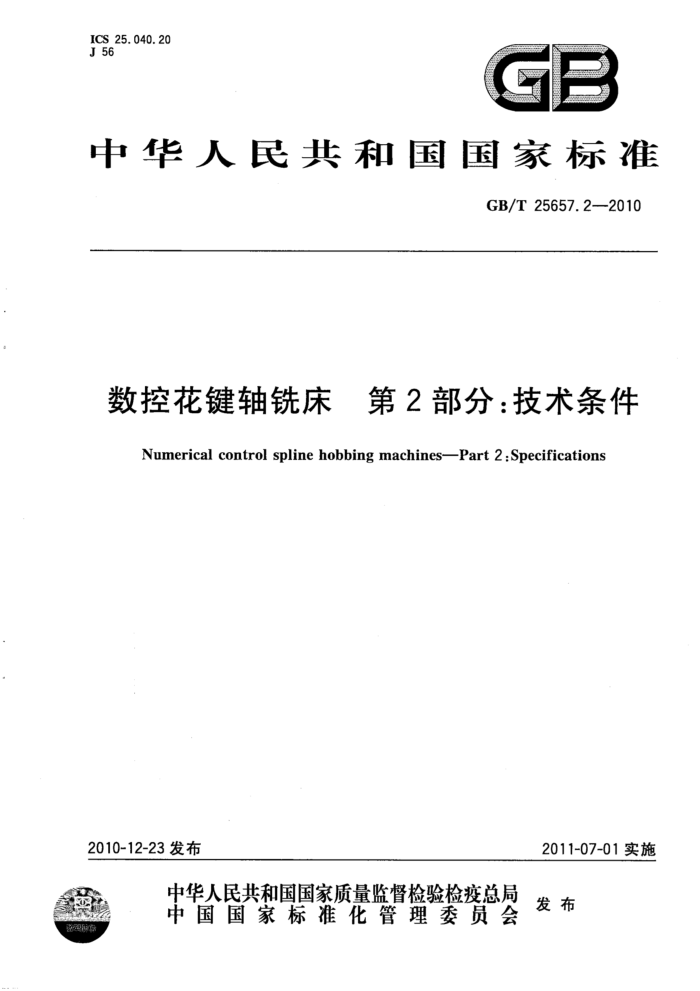
ICS 25.040.20 J 56
L
中华人民共和国国家标准
GB/T 25657.2--2010
数控花键轴铣床 第2 部分:技术条件
Numerical control spline hobbing machines—Part 2 : Specifications
2010-12-23发布
2011-07-01实施
中华人民共和国国家质量监督检验检疫总局
中国国家标准化管理委员会 发布
GB/T25657.2—2010
前言
GB/T25657《数控花键轴铣床》分为两个部分:
第1部分:精度检验:第2部分:技术条件。
本部分为GB/T25657的第2部分。 本部分由中国机械工业联合会提出。 本部分由全国金属切削机床标准化技术委员会(SAC/TC22)归口。 本部分起草单位:青海第二机床制造有限责任公司、重庆机床(集团)有限责任公司。 本部分主要起草人:郭林、颜芳、阎发治。
GB/T 25657.2—2010
数控花键轴铣床第2部分:技术条件
1 范围
GB/T25657的本部分规定了数控花键轴铣床设计、制造、检验与验收的要求。 本部分适用于最大铣削直径至400mm,最大工件长度至4000mm的数控花键轴铣床(以下简称
“机床”)。 2规范性引用文件
下列文件中的条款通过GB/T25657的本部分的引用而成为本部分的条款。凡是注日期的引用文件,其随后所有的修改单(不包括勘误的内容)或修订版均不适用于本部分,然而,鼓励根据本部分达成协议的各方研究是否可使用这些文件的最新版本。凡是不注日期的引用文件,其最新版本适用于本部分。
GB5226.1机械安全机械电气设备第1部分:通用技术条件(GB5226.1-2008IEC60204-1: 2005,IDT)
GB/T6576—2002机床润滑系统(eqvISO5170:1977) GB/T9061--2006金属切削机床通用技术条件 GB/T10095.1--2008 圆柱齿轮 精度制第1部分:轮齿同侧齿面偏差的定义和允许值
(ISO1328-1:1995,IDT)
GB15760金属切削机床 安全防护通用技术条件 GB/T17421.1一1998机床检验通则第1部分:在无负荷或精加工条件下机床的几何精度
(eqv ISO 230-1:1996)
GB/T23570-2009 金属切削机床 焊接件通用技术条件 GB/T23572---2009 金属切削机床 液压系统通用技术条件 GB/T25372—2010 金属切削机床 精度分级 GB/T25373—2010 金属切削机床装配通用技术条件 GB/T25374---2010 金属切削机床“清洁度的测量方法 GB/T25376—2010 金属切削机床机械加工件通用技术条件 GB/T25657.1一2010数控花键轴铣床第1部分:精度检验 JB/T3997—1994 金属切削机床灰铸铁件技术条件 JB/T8832—2001 机床数控系统通用技术条件
3技术要求 3.1一般要求
本章是对GB/T9061、GB/T25376、GB/T23570、GB/T25373等标准的具体化和补充,机床的设计与制造除应符合本章的规定外。还应符合上述标准中未经本章具体化的其他技术要求。 3.2布局和造型 3.2.1机床造型设计美观大方。外部结构与色彩匀称、和谐,外露的附件、配套件应与整机协调。 3.2.2机床各部件及装置应布局合理、高度适中,便于操作者观察加工区域。机床应排屑方便。 3.2.3机床的操作按钮应布置合理、操作方便,并应符合人类工效学原则。 3.2.4机床应装、拆、调整和维修方便,并应符合运输和装载的要求。
1
GB/T25657.2—2010
3.3附件和工具 3.3.1 机床应随机供应表1所列的附件和工具。
表 1
名称刀具心轴拉杆拔盘顶尖中心架跟刀架分度挂轮水平座专用扳手地脚螺钉机床垫铁
用 ·途
数 量全套 1件 1套 1套 1套 1套 1套 1件 1套 1套 1套
备 注
包括套、垫圈、平键、螺母
安装刀具带动工件
支承工件
调整机床
包括螺母、垫圈
安装机床
3.3.2扩大机床性能的特殊附件,可根据用户要求按协议供应。 3.3.3机床的标准附件和工具,均应保证连接部位的互换性和使用性能。 3.4电气系统
机床的电气系统应符合GB5226.1的规定。 3.5数控系统
机床的数控系统应符合JB/T8832的有关规定。 3.6液压、润滑和冷却系统 3.6.1机床的液压系统应符合GB/T23572的规定。 3.6.2机床的润滑系统应符合GB/T6576的规定。 3.6.3机床的冷却系统应保证冷却充分、可靠。 3.6.4机床的液压、润滑、冷却系统及其他部位均不应漏(渗)油、漏(渗)水。切削冷却液不应混入液压系统和润滑系统。 3.7安全卫生
机床上有可能对人身体健康或对设备易造成损伤的部位,应采取安全措施,机床的安全防护应符合 GB15760的规定。 3.8寿命 3.8.1机床的轴向进给导轨副、径向进给导轨副、尾座导轨副等重要导轨副应采取耐磨措施,并符合有关材质及热处理的规定。 3.8.2主轴、刀具主轴、尾座套筒、轴向进给丝杠及螺母、分度蜗杆副、刀具末端传动副、高速齿轮副等主要零件应采取与寿命相适应的耐磨措施,并符合材质及热处理的规定。 3.8.3机床导轨、丝杠等易被尘屑磨损的部位宜采取防护装置。 3.9加工质量 3.9.1机械加工件、焊接件应符合图样、工艺文件及GB/T25376、GB/T23570等的有关规定。 3.9.2灰铸件质量应符合JB/T3997的规定。 3.9.3机床的床身、溜板、铣头体、铣头箱体、床头箱体、尾座体等重要铸件应在粗加工后进行时效 2
GB/T25657.2—2010
处理。 3.9.4 热处理件质量应符合有关标准的规定。 3.10 装配质量 3.10.1 机床的装配质量应符合GB/T25373的规定。 3.10.2 下列结合面按GB/T25376和GB/T25373中“重要固定结合面”的要求检验:
a) 轴向(Z轴)进给滚珠丝杠支承箱与其相配件的结合面; b) 径向(X轴)进给滚珠丝杠支承箱与其相配件的结合面; c) 轴向(Z轴)进给滚珠丝杠螺母座与其配件的结合面; d) 径向(X轴)进给滚珠丝杠螺母座与其配件的结合面; e) 花键座与其配件的结合面。
3.10.3 床头箱与其相配件的结合面按GB/T25376和GB/T25373中“特别重要固定结合面”的要求检验。 3.10.4 下列导轨按GB/T25376和GB/T25373中“滑动导轨”的要求检验:
a) 轴向进给导轨副; b) 径向进给导轨副。
3.10.5 下列导轨按GB/T25376和GB/T25373中“移置导轨”的要求检验:
a) 尾座导轨副; b) 铣头回转导轨副; c) 铣刀主轴刀杆支撑导轨副: d) 机动窜刀导轨副。
3.10.6 机床装配过程中清洁度的检测按GB/T25374规定的方法进行,其中床头箱、铣头、铣头箱、润滑系统、液压系统的清洁度按重量法检验(抽查),其他部位按目测、手感法检验,不应有脏物。 3.10.7床头箱、铣头、铣头箱内部的杂质、污物不应超过表2的规定。
表2 最大铣削直径/mm
125
检验部位
>125~200 脏物质量/mg
>200~400
7 000 800 4 500
床头箱铣头铣头箱
800 800 1200
6 500 800 4 000
3.10.8机床液压、润滑系统的清洁度:在机床运行30min后,立即在液压系统(或润滑系统)回油口处取样,般不少于200mL,其杂质、污物不应超过150mg/L。 3.11外观质量 3.11.1机床外观表面不应有图样未规定的凸起、凹陷、粗糙不平和其他损伤。 3.11.2机床的防护罩应平整、匀称,不应翘曲、凹陷。 3.11.3机床零、部件外露结合面的边缘应整齐、匀称,除设计允许外不应有明显的错位。错位量和错位不匀称量宜符合表3的规定。 3.11.4机床的门、盖与机床的结合面应贴合,贴合缝隙值不大于表3的规定。 3.11.5机床的电气柜、电气箱等的门、盖周边与其相关件的缝隙应均匀,缝隙不均匀值不大于表3的规定。
3
GB/T25657.2—2010
表3
单位为毫米
>1 250~3 150
结合面边缘及门、盖边长尺寸
>500~1 250
≤500 1.5 1 > 1
错位量错位不匀称量贴合缝隙值缝隙不均匀值
2 1 1. 5 1.5
1. 5 2 2
注1:当配合面边缘及门、盖边长尺寸的长、宽不一致时,按长边尺寸确定允许值。 注2:错位不匀称量指外露结合面边缘同一边或对应边最大错位量与最小错位量之差值。 注3:缝隙不均勾值指门、盖间对开缝或其相对机床本体间最大缝隙值与最小缝隙值之差值。
3.11.6焊接件外露的焊缝宜修正平直、均匀。 3.11.7装入沉孔的螺钉不应突出于零件表面,其头部与沉孔之间不应有明显的偏心。固定销(轴用固定销两端均露者除外)一般应略突出于零件外表面。螺栓尾端应略突出于螺母端面。外露轴端一般应突出于包容件的端面,突出值约为倒棱值。内孔表面与壳体凸缘间的壁厚应均匀对称,其凸缘壁厚之差不应大于实际最大壁厚的25%。 3.11.8机床外露零件表面不应有磕碰、锈蚀。螺钉、铆钉、销子端部不应有扭伤、锤伤等缺陷。 3.11.9电镀件、发蓝件、发黑件色调应一致,防护层不应有褪色、脱落现象。 3.11.10电气、液压、润滑和冷却等管道的外露部分应布置紧凑、排列整齐,并不应产生扭曲、折叠等现象。 3.11.117 机床零件未加工的表面应涂以油漆。机床涂漆颜色及光泽应均匀一致,涂漆层应平整,涂漆表面不应有起泡及脱落等缺陷。机床可拆卸的零、部件装配结合面的接缝处,在涂漆以后应切开,切开时不应扯破漆面。 3.11.12机床上的各种标牌应清晰、耐久。产品铭牌宜固定在机床的明显位置,并应平整牢固、不歪斜。 4检验与验收 4.1一般要求 4.1.1本章是对GB/T9061.GB/T25376、GB/T23570、GB/T25373等标准的具体化和补充。按本章检验与验收机床时,应同时对上述标准中未经本章具体化的其余有关验收项目进行检验。 4.1.2验收机床时,按GB/T25372规定的V级精度机床的要求检验。 4.2机床的空运转试验 4.2.1在无负荷状态下,机床刀具轴主运动机构依次作低、中、高速运转,高速运转时间不应少于1h,使主轴轴承达到稳定温度。在靠近刀具主轴轴承的外壳处测量轴承的温度和温升,其值不应超过表4 的规定。
表4 温 度
单位为摄氏度
温 豐升 30 40
轴承型式
滑动轴承滚动轴承
60 70
注:机床经过一定时间运转后,其测量温度值上升幅度不超过每小时5℃时,可认为达到了稳定温度。
4
GB/T25657.2—2010
4.2.2液压系统应在额定工作压力下连续运转至油液达到热平衡后,测量油液的温度和温升,其温度值不应超过60℃,温升值不应超过30℃。
注:油液达到热平衡系指温升幅度每小时<2℃时的温度。 4.2.3检验(抽查)主运动和进给运动各级转速和进给量的数值,有级传动的各级主轴转速和进给量的实际偏差不应超过指令值或标示值的士5%,无级变速传动的各级主轴转速和进给量的实际偏差不应超过指令值或标示值的10%。 4.2.4机床动作试验一般包括下述内容:
a)机床刀具主轴、工件主轴在中等转速下连续进行正转、反转、停止试验,各不少于10次,动作应
灵活、可靠; b) 机床各直线运动部件在全行程上分别做低,中、高进给量变换试验,其运动应平稳、灵活,无明
显的爬行和振动现象; c) 反复变换主运动和进给运动的速度,检查变速机构是否平稳、可靠和指示的准确性; d) 用数控指令操作机床,在中等速度下分别对各坐标轴进行正、反向启动、停止(或制动)、工作
进给、快速进给及定向试验,各进行10次,动作应灵活、准确、可靠:
e): 按设计要求,对机床的各坐标轴联动、定位、直线插补、圆弧插补、进给坐标超程保护、坐标位置
显示、回基准点、手动数据输人、程序、序号指示和检索、程序暂停、程序消除等功能分别进行试验,其功能应可靠、动作应灵活、准确;
f)有锁紧机构的运动部件,在其行程的两端和中间位置做锁紧试验,每个位置各锁紧两次,锁紧
机构应可靠; g)检验装卸工件、刀具和附件等装置是否灵活、可靠; h)机床排屑装置进行运转试验,应可靠; i)模拟机床工作状态,操纵机床“急停”按钮(或开关),连续10次,应可靠。
4.2.5机床刀具轴主运动机构在各级速度下空运转至功率稳定后,测量机床主传动系统的空运转功率,其值不应超过设计规定(抽查)。 4.2.6机床模拟工作状态进行连续空运转试验,循环过程中应包括各种程序功能,其时间不少于36h。 在空运转过程中,各部分工作应正常,运行应平稳。各项功能、性能应可靠,不出现故障。各次循环程序之间的休止时间不应超过1min。
当出现异常或故障时应查明原因并加以排除,然后重新进行试验。 4.3机床的负荷试验 4.3.1最大铣削直径>200.mm~400mm的数控花键轴铣床应作承载工件最大重量的运转试验(抽查)。用低速及设计规定的高速运转机床,检验机床是否平稳、可靠。 4.3.2机床采用切削方法进行负荷试验,其切削条件及规范由设计规定,使机床达到最大功率(设计功率)。试验时,各机构工作应正常,无异常尖叫声,试件齿面无明显振纹。
切削时宜按以下公式检查机床在单位时间内的切除量,以评定机床的生产率(抽查):
P=(Wi--W2)/t
....(1)
式中: P---单位时间内的金属切除量,单位为千克每小时(kg/h); W.试件坏料的质量,单位为千克(kg); W.---切前试验后试件的质量,单位为于克(kg)
t--一切削时间,单位为小时(h)。
4.3.3定型产品出厂验收时,按设计规定的切削条件及规范进行负荷切削试验。
5
GB/T25657.2--2010
4.4机床的精度检验
机床的几何精度及工作精度检验应符合GB/T25657.1的规定。
4.4.1几何精度刀具主轴锥孔轴线与刀具托架轴承孔轴线的重合度”应在机床中速稳定温度时检验。 4.4.2工作精度检验按设计文件规定的切削规范进行。 4.4.3工作精度检验时,矩形花键试件键侧表面(或渐开线花键试件齿面)和齿轮试件齿面的表面粗糙度Ra最大允许值为3.2μm。 4.4.4按表5的规定进行工作精度检验(抽查)。
表5
单位为毫米
检验方法参照
序号
检验性质 切削条件检验项目 允差 检验工具 GB/T17421.1—1998
简图和试件参数
的有关条款
精铣渐开 AA级齿 公法线长 0.03 齿轮测 按GB/T10095.1
度的一致性
量仪器 的规定分别测量七个
线圆柱台 轮滚刀阶齿轮,按数控程序连续切削七个试件
齿轮的公法线长度,其尺寸的最大变化值,即为其公法线长度的一致性误差(齿圈1和齿圈2均需检验)
Bp4
D一(0.5~1)最大铣削直径 mpa~0.75机床最大模数 Bp≥6机床最大模数其余试件参数由制造厂确定材料:45钢正火 Dp4——齿项圆直径;
P4
一法向模数;
mp4
Bp4 一齿宽;
一齿圈1齿高; h2———齿圈2齿高; b1 一齿圈1部分齿宽: ba 一齿圈2齿宽
h1