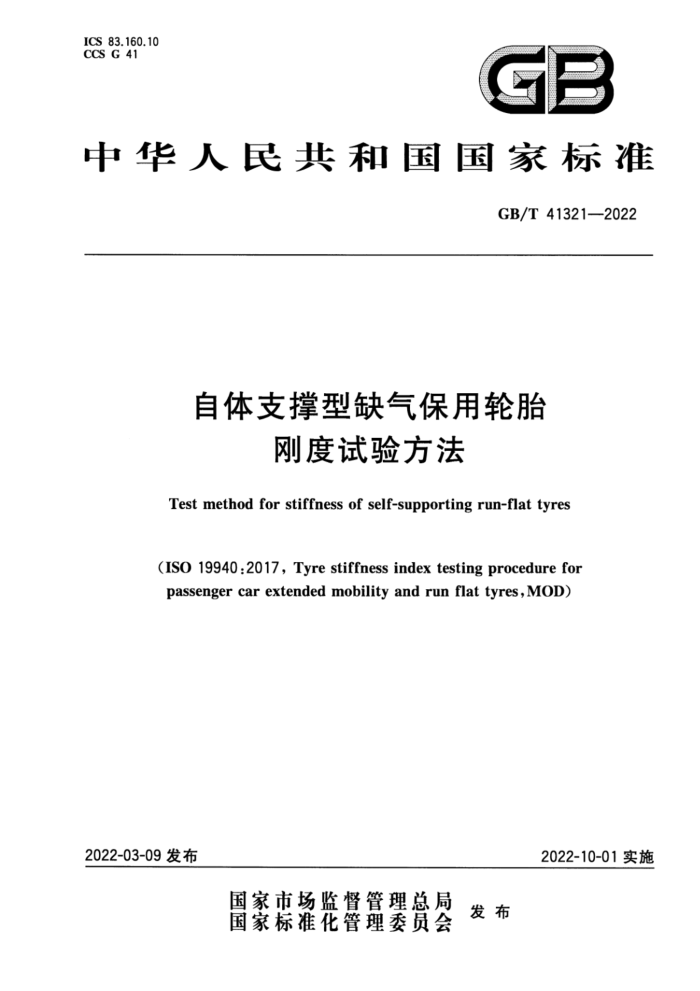
ICS 83.160.10 CCS G 41
GP
中华人民共和国国家标准
GB/T41321—2022
自体支撑型缺气保用轮胎
刚度试验方法
Test method for stiffness of self-supporting run-flat tyres
(ISO 19940:2017, Tyre stiffness index testing procedure for passenger car extended mobility and run flat tyres,MOD)
2022-10-01实施
2022-03-09发布
国家市场监督管理总局
国家标准化管理委员会 发布
GB/T41321—2022
前言
本文件按照GB/T1.1一2020《标准化工作导则 第1部分:标准化文件的结构和起草规则》的规定起草。
本文件修改采用ISO19940:2017《乘用车用移动延续型轮胎和缺气保用轮胎刚度指数试验程序》。 本文件与ISO19940:2017相比做了下述结构调整:
删除了3.13.11、3.18、3.19;第5章对应ISO19940:2017附录A。
-
一
本文件与ISO19940:2017的技术性差异及其原因如下:
规范性引用文件中用GB/T2978代替了ISO4000-1和ISO4000-2。同时根据需要增加了规范性引用文件GB/T6326和GB/T30196;
—删除了3.1~3.11,因已在规范性引用文件GB/T6326中有了定义;一第5章试验报告按照试验方法标准编写规范,规定了试验报告包括的内容。 本文件做了下列编辑性改动:
为与现有标准协调,将标准名称改为《自体支撑型缺气保用轮胎刚度性试验方法》。 请注意本文件的某些内容可能涉及专利。本文件的发布机构不承担识别专利的责任。 本文件由中国石油和化学工业联合会提出。 本文件由全国轮胎轮辋标准化技术委员会(SAC/TC19)归口。 本文件起草单位:山东玲珑轮胎股份有限公司、安徽佳通乘用子午线轮胎有限公司、中策橡胶集团
有限公司、汕头市浩大轮胎测试装备有限公司、北京橡胶工业研究设计院有限公司、双星集团有限责任公司、三角轮胎股份有限公司、浦林成山(山东)轮胎有限公司、万力轮胎股份有限公司、厦门正新橡胶工业有限公司、赛轮集团股份有限公司、双钱轮胎集团有限公司、四川轮胎橡胶(集团)股份有限公司、山东丰源轮胎制造股份有限公司、山东华盛橡胶有限公司、山东兴鸿源轮胎有限公司、普利司通(中国)投资有限公司、住友橡胶(中国)有限公司、焦作市质量技术监督检验测试中心、北京中启化标测控技术有限公司。
本文件主要起草人:陈少梅、张卫国、王剑波、黄县强、牟守勇、郑蕊、王君、李栋林、李崇兵、周琼、 陈建明、张晓军、李茂枝、唐件荣、孔东东、徐凯、李仁国、谷云鹏、章斌、张宏伟、王克先、李淑环、徐丽红、 王东。
I
GB/T41321—2022
自体支撑型缺气保用轮胎
刚度试验方法
1范围
本文件规定了自体支撑型缺气保用轮胎刚度的试验方法(包括测量试验设备及其精度要求、试验条件及试验步骤)和试验报告。
本文件适用于自体支撑型缺气保用轿车子午线轮胎刚度的测量。
2 规范性引用文件
下列文件中的内容通过文中规范性引用而构成本文件必不可少的条款。其中,注日期的引用文件,仅该日期对应的版本适用于本文件;不注日期的引用文件,其最新版本(包括所有的修改单)适用于本文件。
GB/T 2978 3轿车轮胎规格、尺寸、气压与负荷 GB/T6326轮胎术语及其定义(GB/T6326—2014,ISO4223-1:2002,NEQ) GB/T30196 自体支撑型缺气保用轮胎(GB/T30196—2022,ISO16992:2018,MOD)
3术语和定义
GB/T6326和GB/T30196界定的以及下列术语和定义适用于本文件。
3.1
标准气压referenceinflationpressure Pref 测试条件下第一阶段测试所用的充气压力。 注:单位为千帕(kPa)。
3.2
试验气压testinflationpressure p: 第“;”阶段的充气压力。 注:单位为千帕(kPa)。
3.3
垂直刚度verticalstiffness Kz 在轮胎充气条件下,通过施加垂直力测量的轮胎刚度。 注:单位为牛每毫米(N/mm)。
1
GB/T41321—2022
3.4
结构刚度structuralstiffness Kstr 零充气压力模式下测量所得的轮胎垂直刚度。 注:结构刚度是轮胎本身结构和技术的函数,单位为牛每毫米(N/mm)。
3.5
气压刚度 airstiffness Kair 一种轮胎特性,其计算方式为轮胎垂直刚度(充气时)与轮胎结构刚度(未充气时)的差值。 注:气压刚度是轮胎本身内腔空气体积与充气压力的函数,单位为牛每毫米(N/mm)。
3.6
下沉量deflection Sz 轮胎在承载板上在Z方向上的垂直位移。 注:单位为毫米(mm)。
4试验方法
4.1通则
自体支撑型缺气保用轮胎应符合GB/T30196的规定。 4.2 2充气轮胎垂直刚度测量 4.2.1轮胎的准备
标准型轮胎充气压力为250kPa,增强型轮胎充气压力为290kPa,将轮胎安装至4.2.3规定的试验轮辋上,并在(25士3)℃条件下存放至少3h。充气压力的偏差为士3kPa。
4.2.2轮胎测量位置
在轮胎的圆周取3个平均分布的位置进行测量。
参照位置可自由选择,但需能够接触承载板。如接头可见,应避开接头。 一一另外两个位置应平均分布在轮胎的圆周,每个位置的圆周跨度约为120°。
4.2.3 3试验轮辋
试验轮辋两侧应有突峰(平峰或圆峰),其宽度应符合GB/T2978的规定。试验轮辋应使用硬合金轮辋或重型轮辋。 4.2.4试验设备基本要求 4.2.4.1试验设备应能对轮胎和承载板加载相应的负荷,承载板的尺寸应大于轮胎印痕尺寸,且能实现两者间相互移动(轮胎向承载板或承载板向轮胎)。 4.2.4.2试验轮胎的旋转轴线应平行于承载板,且两者间的相互移动应能保持平行;最大移动速度应为 1mm/s,且每移动1mm能够至少采集5个数据点。
2
GB/T41321—2022
4.2.5 5试验设备设置
4.2.5.1 试验前,重置轮胎负荷传感器应在100N时启动测量数据收集工作。 4.2.5.2至少记录以下数据:
垂直负荷(F2)(N),负荷精度为负荷传感器满量程的士0.5%,但在所有情况下的最大值不应超过100N;绝对位置(z)(mm),精度为士0.5mm。
垂直负荷值(Fz)与绝对位置值(z)应为一一对应关系。 4.2.5.3测量设备周围环境温度应为(25士3)℃。 4.2.5.4每个充气压力阶段下(按表1)获得的数据点总数应在100~1000个之间。测量过程中,轮胎接触的承载板应为光滑钢面。
表1各试验阶段的试验条件
试验气压(P:)
下沉量
试验阶段i
kPa p ref 100 70 30
1 2 3 4
加载至负荷指数对应负荷能力的150%对应的下沉量(Szmx)
Szmx Szmx Szmx
4.2.6 最大试验负荷
轮胎标准气压(pref)下的最大试验负荷为负荷指数值对应的负荷能力的150%。 4.2.7试验步骤 4.2.7.1 将试验轮胎安装在试验设备上。 4.2.7.2试验轮胎和承载板之间的初始距离至少为10mm;此距离应为轮胎最低点和承载板之间的垂直距离。为设置数据收集的起点,给充气轮胎施加较小的负荷(Fz≤100N),以便确定轮胎和承载板的接触点。在此接触点基础上,将轮胎向远离承载板的方向移动至少10mm。最后的位置就是后续所有充气压力阶段的起点(0,0)。 4.2.7.3开始记录数据。 4.2.7.4以最高1mm/s的恒定加载速度,开始施加负荷。 4.2.7.5试验阶段1应在达到最大试验负荷(负荷指数对应负荷能力的150%)时停止,记录最大下沉量(Szmax),并将其作为后续所有试验阶段的止停线。 4.2.7.6卸载轮胎并按照4.2.7.2的描述将其回移至(0,0)位置。 4.2.7.7试验阶段2、3、4,需重复4.2.7.3、4.2.7.4、4.2.7.6的操作。每个阶段试验气压值按表1规定,测试时应确保加载停止线均为Szmx。阶段1~阶段4的垂直负荷与下沉量(Sz没有修正)的曲线图实例如图1所示。 4.2.7.8每个测量点都应重复4.2.7.3~4.2.7.7的流程。
3
GB/T 41321—2022
Y 10 000
8 000
6 000
4 000
2 000
-
1
0L 0
0x
5
10
15
20
25
标引符号与标引序号说明: X 轴 下沉量(Sz),单位为毫米(mm); Y轴 垂直负荷(F2),单位为牛(N);
试验气压为P时的拟合曲线:试验气压为100kPa时的拟合曲线;试验气压为70kPa时的拟合曲线;试验气压为30kPa时的拟合曲线。
1 2 3 4
图1阶段1~阶段4的垂直负荷与下沉量(Sz没有修正)的曲线图
4.3 零充气压力轮胎结构刚度测定 4.3.1概述
在零充气压力测量时,轮胎可能出现胎侧弯曲和胎面凸起;这种现象可能导致出现测量问题并产生不同的结果。因此,0kPa测量曲线应根据式(1)计算值进行绘制,使用4.2.7.7的4个试验阶段所得数据:
Fz(Szp,)=Fstr(Sz-IG,p;)+Far(Sz,p,)
...(1 )
式中: Fz—垂直负荷; Sz—下沉量; p:——每个阶段的轮胎试验气压(i为1~4); Fstr—轮胎结构特性所承受负荷; F——轮胎因充气所承受负荷。 计算的0kPa曲线斜率代表轮胎的结构刚度。阶段1阶段4的垂直负荷与下沉量关系曲线图和
0kPa条件下通过计算所得的曲线图如图2所示。
4
GB/T41321—2022
Y10 000
8 000
6 000
4 000
2 000
.0x
10
15
20
25
5
0
标引符号与标引序号说明: X 轴 下沉量(Sz),单位为毫米(mm); Y轴 垂直负荷(Fz),单位为牛(N);
试验气压为pr时的拟合曲线;试验气压为100kPa时的拟合曲线;试验气压为70kPa时的拟合曲线;试验气压为30kPa时的拟合曲线;气压为0kPa的拟合外推曲线。
1 2 3 4 5
图2阶段1~阶段4的垂直负荷与下沉量关系曲线图和 0kPa条件下通过计算所得的曲线图(Sz没有修正)
4.3.2 垂直负荷的数学模型
垂直负荷(Fz)与下沉量(S2)和充气压力(p:)关系的数学模型见式(2),应综合计算4个试验阶段的拟合曲线。
Fz(Szp)=(a.Sz3+b.S2+c.Sz)+d.p;Sz+f·p+e ......(2)
式中: a,b,c,dir,far,e 拟合参数; Sz
下沉量,单位为毫米(mm);每个阶段的轮胎试验气压(i为1~4),单位为千帕(kPa)。
p; 4.3.3近似度
按式(3)计算相对误差(r),且不应超过3.5%,如超过,应重新试验。
[Fz; - Fz(Fin) ] ?
(3)
2F
5
GB/T41321—2022
式中: Fz
垂直负荷的测量值,单位为牛(N);
F z;(Fi) 一垂直负荷的计算值,按式(2),单位为牛(N);
测量点的数量。
n
4.3.4总刚度的数学模型
总刚度(Kz)按式(4)进行计算,其源于式(2)负荷-下沉量曲线的斜率:
dFz
Kz(Sz+p.): dSz =3a·S2+2b.Sz+c+dar·pi
..(4)
式中: 3a·S2+26·Sz+c 结构部分; dair-pi
气压部分。
Kz可分为结构刚度部分和气压刚度部分,按式(5)进行计算:
Kz(Sz,p:)=Ksr(Sz)+Ka(p:)
·(5)
结构刚度按式(6)计算:
Ksr(Sz)=3a·S2+2b·Sz+c
.(6)
从式(6)看出结构刚度(Kr)取决于下沉量(Sz)。 充气压力为p:的气压刚度按式(7)计算:
K(p)=drp:
..(7)
4.3.5下沉量的计算
标准气压(prr)下垂直负荷为负荷指数对应负荷能力的0.8倍(0.8LI)的Fzo8,以及垂直负荷为负荷指数对应负荷能力的1.3倍(1.3LI)的Fz13的下沉量,按照式(8)和式(9)进行计算:
(8) ·(9)
Fz08(Sz08,Prer)=0.8LI Fz13(Sz13,pref)=1.3LI
式中: Sz08-—Pret下垂直负荷(Fzo8)的下沉量; Sz13—prer下垂直负荷(Fz13)的下沉量。 轮胎总刚度(Kot)和结构刚度(K,r)曲线图,以及标准气压下根据垂直负荷-下沉量曲线确定的
Szo8和Sz13如图3所示。
6