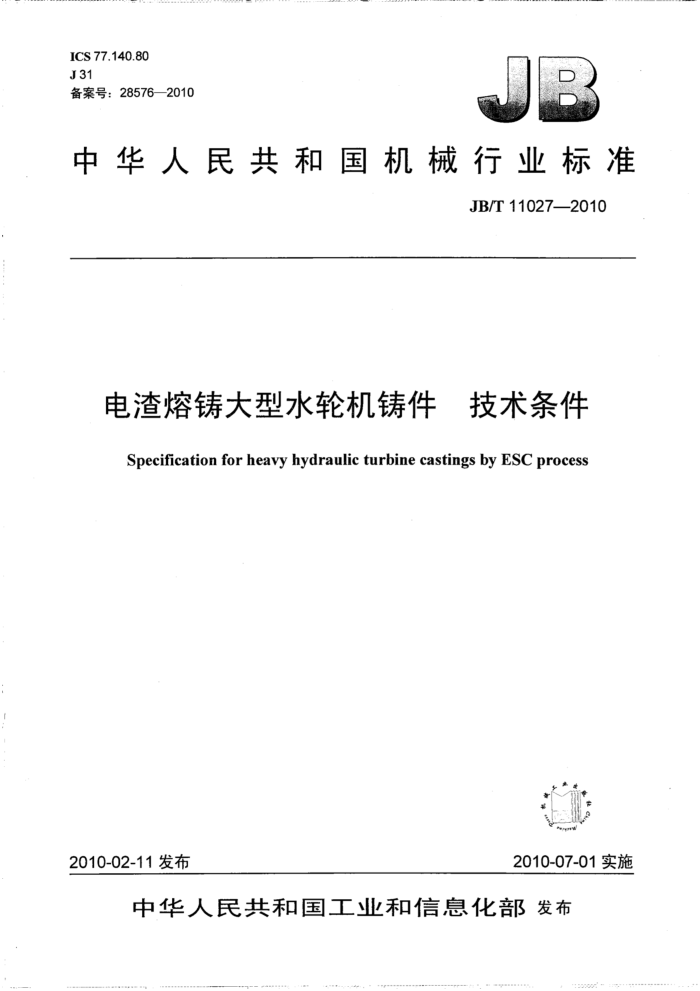
ICS 77.140.80 J31 备案号:28576—2010
中华人民共和国机械行业标准
JB/T110272010
电渣熔铸大型水轮机铸件 技术条件
Specification for heavy hydraulic turbine castings by ESC process
2010-07-01实施
2010-02-11发布
中华人民共和国工业和信息化部发布
JB/T11027—2010
目 次
前言
范围 2规范性引用文件 3”订货要求.. 4 制造工艺 4.1 冶炼. 4.2 铸造 4.3 热处理, 4.4 缺陷的处理 4.5 机械加工
1
5 技术要求 5.1 化学成分 5.2 力学性能 5.3 表面质量 5.4 形状和尺寸公差, 5.5 重量公差 5.6 无损检测 6 试验方法和检验规则 6.1 化学成分分析 6.2°力学性能检验 6.3 无损检测 6.4 型线检测 7 质量证明书, 8标志、包装和运输表1铸件的化学成分表24 铸件的力学性能,表3 铸件尺寸公差表4铸件的机械加工余量
..
JB/T11027—2010
前 言
本标准由中国机械工业联合会提出。 本标准由机械工业大型铸锻件标准化技术委员会归口。 本标准起草单位:沈阳铸造研究所、哈尔滨电机厂有限责任公司、东方电机有限公司。 本标准主要起草人:陈瑞、王安国、娄延春、姜云飞、王洪峰、李旭东、于洪若、张家东、王大威、
蒋国森、祝强、高尚书、李宝东、谢华生、王子文、过杰、王辉亭、马德生。
本标准为首次发布。
T
JB/T11027—2010
电渣熔铸大型水轮机铸件 技术条件
1范围
本标准规定了电渣熔铸大型水轮机铸钢件的订货要求、制造工艺、技术要求、试验方法和检验规则及质量证明书等。
本标准适用于500MW及以上大型水轮机的整铸导叶、分体组焊式导叶等铸钢件的订货、制造、 检验和验收。 2规范性引用文件
下列文件中的条款通过本标准的引用而成为本标准的条款。凡是注日期的引用文件,其随后所有的修改单(不包括勘误的内容)或修订版均不适用于本标准,然而,鼓励根据本标准达成协议的各方研究是否可使用这些文件的最新版本。凡是不注日期的引用文件,其最新版本适用于本标准。
GB/T223(所有部分).钢铁及合金化学分析方法 GB/T228金属材料室温拉伸试验方法(GB/T228—2002,.eqvISO6892:1998) GB/T229 金属材料夏比摆锤冲击试验方法(GB/T229—2007,ISO148-1:2006,MOD) GB/T231.1金属材料布氏硬度试验第1部分:试验方法(GB/T231.1一2009,ISO6506-1:
2005,MOD)
GB/T232 金属材料弯曲试验方法(GB/T232—1999,eqvISO7438:1985) GB/T7233 铸钢件超声探伤及质量评级方法 GB/T9443 铸钢件渗透检测(GB/T9443—2007,ISO4987:1992,IDT) GB/T9444 铸钢件磁粉检测(GB/T9444-2007,ISO4986:1992,IDT) GB/T10969 水轮机、蓄能泵和水泵水轮机通流部件技术条件 GB/T11351—1989铸件重量公差 JB/T7349 混流式水轮机焊接转轮不锈钢叶片铸件 JB/T10384中小型水轮机通流部件铸钢件
3订货要求 3.1 供需双方应在订货合同或技术协议中规定铸件名称、采用标准、材料牌号、订货数量和供货状态等。 3.2 需方必须向供方提供订货图样,并标明产品尺寸、公差、表面粗糙度和检验项目等。 3.3当需方提出本标准规定以外的特殊要求和补充要求时,应经供需双方协商确认。 4 制造工艺 4.1冶炼
供方应按技术条件规定的方法进行自耗电极的冶炼,当需方对冶炼方法未作要求时,供方可自行决定自耗电极的冶炼方法。 4.2铸造 4.2.1结晶器
结晶器由内、外腔板及法兰板等组成,采用结构焊接、法兰密封或整体铸造的方法制造。 4.2.2熔渣
JB/T11027-2010
熔渣采用CaF2-Al2O3渣系,熔渣组分的质量百分比纯度应为:CaF2≥95%,AI2O3≥97%。 4.2.3电渣熔铸
铸件采用电渣熔铸方法成型。工艺补偿部分应在最终热处理前清除。 4.3热处理
不锈钢铸件的热处理采用正火加回火的方式进行、ZG20SiMn铸件的热处理可采用正火或正火加回火的方式进行。 4.4缺陷的处理 4.4.1允许对超标缺陷进行补焊修复。补焊前应采用机械加工、打磨等方法清除缺陷,并应进行无损检测(通常为磁粉检测或渗透检测),确认缺陷已完全清除,并应作好补焊记录。 4.4.2:缺陷的补焊应由有相应资格的操作人员按补焊工艺要求进行,焊接材料的化学成分应与铸件化学成分相同或相近。 4.4.3铸件在补焊后应打磨平整,并应按照补焊前的无损检测要求对补焊部位和热影响区进行检查,以确认补焊质量。 4.4.4铸件在补焊后应进行消除应力热处理。消应处理后原则上不应再进行补焊,如有少量缺陷必须进行补焊,则焊后应进行局部消应热处理并作记录。 4.5机械加工
供方应按订货要求对铸件进行加工。 5·技术要求 5.1化学成分
铸件钢水应进行熔炼分析,其化学成分的质量分数应符合表1规定。
表1 铸件的化学成分(质量分数)
(%)
残余元素
M
材料牌号
Mn
S
P
Ni
Mo
Si
Cr
总量
Cu
V
W
ZG06Cr13Ni4Mo ≤0.05≤1.00 ≤1.00 1 M 12.00~ 3.50~ 0.40 0.50 0.10 0.03 0.80
0.015 0.030 13.50 5.00 1.00 V M 12.00~ 4.50 0.40 0.015 0.030 13.50 5.50 1.00 V
0.50 0.10 0.03 0.80
ZG06Cr13Ni5Mo ≤0.05 ≤1.00 ≤1.00
12:00 5.00 0.40~
0.50 0.10 0.03 0.80
ZG06Cr13Ni6Mo ≤0.05 ≤1.00 ≤1.00
0.015 0.030 13.50 6.50 1.00
ZG06Cr16Ni5Mo ≤0.05 ≤1.00 ≤1.00 V
15.50~ 4.50 0.40
0.50. 0.10 0.03 0.80
0.015 0.030 17.50 6.00 1.00
ZG06Cr13Ni5Mn3Moj≤0.05 ≤1.00 2.50~
V 12.00~ 4.50~ 0.40~
4.00 0.015 0.030 13.50 5.50 1.00 0.50
0.10 0.03 0.80
0.16~ 0.55~ 1.00~ ≤ V 0.22 0.85 1.30 0.015 0.030
≤0.40
ZG20SiMn
注:需方无要求时,残余元素含量的测定仅作参考。 5.2力学性能
铸件的力学性能见表2。 5.3表面质量 5.3.1一般要求
铸件表面不得有裂纹、密集性气孔缺陷存在,
2
JB/T110272010
表2铸件的力学性能 Rm
Rel/Rpo.2 MPa M 550 550 550 590 750 295
4 (%) ≥ 16 16 16 15 14 16
z (%) M 40 40 40 35 35 30
Akv J 80 80 80 55 50 30
材料牌号
MPa M 750 750 750 785 900 510
HBW
221~286 221~286 221~286 221~286 330~370 ≥150
ZG06Cr13Ni4Mo ZG06Cr13Ni5Mo ZG06Cr13Ni6Mo ZG06Cr16Ni5Mo ZG06Cr13Ni5Mn3
ZG20SiMn 5.3.2表面粗糙度
铸件表面粗糙度应符合订货图样规定。如图样未作规定,则表面粗糙度应达到Ra25um,需作无损检测的铸件,其表面粗糙度应符合无损检测要求。 5.4形状和尺寸公差
铸件的几何形状和尺寸应符合订货图样的要求,采用通用量具及专用样板等进行检验。毛坏尺寸公差要求应符合表3规定,不低于CT13级;粗磨或加工的铸件机械加工余量见表4,余量等级应不低于 J级。
表3 铸件尺寸公差
单位:mm
铸件尺寸公差等级CTa
毛坏铸件基本尺寸大于 160 250 400 630 1000 1600 2500 4000 6300 对壁厚采用低一等级公差,最多不低于CT13级。
至 250 400 630 1000 1600 2 500 4000 6300 10 000
10 4 4.4 5 6 7 8 9 10 11
11 5.6 6.2 7 8 9 10 12 14 16
12 8 .9 10 11 13 15 16 18 20
13 11 12 14 15 16 18 20 23 25
表4 铸件的机械加工余量
单位:mm
机械加工余量等级要求
最大尺寸
大于 200 400 .630 1000 1 600 2 500 4000 6300 注:最大尺寸是指最终机械加工后铸件的最大轮廓尺寸。
至 400 .630 1000 1 600 2.500 4.000 6300 10 000
G 3.5 4 5. 5.5 6 7 8 9
H 5 6 7 8 9 10 11 12
.J. 7 9 10 11 12. 14 16 17
JB/T110272010
样应按6.2.1和6.2.4的规定进行检验。
冲击试验应制备三个试样进行复试。复试的每个试样的值都应等于或超过规定的最小平均值,否则应将试块连同所代表的铸件重新进行热处理。重新热处理后的试样应按6.2.2的规定进行检验。
铸件和试块重新热处理的次数不得超过两次(回火次数不计)。若重新热处理后的试验结果仍不合格,则该铸件应予以报废。 6.3无损检测
超声检测应按GB/T7233的规定执行。渗透检测应按GB/T9443的规定执行。磁粉检测应按GB/T 9444的规定执行。当需方有特殊要求时,按需方要求执行。 6.4.型线检测
型线检测方法可由供需双方协商确定,也可参照GB/T10969、JB/T7349及JB/T10384的规定执行但应充分考虑到打磨及加工余量对铸件毛坏的影响。
质量证明书交货时,供方应向需方提供质量证明书。质量证明书一般应包含以下内容: a)订货合同号; b)订货图号、产品名称; c)标准号和材料牌号; d)铸造方法; e)熔铸炉号、件号; f)热处理状态; g)产品重量; h)化学成分分析结果; i)力学性能检验结果; j)无损检测结果; k)主要缺陷补焊记录(包括位置与尺寸草图); 1)铸件型线尺寸检查记录; m)其他需方要求的检验结果: n)供方单位名称。
7
8标志、包装和运输 8.1供方应在每个铸件上打印炉号、件号及供货方单位名称等标记。 8.2 供方应根据运输条件要求进行包装。