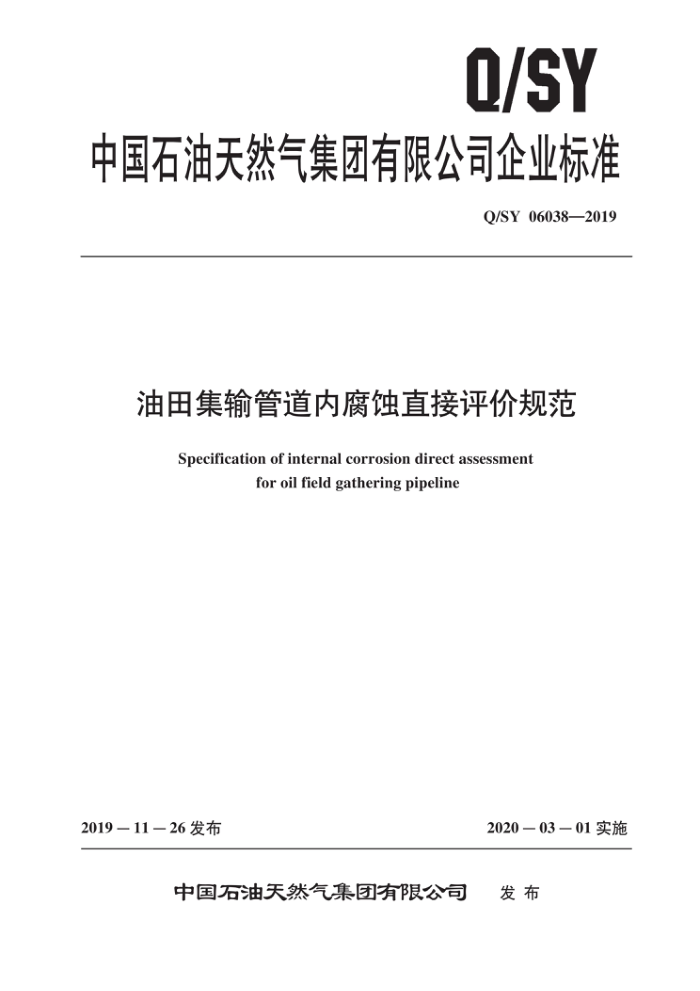
Q/SY
中国石油天然气集团有限公司企业标准
Q/SY 06038—2019
油田集输管道内腐蚀直接评价规范
Specification of internal corrosion direct assessment
for oil field gathering pipeline
2019-11—26发布
2020-03-01实施
中国石油天然气集团有限公司 发布
Q/SY06038—2019
目 次
.ⅡI
前言:
范围 2 规范性引用文件 3 术语和定义基本规定
4
预评价
5
5.1一般要求 5.2可行性分析 5.3 ICDA管段划分间接评价
6
6.1 一般要求 6.2 管道内流动状态计算与ICDA子管段划分 6.3 内腐蚀预测模型的确立 6.4 内腐蚀高风险点和开挖点的确定直接检测 7.1 -般要求 7.2 开挖检测 7.3 腐蚀管道的剩余强度评价 7.4 修正后评价
4
8
8.1 般要求 8.2 ICDA有效性评价 8.3 再评价时间间隔的确定 8.4 原因分析 8.5 提出维修维护建议记录和报告
9
4
9.1记录 9.2报告附录A(规范性附录) 各种预评价记录表格附录B(资料性附录) 影响腐蚀严重程度的因素附录C(资料性附录) 内腐蚀预测模型
6
11
Q/SY06038—2019
前言
本标准按照GB/T1.1一2009《标准化工作导则第1部分:标准的结构和编写》给出的规则起草。 本标准由中国石油规划总院、中国石油天然气股份有限公司勘探与生产分公司提出。 本标准由中国石油天然气集团有限公司标准化委员会石油石化工程建设专业标准化技术委员会归口。 本标准起草单位:规划总院、西南油气田分公司、长庆油田分公司。 本标准主要起草人:许道振、罗锋、刘明、付勇、闫静、肖杰、李岩、黎成、马相阳。
I
Q/SY06038—2019
油田集输管道内腐蚀直接评价规范
1范围
本标准规定了油田集输管道内腐蚀直接评价的方法。 本标准适用于输送包括油、气、水等在内的多相流动介质,且未进行内防腐的油田钢质管道内腐
蚀直接评价。
规范性引用文件
2
下列文件对于本文件的应用是必不可少的。凡是注日期的引用文件,仅注日期的版本适用于本文件。凡是不注日期的引用文件,其最新版本(包括所有的修改单)适用于本文件。
SY/T0087.1 钢质管道及储罐腐蚀评价标准 埋地钢质管道外腐蚀直接评价 SY/T 0087.2 钢质管道及储罐腐蚀评价标准埋地钢质管道内腐蚀直接评价 SY/T 0546 腐蚀产物的采集与鉴定技术规范 SY/T 6151 钢质管道管体腐蚀损伤评价方法 SY/T 6477 含缺陷油气管道剩余强度评价方法 SY/T10048 腐蚀管道评估推荐作法 Q/SY01023 油气集输管道和厂站完整性管理规范
3 术语和定义
下列术语和定义适用于本文件。
3.1
内腐蚀直接评价 ↑internalcorrosiondirectassessment(ICDA) 种评价管壁内腐蚀程度的方法,由预评价、间接评价、直接检测和后评价四个步骤组成。
3.2
ICDA管段 ICDAregion 在管网或者管道系统中,由入口、出口、注入点、分输点等划分的具有材质、管径、输送介质及
防护措施相似的连续管段。 3.3
ICDA子管段 ICDAsubregion ICDA管段内具有相同流型的连续管段。
3.4
预评价 pre-assessment 收集管道资料,确定管道是否符合ICDA执行条件,并进行ICDA管段划分。
3.5
间接评价indirectinspection
1
Q/SY06038—2019
应用流动模型和内腐蚀预测模型对管道腐蚀状况进行评价,确定管道内腐蚀高风险点并根据评价
结果在管段内推荐开挖检测点。 3.6
直接检测directexamination 对间接评价确定的开挖点位置进行检测,确定是否有腐蚀引起的管壁损失及损失程度。
3.7
后评价postassessment 对预评价、间接评价、直接检测的过程和方法进行有效性评价、确认结果有效性,确定腐蚀控制
和减缓计划及确定下次评价时间间隔的方法。
4基本规定
4.1ICDA应在Q/SY01023的指导下开展。 4.2ICDA应为一个连续、循环、不断修正趋准的检测和评价过程,通过识别评价发生腐蚀的部位和趋势,提出维护建议。 4.3ICDA前应根据管道的使用情况,编制工作方案,识别工作过程中的危险有害因素,并应采取安全防护措施。 4.4ICDA宜由包括工艺、腐蚀、检测等专业人员共同完成。 4.5可根据管道的运行情况和腐蚀状况开展ICDA,首次ICDA宜在管道投产3年内开展。 4.6调查、检测中需要室内分析、化验的项目应按规定取样,并应由专业实验室按相关标准规定的试验方法进行分析。 4.7管道内检测数据可作为确定直接检测开挖点位置的参考值,也可作为间接评价选点结果的验证对比数据。 4.8管道存在外腐蚀时,应按照SY/T0087.1的规定执行。
5预评价 5.1一般要求 5.1.1 预评价主要工作内容包括:资料收集、可行性分析、ICDA管段划分。 5.1.2 2应按照A.1至A.5的要求,收集管道的设计参数、施工概况、运行参数、维修维护历史等情况。 5.1.3 3宜按照A.6至A.8的要求收集管线内腐蚀检测、监测信息及其他可能影响管道内腐蚀的各种信息。 5.1.4 4可根据管道的历史和输送介质情况,收集可能影响管道内腐蚀的其他资料。 5.2 可行性分析 5.2.1 分析资料,确认收集的资料准确性。 5.2.2 2收集的资料能否满足开展油田集输管道内腐蚀直接评价需求。 5.2.3 3开展内腐蚀直接评价的管道能否执行直接检测。 5.3ICDA管段划分 5.3.1应按收集的数据,在管内工况发生突变点划分管段;对于双向输送的管道,应分别在两个方向上划分管段。 5.3.2下列位置处宜为单独的一个ICDA管段划分点: 2
Q/SY06038—2019
a)管道进液和出液处。 b)导致管道温度变化的换热器处。 c)导致管道压力变化的泵处。 d)管道阀门、清管器收发装置等处。 e)化学药剂注人处。 f)局部更换管道处。
5.3.3 3应对ICDA管段的边界进行确认。
6 间接评价 6.1 一般要求 6.1.1 应识别和分析管道ICDA子管段内腐蚀较严重的位置,评价管道内腐蚀高风险点,确定直接检测开挖点位置。 6.1.2 2间接评价应包括以下主要工作内容:
a)管道内多相流动工艺计算。 b)识别其他影响管道内腐蚀的因素,包括不稳定流动、清管历史等。 c)依据流动模型和地形起伏预测固体颗粒沉积趋势。 d)依据工艺计算识别的流型划分ICDA子管段。 e)依据内腐蚀预测模型预测各ICDA子管段内腐蚀严重程度。 f)确定管道内腐蚀高风险点。 g)依据内腐蚀风险点确定直接检测开挖点。
6.2管道内流动状态计算与ICDA子管段划分
6.2.1管道内流动状态计算应基于预评价收集的管道数据。 6.2.2管道内流动状态可采用数学模型进行计算,也可采用商业软件进行计算:对于管道弯头、地形连续起伏等需要详细分析流动状态的局部管段可采用计算流体力学的方法进行计算。 6.2.3管道内流动状态计算应能提供以下参数:
a)流型。 b)气体流速。 c)液体流速。 d)温度和压力。 e)持液率。 f)固体颗粒沉积趋势。
6.2.4应根据流动状态计算确定的管内流型划分ICDA子管段。
6.3 内腐蚀预测模型的确立
6.3.1[ 内腐蚀预测模型用于确定同一ICDA子管段内不同部位的腐蚀风险 6.3.2内腐蚀预测模型的选取和建立应基于对腐蚀原因的分析,内腐蚀预测模型的输人参数宜包含导致管壁内腐蚀的主要因素。 6.3.3内腐蚀预测模型宜能识别不同管段由于温度、压力、CO2、H,S、pH、CI-、矿化度、流速(或壁面剪切力)等因素而引起的管道内腐蚀风险的不同。 6.3.4内腐蚀预测模型应综合考虑影响管道内腐蚀的主要因素,宜采用多种内腐蚀预测模型进行预
3
Q/SY06038—2019 测,综合分析计算结果。 6.3.5内腐蚀预测模型可依据6.2中计算的沿程温度、压力等结果作为计算输入,也可在模型中内置流动参数计算方法, 6.3.6在ICDA子管段内应选取合适长度的管道间隔进行内腐蚀程度预测。 6.3.7应结合第7章直接检测对内腐蚀预测模型进行修正。 6.4内腐蚀高风险点和开挖点的确定 6.4.1应结合多相流模型和内腐蚀预测模型的结果判断内腐蚀高风险位置,内腐蚀高风险位置可按照以下准则确定:
a)根据内腐蚀预测模型计算的腐蚀风险较高点,ICDA子管段腐蚀风险的高点。 b)多相流引起的管道流动参数改变点,主要包括段塞流引起的管道内壁面剪切力及流速改变等。 c)管道曲率过大、弯头、截止阀、注入点等流体模型难以预测的管道部位。 d)管道内固体颗粒易于沉积处。
6.4.2从内腐蚀高风险点中选择具备开挖检测条件的点作为直接检测位置。 6.4.3如果多个位置腐蚀机理相同,腐蚀严重程度也相同,可选择一个位置作为直接检测位置。 6.4.4采用钢/复合材料套筒修复过的位置,不宜作为直接检测位置。 6.4.5 5每个ICDA管段直接检测位置宜不少于2处。
7直接检测 7.1一般要求 7.1.1 直接检测应结合间接评价结果,确定管道内腐蚀活性点,并应收集数据进行管体腐蚀安全评价。 7.1.2 2直接检测应包括下列内容:
a)开挖检测。 b)腐蚀管道安全评价。 c)修正。
7.2开挖检测
1管道内腐蚀状况的测量可采用非破坏性检测技术检测确定开挖坑内管段腐蚀严重部位。
7.2.1
7.2.2 2宜根据条件选择超声波测厚、超声导波、超声波C扫描、外漏磁检测等多种技术相结合的方法进行管道内壁腐蚀尺寸检测,并确定最大腐蚀深度、最大轴向长度和最大环向长度。 7.2.3 3当采用超声波测厚对壁厚损失进行定量评价,应多方位测量管道壁厚,确定轴向和环向壁厚损失。 7.3腐蚀管道的剩余强度评价 7.3.1直接检测位置减薄超过壁厚的10%的部位,应进行管道剩余强度评价。
a)管道剩余强度评价应按SY/T10048、SY/T6477或SY/T6151等进行。 b)对管道存在内腐蚀和外腐蚀并存的ICDA管段,应分别进行内腐蚀和外腐蚀的评价,然后进
行评价结果的综合分析,确定ICDA管段的剩余强度。 2对每个ICDA管段的剩余强度评价结果进行综合分析,以评价得出的剩余强度最小值或最严重
7.3.2 评价级别可确定为ICDA评价管段的最终评价结果。
7.3.3开挖检测发现应力腐蚀、焊接缺陷等其他管材内部缺陷时,应采用其他相应的方法进行评价。 4