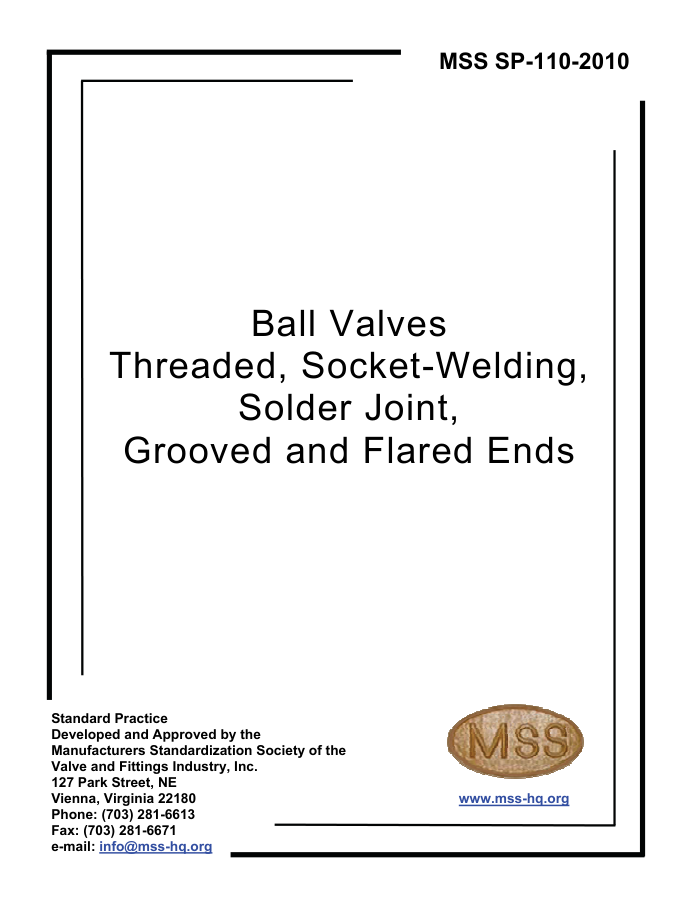
MSS SP-110-2010
BallValves
Threaded, Socket-Welding
Solder Joint.
Grooved and Flared Ends
StandardPractice DevelopedandApprovedbythe ManufacturersStandardizationSocietyofthe Valveand FittingsIndustry,Inc. 127ParkStreet,NE Vienna, Virginia 22180 Phone:(703)281-6613 Fax:(703)281-6671 e-mail: info@mss-hq.org
MSS
www.mss-hg.org
SP-110
MSS
STANDARDPRACTICE
This MSS Standard Practice was developed under the consensus of the MSS Technical Committee 4o1 and the MsS Coordinating Committee.The content of this Standard Practice is the result of the efforts of competent and concerned volunteers to provide an effective, clear, and non-exclusive specification that will benefit the industry as a whole.This MsS Standard Practice is intended as a basis for common practice by the manufacturer, the user,and the general public.The existence of an Mss Standard Practice does not in itself preclude the manufacture,sale,oruse of productsnot conformingtotheStandardPractice.Mandatory conformance is established onlybyreference in a code, specification, sales contract, or public law,as applicable.
"Other standards documents referred to herein are identified by the date of issue that was applicable to this Standard Practice at the date of issue of this Standard Practice. See Annex A.This Standard Practice shall remain silent on the applicability of those other standards of prior or subsequent dates of issue even though applicableprovisions may not have changed References contained herein which arebibliographic in nature are noted as 'supplemental'in thetext."
Unless otherwise specifically noted in this Mss SP, any standard referred to herein is identified by the date of issue that was applicable to the refereced standard(s) at the dae of issue of this Mss Standard Practice (See Annex A). In this Standard Practice all notes, annexes,tables, and figures are construed to be essential to the understanding of the message of the standard,and are considered part of the text unless noted as"supplemental".All appendices, if included, that appear in this document are construed as"supplemental". Supplemental information does not include mandatory requirements for this Standard Practice.
U.S. customary units in this Standard Practice are the standard; metric (SI) units are for reference only.
Substantive changes in this 2010 edition are “flagged" by parallel bars as shown on the margins of this paragraph.The specific detail of the change may be determined by comparing thenaterial flagged with that in the previous edition.
Non-toleranced dimensions in this Standard Practice are nominal, and, unless otherwise specified shall be considered"for reference only"
Anypart of this Standard Practicemaybequoted.Credit linesshould read'Extractedfrom Mss SP-I10 2olowithpermissionofthepublisher,theManufacturersStandardizationSocietyof theValveand FittingsIndustry,Inc.':Reproductionprohibitedundercopyrightconventionunlesswrittenpermissionis granted by the Manufacturers Standardization Society of the Valve and Fittings Industry,Inc.
Originally Approved: May 1992
Copyright , 1992, 1996, 2010 by Manufacturers Standardization Society
of the
Valve and Fittings Industry, Inc.
Printed in U.S.A.
i
MSS
SP-110
STANDARDPRACTICE
TABLEOFCONTENTS
SECTION
PAGE
SCOPE.... PRESSURE-TEMPERATURE RATINGS MATERIALS. DESIGN. DIMENSIONS MARKING. TESTING
1 2 3 4 5 6 7
TABLE 1 2 3
Port Sizes for Ball Valves.. Shell Test Duration (Visual Test Methods) Seat Test Duration ...
FIGURE
6
1 2 ANNEX
ExamplesofValveTypes Typical Nomenclature for Ball Valve Parts..
A
Referenced Standards and Applicable Dates .
10
ii
SP-110
MSS
STANDARDPRACTICE
Manufacturers Standardization Society of the Valve And Fittings Industry, Inc.
MSS
127 Park Street, NE · Vienna, VA 22180-4602 · 703-281-6613 · FAX 703-281-6671 · www.mss-hq.org e-mail:info@mss-hq.org
EXECUTIVEDIRECTOR: Robert F.O'Neill
ERRATASHEETFORMSSSP-110-2010
BALLVALVESTHREADED,SOCKET-WELDING,SOLDERJOINT.
GROOVEDANDFLAREDENDS
August 23, 2010
Notethefollowingcorrection:
1. Page 2, Section 3.3, Other Parts. Under “Caution for Users," the second sentence
should read“Forguidance,see ASME B31.3,AppendixF."
ThisErrata Sheetisincluded in the StandardPractice
Futureprintingof theStandard Practicewill includethis revised data
PRESIDENT: J.V.BallunVal-Matic Valve& Mfg.Corp
VICE PRESIDENTS: T.J.Hannafin-KITZ Corp.of America ·M.A. Clark-NIBCO,Inc
TREASURER: G.M. Johnson - United Valve
ili
MSS
SP-110
STANDARDPRACTICE
BALLVALVES
THREADED,SOCKET-WELDING,SOLDERJOINT,
GROOVEDANDFLAREDENDS
1. SCOPE 1.1 General
1.3 Description of ValveTypesandParts 1.3.1Examples of somevalvetypes are shown in Figure 1. When variations ofthese basic types are used, they shall be named by the manufacturer. 1.3.2The names of basic valveparts are given in Figure 2. Note: The valve sketches shown in Figures 1 and 2are for the purposeof illustration and nomenclature only and do not represent or endorse any manufacturer's product.
1.1.1 This StandardPractice coversround opening,full, regular and reduced port metal ball valves. 1.1.2 End connectionscovered hereinare threaded, socket-welding, solder joint, grooved and flared end in nominal pipe sizes /4 through 4 inch. 1.1.3 These valves are intended for on-off operation and should be used for modulating or throttling service only when recommended by the manufacturer. 1.1.4 This Standard Practice covers ball valves of the following materials:
2. PRESSURE-TEMPERATURE RATINGS
2.1 Basis ofRatings
The pressure-temperature ratings for assembled valves shall be determined by the material of the body, seats, stem seals, end connections or any other component or type of construction that would be restrictive. Manufacturers should be consulted for exact ratings applicable for a particular material or type. Pressure-temperature ratings of steel valves, shall not exceed those specified in ASME B16.34, where applicable. 2.2 SolderEndRatings Ratings of solder-end connections shall not exceed the limitations of ASME B16.18.It shall be the responsibility of the user to select a solder composition that is compatible with the service conditions. 2.3 Cold WorkingPressure (CWP) The cold working pressure rating of the valve shell and components is themaximum allowable non-shock pressure at 1oo°F.The maximum working pressure at any other temperature shall not exceed this rated pressure.
Carbon Steel Alloy Steels Stainless Steels Gray Cast Iron Ductile Iron Malleable Iron Copper Alloy
1.2References 1.2.1 Standards and specifications adopted by reference in this Standard Practice and names and addresses of the sponsoring organizations are shown in Annex A. It is not considered practical to refer to a specific edition of each of the standards and specifications in the individual references. Instead, the specific edition references are included in Annex A. A product made in conformance with the edition reference applicable during the time of manufacture, and in all other respects conforming to this Standard Practice, will be considered to be in conformance even though the edition referencemay be changed in a subsequent revision of this Standard Practice.
1
MSS
SP-110
STANDARDPRACTICE
4. DESIGN 4.1 General
3. MATERIALS
3.1 Valve Body 3.1.1 SteelSteels shall bemade toASTM,AISI or other standards for which mechanical and chemical data are available. The valve pressure boundary parts and bolts shall bemade from metals that have the allowable stress established for the temperature range for which the valve is designed. This can be metals that the ASME has established allowable design stress at temperatures the valve will be used at or stress established by testing in accordance with the rules of ASME Consideration of welding characteristics shall be given to those steels intended for socket weld end valves. 3.1.2 Iron Casting for Threaded End Valves Cast iron shall conform to ASTMA126, Class B orC.Malleable iron castings shall conform to ASTMA47(Grades32510.35018)orASTM A197.Ductile iron castings shall conform to ASTM A395 or ASTM A536 (Grades 60-40-18 or 65-45-12). 3.1.3Nonferrous AlloysNon-ferrous materials shall be made to ASTM,CDA, or other standards forwhichmechanical andchemicaldataare available. 3.2Bolting Preferred bolting materials are as specified in ASMEB16.34 Table 1,Group 4.If non-listed materials are used, the valve manufacturer shall be prepared to certify that the products are at least equally suitable for the intended use. 3.3OtherParts Parts,for example stems,glands, packing nuts, balls, seats, and seals shall be of materials suitable for the pressure-temperature rating. Caution for Users: Service conditions other than pressure-temperature may affect suitability of the valve materials. For guidance, see ASME B31.3, Appendix E.
The valve design and materials of construction shall be structurally suitable for their stated pressure ratings and temperature limits.Any additional metal thickness above the thickness necessary tocontainpressuresuchasmay be needed for assembly stresses, valve closing stresses. shapes other than circular. stress concentrations,and corrosion allowances,shall be determined by the manufacturer. 4.2Joints 4.2.1The design of the valve shall be such as to provideagainst detrimental distortion under hydrostatic test conditions, assembly stresses, closing stresses,pipe reaction stresses, or when rated pressure is applied across a closed valve. 4.2.2 Bolting shall be threaded in accordance with ASMEB1.1.
4.2.3 Top entry valve bonnet joints shall be designed as follows: 4.2.3.1Flanged bonnet bolting shall be such that adirectnominalstressresultingfromthe maximum working pressure acting on an area bounded by the effective outside periphery of the bonnet seal shall not exceed the allowable bolt stress values listed in ASME Boiler and Pressure Vessel Code,Section VIlIDivision l;not to exceed 20,o00 psi. For non-listed bolt materials the allowable bolt stress shall be taken as 25% of the yield strength, not to exceed 20,000 psi. 4.2.3.2Threaded bonnet or cover joints shall have a thread shear area that satisfies the following:
P(Ag/As) ≤.6Sa where: P= Valve cold working pressure,psig
2
MSS
SP-110
STANDARDPRACTICE
4.3.2Socket dimensions of socket welding ends shall be in accordance with ASME B16.11. 4.3.3Solder cup dimensions of solder joint ends shall be in accordance with ASME B16.18. 4.3.4 Grooved ends shall have groove dimensions in accordance with MIL-P-11087G. 4.3.5Flared ends shall be in accordance with ASMEB16.26. 4.4Stems 4.4.1 To prevent removal of the stem while the valve is pressurized, the valve shall be designed so that the stem seal retainer assembly (gland) alone does not retain the stem. 4.4.2 In those cases where service conditions require electrical continuity between the stem and body, the purchaser must so specify. 4.5StemPacking 4.5.1Thevalve shallhave provisions for adjustment of a gland or packing nut in order to obtain a seal at the stem packing. The exception is for valves with elastomeric stem seals,where adjustment is not possible. 4.6PositionIndication 4.6.1The valve shall have a positive means of indication of ball port position. If the handle is the only means of indication (i.e.,valve not equipped with position indication), it shall be designed such that the handle cannot be assembled to indicate other than the position of the ball port.
Ag = Area bounded by the effective outside periphery of a gasket or O-ring, or other seal effective periphery,except that in the case of a ring-joint, the bounded area is defined by the pitch diameter of the ring, square inches. As = Total effective thread shear area, square inches. Sa =Allowableminimum body/bonnet stress, from ASME Boiler and Pressure Vessel Code, Section VIII, Division 1, not to exceed 20,o00 psi. For non-listed materials, the allowable stress shall be thelesser of 25%ofthe minimumtensile strength, or 67% of the minimum yield strength, not to exceed 20,000 psi. 4.2.4Valves having flanged body joints which split the valve either perpendicular to or at an angle with the piping are subject to piping loads. Bolting in these cases shall be such that a direct tensile stress shall not exceed /g of the allowable stress listed in ASME Boiler and Pressure Vessel Code,Section VIIl,Division 1,not to exceed 20,000 psi. For non-listed bolting materials, the allowable bolt stress shall be taken as 25% of the yield strength not to exceed 20,000 psi. 4.2.5Valves of a one-piece end entry type shall be designed so that the body insert is sufficient to withstand the full differential pressure permissible for the valve. 4.2.6Threaded body joints exposed to piping loads shall satisfy the following thread shear area requirements:
P(Ag/As) ≤ .47Sa where: P,Ag,As, and Sa are as defined in Section 4.2.3.2. 4.3EndConnections 4.3.1 Threaded pipe ends shall have taper pipe threads in accordance with ASME B1.20.1.
5. DIMENSIONS
5.1 Valve port diameters for full port, regular port and reduced port are defined in Table 1. All components forming the flow stream shall have an inside diameter no smaller than as indicated.
3
MSS
SP-110
STANDARDPRACTICE
6. MARKING
7.1.3For valves having CWP no greaterthan 1500 psig, the manufacturer may, as a substitute for the test specified in Section 7.1.1 test each valve using gas at a minimum pressure of 80 psig for a duration of not less than set forth in Table 2. In order to exercise this option, the manufacturer must sample production lots to ASQ Z1.4,Level II, 0.4 AQL using the test specified in Section 7.1.1. 7.1.4 For reduced port, end entry valves having one-piece bodies in nominal pipe sizes 2 and smaller that have aCWPno greater than 2000 psig, the manufacturer may, as a substitute for the test specified in Section 7.1.1 test each valve usinggas at a minimumpressure of 80 psig for a duration of not less than set forth in Table 2. In order to exercise this option, the manufacturer must sampleproduction lots toASQZ1.4,Level II, 0.4 AQL using the test specified in Section 7.1.1. 7.1.5The ball shall be in such a position during the shell test as to assure full pressurization of the valve shell. 7.1.6 When tested with a liquid, the valve exterior shall show no visibleleakage.When tested with a gas, the valve shall show no visible leakage when immersed in water or coated with a leak detection solution. 7.1.7 Visuallydetectableleakagethrough pressureboundarywallsis not acceptable Leakage through adjustable stem packing during testing shall not be cause for rejection. The stem
6.1 Ball valves shall be marked in accordance with MSS SP-25
6.2Copperalloy ball valves madewith copper alloy components including end pieces or caps, stem, ball (which may be either plated or unplated) and the manufacturer's standard seat material for those valves do not need trim marking per Section 7.1.3 of MSS SP-25. 6.3Copper alloy ball valvesmanufacturedwith optional trim componentsforball,stem,or seats shall be marked to indicate the optional ball, stem. or seat per MSS SP-25, or as identified by the manufacturer's figure or model number.
7. TESTING
7.1 Shell Test
7.1.1Each valve, except as noted in Sections 7.1.2 thru 7.1.4, shall be given a shell test, at a pressure of 1.5 times the CWP, and rounded off to the next higher 25 psi. The test fluid shall be air gas, water, kerosene, or liquids with a viscosity no greater than thatof water.Thetestfluid temperature shall be below 100°F.The duration of the test shall be as set forth in Table 2.
7.1.2 Forvalveshaving CWPnogreaterthan 1000 psig,the manufacturer may,as a substitute for the test specified in Section 7.1.1 test each valve using gas at a minimum pressure of 80 psig for a duration of not less than that set forth in Table 2. In order to exercise this option,the packing or stem seals shall be capable of retaining manufacturermustbeabletocertifythat
pressure at least equal to the rated cold working
production sample of the valve model so tested pressure of the valve without visible leakage. has been subjected to a hydrostatic shell test of at
7.1.8When volumetric loss testing devices are usedthe valvemanufacturer must be able to demonstrate that leakage sensitivity of the device produces results that are equivalent to those which are acceptable when visual examination methods are employed.
least2.5timesCWPwithnodetrimental distortion as evidenced by a subseguent seat test.
4