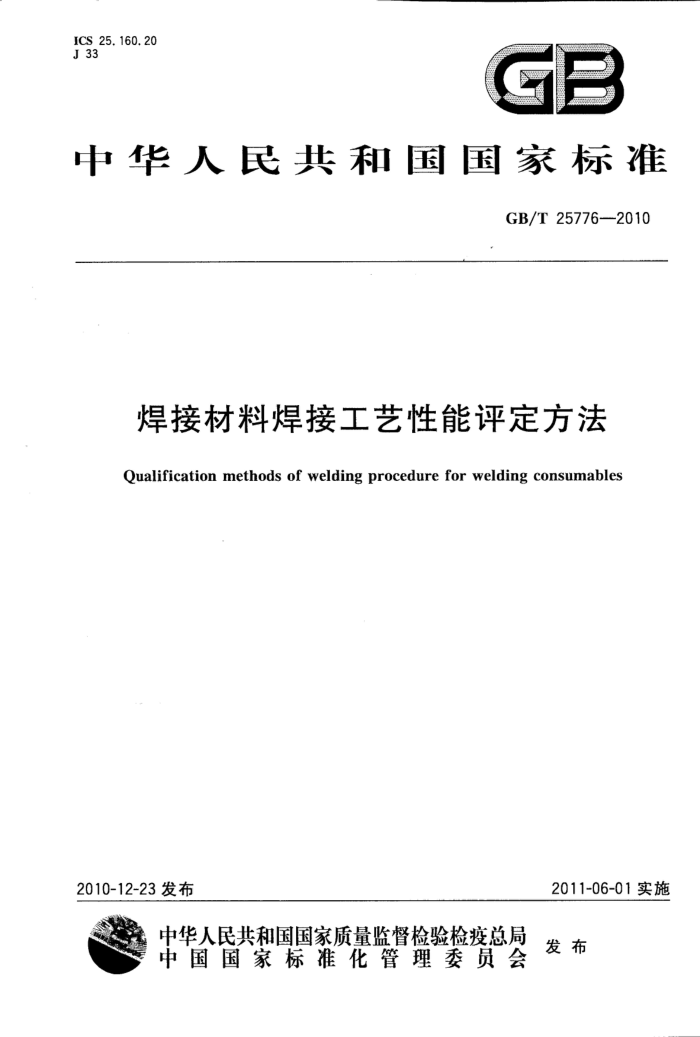
ICS25.160.20 J33
GB
中华人民共和国国家标准
GB/T257762010
焊接材料焊接工艺性能评定方法
Qualification methods of welding procedure for welding consumables
2011-06-01实施
2010-12-23发布
中华人民共和国国家质量监督检验检疫总局
中国国家标准化管理委员会 发布
GB/T 25776-2010
目 次
前言 1 范围 2术语和定义 3评定方法 3.1一般原则 3.2电焊条评定方法 3.3其他焊接材料评定方法
I
评定记录
4
GB/T 25776—2010
前 言
本标准由全国焊接标准化技术委员会(SAC/TC55)提出并归口。 本标准起草单位:哈尔滨焊接研究所、常州华通焊丝有限公司、四川大西洋焊接材料股份有限公司、
天津市金桥焊材集团有限公司、北京金威焊材有限公司、建德市新安江电焊条厂。
本标准起草人:储继君、李振华、李春范、陈义岗、侯永泰、崔晓东、洪韬。
I
GB/T25776—2010
焊接材料焊接工艺性能评定方法
1范围
本标准规定了焊接材料的电弧稳定性、脱渣性、再引弧性能、飞溅率、熔化系数、熔敷效率及焊接发尘量等焊接工艺性能的评定方法
本标准适用于焊条电弧焊、熔化极气体保护电弧焊、药芯焊丝电弧焊等焊接用钢、镍及镍合金、铜及铜合金、铝及铝合金等焊接材料的焊接工艺性能评定。 2术语和定义
下列术语和定义通 CHIN
本标准
2. 1
交流电弧稳定性 AC arc stability 采用交流焊接电源施焊时,电弧保持稳定燃烧的程度脱渣性 detanability 渣壳从焊缝 脱落的难易程度
2. 2
2.3
再引弧性能 Prei eignition capability 焊接一段时间停弧后,重新引燃电弧的能力
2. 4
S spatter oss rate
飞溅率
飞溅损失的量写熔化的焊丝(或焊条)量的百分比
A
2.5
熔化系数 melting fficien
C
熔焊过程中,单位电流单位时间内,焊芯(或焊丝)的熔化量[g/(
.h)
LS
2.6
熔敷效率deposition efficiency 熔敷金属量与熔化的填充金属(焊芯或焊丝)量的百分比
2.7
焊接发尘量totalamountofweldfumes 焊接时,单位质量的焊接材料(焊条或焊丝)所产生的烟尘量Lg/kg]。
3评定方法 3.1一般原则
在评定中如无特殊要求,焊接电流采用制造厂推荐的最大电流的90%,交直流两用的焊接材料采用交流施焊,焊接电压和烘干等规范采用制造厂推荐规范。除镍、铜、铝采用相应的试板外,其他焊接材料采用与其熔敷金属化学成分相当的试板或碳含量不超过0.2%的碳锰焊接结构钢,试板的表面应经打磨或机械加工,以去除油污、氧化皮等。
GB/T25776—2010
电弧稳定性、熔化系数、熔敷效率等项目也可采用相应仪器进行评定。 3.2电焊条评定方法 3.2.1交流电弧稳定性
试验应采用交流焊接电源,在尺寸为400mm×100mm×(12~20)mm的试板上施焊一条焊道,焊条的剩余长度约为50mm。在施焊过程中,观察灭弧、喘息次数。每种焊条测定三根,取其算术平均值。 3.2.2脱渣性
试验在单块尺寸为400mm×100mm×(14~16)mm的两块试板对接坡口内焊接,焊前点焊固定试板,直径不大于$5.0mm的焊条坡口角度为70°士1°,直径大于$5.0mm的焊条坡口角度为90°士1°,钝边为1mm~3mm,不留根部间隙。
焊接时采用单道焊,焊条不摆动,焊道长度和熔化焊条长度比值约为1:1.3,焊条的剩余长度约 50mm。试板焊接后,立即将焊道朝下水平置于锤击平台上,保证落球锤击在试板中心位置。将质量为 2kg的铁球置于1.3m高的支架上。焊后1min,使铁球从固定的落点,以初速度为零的自由落体状态锤击试板中心。
酸性焊条连续锤击三次,碱性焊条连续锤击五次,按公式(1)计算脱渣率。每种焊条测定两次,取其算术平均值。
l-l ×100%
D=
(1)
式中: D脱渣率; lo 焊道总长度,单位为毫米(mm); 1—未脱渣总长度,单位为毫米(mm)。 其中,未脱渣总长度I按公式(2)计算。
1=l+12+0.2×13
(2 )
式中: l——未脱渣总长度,单位为毫米(mm);未脱渣长度",单位为毫米(mm); l2-严重粘渣长度2,单位为毫米(mm); ls-—轻微粘渣长度3,单位为毫米(mm)。
3.2.3再引弧性能
试验前,准备尺寸为400mm×100mm×(1220)mm的施焊试板和尺寸为200mm×100mm× (12~20)mm的再引弧试板,再引弧试板必须无氧化皮和锈蚀,平整光洁与导线接触良好。
焊条在施焊板上焊接15s停弧,停弧至规定的“间隔”时间后,在再引弧板上进行再引弧。再引弧时以焊条熔化端与钢板垂直接触,不做敲击动作,不得破坏焊条套筒。
同“间隔”时间用三根焊条分别进行,每次再引弧前均须焊接15s。三根焊条中有两根以上出现电弧闪光或短路状态即判定为通过,另换一组焊条进行下二“间隔”时间的判定。
酸性焊条“间隔”时间从5s起,碱性焊条从1s起。 3.2.4飞溅率
将尺寸为300mm×50mm×20mm的试板立放在厚度大于3mm的紫铜板上,在紫铜板上放置 1)未脱渣—渣完全未脱,呈焊后原始状态。 2)严重粘渣一一渣表面脱落,仍有薄渣层,不露焊道金属表面。 3)轻微粘渣- 一焊道侧面有粘渣,焊道部分露出焊道金属或渣表面脱落,断续地露出焊道金属。
2
GB/T25776—2010
一个用约1mm厚的紫铜薄板围成的高400mm的圆筒简,其周长为1500mm~2000mm,以防止飞溅物散失。
试验在圆简内进行,焊条熔化至剩余长度约50mm处灭弧。每组试验取三根焊条,分别在三块试板上施焊。焊前称量焊条质量,焊后称量焊条头和飞溅物的质量,称量精确至0.01g,按公式(3)计算飞溅率。
m m m
×100%
S:
·(3)
式中: S.飞溅率;
一飞溅物总质量,单位为克(g);
m-
mi- 焊条总质量,单位为克(g);
焊条头总质量,单位为克(g)。
m2"
3.2.5熔化系数
试板尺寸为300mm×50mm×20mm。每组试验取三根焊条,分别在三块试板上施焊,焊条剩余长度约为50mm。焊前测量焊条长度,焊接时准确记录焊接电流和焊接时间。焊后将剩余焊条去掉药皮,用细砂纸磨光,测量焊后焊芯长度,称量焊后焊芯质量,称量精确至0.1g,按公式(4)计算熔化系数。
M=m-m2
·(4)
Ixt
式中: M— 熔化系数; m1 焊前焊芯的总质量,单位为克(g); mz 焊后焊芯的总质量,单位为克(g);
焊接电流,单位为安培(A);焊接时间,单位为小时(h)。
I-
-
其中,焊前焊芯的总质量㎡1按公式(5)计算。
loXm2
m :
·( 5)
1
式中: mi" 焊前焊芯的总质量,单位为克(g); l。—焊条总长度,单位为毫米(mm); m2—焊后焊芯的总质量,单位为克(g); 1—焊后焊芯总长度,单位为毫米(mm)。
3.2.6熔数效率
每组试验取三根焊条,分别在尺寸为300mm×50mmX×20mm的三块试板上施焊,焊条剩余长度约50mm。焊前测量焊条长度和称量试板质量,焊后再称量试板质量,称量精确至0.1g。焊后将剩余焊条去掉药皮,用细砂纸磨光,测量焊后焊芯长度和称量质量,称量精确至0.1g。按公式(6)计算熔敷效率。
E=m × 100%
·(6)
m2
式中: E-熔敷效率; mi 焊条熔敷金属总质量,单位为克(g); m2" 熔化焊芯的总质量,单位为克(g)。 其中,焊条熔敷金属总质量m1按公式(7)计算。
3
GB/T 257762010
3.2.7.3将试板及焊条放在筒体内,然后将一张滤纸放在小锥体开口处的铜网下面并紧固大小锥体。 接通冷却水,开动真空泵,打开二通活塞,抽气量调节到5m/h,观察U型水压计的水压差是否正常,筒体内应为负压,然后进行施焊。焊接时,焊条应尽量垂直不摆动,两个焊道相距10mm以上,焊条剩余长度约50mm。停焊后继续抽气5min,关闭二通活塞,打开小锥体取下集尘滤纸折叠后单独放在小纸袋中保存。用称过质量的少量脱脂棉擦净小锥体内壁的尘,将带尘的棉花放回原处。 3.2.7.4重复上述操作,焊完三根焊条后打开大小锥体帽,用剩余的脱脂棉擦净大筒体和大小锥体内壁上的尘,将带尘的棉花放回原处。为了避免混入飞溅颗粒,大筒体下部180,mm处以下不擦。 3.2.7.5将带尘脱脂棉及滤纸一同放入干燥皿中,干燥时间与称量原始质量前的干燥时间相同,然后进行第二次称重,并称量三根焊条头的总质量。按公式(9)计算焊接发尘量。
F= g1+A2 × 1 0
·(9)
△g3
式中: F 焊接发尘量; Ag1- 三张滤纸集尘前后质量差,单位为克(g); △g2- 棉花集尘前后质量差,单位为克(g); △g3 三根焊条焊接前后质量差,单位为克(g)。 3.3其他焊接材料评定方法
其他焊接材料焊接工艺性能的评定,可参照上述电焊条焊接工艺性能的评定方法进行。 评定记录
7
评定记录应包括以下内容: a)试板和焊接材料
试板材料;试板尺寸;焊接材料型号、牌号;焊接材料的批号或炉号;焊接材料尺寸;焊接材料的烘干规范(如需要)。
b)采用的焊接条件
焊接方法;一焊接电源;电流类型和极性;一焊接电流(送丝速度)、焊接电压和焊接速度;一电源空载电压(如需要);千伸长;保护气类型和流量。
-
c)与本标准规定不一致的情况。 d)试验结果
原始数据;测试结果。
ICS25.160.20 J33
GB
中华人民共和国国家标准
GB/T257762010
焊接材料焊接工艺性能评定方法
Qualification methods of welding procedure for welding consumables
2011-06-01实施
2010-12-23发布
中华人民共和国国家质量监督检验检疫总局
中国国家标准化管理委员会 发布
GB/T 25776-2010
目 次
前言 1 范围 2术语和定义 3评定方法 3.1一般原则 3.2电焊条评定方法 3.3其他焊接材料评定方法
I
评定记录
4
GB/T 25776—2010
前 言
本标准由全国焊接标准化技术委员会(SAC/TC55)提出并归口。 本标准起草单位:哈尔滨焊接研究所、常州华通焊丝有限公司、四川大西洋焊接材料股份有限公司、
天津市金桥焊材集团有限公司、北京金威焊材有限公司、建德市新安江电焊条厂。
本标准起草人:储继君、李振华、李春范、陈义岗、侯永泰、崔晓东、洪韬。
I
GB/T25776—2010
焊接材料焊接工艺性能评定方法
1范围
本标准规定了焊接材料的电弧稳定性、脱渣性、再引弧性能、飞溅率、熔化系数、熔敷效率及焊接发尘量等焊接工艺性能的评定方法
本标准适用于焊条电弧焊、熔化极气体保护电弧焊、药芯焊丝电弧焊等焊接用钢、镍及镍合金、铜及铜合金、铝及铝合金等焊接材料的焊接工艺性能评定。 2术语和定义
下列术语和定义通 CHIN
本标准
2. 1
交流电弧稳定性 AC arc stability 采用交流焊接电源施焊时,电弧保持稳定燃烧的程度脱渣性 detanability 渣壳从焊缝 脱落的难易程度
2. 2
2.3
再引弧性能 Prei eignition capability 焊接一段时间停弧后,重新引燃电弧的能力
2. 4
S spatter oss rate
飞溅率
飞溅损失的量写熔化的焊丝(或焊条)量的百分比
A
2.5
熔化系数 melting fficien
C
熔焊过程中,单位电流单位时间内,焊芯(或焊丝)的熔化量[g/(
.h)
LS
2.6
熔敷效率deposition efficiency 熔敷金属量与熔化的填充金属(焊芯或焊丝)量的百分比
2.7
焊接发尘量totalamountofweldfumes 焊接时,单位质量的焊接材料(焊条或焊丝)所产生的烟尘量Lg/kg]。
3评定方法 3.1一般原则
在评定中如无特殊要求,焊接电流采用制造厂推荐的最大电流的90%,交直流两用的焊接材料采用交流施焊,焊接电压和烘干等规范采用制造厂推荐规范。除镍、铜、铝采用相应的试板外,其他焊接材料采用与其熔敷金属化学成分相当的试板或碳含量不超过0.2%的碳锰焊接结构钢,试板的表面应经打磨或机械加工,以去除油污、氧化皮等。
GB/T25776—2010
电弧稳定性、熔化系数、熔敷效率等项目也可采用相应仪器进行评定。 3.2电焊条评定方法 3.2.1交流电弧稳定性
试验应采用交流焊接电源,在尺寸为400mm×100mm×(12~20)mm的试板上施焊一条焊道,焊条的剩余长度约为50mm。在施焊过程中,观察灭弧、喘息次数。每种焊条测定三根,取其算术平均值。 3.2.2脱渣性
试验在单块尺寸为400mm×100mm×(14~16)mm的两块试板对接坡口内焊接,焊前点焊固定试板,直径不大于$5.0mm的焊条坡口角度为70°士1°,直径大于$5.0mm的焊条坡口角度为90°士1°,钝边为1mm~3mm,不留根部间隙。
焊接时采用单道焊,焊条不摆动,焊道长度和熔化焊条长度比值约为1:1.3,焊条的剩余长度约 50mm。试板焊接后,立即将焊道朝下水平置于锤击平台上,保证落球锤击在试板中心位置。将质量为 2kg的铁球置于1.3m高的支架上。焊后1min,使铁球从固定的落点,以初速度为零的自由落体状态锤击试板中心。
酸性焊条连续锤击三次,碱性焊条连续锤击五次,按公式(1)计算脱渣率。每种焊条测定两次,取其算术平均值。
l-l ×100%
D=
(1)
式中: D脱渣率; lo 焊道总长度,单位为毫米(mm); 1—未脱渣总长度,单位为毫米(mm)。 其中,未脱渣总长度I按公式(2)计算。
1=l+12+0.2×13
(2 )
式中: l——未脱渣总长度,单位为毫米(mm);未脱渣长度",单位为毫米(mm); l2-严重粘渣长度2,单位为毫米(mm); ls-—轻微粘渣长度3,单位为毫米(mm)。
3.2.3再引弧性能
试验前,准备尺寸为400mm×100mm×(1220)mm的施焊试板和尺寸为200mm×100mm× (12~20)mm的再引弧试板,再引弧试板必须无氧化皮和锈蚀,平整光洁与导线接触良好。
焊条在施焊板上焊接15s停弧,停弧至规定的“间隔”时间后,在再引弧板上进行再引弧。再引弧时以焊条熔化端与钢板垂直接触,不做敲击动作,不得破坏焊条套筒。
同“间隔”时间用三根焊条分别进行,每次再引弧前均须焊接15s。三根焊条中有两根以上出现电弧闪光或短路状态即判定为通过,另换一组焊条进行下二“间隔”时间的判定。
酸性焊条“间隔”时间从5s起,碱性焊条从1s起。 3.2.4飞溅率
将尺寸为300mm×50mm×20mm的试板立放在厚度大于3mm的紫铜板上,在紫铜板上放置 1)未脱渣—渣完全未脱,呈焊后原始状态。 2)严重粘渣一一渣表面脱落,仍有薄渣层,不露焊道金属表面。 3)轻微粘渣- 一焊道侧面有粘渣,焊道部分露出焊道金属或渣表面脱落,断续地露出焊道金属。
2
GB/T25776—2010
一个用约1mm厚的紫铜薄板围成的高400mm的圆筒简,其周长为1500mm~2000mm,以防止飞溅物散失。
试验在圆简内进行,焊条熔化至剩余长度约50mm处灭弧。每组试验取三根焊条,分别在三块试板上施焊。焊前称量焊条质量,焊后称量焊条头和飞溅物的质量,称量精确至0.01g,按公式(3)计算飞溅率。
m m m
×100%
S:
·(3)
式中: S.飞溅率;
一飞溅物总质量,单位为克(g);
m-
mi- 焊条总质量,单位为克(g);
焊条头总质量,单位为克(g)。
m2"
3.2.5熔化系数
试板尺寸为300mm×50mm×20mm。每组试验取三根焊条,分别在三块试板上施焊,焊条剩余长度约为50mm。焊前测量焊条长度,焊接时准确记录焊接电流和焊接时间。焊后将剩余焊条去掉药皮,用细砂纸磨光,测量焊后焊芯长度,称量焊后焊芯质量,称量精确至0.1g,按公式(4)计算熔化系数。
M=m-m2
·(4)
Ixt
式中: M— 熔化系数; m1 焊前焊芯的总质量,单位为克(g); mz 焊后焊芯的总质量,单位为克(g);
焊接电流,单位为安培(A);焊接时间,单位为小时(h)。
I-
-
其中,焊前焊芯的总质量㎡1按公式(5)计算。
loXm2
m :
·( 5)
1
式中: mi" 焊前焊芯的总质量,单位为克(g); l。—焊条总长度,单位为毫米(mm); m2—焊后焊芯的总质量,单位为克(g); 1—焊后焊芯总长度,单位为毫米(mm)。
3.2.6熔数效率
每组试验取三根焊条,分别在尺寸为300mm×50mmX×20mm的三块试板上施焊,焊条剩余长度约50mm。焊前测量焊条长度和称量试板质量,焊后再称量试板质量,称量精确至0.1g。焊后将剩余焊条去掉药皮,用细砂纸磨光,测量焊后焊芯长度和称量质量,称量精确至0.1g。按公式(6)计算熔敷效率。
E=m × 100%
·(6)
m2
式中: E-熔敷效率; mi 焊条熔敷金属总质量,单位为克(g); m2" 熔化焊芯的总质量,单位为克(g)。 其中,焊条熔敷金属总质量m1按公式(7)计算。
3
GB/T 257762010
3.2.7.3将试板及焊条放在筒体内,然后将一张滤纸放在小锥体开口处的铜网下面并紧固大小锥体。 接通冷却水,开动真空泵,打开二通活塞,抽气量调节到5m/h,观察U型水压计的水压差是否正常,筒体内应为负压,然后进行施焊。焊接时,焊条应尽量垂直不摆动,两个焊道相距10mm以上,焊条剩余长度约50mm。停焊后继续抽气5min,关闭二通活塞,打开小锥体取下集尘滤纸折叠后单独放在小纸袋中保存。用称过质量的少量脱脂棉擦净小锥体内壁的尘,将带尘的棉花放回原处。 3.2.7.4重复上述操作,焊完三根焊条后打开大小锥体帽,用剩余的脱脂棉擦净大筒体和大小锥体内壁上的尘,将带尘的棉花放回原处。为了避免混入飞溅颗粒,大筒体下部180,mm处以下不擦。 3.2.7.5将带尘脱脂棉及滤纸一同放入干燥皿中,干燥时间与称量原始质量前的干燥时间相同,然后进行第二次称重,并称量三根焊条头的总质量。按公式(9)计算焊接发尘量。
F= g1+A2 × 1 0
·(9)
△g3
式中: F 焊接发尘量; Ag1- 三张滤纸集尘前后质量差,单位为克(g); △g2- 棉花集尘前后质量差,单位为克(g); △g3 三根焊条焊接前后质量差,单位为克(g)。 3.3其他焊接材料评定方法
其他焊接材料焊接工艺性能的评定,可参照上述电焊条焊接工艺性能的评定方法进行。 评定记录
7
评定记录应包括以下内容: a)试板和焊接材料
试板材料;试板尺寸;焊接材料型号、牌号;焊接材料的批号或炉号;焊接材料尺寸;焊接材料的烘干规范(如需要)。
b)采用的焊接条件
焊接方法;一焊接电源;电流类型和极性;一焊接电流(送丝速度)、焊接电压和焊接速度;一电源空载电压(如需要);千伸长;保护气类型和流量。
-
c)与本标准规定不一致的情况。 d)试验结果
原始数据;测试结果。