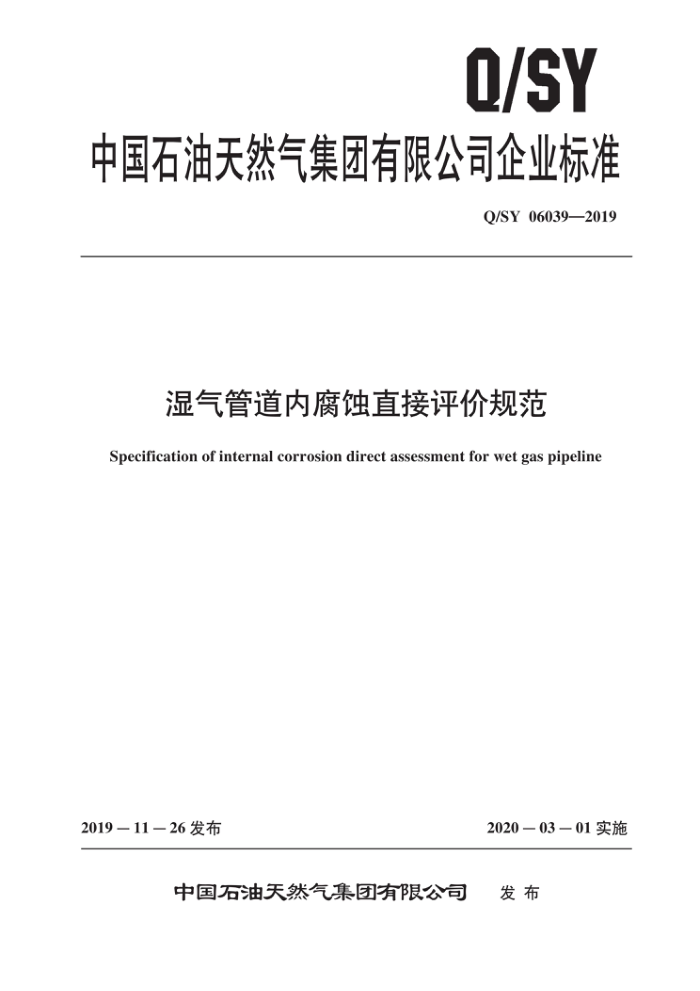
Q/SY
中国石油天然气集团有限公司企业标准
Q/SY 06039—2019
湿气管道内腐蚀直接评价规范
Specification of internal corrosion direct assessmentforwet gas pipeline
2019-11—26发布
2020-03-01实施
中国石油天然气集团有限公司 发布
Q/SY06039—2019
目 次
.ⅡI
前言
范围 2 规范性引用文件 3 术语和定义
一般规定预评价
4
5
5.1 预评价工作内容 5.2 资料收集 5.3 可行性分析 5.4 ICDA管段划分间接评价
6
6.1 间接评价工作内容 6.2 流动状态计算及ICDA子管段划分 6.3 内腐蚀预测模型确立 6.4 内腐蚀高风险点和开挖点的确定直接检测 7.1 直接检测工作内容 7.2 开挖检测 7.3 管道剩余强度评价 7.4 修正 8 后评价 8.1 后评价工作内容 8.2 有效性评价 8.3 确定再评价时间间隔 8.4 原因分析 8.5 提出维修维护建议记录和报告
7
9
9.1 记录 9.2 报告附录A(规范性附录) 管道预评价数据记录表格附录B(资料性附录) 常用内腐蚀预测模型主要考虑因素
10
Q/SY06039—2019
前言
本标准按照GB/T1.1一2009《标准化工作导则第1部分:标准的结构和编写》给出的规则起草。 本标准由西南油气田分公司、中国石油天然气股份有限公司勘探与生产分公司提出。 本标准由中国石油天然气集团有限公司标准化委员会石油石化工程建设专业标准化技术委员会归口。 本标准起草单位:西南油气田分公司、规划总院、长庆油田分公司。 本标准主要起草人:肖杰、宋彬、李珊、刘海峰、闫静、唐永帆、顾锡奎、罗锋、许道振、
谷坛、刘明、付勇、刘畅、舒洁、刘正雄、李媛、张纯、李曙华。
II
Q/SY06039—2019
湿气管道内腐蚀直接评价规范
1范围
本标准规定了湿气管道内腐蚀直接评价的方法。 本标准适用于输送湿气且未进行内防腐的钢质管道的内腐蚀直接评价。
规范性引用文件
2
下列文件对于本文件的应用是必不可少的。凡是注日期的引用文件,仅注日期的版本适用于本文
件。凡是不注日期的引用文件,其最新版本(包括所有的修改单)适用于本文件。
SY/T0087.1钢质管道及储罐腐蚀评价标准第1部分:埋地钢质管道外腐蚀直接评价 SY/T0087.2 钢质管道及储罐腐蚀评价标准 埋地钢质管道内腐蚀直接评价 SY/T 0546 腐蚀产物的采集与鉴定技术规范 SY/T 6477 含缺陷油气管道剩余强度评价方法 Q/SY01023 油气集输管道和厂站完整性管理规范
3 术语和定义
下列术语和定义适用于本文件。
3.1
湿气 wetgas 含有可凝液态烃或游离水或运行温度低于其露点温度,且标况下液相含量低于5%(体积百分比)
的天然气。 3.2
内腐蚀直接评价internalcorrosiondirectassessment(ICDA)种评价管壁内腐蚀程度的方法,由预评价、间接评价、直接检测和后评价四个步骤组成。
3.3
ICDA管段 ICDAregion 在管网或者管道系统中,由入口、出口、注入点、分输点等划分的具有材质、管径、输送介质及
防护措施相似的连续管段。 3.4
ICDA子管段 ICDA subregion ICDA管段内的具有相同流型的连续管段。
3.5
气液比 gas-liquid ratio (GLR) 标准状态下(0℃,101.325kPa),气体体积流量和液体体积流量的比例。
3.6
预评价 pre-assessment
1
Q/SY06039—2019
收集管道资料,确定管道是否符合ICDA执行条件,并进行ICDA管段划分。
3.7
间接评价indirectinspection 应用流动模型和内腐蚀预测模型评价管道腐蚀状况,确定ICDA子管段内腐蚀高风险位置和直接
检测位置。 3.8
直接检测directexamination 对间接评价确定的开挖点位置进行检测,确定是否有腐蚀引起的管壁损失及损失程度。
3.9
后评价postassessment 对预评价、间接评价、直接检测的过程和方法进行有效性评价,确认结果的有效性,确定腐蚀控
制和减缓计划及确定下次评价时间间隔的方法 3.10
持液率liquidholdup 气液两相流动过程中,液相的过流断面面积占总过流面积的比例。
3.11
表观气相流速 superficial gas velocity 管道运行温度和压力下,气体体积流量和管道横截面积之比。
3.12
表观液相流速 速superficial liquidvelocity 管道运行温度和压力下,液体体积流量和管道横截面积之比。
4一般规定
4.1ICDA应在Q/SY01023的指导下开展。 4.2ICDA是一个连续、循环、不断修正趋准的过程,通过识别评价发生腐蚀的部位和趋势,提出维护建议。 4.3ICDA前应根据管道的使用情况,编制工作方案,识别工作过程中的危险有害因素,并采取相关的安全防护措施。 4.4ICDA宜由工艺、腐蚀、检测等专业人员共同完成。 4.5可根据管道的运行情况和腐蚀状况开展ICDA,首次ICDA宜在管道投产初期3年内开展。 4.6调查、检测中需要室内分析、化验的项目应按规定取样,并应由专业实验室按相关标准规定的试验方法进行分析。 4.7管道内检测数据可作为确定开挖点位置的参考值,也可作为间接评价选点结果的验证对比数据, 4.8管道存在外腐蚀时,应按SY/T0087.1的规定执行。
5预评价 5.1 预评价工作内容
预评价主要工作内容应包括:资料收集、可行性分析、ICDA管段划分。 5.2资料收集 5.2.1 应按照A.1至A.10的要求,收集管道原始特征、设计参数、施工概况、运行参数、介质成分 2
Q/SY06039—2019
等情况。 5.2.2宜按照A.11、A.12的要求,收集管道维护维修历史、检测评价情况、腐蚀监测信息等情况。 5.2.3可根据管道的历史和输送介质情况,收集可能影响管道内腐蚀的其他资料。 5.3可行性分析 5.3.1 分析资料,确认收集的资料准确性。 5.3.2 收集的资料能否满足开展湿气管道内腐蚀直接评价的需求, 5.3.3开展内腐蚀直接评价的管道能否执行直接检测。 5.4 ICDA管段划分 5.4.1J 应依据收集的资料,在管道的属性数据和工况数据突变点划分ICDA管段。对于双向输送的管道,应分别在两个方向上划分管段。 5.4.2下列位置处宜为单独的一个ICDA管段划分点:
a)管道进气和出气处。 b)导致管道温度变化的换热器、加热炉处。 c)导致管道压力变化的压缩机处。 d)管道阀门、清管器收发装置等处 e)化学药剂注人处。 f)局部更换管道处。
5.4.3J 应对ICDA管段的边界进行确认。
5间接评价
6
6.1间接评价工作内容
间接评价主要工作内容应包括: a)流动状态计算及ICDA子管段划分。 b)内腐蚀模型确立。 c)内腐蚀高风险点和开挖点的确定。
6.2流动状态计算及ICDA子管段划分
6.2.1应使用气液两相流模型或商业软件对预评价中确定的ICDA管段的流动状态进行分析。 6.2.2气液两相流模型或商业软件的选取宜充分考虑管道结构特点、模型或软件的建模机理及适用范围,选取的模型或软件应能获取管道沿程流型、压力、温度、持液率、表观气相流速、表观液相流速及其他评价过程中所需的流动状态参数 6.2.3气液两相流模型或商业软件预测出的参数应与实际运行参数或历史运行参数进行对比分析并修正。 6.2.4管道弯头、地形连续起伏等局部管段内的流动状态可采用计算流体力学的方法进行计算。 6.2.5 应根据流动状态计算结果中的流型划分ICDA子管段。
6.3 内腐蚀预测模型确立 6.3.1内腐蚀预测模型用于确定同一子ICDA管段内不同部位的腐蚀风险。 6.3.2内腐蚀预测模型应基于管道内腐蚀机理分析,结合腐蚀预测模型的建模机理、主要影响因素及适用范围进行选取,也可自行建立。腐蚀预测模型选取可参照附录B。
3
Q/SY06039—2019 6.3.3自行建立内腐蚀预测模型时应选取合适的建模方法,通过试验或文献调研获取足够多的腐蚀数据样本,建立能够代表管道内腐蚀状况的预测模型 6.3.4加注缓蚀剂的管道,应在内腐蚀预测模型中添加修正因子 6.3.5内腐蚀预测模型应进行应用分析评价,根据已有的腐蚀数据样本对内腐蚀预测模型进行修正。 6.4内腐蚀高风险点和开挖点的确定
6.4.1应结合气液两相模型和内腐蚀预测模型的结果,判断内腐蚀高风险位置。内腐蚀高风险位置可按照以下准则确定:
a)根据内腐蚀预测模型计算的管道腐蚀速率较高点,ICDA子管段腐蚀速率的高点。 b)基于内腐蚀机理分析,根据内腐蚀主要影响因素中流动因素对腐蚀的影响权重,综合评价基
于流动的管道沿线内腐蚀风险,确定风险高点位置,
6.4.2 从内腐蚀高风险点中选择具备开挖检测条件的点作为直接检测位置。 6.4.3 3如果多个位置腐蚀机理相同,腐蚀严重程度也相同,可选择一个位置作为直接检测位置。 6.4.4采用钢/复合材料套筒修复过的位置不宜作为直接检测位置。 6.4.5 5每个ICDA管段直接检测位置不宜少于2处。
7直接检测 7.1直接检测工作内容
直接检测的主要工作内容应包括: a)开挖检测。 b)管道剩余强度评价。 c)修正。
7.2开挖检测
7.2.1直接开挖检测时,探坑的开挖、回填、外防腐层检测及管壁外腐蚀应按SY/T0087.1执行。
2应对开挖管段的内腐蚀特征进行详细的检测,宜根据管道具体情况和检测技术的特点选取超声
7.2.2
波测厚、超声波C扫描、X射线、超声导波、外漏磁检测等多种无损检测方法相结合的检测方法。 7.2.3应采用无损检测方法对壁厚损失进行定量评价,对开挖管段的腐蚀严重部位应进行内腐蚀尺寸检测,确定最大腐蚀深度、最大轴向长度和最大环向长度。 7.2.4采用超声波测厚对壁厚损失进行定量评价时,应多方位测量管道壁厚,确定轴向和环向壁厚损失,应按SY/T0087.2执行。 7.3管道剩余强度评价 7.3.1直接检测位置减薄超过壁厚的10%,应进行管道剩余强度评价。管道剩余强度评价应按SY/T 6477执行。 7.3.2对管道存在内腐蚀和外腐蚀并存的ICDA管段,应分别进行内腐蚀和外腐蚀的评价,然后进行评价结果的综合分析,确定ICDA管段的剩余强度。 7.3.3对每个ICDA管段的剩余强度评价结果进行综合分析,以评价得出的剩余强度最小值或最严重评价级别确定ICDA评价管段的最终评价结果 7.3.4开挖检测时,发现应力腐蚀、焊接缺陷等其他管材内部缺陷时,应采用其他相应的方法进行评价。 4