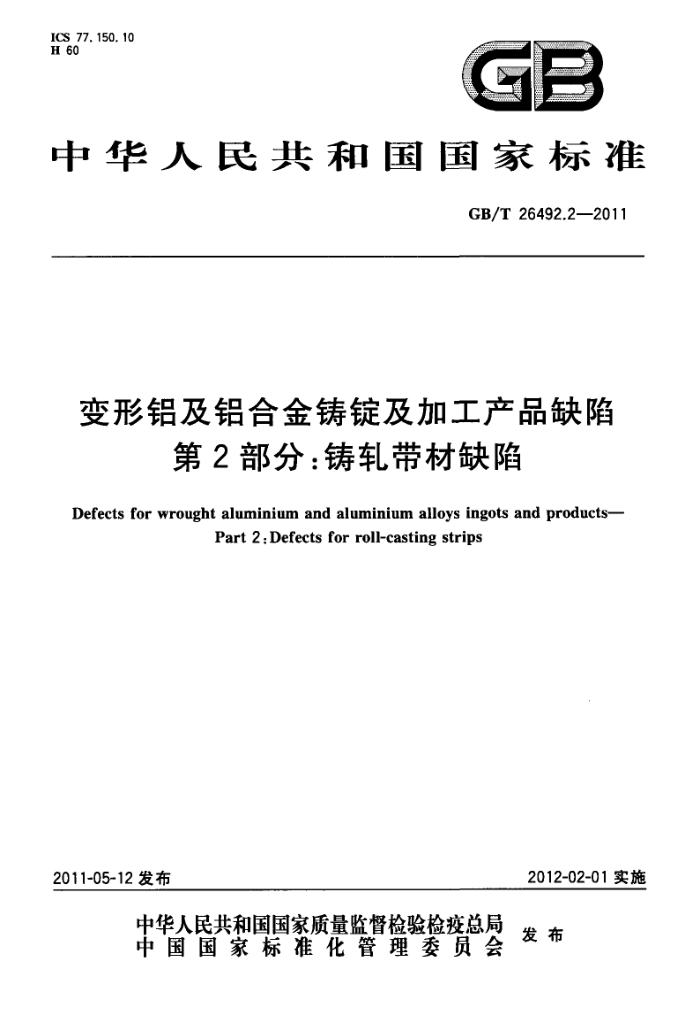
ICS 77.150.10 H 60
GB
中华人民共和国国家标准
GB/T26492.2—2011
变形铝及铝合金铸锭及加工产品缺陷
第2部分:铸轧带材缺
Defects for wrought aluminium and aluminium alloys ingots and products-
Part 2:Defects for roll-casting strips
2012-02-01实施
2011-05-12发布
中华人民共和国国家质量监督检验检疫总局
中国国家标准化管理委员会 发布
GB/T26492.2—2011
前言
GB/T26492《变形铝及铝合金铸锭及加工产品缺陷》分为5个部分:
第1部分:铸锭缺陷;一第2部分:铸轧带材缺陷;第3部分:板、带缺陷;一第4部分:铝箔缺陷;一第5部分:管材、棒材、型材、线材缺陷。 本部分为GB/T26492的第2部分。 本部分由全国有色金属标准化技术委员会(SAC/TC243)归口。 本部分负责起草单位:华北铝业有限公司。 本部分参加起草单位:中铝瑞闽铝板带有限公司、云南新美铝铝箔有限公司、中国铝业西北铝加工
分公司、郑州铝业股份有限公司、东北轻合金有限资任公司、江苏常铝铝业股份有限公司。
本部分主要起草人:潘军朋、王志勇、杨碧烟、郭义庆、高珺、张国良、侯波、韩于永、郭瑞、王进卫、 孔祥鹏。
I
GB/T26492.2—2011
变形铝及铝合金铸锭及加工产品缺陷
第2部分:铸轧带材缺陷
1范围
本部分规定了双辑连续铸轧铝带产品中常见缺陷的定义、特征,并分析了其主要产生原因。 本部分适用于双辊式铸轧机生产的变形铝及铝合金铸轧带缺陷的分析与判定。
2缺陷定义、特征和主要产生原因 2. 1
分层裂纹laminationcrack 铸轧带表层下出现由低熔点相和Fe、Si等杂质隔开的分层。有时分层延伸到表面,形成马蹄形裂
口[如图1a)]。延伸或未延伸到表面的这种缺陷称之为分层裂纹。分层裂纹一般是各个分离且成群出现[如图1b)]。裂纹两侧组织差异较大,表面低熔点相和杂质相较少,晶粒较粗大,内部低熔点相和杂质相较多,晶粒细小。
主要产生原因:分层裂纹是由于铸轧带在凝固过程中,凝壳抗剪强度小于表面粘着区和中心变形区之间的附加切应力所致。
a)表面
b)侧向截面
图1分层裂纹
2.2
通条裂纹 run-through crack 铸轧带表面出现弧形、V形或无固定横向裂纹或裂口,沿着轧制方向形成或排列成裂纹带。它往
往同气道、表面偏析带、粗晶带等缺陷伴生。
主要产生原因: a)供料嘴局部堵塞; b)嘴唇局部破损或结渣。
2. 3
热带 专hotstrip 铸轧带局部未受轧制变形,具有自由结晶表面的区域(如图2)。缺陷严重时会穿透板厚,形成孔
洞;热带形状不规则,有不同程度的凹陷。凹陷的表面不平整,往往伴随有裂缝出现,有时有偏析浮出物。
主要产生原因:
1
GB/T26492.2—2011
a)铸轧温度过高、速度过快、冷却强度不够等原因致使熔体出现局部未完全凝固; b) 前箱液面太低;
供料嘴严重堵塞等原因致使局部熔体供给不足,熔体不能和辊面充分接触,因而未受轧制变形,保留铸态组织。
10mm
图2热带(表面)
2.4
气道void 铸轧带内形成的纵向连续或间断延伸不规则的凹坑。通过低倍试片肉眼可见的孔洞称为气道。借
助放大镜才能发现的称为微孔。气道附近晶位发生歪扭,表面多显现白道,严重时可延续到铸轧带全长,常伴有通条裂纹和麦穗状晶。气道分横向位置固定气道和游动性气道(如图3)。
主要产生原因: a)熔体含气量多; b) 供料系统干燥不彻底; c)供料嘴结渣; d) 铸轧辊表面温度与环境温度差过大。
图3气道(表面)
2.5
粗大晶粒coarsegrain 在宏观组织上出现的均匀或不均匀的、超出晶粒标准规定的大晶粒(如图4)。粗大晶粒组织具有
很强的各向异性:冷轧后表面出现白色条状缺陷,再结晶退火后晶粒易长大。
主要产生原因: a)熔体过热; b)结晶前沿温度梯度过大; c) 液面过低; d) 熔体在炉内停留时间过长; e) 晶粒细化效果不良。
2
GB/T26492.2—2011
图4五级大晶粒(表面)
2.6
晶粒不均 unevengrains 同一铸轧带不同区域晶粒大小有明显差异的现象(如图5)。晶粒不均有两种形式:一种为同一表
面不同区域晶粒大小不同,另一种为上下表面晶粒大小不同。
主要产生原因:晶粒不均是由于在铸嘴出口处结晶条件差异所致。
图5晶粒不均(混合酸洗后表面)
2.7
表面偏析条纹surfacesegregation 铸轧带表面点状缺陷集聚成带状,纵贯铸轧带全长(如图6)。未经浸蚀时缺陷不易发现,缺陷部位
反光性稍差,较暗;经高浓度混和酸或碱浸蚀后发黑。显微组织为两相共晶组织,缺陷部位化合物比正常部位明显增多,其中Si、Fe、Cu等与铝形成共晶转变的元素含量升高,而与铝形成包晶转变的Ti的含量则明显降低。表面偏析条纹是一种逆偏析。
主要产生原因:供料嘴的唇缘损坏、脱落或挂渣。
图6表面偏析条纹
2.8
中心层(线)偏析intermediatelayersegregation 铸轧带中,最终凝固的中心层附近集中了不平衡过剩组合物的现象(如图7)。中心层(线)偏析量
随合金元素含量的增加或铸轧速度的提高而增加。在轧辊压力作用下,富集合金元素的液态铝沿枝晶
3
GB/T26492.2—2011
间隙,从较冷区挤到中部较热区(即所谓孔道效应),全部凝固后在中部形成共晶,局部还可能出现过共晶。
主要产生原因: a)铸轧速度过快; b)合金元素含量高; c)铸轧区过小。
2
图7中心层(线)偏析
2.9
重熔斑纹 remeltingmottle 铸轧时,铸造区铝凝壳发生重熔,在铸轧带表面形成皱纹或斑纹的现象。这种缺陷多以周期性横向
皱纹形式出现,严重时可见成层,甚至出现类似偏析浮出物的斑点。重熔斑纹实际上是一种逆偏析。偏析区内组织粗大,中间化合物大且集中,破坏了铸轧带表面组织的均匀性。
主要产生原因: a)熔体温度过高; b)铸轧速度快; c)凝壳薄; d) 铸轧辊局部导热性能差; e) 供料嘴组装及流场分布不良,熔体温度不均; f) 铸轧机振动等。
2.10
夹杂inclusion 铸轧带内含有的炉渣、熔剂、各种耐火材料碎块、金属氧化物及其他杂物。夹杂形貌多种多样,多呈
黑色或耐火材料的颜色,形状不规则。
主要产生原因: a)熔体不干净; b)精炼、过滤效果不佳或过滤片损坏; c)料嘴内部保温材料脱落; d)液面波动大,氧化膜带入。
2.11
表面纵向条纹 surfacelongitudinal streak 铸轧带表面沿轧制方向出现的有一定色差没有深度的条纹,一般贯穿整个纵向板面。 主要产生原因: a)嘴辊间隙小,铸嘴前沿摩擦辊面; b)铸嘴局部破损; c) 铸嘴前沿挂渣;
4
GB/T26492.2—2011
d)嘴腔局部堵塞; e) 轧辊辊面磨削质量不好,轧辊辊面或牵引辊辊面有划痕。
2.12
横向波纹 crosswisewaviness 铸轧时,嘴辊间隙处包覆铝液和氧化膜周期振荡并发生破裂,使带坏表面的凝固速度周期变化,枝
晶间距周期变化。经过高浓度混和酸或碱浸蚀后出现较粗大的树枝晶组织或较粗大的化合物颗粒与正常晶粒组织间隔的现象(如图8)。
主要产生原因: a)铸轧速度过快; b) 供料嘴与轧辊间隙较大; c)冷却强度过大; d) 前箱液面高度过高或不稳定; e) 机架、供料系统振动等致使铸嘴前沿弯液面在辊面和铝凝固壳之间波动。
图8 8横向波纹(酸侵蚀后)
2.13
粘辊roll sticking 铸轧时,铸轧带局部或整个带宽度上在离开轧辊中心连线后不能与轧辊分离,而由卷取张力强行分
离,使带坏出现表面粗糙、翘曲不平或横纹等缺陷的现象。
主要产生原因: a)熔体温度偏高; b) 铸轧速度快; c) 冷却强度低; d) 铸轧辊辊面温度不均; e) 铸轧辊表面粗糙度不适宜; f) 清辊器或润滑介质欠佳; g) 卷取张力小。
2.14
层间粘伤 5stickingtrace 铸轧带被卷取时层与层之间发生的局部粘连的现象,强行展开后,粘连区呈现片状、条状或点状伤
痕。发生粘连的两接触表面对应点上的伤痕相互吻合。
主要产生原因: a)铸轧速度太快;
5
GB/T26492.2—2011
b)铸轧带温度过高; c)卷取张力过大。
2. 15
辊印rollmark 由于轧辊辊面、牵引辊或导向辊辊面损伤或粘铝[如图9a)]、铸轧辊龟裂[如图9b)等印在铸轧
带表面呈现周期性出现的凸起或凹下的现象。
注:铸轧辊龟裂是由于使用时间长,承受交变热应力、机械应力、以及辊面与高温熔体发生一系列物理化学作用引
起的。
b)铸轧辊龟裂造成的辊印
a)辊印缺陷
图9辊印
2.16
非金属压入rolled-indirt 压人铸轧带表面的非金属夹杂物。非金属压入物呈点状、长条状或不规则形状,颜色随压人物不同
而不同。
主要产生原因: a)供料嘴唇掉渣或局部脱落; b) 清辊器毛毡脱落; c)[ 喷涂介质在辊面堆积; d) 非金属异物经输送辊道或卷取压入铸轧带表面。
2. 17
金属压入rolled-inmetal 铸轧带表面嵌入金属碎片或碎屑。 主要产生原因: a)铸轧辊粘铝或热状态铸轧带坏粘上外来金属碎屑未及时清除; b)铸轧带在线铣边时铝屑未吸取干净,压人表面。
2.18
机械损伤 5mechanicaldamage 铸轧带表面出现的划伤(断续或连续的单条沟线状缺陷。一般是由尖锐物与产品接触并相对移动
所致)、擦伤(成束或成片细小的划伤。一般是物体的棱与面或面与面接触后发生相对移动或错动所致)、碰伤和压伤(产品与其他物体互相碰撞或挤压形成的一个或多个伤痕)等。
主要产生原因: a)设备和工具有突出尖锐角或粘铝; b)导辊与移动不同步;
6