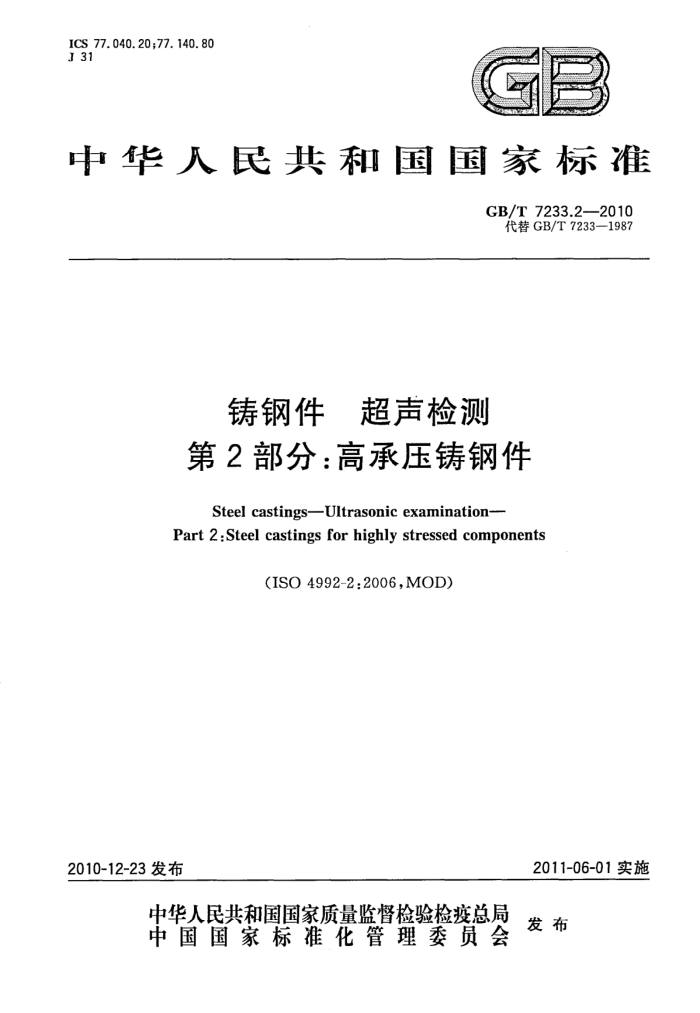
ICS 77.040.20;77.140.80 J 31
中华八民共和国国家标
GB/T7233.2—2010
代替GB/T7233—1987
铸钢件 超声检测第2部分:高承压铸钢件 Steel castings-—UItrasonic examination- Part 2 :Steel castings for highly stressed components
(ISO 4992-2:2006,MOD)
2011-06-01实施
2010-12-23发布
中华人民共和国国家质量监督检验检疫总局
中国国家标准化管理委员会 发布
GB/T7233.2—2010
目 次
前言
范围 2 规范性引用文件 3 术语和定义 4. 一般要求 4. 1 订货信息 4.2 检测范围 4. 3 允许的最大缺陷尺寸 4. 4 人员资格 4. 5 壁厚分区 4.6 质量等级 5 检测 5.1 总则 5.2 材料 5.3 设备、耦合剂、探测灵敏度和分辨力 ... 5. 4 铸钢件被检表面的准备 5.5 检测程序 .... 5.6检测报告附录A(规范性附录) 整套设备(仪器/探头组合)的探测分辨力附录B(资料性附录) 声束直径附录C(资料性附录) 缺陷的类型附录D(资料性附录) 传输修正附录E(资料性附录) 耦合传输修正的测定
1
..
..
12 13 15 21 23
GB/T7233.22010
前言
GB/T7223《铸钢件超声检测》分为两个部分:
第1部分:一般用途铸钢件; -第2部分:高承压铸钢件。
一
本部分为GB/T7233的第2部分,对应于ISO4992-2:2006《铸钢件超声检测第2部分:高承压铸钢件》。
本部分修改采用了ISO4992-2:2006,标准结构和技术内容与ISO4992-2:2006略有差异。与 ISO4992-2:2006相比,主要内容作了如下修改:
-按照汉语习惯对一些编排格式进行了修改;一将一些适用于国际标准的表述改为适用于我国标准的表述;
用小数点“”代替作为小数点的逗号“,”;
-增加了图6测量壁厚方向上缺陷的尺寸;增加了附录D传输修正; -增加了附录E耦合传输修正的测定。
本部分代替GB/T7233--1987《铸钢件超声探伤及质量评级方法》。 本部分与GB/T7233一1987相比,主要技术内容变化如下:
修改了标准的适用范围(见第1章);增加了订货信息(见4.1);修改了质量等级的要求(见4.3);修改了检测方法; -增加了附录A、附录B、附录C、附录D和附录E,删除了1987年版的附录A、附录B和附录C。
本部分的附录A为规范性附录,附录B、附录C、附录D和附录E为资料性附录。 本部分由全国铸造标准化技术委员会(SAC/TC54)提出并归口。 本部分主要起草单位:沈阳铸造研究所、沈阳北方重工集团公司、沈阳鼓风机集团公司。 本部分主要起草人:张钊赛、孙春贵、王立华、李冷西、齐兴、李兴捷。 本部分所代替标准的历次版本发布情况为:
GB/T7233—1987。
II
GB/T7233.2—2010
铸钢件超声检测第2部分:高承压铸钢件
1范围
GB/T7233的本部分规定了高承压铸钢件(非奥氏体)超声波检测的术语和定义、一般要求和应用脉冲反射技术检测内部缺陷的方法。
本部分适用于高承压铸钢件(非奥氏体)细化晶粒热处理后且厚度不超过600mm铸钢件的超声检测。对于厚度大于600mm的铸钢件,应有协议规定检测方法和记录限值。
本部分不适用于奥氏体钢。 2规范性引用文件
下列文件中的条款通过GB/T7233的本部分的引用而成为本部分的条款。凡是标注日期的引用文件,其随后所有的修改单(不包括勘误的内容)或修订版均不适用于本部分,然而,鼓励根据本部分达成协议的各方研究是否可使用这些文件的最新版本。凡是不注日期的引用文件,其最新版本适用于本部分。
GB/T5616 无损检测应用导则 GB/T9445无损检测人员资格鉴定与认证(GB/T9445—2008,ISO9712:2005,IDT) GB/T12604.1无损检测术语超声检测(GB/T12604.1-2005,ISO5577:2000,IDT) GB/T15056铸造表面粗糙度评定方法 GB/T18694 无损检测超声检验探头及其声场的表征(GB/T18694—2002,eqvISO10375:
1997)
GB/T19799.1 无损检测 超声检测1号校准试块(GB/T19799.1—2005,ISO2400:1972, IDT)
GB/T19799.2 无损检测超声检测2号校准试块(GB/T19799.2—2005,ISO7963:1985, IDT)
JB/T9214 A型脉冲反射式超声探伤系统工作性能测试方法(JB/T9214一1999,neq JISZ2344—1993)
JB/T10061 1A型脉冲反射式超声波探伤仪通用技术条件(JB/T10061一1999,ncqASTM E 750-1980) 3术语和定义
GB/T12604.1确立的以及下列术语和定义适用于本部分。
3. 1
参考缺陷回波尺寸referencediscontinuityechosize 超声检测通常用平底孔直径来表示可接受的最小缺陷尺寸。
3.2
点状缺陷pointdiscontinuity 缺陷的尺寸小于或者等于声束直径。 注:尺寸指长、宽和壁厚方向上的尺寸。
GB/T7233.2—2010
3.3
延伸性缺陷complexdiscontinuity 缺陷的尺寸大于声束直径。 注:尺寸指长、宽和壁厚方向上的尺寸。
3. 4
平面型缺陷 planar discontinuity 能测量二维缺陷的尺寸。
3.5
体积型缺陷 volumetricdiscontinuity 能测量三维缺陷的尺寸。
3.6
特殊的外层 specialrimzone 有特殊要求的外层区域。 注:特殊要求,比如机加工、高压和密封的表面等。
3.7
补焊finishingwelding 通过焊接以获得与铸钢件同样的质量。
4一般要求
4.1订货信息
订货时需方应提供下列信息:
一超声检测的铸钢件区域、数量或百分数;铸钢件各部位的质量等级; -检测工艺要求;是否有其他检测要求,见5.5.1。
4.2检测范围
应采用最适宜的检测方法,检测铸钢件的全部被检区域(铸钢件的形状适合检测时)。 对于厚度大于600mm的铸钢件,其检测方法、记录限值、验收等级等由供需双方商定。
4.3允许的最大缺陷尺寸 4.3.1总则
需方应根据质量等级要求,确定铸钢件不同区域的体积型和平面型缺陷的验收等级。 4.3.2不能测量尺寸的缺陷(点状缺陷)
在特殊外层和准备焊接区,不能测量尺寸的缺陷不应超过表1的限值。 4.3.3能测量尺寸的缺陷(延伸性缺陷) 4.3.3.1平面型缺陷
平面型缺陷的尺寸不应超过图2的限值。 对能测量长度而不能测量壁厚方向上尺寸的缺陷面积,应按图2的公式计算。 随着声程距离的增加,声束直径变大,不宜按照图2测量小平面型缺陷的尺寸。通常在30mm的
外层测量这些尺寸,应使用聚焦探头,如双晶探头。 4.3.3.2体积型缺陷
体积型缺陷尺寸,外层不能超过图3的限值,内层不能超过图4限值。 1级不充许有能测量尺寸的缺陷。 能测量长度但不能测量宽度的缺陷面积,应按图3和图4的公式计算。
2
GB/T7233.2—2010
4.4人员资格
超声检测人员应依据GB/T9445的要求,取得相应资格证书。
4.5壁厚分区
壁厚分区见图1,这些区域按铸钢件最终使用尺寸划分。 4.6质量等级
需方在铸钢件不同区域要求的质量等级不同,应清楚地在图纸上注明:
准确的区域及尺寸;准备焊接区域和特殊外层厚度,
-
1级仅适用于准备焊接区和特殊的外层。除非订货时另有约定,否则补焊区同母材一样验收。 5检测
5.1总则
GB/T5616给出超声检测的基本规则。 5.2材料
材料的超声可探性,可通过比较参考反射体回波高度(通常是一次底波)和噪声信号来评价。评价应选择铸钢件具有代表性的区域,该区域必须是上下面平行的最终表面和最大厚度。
依据表2的参考回波高度,至少高出噪声信号6dB。 如果在检测的最大厚度探测到的最小平底孔或相当的横孔直径回波高度不大于噪声信号6dB,超
声可探性下降。在小于6dB的信噪比下,探测到的平底孔或横孔直径应在检测报告中说明,并经供需双方同意。
注:为确定适当的平底孔尺寸,可以采用距离增益尺寸法(DGS)或者使用具有相同的金属材料、热处理状态和壁厚
的平底孔试块,试块平底孔直径依据表2或相当的横孔直径。 用于平底孔和横孔的直径转换见公式(1):
4.935XDrBH Do-
.(1)
>2×s
式中: D—横孔直径,单位为毫米(mm); DEBH- 平底孔直径,单位为毫米(mm);
入--波长,单位为毫米(mm); s—声程,单位为毫米(mm)。 公式(1)仅适用于D≥2入、s≥5倍近场长度、单晶探头。
5.3设备、耦合剂、探测灵敏度和分辨力 5.3.1超声仪器
超声仪器应满足JB/T10061的要求,并具备下列特性:
范围调整,钢中纵波和横波,至少在10mm和2000mm内可连续选择; -增益,调整范围在80dB以上,步进级每档不大于2dB,精度1dB;一时基线性误差不大于1%,垂直线性误差不大于5%;一至少能适应1MHz~6MHz频率脉冲反射技术所用的单晶和双晶探头。
5.3.2探头和频率
探头和频率应符合GB/T18694的要求,并满足下列规定:
额定频率范围在1MHz~6MHz之间;斜探头角度范围在35°~70°之间。
注:在高承压铸钢件检测中,应依据铸钢件的形状和探测的缺陷类型来选择直探头和斜探头。
3
GB/T7233.2——2010
检测近表面区,应使用双晶探头。
5.3.3校准超声检测设备
操作人员应按JB/T9214的规定,定期校准超声检测设备。 5.3.4耦合剂
耦合剂应湿润检测表面并确保声波传播,如机油、浆糊、甘油和水等,在校准和检测中应使用同一种耦合剂。
注:声波传播采用表面平行区域的一次或多次底波来校对。 5.3.5探测灵敏度和分辨力
仪器的探测灵敏度至少应满足5.5.3要求的灵敏度调整。 整套设备(仪器/探头组合)的探测分辨力应符合附录A的要求。
5.4铸钢件被检表面的准备
被检表面应能使探头达到良好的耦合效果,应无影响声波传播和探头移动的锈蚀、氧化皮、焊接飞溅或其他不规则物。
使用单晶探头时,为达到良好的耦合效果,被检表面粗糙度至少应Ra≤25μm。机加工的被检表面粗糙度应达到Ra<12.5μm。特殊的检测技术,对表面粗糙度的要求更高,例如Ra≤6.3uμm(见 GB/T15056)。 5.5检测程序 5.5.1总则
主要依据铸钢件的形状、铸造或补焊后可能产生的缺陷,来选择最佳人射方向和适合的探头。 铸钢件供方应明确所用的检测工艺规范,在特定条件下要编制书面协议。 尽可能从相对的两个方向检测,当只能从一个方向检测时,为了发现近表面缺陷应附加使用近场分
辨探头,在壁厚不到50mm时应使用双晶探头。
此外,当供需双方没有其他约定时,应使用双晶直探头和斜探头检测铸钢件下列50mm内的区域:
重要区域,如内圆角、变截面、加外冷铁处; —补焊区;
准备焊接区;涉及铸钢件重要性能的特殊外层。
深度超过50mm的补焊区,应使用其他合适的斜探头补充检测。 斜探头的角度大于60°,声程不应超过150mm。 探头的扫查应有重叠,重叠率应大于探头直径或边长15%,应有规律的扫查所有被检区域,扫查速
度应不超过150mm/s。 5.5.2范围调整
在检测仪器的荧屏上进行范围调整,使用直或斜探头,选择下列试块:
-GB/T19799.1校准试块1或者GB/T19799.2校准试块2;与被检材料有相同声学特性的校准试块;
一一用直探头在具有平行表面且厚度可测的铸钢件本体调整。
5.5.3灵敏度调整 5.5.3.1总则
范围调整(见5.5.2)后进行灵敏度调整,采用下述两种方法之一: a)距离幅度校正曲线法(DAC)
距离幅度校正曲线法是用一系列相同的反射体(平底孔FBH或横孔SDH)的回波高度得出的,每个反射体有不同的声程。
注:通常采用2MHz~2.5MHz的额率和6mm直径的平底孔。
4
GB/T7233.2—2010
b)距离增益尺寸法(DGS)
距离增益尺寸法是用一系列理论上计算出的声程、仪器增益、垂直于声束轴线的平底孔直径的关系得出的曲线。
5.5.3.2传输修正
传输修正应按照附录D确定。 当使用校准试块时,需要进行传输修正。传输修正不仅要考虑耦合面的粗糙度,也要考虑对应面的
粗糙度,因为对应面粗糙度影响底波高度,如果对应面是机加工表面或表面粗糙度Ra≤25μm,满足传输修正的测定。 5.5.3.3缺陷的探测
为了探测缺陷,应将增益一直提高到荧屏上可见噪声水平线(扫查灵敏度)。 表2给出的平底孔或相当横孔的直径,在检测的最大厚度范围内,回波高度不低于荧屏的40%。 在检测过程中,如果怀疑因缺陷引起底波衰减,超出规定的记录值(见表3),应降低检测灵敏度,准
确测定底波衰减的dB值。
斜探头灵敏度调整应使反射体在荧屏上清晰地显示典型的动态回波图形(见图6)。 推荐斜探头灵敏度调整使用自然的(非人工)平面型缺陷(裂纹尺寸在壁厚方向)或垂直于表面且远
大于声束的侧壁来校核。探头底面要尽量与铸钢件表面形状吻合。 5.5.4不同类型缺陷的评定
在铸钢件检测中发现一种或多种以下缺陷类型,应进行评定:
不是由铸钢件外形或耦合引起的底波衰减;一缺陷的回波。
底波衰减用底波高度下降的dB值表示,缺陷回波高度用平底孔或横孔直径表示。 5.5.5记录 5.5.5.1底波衰减
底波衰减超过12个dB(2MHz~2.5MHz的检测频率)应记录,底波衰减的区域应该当作缺陷区域进行标记和测量。 5.5.5.2缺陷回波
回波的记录限值应根据参考缺陷回波尺寸来确定信号波幅大小,当信号波幅超过图3、图4和表3的要求,能测量尺寸缺陷的回波应记录,应识别表4给出的缺陷类型。 为了区别缺陷类型,根据缺陷到被检表面的距离、几何形状、被检表面的最终状态,检测灵敏度可
以调整。
当使用斜探头时,不考虑缺陷回波的幅度,应记录所有具有游动特征或在壁厚方向上能测量尺寸的信号,并按5.5.7.3测定。
记录缺陷的位置,应标注在检测报告里,并附简图或照片。 5.5.6记录缺陷的验证
记录的缺陷(见5.5.5),应更准确地验证它们的类型、形状、尺寸和位置。这个验证可采用改变超声波检测技术(例如改变入射角度)或者另外采用射线照相检测技术。 5.5.7缺陷的性质和尺寸 5.5.7.1总则
对于工程应用,只有在一定条件下(如已知缺陷的类型、缺陷简单的几何形状、缺陷对声束处于最佳反射状态),才能用超声波技术比较准确测量缺陷的尺寸。
通过其他声束方向和入射角度可以验证缺陷的性质,简单地将缺陷按下列分类:
不能测量尺寸的缺陷(点状缺陷);
5