渣
中间包
燕汽回收或有组织排放
钢渣
图4水淬流程示意图
7.3水淬设备 7.3.1 一般要求
水淬设备应符合设计图纸要求。 7.3.2水粒化器
水淬粒化器是用于将钢渣粒化的设备,主要由粒化器本体和喷嘴组成,粒化器材质一般为普通碳素结构钢,喷嘴材质一般为碳钢或不锈钢。 7.3.3倾翻装置
用于中间包的倾翻,使中间包内的液态钢渣呈瀑布状流出。 7.3.4中间包
包壳材质一般为铸钢,内衬为耐火材料。
5
GB/T29514—2013
7.3.5水淬池
水淬池应耐冲刷、耐腐蚀,用于收集水淬渣和水。 7.3.6供水设备
供水应满足使用要求,可设置事故用水。粒化器前的供水管路应设流量、压力测量仪表。
8环境保护
8.1 钢渣处理用水应循环使用。 8.2噪声控制应符合GB12348的规定。 8.3钢渣处理过程中的粉尘排放应符合国家、地方有关规定。
9.操作、维护与安全
9.1一般要求 9.1.1吊运盛有液态渣的渣罐或渣盆,应使用铸造起重机。 9.1.2液态渣罐周围的平台梁柱、起重机梁、厂房柱及其他建筑物应考虑辐射热的影响。 9.1.3包括厂房等内容的工程设计应符合GB50016、GB50046、AQ2001有关规定, 9.1.4钢渣处理生产管理应符合AQ2001有关规定。 9.2热工艺技术 9.2.1倒渣前应确认热闷罐底无积水,并确保底部有一定厚度的干渣。 9.2.2倒渣前应对吊具、斗具等进行详细安全检查和试吊确认,安全保护装置处于完好状态。 9.2.3吊运、倒渣过程中,相应作业区周围禁止人员停留,操作人员应处于安全位置。不应在翻渣作业之前先挂上倾翻渣罐或渣盆的小钩。 9.2.4定期检查热闷盖泄爆装置是否正常,保证热闷过程的安全。 9.2.5热闷罐蒸汽、回水通道要保持通畅。 9.2.6保持热闷车间地面无积水。 9.2.7出渣中应避免出现红渣。 9.3滚筒工艺技术 9.3.1钢渣应按设计要求均匀倒出,发现滚筒出红渣或滚筒内有响爆声音时,暂停进渣或减少进渣量并增加水量。 9.3.2倒渣时发现钢水,应立即停止倒渣。 9.3.3操作人员应在安全作业区内进行操作。 9.3.4倒渣结束后,滚筒应继续喷水10min~15min。 9.3.5当滚筒设备周围积渣时,需及时清理。 9.3.6当滚筒内钢球量低于设计要求时,需及时补加钢球。 9.4风碎工艺技术 9.4.1在钢渣处理附近应设置专门的观测点,对渣罐倒出的钢渣流动性进行观测。一般要求在渣罐倾倒钢渣时能呈束状流下,未发现凝固态钢渣,即可进行风碎处理。
6