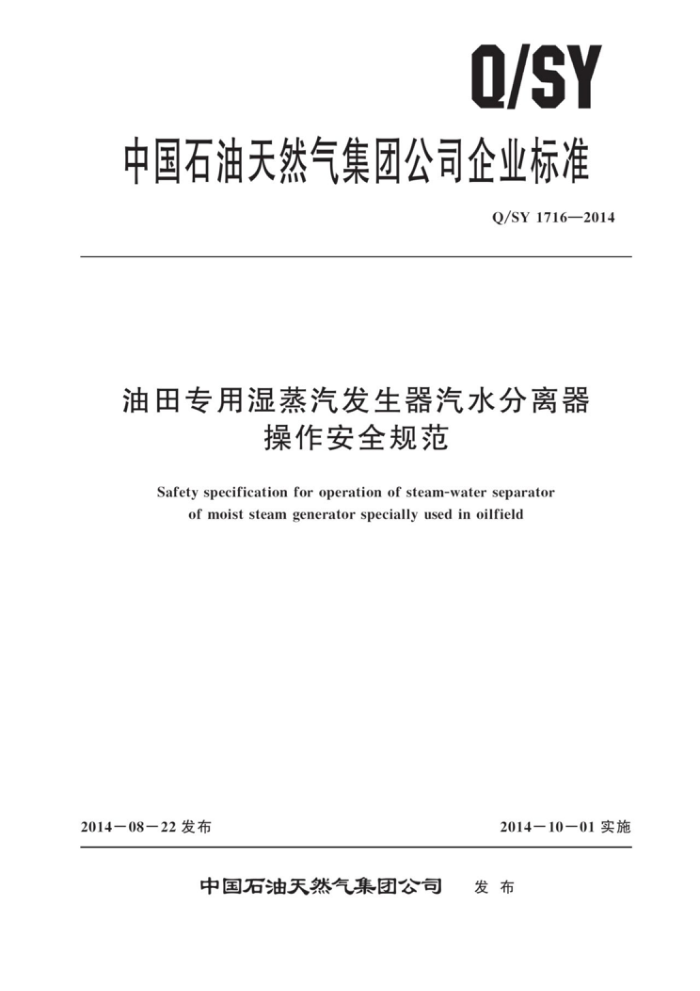
Q/SY
中国石油天然气集团公司企业标准
Q/SY 1716—2014
油田专用湿蒸汽发生器汽水分离器
操作安全规范
Safety specification for operation of steam-water separator
of moist steam generator specially used in oilfield
2014—08—22发布
2014一10一01实施
中国石油天然气集团公司 发布
Q/SY1716—2014
目 次
前言
1
范围 2 规范性引用文件 3 术语和定义 4 工艺原理 5 操作前准备 6 系统运行 7 系统停运 8 要求附录A(资料性附录) 汽水分离器工艺流程图附录B(资料性附录) 汽水分离器检查记录表
1
4
I
Q/SY1716—2014
前言
本标准按照GB/T1.1一2009《标准化工作导则 第1部分:标准的结构和编写》给出的规则起草。
本标准由中国石油天然气集团公司标准化委员会健康安全环保专业标准化技术委员会提出并归口。
本标准起草单位:中国石油天然气股份有限公司辽河油田分公司。 本标准主要起草人:郭崇华、郭静、韩树柏、李闪星、雷光明、柏长春、黄盛华、詹琪、杨海
涛、李冬毅、盖艳、苏雪丽。
II
Q/SY1716—2014
油田专用湿蒸汽发生器汽水分离器操作安全规范
1范围
本标准阐述了汽水分离器的工艺原理,规定了汽水分离器的操作前准备、系统运行、停运及
要求。
本标准适用于油田专用湿蒸汽发生器汽水分离器的操作。
2规范性引用文件
2
下列文件对于本文件的应用是必不可少的。凡是注日期的引用文件,仅注日期的版本适用于本文件。凡是不注日期的引用文件,其最新版本(包括所有的修改单)适用于本文件。
TSGR0004—2009固定式压力容器安全技术监察规程
3术语和定义
下列术语和定义适用于本文件。
3.1
汽水分离器steam-waterseparator 湿蒸汽发生器出口的汽水混合物经旋风分离器、百叶窗分离器的作用,将蒸汽中的细小水滴分离
出来,最终实现汽、水分离目的的装置 3. 2
旋风分离器 cycloneseparator 综合了离心分离、重力分离及膜式分离三项作用来进行汽水分离的元件。
3.3
分配器 distributor 为使进人每个旋风分离器的流量均勾,在筒体外设置的元件。
3. 4
百叶窗分离器 louverseparator 在旋风分离器上部蒸汽出口处设置的二次分离元件。
3.5
均汽孔板 orificeplateof eual steam 在旋风分离器人口处为防止汽、水流速不均匀而影响分离效果设置的挡板
3. 6
双色液位计 double color liquidmeter 用于监视液位设置的元件。
3. 7
液位调节阀 level control valve 为了调节液位设置的元件。
1
Q/SY1716—2014
4工艺原理
4.1原理
湿蒸汽发生器产生的汽水混合物在分配器及均汽孔板的作用下均匀、均速进入旋风分离器,通过
离心力和重力作用,将汽、水进行初步分离。另有少量水滴被螺旋上升的汽流带入旋风分离器上部的波形板,通过膜式分离作用进一步将汽、水分离,被分离出的水经过导流叶片及十字形挡板被导人至余热回收系统,含有细小水滴的蒸汽经过水平式百叶窗分离器的引出管道,连续不断地将汽、水引出,最终达到汽水分离的目的。
4.2 工艺流程
汽水分离器是由旋风分离器和配套工艺管道、阀门、仪表等构成的。其主要工艺流程参见附
录A。 4.3技术参数
技术参数如下: a) 仪表及附件环境温度:0℃~40℃。 b) 仪表及附件平均湿度:≤60%RH。 c) 人口蒸汽干度(化学分析):≥70%。 d) 排水温度:≤90℃。 e) 工作压力:3MPa~21MPa。 f) 动力电压:380V/50Hz三相交流电。 g) 设备第一次升温速度:≤50℃/min。
5操作前准备
5.1 汽水分离器试运前,必须完成各系统的分部试运和试验工作,主要包括水压试验、热工测量系统、控制调节系统、取样及冷却系统、余热利用系统 5.2系统通电前应做以下检查:
a) 按产品动力配线图检查各设备启动的额定电流。 b) 检查控制柜和动力盘对地绝缘。 c) 按产品控制原理图检查各回路接线情况。 d) 检查系统各元件。 e) 热工仪表校验合格,附属零配件及装置齐全。
5.3系统通电后应做以下检查:
a) 检查各系统回路及CPU程序。 b) 匹配一、二次仪表功能检查和调整分类系统的各项参数设置 c) 在有介质的动态情况下,检验各系统设限压力点的准确性。 d) 检验设限温度点、流量点、液位报警的准确性,可采取改变原设定值的方法,试验后再
复原。 e) 试验差压变送器。 f)试验压力变送器。
5.4汽水分离器操作风险辨识及控制措施见表1。 2
Q/SY1716—2014
表1汽水分离器风险辨识及控制措施
风险等级
风险削减与控制措施
设备设施名称
危害因素
危害事件
腐蚀、密封泄漏、丝杠打出 烫伤、物体打击 中度 按时巡检,更换维修或严禁超压使用
阀门
设备损坏,不能正常运行
一般 配电柜、电气线路避免受潮、高温
高温、受潮
自动控制系统 报警装置未定期校验或失效 设备损坏,不 中度
报警装置定期校验
能正常运行
触电
电线虚接,电缆老化绝缘不良
一般 检查电线无虚接,电缆老化及时更换
及时检查,确保保温良好及时巡检,确保保温良好无腐蚀;
水换热器 焊口开焊、无保温或保温破损 泄漏、烫伤
一般一般
烫伤物体打击、烫伤 中度管线甩龙、物体
保温破损腐蚀
设置高温高压安全标志牌定期检查、检测、维护,
未定期检测
发现问题及时处理定期检查、检测、维护,设置隔离区域,发现问题
汽水分离器
重大
腐蚀、管壁减薄变形
打击、人身伤害
及时处理
定期检测、维护,运行参数合理,管线无超压、
管线甩龙、物体打击、人身伤害
重大
超压、憨压
超温、冻堵
系统运行
6
汽水分离器第一次启动前应做如下水压试验:
6.1
将汽水分离器出口阀及各测量仪表前的针阀关闭。拆除安全阀,安全阀接口采用盲板封死。
a) b)
接通给水流程,当水充满汽水分离器后,缓慢升压至设计压力,确定无泄漏后继续升压至规定的试验压力,保压足够时间,然后降至设计压力,保压足够时间进行检查。检查期间压力应保持不变,以无渗漏、无可见变形、无异常响声为合格。 水压试验结束后,放净汽水分离器内积水。
c)
6.2 汽水分离器升压前,水位表高低水位标志应清晰,位置正确。 6.3 设备投运时,阀门应按如下步骤开启(参见附录A):
a) 缓慢开启汽水分离器入口阀门(阀门1、阀门2)、去井阀门(阀门3)、取样冷却系统阀门
(阀门13、阀门15)、蒸汽取样阀门(阀门12)、余热回收系统阀门(阀门9、阀门11) b) 缓慢关闭换热器旁通阀门(阀门10)。 c) 待液位建立起来后,开启换热器污水人口阀门(阀门5、阀门6)、换热器污水出口阀门(阀
门8)。 d) 缓慢关闭蒸汽出口旁通阀门(阀门4)。 e) 设备完全投入运行,调整换热器污水出口阀门(阀门8),使其阀门前压力达到1MPa
~2MPa。
6.4 根据双色液位计的液位显示,调整液位调节阀控制汽水分离器液面。 6.5按顺序依次打开各测量阀门及二次仪表开关,正常记录10min后,按设计要求调整流量,录取温度、压力、流量、干度、累计流量参数。 6.6 设备运行时,应悬挂高温高压警示标识,安全附件灵活好用,各部流程保温完好。控制室内照
3
Q/SY1716—2014
明良好,能监视设备水位。岗位人员正确劳保着装,按巡检路线每小时检查一次,记录相关参数(检查记录表参见附录B)。 6.7运行途中停运再投运,执行6.2~6.6。
7系统停运 7. 1 1正常停运
如图A.1所示,缓慢开启蒸汽出口旁通阀门、余热回收系统旁通阀门(阀门4、阀门10),关闭汽水分离器出、入口阀门(阀门1、阀门3)及余热回收出、入口阀门(阀门9、阀门11)。缓慢开启排污阀门(阀门14),将污水排掉。 7.2紧急停运
如图A.1所示,缓慢开启蒸汽出口旁通阀门(阀门4),关闭汽水分离器出、入口阀门(阀门1、 阀门3)。缓慢开启排污阀门(阀门14),将污水排掉。 7.3长期停运 7.3. 1 汽水分离器停运时间超过30d,采用除氧水充满设备,关闭所有进出口阀门。 7.3.2 如汽水分离器冬季停运,可采取以下方法进行防冻:
a) 每小时循环走水一次,每次走水时间为10min。 b) 排空所有管线内积水,采用压风车进行吹扫置换。 c) 缠绕电加热带并保温
8要求
8.1装置要求 8. 1. 1 1汽水分离器出厂
制造单位应向用户提供以下技术文件和资料:
竣工图纸,主要包括总图、工艺流程图、设备基础条件图、动力及控制原理图和管线布置
a)
图。如在原蓝图上修改则应有修改人、技术审核人确认标记
b) 产品质量证明书,主要包括出厂合格证、材料质量证明、焊接质量证明和水压试验记录。 c) 特种设备监督检验证明书。 d) 汽水分离器安装使用说明书。 e) 各项保护装置整定值。 f)辅助配件使用说明书。 g) 自动控制程序及用户密码
8.1. 2 2汽水分离器安装
汽水分离器在安装前,安装单位应向使用登记机关书面告知。安装过程中,应依据设计图纸有关要求进行,安装过程如有变动应征得设计、制造、使用单位同意,并提供以下安装施工方案:
a) 施工单位、技术人员、特种作业人员资格,施工机具、检测设备情况。 b) 施工方案编制的依据 c)工程总量及分项工程明细目录。
4