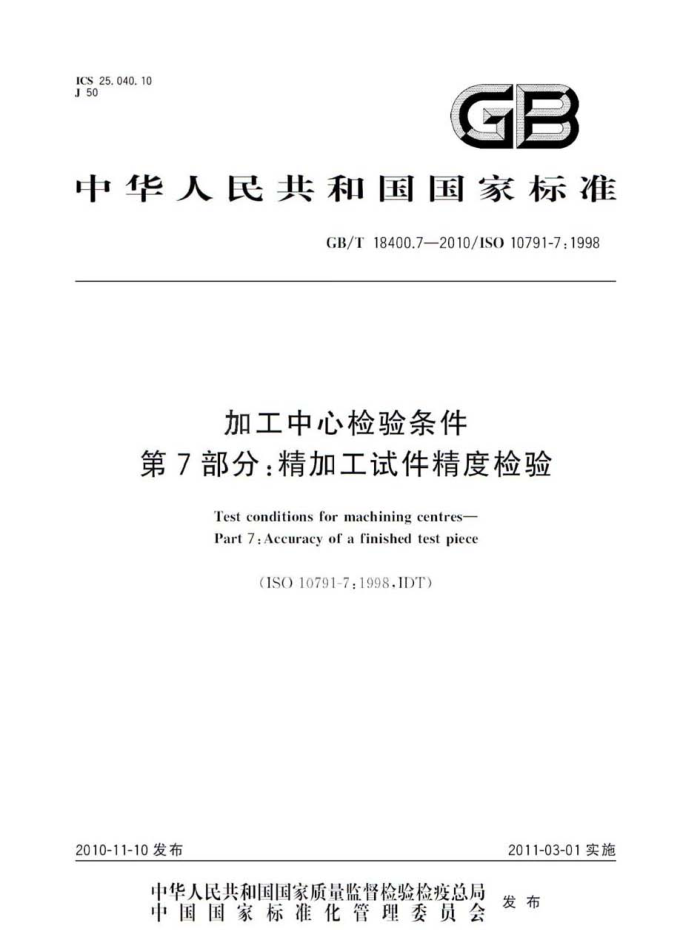
ICS25.040.10 J50
GB
中华人民共和国国家标准
GB/T18400.72010/IS010791-7:1998
加工中心检验条件
第7部分:精加工试件精度检验
Test conditions for machining centres- Part 7:Accuracy of a finished test piece
(ISO10791-7:1998.IDT)
2011-03-01实施
2010-11-10发布
中华人民共和国国家质量监督检验检疫总局
中国国家标准化管理委员会 发布
GB/T18400.7—2010/1S010791-7:1998
前言
GB/T18400加工中心检验条件分为以下十个部分:
第1部分:卧式和带附加主轴头机床儿何精度检验(水平乙轴):第2部分:立式或带垂直主回转轴的万能主轴头机床儿何精度检验(垂直Z轴);第3部分:带水平主回转轴的整体万能主轴头机床儿何精度检验(垂直Z轴):第4部分:线性和回转轴线的定位精度和重复定位精度检验;第5部分:工件夹持托板的定位精度和重复定位精度检验:第6部分:进给量、速度和插补精度检验:
-
-
第7部分:精加工试件精度检验;
第8部分:三个坐标平面上轮廊特性的评定:第9部分:刀具转换和托板转换动作时间的评定:第10部分:热效应的评定
-
本部分为GB/T18400的第7部分。 本部分等同采用IS010791-7:1998加工中心检验条件 第7部分:精加工试件精度检验(英
文版)。
考虑到我国国情,在采用ISO10791-7:1998时,本部分做了一些编辑性修改:
“本标准”词改为“本部分”;第3章标题“简要说明”改为“一般要求”;
一删除了1SO10791-7:1998的前言和引言,增加了国家标准的前言: —删除了ISO10791-7:1998的附录A(资料性附录)本部分由中国机械工业联合会提出。 本部分由全国金属切削机床标准化技术委员会(SAC/TC22)归口本部分起草单位:北京第一机床厂,四川长征机床集团有限公司、北京机床研究所。 本部分主要起草人:胡瑞琳、王晓慧、李祥文、张维。
I
GB/T18400.7—2010/ISO10791-7:1998
加工中心检验条件
第7部分:精加工试件精度检验
1范围
GB/T18400的本部分规定了在精加工条件下标准试件的一系列切削检验要求,以及试件本身的特征和尺寸,本部分可作为评定加工中心切前精度的基本要求,根据供方/制造厂与用户之间的协议,可以采用进行不同的更加严格的检验
2规范性引用文件
下列文件中的条款通过GB/T18400的本部分的引用而成为本部分的条款,凡是注日期的引用文件,其随后所有的修改单(不包括勘误的内容)或修订版均不适用于本部分,然而,鼓励根据本部分达成协议的各方研究是否可使用这些文件的最新版本。凡是不注日期的引用文件,其最新版本适用于本部分。
GB/T5342.1一2006可转位面铣刀第1部分:套式面铣刀(ISO6462:1983MOD GB/T17421.1一1998机床检验通则第1部分:在无负荷或精加工条件下机床的几何精度
(eqvISO230-1.1996) 3一般要求 3.1测量单位
本部分中的所有线性尺寸、偏差和相应的公差的单位为毫米(mm):角度尺寸的单位为度(),角度偏差和相应的公差用比值表示。在有些情况下为了清晰,也用微弧度(urad)或角秒(")表示。其换算关系见下式:
0.010/1000-10×10==10,urad~2
co
3.2参照标准
使用本部分时应参照GB/T17421.1-1998,尤其是精度检验前的安装、主轴和其他部件的空运转升温、检验方法、检验工具的精度。 3.3检验顺序
本部分所列出的检验项目的顺序,并不表示实际的检验颠序,为了装拆检验工具和检验方便,可按任意次序进行检验。 3.4检验项目
检验机床时,根据结构特点并不是必须检验本部分中的所有项目,为了验收目的而要求检验时,可由用户取得制造厂同意选择一些感兴趣的检验项目,但这些项目必须在机床订货时明确提出。 3.5检验工具
本部分所规定的检验工具仅为举例。可以使用相同指示量和至少具有相同精度的其他检验工具。 指示器应具有0.001mm或更高的分辨率, 4试件的型式
在本部分中提供了两种型式,且每种型式具有两种规格的试件,试件的型式,规格和标志见表1。 原则上在验收时每种试件仅应加工一件。在特殊要求的情况下,例如机床的性能统计评定,可按制
1
GB/T18400.72010/1S010791-7:1998
造厂和用户之间的协议确定加工试件的数量。
表1 试件的型式、规格和标志
型 式 A 轮廊加工试件
标志
名义规格
160 320 80 160
试件GB/T18400.7-A160 试件GB/T18400.7-A320 试件GB/T18400.7-B80 试件GB/T18400.7-B160
B 端铣试件
试件的定位试件的定位位置应根据制造厂和用户之间的协议规定,当无特殊要求时,试件应近似定位于X轴
5
线行程的中间位置,并沿Y轴线和Z轴线在适合于试件和/或夹具定位及刀具长度的位置处放置。 6 试件的固定
试件应适当安装在专用的夹具上,以达到刀具和夹具的最大稳定性,夹具和试件的安装面应平直应检查试件安装表面与夹具夹持面的平行度。应使用合适的夹持方法以便使刀具能贯穿和加工中心孔的全长。建议使用理头螺钉固定试件,以避免刀具与螺钉发生干涉。也可选用其他等效的方法。试件的总高度取决于所选用的固定方法。
试件的材料、刀具和切削参数
7
试件的材料和切削刀具及切削参数应按照制造厂与用户之间的协议选取,并应记录下来,在第9章和第10章中给出了推荐的切削参数。
试件的尺寸
8
如果轮廊加工试件被加工多次·会使外形尺寸相应减小,孔径相应增大,当试件用于验收目的时·建议选用的最终轮廊加工试件应符合本部分中规定的尺寸,以便能如实反映出机床的切削精度。
如果轮廓加工试件可被重复使用,其特征尺寸应保持在本部分所给出的特征尺寸的士10%以内,当试件再次使用时,在进行新的精切试验前,应进行一次薄层切削,以清理所有的表面。
建议在轮廓加工试件上标示出机床的型号和编号、检验日期、轴线的名称和方向,以便在机床交货时用于参考 9轮廓加工试件(型式A) 9.1概述
该检验包括五个孔的定位加工和镗削,以及在不同轮上的一系列精加工,用来检查不同运动条件下的机床性能,即仅一个轴线进给、两轴线的线性插补和圆弧插补
该检验通常在X-Y平面内进行,下列所示的检验即这种情况。但当备有万能主轴头时,同样可以在其他平面内进行该检验。 9.2尺寸
本部分提供了两种规格的轮廊加工试件,其尺寸见表2。
表2试件尺寸
单位为毫米一 52 100
m 140 280
名义尺寸!
p 30 50
9 110 220
160 320
2
GB/T18400.7—2010/IS010791-7:1998
试件的最终形状(如图1和图2所示)应由下列加工形成: a) 通镗位于试件中心直径为p的孔; b) 加工边长为1的外正四方形和边长为m的正四方形底座: c) 加工正四方形上面边长为9的菱形(对角线倾斜75的正四方形); d) 加工菱形上面直径为(g一2)mm、且深为6mm的圆: e 在外正四方形两边上加工角度为3或正切值为0.05、且深为6mm的倾斜面; f) 镗削直径为26mm(或大规格试件上为43mm)的四个孔和直径为28mm(或大规格试件上为
45mm)的四个孔:加工时,直径为26mm的孔沿轴线的正向趋近,直径为28mm的孔沿轴线的负向趋近,在距试件中心为处定位这些孔,
因为是在不同的轴向高度加工不同的轮廓表面,因此应保持刀具与下表面平面离开零点几毫米的距离以避免面接触。
单位为毫米
2-
O $45
0.015
$43 $50 0.0154
¥0.020D
@ 9
2E
2
标维分享业
bzfxw.com 0.020日 O0.020
4外 0.015
0.015
WW
20.020
4处 0.050
2处 0.015
001
20.020
082
2处 0.015
001 Z
-
10.020B 0.025
?
3
[100]
100
zl
0.015
注:周定尺寸与M16内六角螺钉有关
图1大规格轮廓廊加工试件
3
GB/T18400.7-2010/IS010791-7:1998
9.5毛坏和预加工
毛坏的底部为正方形底座,该底座边长为m,高度根据安装方法确定。 固定试件用的螺钉孔应位于菱形边之外的正方形底座上,如图1和图2所示为使切削深度尽可能保持一致,应进行预加工。
9.6 检验和公差
按GB/T18400的本部分进行精加工的试件的检验和公差见表3。
表3轮廊加工试件几何精度检验
单位为毫米
公 秦
检验项目
检验工具
名义规格 {=320
名义规格 [=160
中心孔 a) 圆柱度 b)孔轴线对基准A的垂直度正四方形 e)边的直线度 d) 相邻边对基准B的垂直度 e 相对边对基准B的平行度菱形 D 边的直线度 g) 四边对基准B的倾斜度圆 h)圆度 D外园和中心孔C的同心度 6 $0.025 0 $0.025 斜面)面的直线度
0.015 b) $0.015 b) $0.010 b) 坐标测量机
a) 0.010
a) 坐标测量机
a)
c) 0.015 dy 0.020
c) 0.010 d). 0.010 e) 0.010
e) 坐标测量机或平尺和指示器 d) 坐标测量机或角尺和指示器)坐标测量机或高度规或指示器
0.020 1
e)
0-0.015 f 0.010 坐标测量机或平尺和指示器 g)0.020 g 0,010 g) 坐标测量机或正弦规和指示器 h) 0.020
4
h0.015 h坐标测量机或指示器或度测量仪
3
坐标测量机或指示器或圆度测量仪
j)0.015 k)0.020 k) 0,010 k) 坐标测量机或正弦规和指示器
j) 0.010
坐标测量机或平尺和指示器
k)斜面对基准B的倾斜度键孔 n) 孔相对于中心孔C的位置度 0) 内孔与外孔D的同心度
n) $0.05 n) $0, 05 o) $0.02 0) $0.02
n) 坐标测量机 0) 坐标测量机或度测量仪
注1:如果可能,应将试件放在坐标测量机上进行测量,注2:对于直边(或正四方形、菱形和斜面)的检验,为得到直线度、垂直度和平行度的偏差,测头至少在10个点
处触及被测表面
注3:对于圆度(或圆柱度)检验,当测量为非连续性时,则至少检查15个点(圆柱度在每个测量平面内)。建议
圆度检验最好采用连续测量
9.7 记录的信息
按本部分的要求进行检验时,应尽可能完整地将下列信息记录到检验报告中去: a) 试件的材料和标志; b) 刀具的材料和尺寸: c) 切削速度: d) 进给量: e) 切削深度; f) 斜面3和tan0.05间的选择。
5
GB/T18400.7-—2010/ISO10791-7:1998
10端铣试件(型式B) 10.1概述
本试验的目的是检验通过两次走刀精铣端面时的平面度,两次走刀重叠约为直径的20%。通常该试验是通过沿×轴轴线的纵向运动和沿Y轴轴线的横向运动来完成的·但也可按制造厂和用户之间的协议,用其他的方法来完成, 10.2试件尺寸
两种试件尺寸和有关刀具的选择由制造厂规定或按制造厂与用户之间的协议在表4中,试件表面宽度是刀具直径的1.6倍,用80%刀具直径两次走刀来完成试件表面宽度的
切削,为了使两次走力的切削宽度近似相同,第一次走刀时刀具伸出试件表面约20%刀具直径,第三次走刀时刀具应伸出试件另一边约1mm(见图3)。试件长度应为宽度的1.25倍~1.6倍。
表4切削参数
试件表面宽度W/mm试件表面长度L/mm 切削宽度w/mm
刀具直径/mm
刀具齿数
50 100
80 160
100~130 200~250
40 80
4 8
20%刀具直径
第1次走刀
第2次走刀
-1mm
4
图3端铣试件走刀图
10.3刀具
采用可转位面铣刀(见GB/T5342.1-2006)。 10.4切削参数
本部分对试件的材料未做具体规定,当使用铸铁件时,可参见表4的切削参数。 当进给速度为300mm/min时,每齿进给量约为0.12mm,切削深度不应超过0.5mm。如果可
能.在切削时,垂直手被加工表面的轴线(通常为乙轴轴线)应锁紧。 10.5毛坏和预加工
毛坏底座应具有足够的刚性,并适合于夹紧到工作台或托板或夹具上,为了使切削深度尽可能保持一致,精切前应进行预切削加工。
力具安装时应符合下列公差要求: a)径向跳动≤0.02mm; b)端面跳动≤0.03mm。
10.6精加工表面的平面度公差
小规格试件被加工表面的平面度公差不应超过0.02mm:大规格试件被加工表面的平面度公差不应超过0.03mm。垂直于铣削方向的直线度检验反映出两次走刀重叠的影响,而平行于铣削方向的直 6