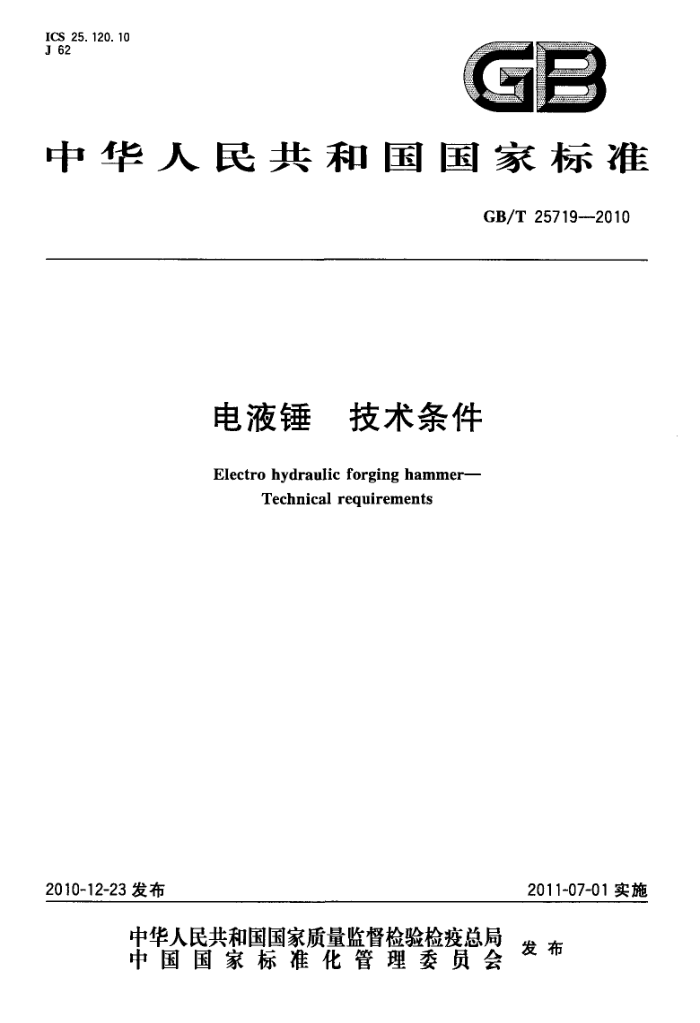
ICS 25.120.10 J 62
中华人民共和国国家标准
GB/T25719---2010
电液锤 技术条件 Electro hydraulic forging hammer
Technical requirements
2011-07-01实施
2010-12-23发布
中华人民共和国国家质量监督检验检疫总局
中国国家标准化管理委员会 发布
GB/T 25719—2010
前言
本标准的附录A为规范性附录。 本标准由中国机械工业联合会提出。 本标准由全国锻压机械标准化技术委员会(SAC/TC220)归口。 本标准起草单位:安阳锻压机械工业有限公司、太原科技大学、深圳市华测检测技术股份有限公司。 本标准主要起草人:王卫东、李永堂、刘福海、朱平、韩涛、马淑叶、王爱娟、李波、常民。
H
GB/T25719—2010
电液锤技术条件
1范围
本标准规定了电液锤的技术要求、试验方法、检验规则及标志、包装、运输和贮存。 本标准适用于电液锤(包括有砧座式自由锻电液锤、模锻电液锤、数控模锻电液锤),也适用于改造
蒸-空锻锤的电液动力头。 2规范性引用文件
下列文件中的条款通过本标准的引用而成为本标准的条款。凡是注日期的引用文件,其随后所有的修改单(不包括勘误的内容)或修订版均不适用于本标准,然而,鼓励根据本标准达成协议的各方研究是否可使用这些文件的最新版本。凡是不注日期的引用文件,其最新版本适用于本标准。
GB/T191 包装储运图示标志(GB/T191-2008,ISO780:1997MOD) GB/T3766 5液压系统通用技术条件(GB/T3766—2001,eqvISO4413:1998) GB5226.1 机械电气安全机械电气设备第1部分:通用技术条件(GB5226.1-2008,
IEC60204-1:2005,IDT)
GB/T6576 机床润滑系统(GB/T6576-2002,eqvISO5170:1977) GB/T7932 气动系统通用技术条件(GB/T7932-2003,ISO4414:1998,IDT) GB/T 9969 工业产品使用说明书总则 GB/T10923 锻压机械精度检验通则 GB/T13306 标牌 GB17120 锻压机械 安全技术条件 GB/T23281 锻压机械噪声声压级测量方法(GB/T23281—2009,ISO11202:1995,NEQ) GB/T25718 电液锤型式与基本参数 JB/T1829 锻压机械通用技术条件 JB/T5775 锻压机械灰铸铁件技术条件 JB/T8356.1 机床包装技术条件 JB/T8467 锻钢件超声波探伤方法 JB/T8609 锻压机械焊接件技术条件 JB/T9954 锻压机械液压系统清洁度
3技术要求 3.1基本要求 3.1.1电液锤应符合JB/T1829和本标准的规定,并按经规定程序批准的图样及技术文件制造。 3.1.2铸铁件应符合JB/T5775的规定,焊接件应符合JB/T8609的规定。 3.1.3使用说明书应符合GB/T9969的规定。 3.1.4重要锻件应进行超声波探伤(如锤杆、锤头、砧块等),超声波探伤应符合JB/T8467的规定,并做好有关记录。 3.1.5电液锤的随机备件、附件应能互换,并符合有关技术文件的规定。 3.1.6电液动力头和机身所用的所有紧固件应采取防松措施,动力头与机身应有减震垫。
1
GB/T25719—2010
3.2型式与基本参数
电液锤的型式与基本参数应符合GB/T25718的规定。用户有特殊要求的除外。
3.3性能 3.3.1电液锤操作系统应安全可靠、灵活自如。 3.3.2自由锻电液锤、模锻电液锤应能实现锤头提升、悬置、重击、轻击、慢降、压紧和急停收锤等工作规范;改变锤头的提升高度,即可改变电液锤的打击能量;数控模锻电液锤能实现提升、重击、轻击和慢降等工作规范,通过调整打击阀闭合时间的长短,可精确控制电液锤的打击能量,以满足锻造工艺要求的使用功能。数控模锻电液锤打击能量控制精确度为士3%。 3.3.3电液锤的运动部件,如锤头系统(含锤头和锤杆)应在有效行程内灵活自如,无卡阻现象出现。 3.3.4自由锻电液锤、模锻电液锤在正常的使用中,提锤应能使锤头从闭合位置上升至行程高度的任意位置;如不立即进行打击,允许悬置锤头有微量滑动,但5s内的滑动距离不应大于10mm。 3.3.5自由锻电液锤、模锻电液锤在实施打击的瞬间,如发现误操作应能立即实施急停收锤,此防误操作工作规范只在应急时使用。 3.3.6数控模锻电液锤在慢降过程中应为点动动作,停止状态下5s内滑动距离不应大于5mm。 3.3.7应设置回程限止装置,以保证锤头系统在最大回程速度下无刚性冲撞。 3.3.8用户有要求时,模锻电液锤、数控模锻电液锤应能带上顶料装置,顶料力应不小于锤头重力的 10倍。 3.3.9数控模锻电液锤打击能量的调整应方便。更换不同模具后,将模具闭合高度参数重新输入,打击能量应能自动调整。 3.4外观 3.4.1电液锤的外观质量应符合JB/T1829的规定。 3.4.2铸件外部表面清除型砂、粘砂、结疤、多肉以后,用500mm的直尺检查不加工表面的平面度,偏差不应大于2.5mm。 3.4.3外部不加工表面清除铁锈、型砂与油污后,根据表面情况打底、抹腻子、涂漆。砧座及埋人件只涂防锈漆。铆焊件可不抹腻子。腻子层厚度不应大于1.5mm,局部加厚处不应大于3mm。 3.4.4机器表面不应有图样未规定的凸起或凹陷和粗糙不平,用板料加工的盖不应出现边缘不整齐的现象,其结合缝隙不应超过表1规定。
表 1
单位为毫米
零部件结合面的边沿尺寸
允许错偏量
≤500 >500≤1000 >1 000
1 2 3
注:边沿尺寸系指直径或相应边长。 3.4.5电气、润滑、液压、冷却管道外露部分应布置紧凑,排列整齐,且用管夹固定,管子不应扭曲折叠,在弯曲处应圆滑,不应压扁或打折。 3.5装配 3.5.1装配质量应符合JB/T1829的规定。 3.5.2电气、液压、气动管路应固定牢固,不应与运动部件发生摩擦。 3.5.3装配前应清洗管道、油管及充液装置。 3.5.4全部液压、气动管路、管接头、法兰以及其他固定和活动连接均应连接可靠,密封良好,不应有油、气渗滑现象。 2
GB/T25719—2010
3.5.5电液动力头重要固定结合面应紧密贴合,预紧后用0.05mm塞尺检查,只允许局部塞人,其塞人部分长度累计不应大于可检长度的10%。 3.6液压系统 3.6.1液压系统应符合GB/T3766的规定。 3.6.2液压系统油箱应有合理容积,油箱不应有渗漏现象;所配备的油液冷却器应保证油温不高于 60℃. 3.6.3液压系统清洁度应符合JB/T9954的规定。 3.6.4液压系统中应设置滤油器。 3.7润滑系统 3.7.1润滑系统应符合GB/T6576的规定。 3.7.2重要的摩擦部位的润滑应采用集中润滑系统,只有当不能采用集中润滑系统时才可采用分散润滑装置。 3.8气动系统 3.8.1气动系统的结构与安全要求应符合GB/T7932的规定。 3.8.2气缸、气罐和蓄能器的充气介质应使用氮气。 3.9电气设备
电气设备应符合GB5226.1的规定。 3.10噪声
空运转时的声音应正常,其A计权噪声声压级不应大于90dB(A)。测量方法应符合GB/T23281 的规定。 3.11安装精度 3.11.1 安装精度的检验应符合GB/T10923的规定, 3.11.2 自由锻电液锤的整体安装精度应符合表2的规定。
表 2
单位为毫米
序号 1 2 3 4 5
检验项目砧座水平度
允许偏差
前后、左右方向均不超过0.5/1000 前后、左右方向偏差均不超过0.5/1000 前后、左右偏差均不超过0.5/1000 前后、左右方向均不超过0.5/1000
锤架上支承面对基础平行度工作缸对基础的垂直度
锤头对砧子的平行度锤头与锤架导轨的双面间隙
1~2
3.11.3 模锻电液锤的整体安装精度应符合表3的规定。
表 3
允许偏差/mm
序号
检验项目
模锻电液锤的公称打击能量/kJ >50~125 >125~250
>250
≤50 ≤0.20/1000 ≤0.20/1000 ≤0.20/1000 ≤0.20/1000
锤头在最下位置时,锤头燕尾槽底面对模座燕尾槽底面的平行度锤头在最下位置时,锤头燕尾槽侧面对模座燕尾槽侧面的偏移锤头在最下位置时,锤头中心对模座键槽中心的偏移
1
≤0.30
0.50
0.80
≤0.80
2
≤3.00
≤1.50
≤2.00
≤3.00
3
3
GB/T25719-—2010
表3(续)
允许偏差/mm
序号
检验项目
模锻电液锤的公称打击能量/kJ >50~125 >125~250
≤50 ≤0.10/1000 ≤0.10/1000 ≤0.10/1000 ≤0.10/1000
>250
两锤架导轨的平行度锤头在最下位置时,锤头与锤架 单边 0.20~0.30 0.20~0.30 0.20~0.40 导轨侧
4
0. 25
4
双边 0.40~0.60 0.40~0.60 0.40~0.80 0.50~1.00
3.11.4 数控模锻电液锤的整体安装精度应符合表4的规定。
表 4
允许偏差/mm
序号
数控模锻电液锤的公称打击能量/kJ
检验项目
<50
>100~125
>125
>50~100
锤头在最下位置时,锤头燕尾槽底面对模座燕尾槽底面的平行度锤头在最下位置时,锤头燕尾槽侧面对模座燕尾槽侧面的偏移锤头在最下位置时,锤头中心对模座键槽中心的偏移两锤架导轨的平行度链头在最下位置时,锤头与锤架 单边 0.15~0.20 0.15~0.20 0.15~0.25 0.20~0.30 导轨侧隙
≤0.10/1000 ≤0.10/1000 ≤0.10/1000 ≤0.10/1000
1
≤0. 20
≤0.60
2
≤0.40
≤0.60
≤1. 00 ≤0.05/1000 ≤0.05/1000 ≤0.05/1000 ≤0.05/1000
≤1.50
≤2.00
≤2.00
3
4
5
双边 0.30~0.40 0.30~0.40 0.30~0.50 0.40~0.60
3.12 安全与防护 3.12.1 安全与防护应符合GB17120的规定。 3.12.2 :电液锤应有防止锤杆意外断裂而引起高压油喷泄的防护装置。 3.12.3 数控模锻电液锤应有防止锤头意外下落的安全销装置,安全销开关应与打击操作开关互锁。 3.12.4电液锤上有可能对人身和设备造成损伤的部分,应采取相应的安全防护措施和警示。 4 试验方法 4. 1 空运转试验 4.1.13 空运转试验时间不应少于2h。 4.1.2 在空运转试验时间内,连续试验时间不应小于1.5h。 4.1.31 试验时各部分应运转平稳,不应有不正常的尖叫声。 4.1.4 电机、油泵启动和停止试验,连续进行,不少于3次,应灵敏可靠。 4.1.5 电机、油泵空运转试验,不少于30min,应无异常。 4.1.6全行程提锤、慢降、锤头悬置试验,连续进行10次,应灵活、轻便、平稳、准确,无卡滞现象,无异常声响。提锤时锤头应能快速提升;自由锻电液锤、模锻电液锤锤头悬置试验时,锤头在任何位置都能停住;慢降时锤头应缓慢下落,慢降过程中锤头在任何位置可随时停住;操纵部件处于打击位置时,锤头能快速实现打击。 4.1.7按GB/T23281的规定测定噪声,其声压级不超过90dB(A)。 4.1.8 电液动力头的空运转试验,应在试验台架上进行。 4
GB/T25719—2010
4.2负荷运转试验 4.2.1试验在用户使用现场结合当时的锻件进行,可试锻两种典型锻件,使用功能应发挥正常。 4.2.2锤的打击能量采用敏粗铜柱法进行测量,试验用试件材料应符合附录A的规定。也可用典型粗工序所需锻击能量做比照性经验评定。 4.2.3其他技术要求应在两个班次的连续工作后进行评定。 4.2.4实际打击能量按下列公式计算:
E- 1
2 mo2
( 1 )
式中: E- - 打击能量,单位为焦耳(J);
落下部分实际质量,单位为千克(kg);上下砧块或上下模块闭合时的速度,单位为米每秒(m/s)。
m U
4.2.5 自由锻电液锤、模锻电液锤最大打击能量不应小于GB/T25718中规定的公称打击能量。 4.2.6 试验数控模锻电液锤打击能量控制精确度 5 检验规则 5. 1 电液锤的检验分为出厂检验和型式检验。 5.2 每台电液锤都应进行出厂检验。检验合格并填写产品合格证明书后才能出厂。 5.3 对于新产品、更新产品(包括结构、主要零件、工艺有较大改变的产品),应进行型式检验。 5. 4 电液锤出厂检验和型式检验的检验项目应符合表5的规定。
表 5
检验类别
技术要求 3. 1 3. 2 3. 3 3. 4 3. 5 3. 6 3. 7 3. 8 3. 9 3. 10 3. 11 3.12 4, 1 4. 2
检验方法直接测量和检查直接测量
检验项目
出厂检验
型式检验 + + +
基本要求基本参数性能外观装配液压系统润滑系统气动系统电气设备噪声安装精度安全与防护空运转试验负荷运转试验注:“十”表示进行检验,“一”表示不进行检验。
+ + + + + + + + + + + + +
直接测量目测和直接测量直接测量和检查直接测量和检查直接测量和检查直接测量和检查直接测量和检查
+ + + + + + + + + + +
直接测量直接测量和检查直接测量和检查
4. 1 4. 2
6标志、包装、运输和存 6.1 电液锤的各类标记和标牌应固定在锤身上明显的位置。
5
GB/T 25719--2010
6.2标牌的型式与尺寸应符合GB/T13306的规定,在标牌上应标明:
a)制造企业的名称; b) 产品名称; c) 产品型号; d) 生产日期或出厂日期; e) 产品编号。
6.3电液锤的包装应符合JB/T8356.1的规定 6.4每台电液锤均应随机附带下列文件:
a) 合格证明书: b) )装箱单; c)使用说明书。
6.5电液锤的包装应符合水路、陆路运输的规定,在运输时不应产生机械性损害;包装运输标志应符合 GB/T191的规定。 6.6电液锤应在干燥、通风、防雨的地方贮存。
6
ICS 25.120.10 J 62
中华人民共和国国家标准
GB/T25719---2010
电液锤 技术条件 Electro hydraulic forging hammer
Technical requirements
2011-07-01实施
2010-12-23发布
中华人民共和国国家质量监督检验检疫总局
中国国家标准化管理委员会 发布
GB/T 25719—2010
前言
本标准的附录A为规范性附录。 本标准由中国机械工业联合会提出。 本标准由全国锻压机械标准化技术委员会(SAC/TC220)归口。 本标准起草单位:安阳锻压机械工业有限公司、太原科技大学、深圳市华测检测技术股份有限公司。 本标准主要起草人:王卫东、李永堂、刘福海、朱平、韩涛、马淑叶、王爱娟、李波、常民。
H
GB/T25719—2010
电液锤技术条件
1范围
本标准规定了电液锤的技术要求、试验方法、检验规则及标志、包装、运输和贮存。 本标准适用于电液锤(包括有砧座式自由锻电液锤、模锻电液锤、数控模锻电液锤),也适用于改造
蒸-空锻锤的电液动力头。 2规范性引用文件
下列文件中的条款通过本标准的引用而成为本标准的条款。凡是注日期的引用文件,其随后所有的修改单(不包括勘误的内容)或修订版均不适用于本标准,然而,鼓励根据本标准达成协议的各方研究是否可使用这些文件的最新版本。凡是不注日期的引用文件,其最新版本适用于本标准。
GB/T191 包装储运图示标志(GB/T191-2008,ISO780:1997MOD) GB/T3766 5液压系统通用技术条件(GB/T3766—2001,eqvISO4413:1998) GB5226.1 机械电气安全机械电气设备第1部分:通用技术条件(GB5226.1-2008,
IEC60204-1:2005,IDT)
GB/T6576 机床润滑系统(GB/T6576-2002,eqvISO5170:1977) GB/T7932 气动系统通用技术条件(GB/T7932-2003,ISO4414:1998,IDT) GB/T 9969 工业产品使用说明书总则 GB/T10923 锻压机械精度检验通则 GB/T13306 标牌 GB17120 锻压机械 安全技术条件 GB/T23281 锻压机械噪声声压级测量方法(GB/T23281—2009,ISO11202:1995,NEQ) GB/T25718 电液锤型式与基本参数 JB/T1829 锻压机械通用技术条件 JB/T5775 锻压机械灰铸铁件技术条件 JB/T8356.1 机床包装技术条件 JB/T8467 锻钢件超声波探伤方法 JB/T8609 锻压机械焊接件技术条件 JB/T9954 锻压机械液压系统清洁度
3技术要求 3.1基本要求 3.1.1电液锤应符合JB/T1829和本标准的规定,并按经规定程序批准的图样及技术文件制造。 3.1.2铸铁件应符合JB/T5775的规定,焊接件应符合JB/T8609的规定。 3.1.3使用说明书应符合GB/T9969的规定。 3.1.4重要锻件应进行超声波探伤(如锤杆、锤头、砧块等),超声波探伤应符合JB/T8467的规定,并做好有关记录。 3.1.5电液锤的随机备件、附件应能互换,并符合有关技术文件的规定。 3.1.6电液动力头和机身所用的所有紧固件应采取防松措施,动力头与机身应有减震垫。
1
GB/T25719—2010
3.2型式与基本参数
电液锤的型式与基本参数应符合GB/T25718的规定。用户有特殊要求的除外。
3.3性能 3.3.1电液锤操作系统应安全可靠、灵活自如。 3.3.2自由锻电液锤、模锻电液锤应能实现锤头提升、悬置、重击、轻击、慢降、压紧和急停收锤等工作规范;改变锤头的提升高度,即可改变电液锤的打击能量;数控模锻电液锤能实现提升、重击、轻击和慢降等工作规范,通过调整打击阀闭合时间的长短,可精确控制电液锤的打击能量,以满足锻造工艺要求的使用功能。数控模锻电液锤打击能量控制精确度为士3%。 3.3.3电液锤的运动部件,如锤头系统(含锤头和锤杆)应在有效行程内灵活自如,无卡阻现象出现。 3.3.4自由锻电液锤、模锻电液锤在正常的使用中,提锤应能使锤头从闭合位置上升至行程高度的任意位置;如不立即进行打击,允许悬置锤头有微量滑动,但5s内的滑动距离不应大于10mm。 3.3.5自由锻电液锤、模锻电液锤在实施打击的瞬间,如发现误操作应能立即实施急停收锤,此防误操作工作规范只在应急时使用。 3.3.6数控模锻电液锤在慢降过程中应为点动动作,停止状态下5s内滑动距离不应大于5mm。 3.3.7应设置回程限止装置,以保证锤头系统在最大回程速度下无刚性冲撞。 3.3.8用户有要求时,模锻电液锤、数控模锻电液锤应能带上顶料装置,顶料力应不小于锤头重力的 10倍。 3.3.9数控模锻电液锤打击能量的调整应方便。更换不同模具后,将模具闭合高度参数重新输入,打击能量应能自动调整。 3.4外观 3.4.1电液锤的外观质量应符合JB/T1829的规定。 3.4.2铸件外部表面清除型砂、粘砂、结疤、多肉以后,用500mm的直尺检查不加工表面的平面度,偏差不应大于2.5mm。 3.4.3外部不加工表面清除铁锈、型砂与油污后,根据表面情况打底、抹腻子、涂漆。砧座及埋人件只涂防锈漆。铆焊件可不抹腻子。腻子层厚度不应大于1.5mm,局部加厚处不应大于3mm。 3.4.4机器表面不应有图样未规定的凸起或凹陷和粗糙不平,用板料加工的盖不应出现边缘不整齐的现象,其结合缝隙不应超过表1规定。
表 1
单位为毫米
零部件结合面的边沿尺寸
允许错偏量
≤500 >500≤1000 >1 000
1 2 3
注:边沿尺寸系指直径或相应边长。 3.4.5电气、润滑、液压、冷却管道外露部分应布置紧凑,排列整齐,且用管夹固定,管子不应扭曲折叠,在弯曲处应圆滑,不应压扁或打折。 3.5装配 3.5.1装配质量应符合JB/T1829的规定。 3.5.2电气、液压、气动管路应固定牢固,不应与运动部件发生摩擦。 3.5.3装配前应清洗管道、油管及充液装置。 3.5.4全部液压、气动管路、管接头、法兰以及其他固定和活动连接均应连接可靠,密封良好,不应有油、气渗滑现象。 2
GB/T25719—2010
3.5.5电液动力头重要固定结合面应紧密贴合,预紧后用0.05mm塞尺检查,只允许局部塞人,其塞人部分长度累计不应大于可检长度的10%。 3.6液压系统 3.6.1液压系统应符合GB/T3766的规定。 3.6.2液压系统油箱应有合理容积,油箱不应有渗漏现象;所配备的油液冷却器应保证油温不高于 60℃. 3.6.3液压系统清洁度应符合JB/T9954的规定。 3.6.4液压系统中应设置滤油器。 3.7润滑系统 3.7.1润滑系统应符合GB/T6576的规定。 3.7.2重要的摩擦部位的润滑应采用集中润滑系统,只有当不能采用集中润滑系统时才可采用分散润滑装置。 3.8气动系统 3.8.1气动系统的结构与安全要求应符合GB/T7932的规定。 3.8.2气缸、气罐和蓄能器的充气介质应使用氮气。 3.9电气设备
电气设备应符合GB5226.1的规定。 3.10噪声
空运转时的声音应正常,其A计权噪声声压级不应大于90dB(A)。测量方法应符合GB/T23281 的规定。 3.11安装精度 3.11.1 安装精度的检验应符合GB/T10923的规定, 3.11.2 自由锻电液锤的整体安装精度应符合表2的规定。
表 2
单位为毫米
序号 1 2 3 4 5
检验项目砧座水平度
允许偏差
前后、左右方向均不超过0.5/1000 前后、左右方向偏差均不超过0.5/1000 前后、左右偏差均不超过0.5/1000 前后、左右方向均不超过0.5/1000
锤架上支承面对基础平行度工作缸对基础的垂直度
锤头对砧子的平行度锤头与锤架导轨的双面间隙
1~2
3.11.3 模锻电液锤的整体安装精度应符合表3的规定。
表 3
允许偏差/mm
序号
检验项目
模锻电液锤的公称打击能量/kJ >50~125 >125~250
>250
≤50 ≤0.20/1000 ≤0.20/1000 ≤0.20/1000 ≤0.20/1000
锤头在最下位置时,锤头燕尾槽底面对模座燕尾槽底面的平行度锤头在最下位置时,锤头燕尾槽侧面对模座燕尾槽侧面的偏移锤头在最下位置时,锤头中心对模座键槽中心的偏移
1
≤0.30
0.50
0.80
≤0.80
2
≤3.00
≤1.50
≤2.00
≤3.00
3
3
GB/T25719-—2010
表3(续)
允许偏差/mm
序号
检验项目
模锻电液锤的公称打击能量/kJ >50~125 >125~250
≤50 ≤0.10/1000 ≤0.10/1000 ≤0.10/1000 ≤0.10/1000
>250
两锤架导轨的平行度锤头在最下位置时,锤头与锤架 单边 0.20~0.30 0.20~0.30 0.20~0.40 导轨侧
4
0. 25
4
双边 0.40~0.60 0.40~0.60 0.40~0.80 0.50~1.00
3.11.4 数控模锻电液锤的整体安装精度应符合表4的规定。
表 4
允许偏差/mm
序号
数控模锻电液锤的公称打击能量/kJ
检验项目
<50
>100~125
>125
>50~100
锤头在最下位置时,锤头燕尾槽底面对模座燕尾槽底面的平行度锤头在最下位置时,锤头燕尾槽侧面对模座燕尾槽侧面的偏移锤头在最下位置时,锤头中心对模座键槽中心的偏移两锤架导轨的平行度链头在最下位置时,锤头与锤架 单边 0.15~0.20 0.15~0.20 0.15~0.25 0.20~0.30 导轨侧隙
≤0.10/1000 ≤0.10/1000 ≤0.10/1000 ≤0.10/1000
1
≤0. 20
≤0.60
2
≤0.40
≤0.60
≤1. 00 ≤0.05/1000 ≤0.05/1000 ≤0.05/1000 ≤0.05/1000
≤1.50
≤2.00
≤2.00
3
4
5
双边 0.30~0.40 0.30~0.40 0.30~0.50 0.40~0.60
3.12 安全与防护 3.12.1 安全与防护应符合GB17120的规定。 3.12.2 :电液锤应有防止锤杆意外断裂而引起高压油喷泄的防护装置。 3.12.3 数控模锻电液锤应有防止锤头意外下落的安全销装置,安全销开关应与打击操作开关互锁。 3.12.4电液锤上有可能对人身和设备造成损伤的部分,应采取相应的安全防护措施和警示。 4 试验方法 4. 1 空运转试验 4.1.13 空运转试验时间不应少于2h。 4.1.2 在空运转试验时间内,连续试验时间不应小于1.5h。 4.1.31 试验时各部分应运转平稳,不应有不正常的尖叫声。 4.1.4 电机、油泵启动和停止试验,连续进行,不少于3次,应灵敏可靠。 4.1.5 电机、油泵空运转试验,不少于30min,应无异常。 4.1.6全行程提锤、慢降、锤头悬置试验,连续进行10次,应灵活、轻便、平稳、准确,无卡滞现象,无异常声响。提锤时锤头应能快速提升;自由锻电液锤、模锻电液锤锤头悬置试验时,锤头在任何位置都能停住;慢降时锤头应缓慢下落,慢降过程中锤头在任何位置可随时停住;操纵部件处于打击位置时,锤头能快速实现打击。 4.1.7按GB/T23281的规定测定噪声,其声压级不超过90dB(A)。 4.1.8 电液动力头的空运转试验,应在试验台架上进行。 4
GB/T25719—2010
4.2负荷运转试验 4.2.1试验在用户使用现场结合当时的锻件进行,可试锻两种典型锻件,使用功能应发挥正常。 4.2.2锤的打击能量采用敏粗铜柱法进行测量,试验用试件材料应符合附录A的规定。也可用典型粗工序所需锻击能量做比照性经验评定。 4.2.3其他技术要求应在两个班次的连续工作后进行评定。 4.2.4实际打击能量按下列公式计算:
E- 1
2 mo2
( 1 )
式中: E- - 打击能量,单位为焦耳(J);
落下部分实际质量,单位为千克(kg);上下砧块或上下模块闭合时的速度,单位为米每秒(m/s)。
m U
4.2.5 自由锻电液锤、模锻电液锤最大打击能量不应小于GB/T25718中规定的公称打击能量。 4.2.6 试验数控模锻电液锤打击能量控制精确度 5 检验规则 5. 1 电液锤的检验分为出厂检验和型式检验。 5.2 每台电液锤都应进行出厂检验。检验合格并填写产品合格证明书后才能出厂。 5.3 对于新产品、更新产品(包括结构、主要零件、工艺有较大改变的产品),应进行型式检验。 5. 4 电液锤出厂检验和型式检验的检验项目应符合表5的规定。
表 5
检验类别
技术要求 3. 1 3. 2 3. 3 3. 4 3. 5 3. 6 3. 7 3. 8 3. 9 3. 10 3. 11 3.12 4, 1 4. 2
检验方法直接测量和检查直接测量
检验项目
出厂检验
型式检验 + + +
基本要求基本参数性能外观装配液压系统润滑系统气动系统电气设备噪声安装精度安全与防护空运转试验负荷运转试验注:“十”表示进行检验,“一”表示不进行检验。
+ + + + + + + + + + + + +
直接测量目测和直接测量直接测量和检查直接测量和检查直接测量和检查直接测量和检查直接测量和检查
+ + + + + + + + + + +
直接测量直接测量和检查直接测量和检查
4. 1 4. 2
6标志、包装、运输和存 6.1 电液锤的各类标记和标牌应固定在锤身上明显的位置。
5
GB/T 25719--2010
6.2标牌的型式与尺寸应符合GB/T13306的规定,在标牌上应标明:
a)制造企业的名称; b) 产品名称; c) 产品型号; d) 生产日期或出厂日期; e) 产品编号。
6.3电液锤的包装应符合JB/T8356.1的规定 6.4每台电液锤均应随机附带下列文件:
a) 合格证明书: b) )装箱单; c)使用说明书。
6.5电液锤的包装应符合水路、陆路运输的规定,在运输时不应产生机械性损害;包装运输标志应符合 GB/T191的规定。 6.6电液锤应在干燥、通风、防雨的地方贮存。
6