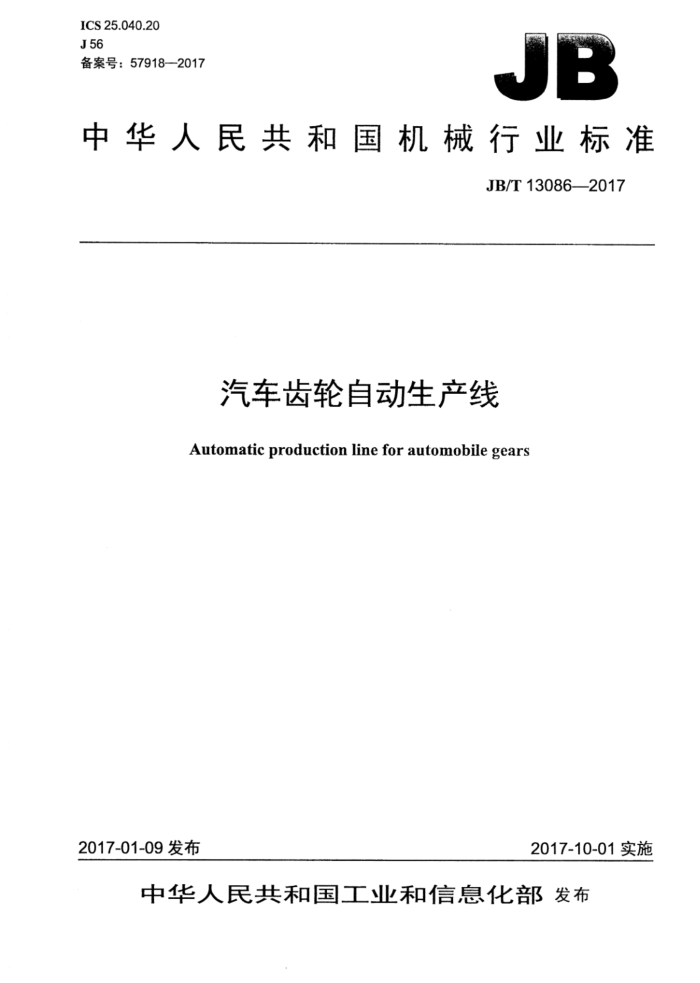
ICS25.040.20 J56 备案号:57918—2017
JB
中华人民共和国机械行业标准
JB/T13086—2017
汽车齿轮自动生产线
Automatic production line for automobile gears
2017-01-09发布
2017-10-01实施
中华人民共和国工业和信息化部发布
JB/T13086—2017
目
次
前言范围
工
1
2规范性引用文件. 3技术要求. 3.1一般要求. 3.2 参数(抽查) 3.3布局和外观.. 3.4 性能与结构.. 3.5 电气系统 3.6 数控系统.. 3.7 液压、气动和润滑系统 3.8 安全卫生 3.9 加工和装配质量. 3.10 自动线的空运转试验要求 3.11 自动线的精度检验要求 4检验验收 4.1 概述 4.2 一般要求 4.3 参数检验(抽查) 4.4 布局和外观检验.. 4.5 性能与结构检验. 4.6 电气系统检验.. 4.7 数控系统的检验. 4.8 液压、气动和润滑系统的检验, 4.9 安全卫生检验 4.10 自动线加工及装配质量检验 4.11 自动线的空运转试验 4.12 自动线的精度检验. 5包装
5
中
-
心
表1错位量、错位不匀称量、贴合缝隙值及缝隙不均匀值表2实际工序能力判断准则.
JB/T13086—2017
前言
本标准按照GB/T1.1一2009给出的规则起草。 本标准由中国机械工业联合会提出。 本标准由全国金属切削机床标准化技术委员会(SAC/TC22)归口。 本标准起草单位:重庆机床(集团)有限责任公司、南京二机齿轮机床有限公司、天津第一机床总
厂、四川普什宁江机床有限公司、武汉重型机床集团有限公司、重庆大学、宜昌长机科技有限责任公司、 嘉力宝控股集团有限公司。
本标准主要起草人:陈鹏、李先广、曾令万、李毅、喻可斌、李红、李光华、柴宝连、张勤、桂林、 刘飞、周泽红、陈立海。
本标准为首次发布。
II
JB/T13086—2017
汽车齿轮自动生产线
1范围
本标准规定了汽车齿轮自动生产线设计、制造、检验和验收的要求。 本标准适用于最大工件直径至260mm,主要完成车削、制齿、倒棱、去毛刺等工序的汽车齿轮自
动生产线(以下简称自动线)。
2规范性引用文件
下列文件对于本文件的应用是必不可少的。凡是注日期的引用文件,仅注日期的版本适用于本文件。凡是不注日期的引用文件,其最新版本(包括所有的修改单)适用于本文件。
GB5226.1-2008机械电气安全机械电气设备第1部分:通用技术条件 GB/T6576-2002 机床润滑系统 GB/T7932---2003 气动系统通用技术条件 GB/T90612006 金属切削机床通用技术条件 GB157602004 金属切削机床安全防护通用技术条件 GB/T16769一2008金属切削机床噪声声压级测量方法 GB/T23570—2009 金属切削机床焊接件通用技术条件 GB/T23571—2009 金属切削机床随机技术文件的编制 GB/T23572—2009 金属切削机床 液压系统通用技术条件 GB/T25373-2010 金属切削机床 装配通用技术条件 GB/T25374-2010 金属切削机床 清洁度的测量方法 GB/T25376—2010 金属切削机床 机械加工件通用技术条件 GB/T26220—2010 工业自动化系统与集成机床数值控制数控系统通用技术条件 JB/T8356机床包装技术条件
一
3技术要求
3.1一般要求 3.1.1按本标准验收机床时,还应对GB5226.1—2008、GB/T9061-2006、GB/T23570—2009、GB/T 25373一2010、GB/T25376一2010等中未经本标准具体化的有关项目进行检验。 3.1.2自动线主要由加工单元(各类加工设备)、控制单元、物流单元(机械手、料仓、交换料道等)和辅助单元(各类检测、清洗等设备)四大部分组成,其中加工单元及辅助单元除应按各自相应的产品标准及协议执行外,还需符合本标准的要求。 3.2参数(抽查)
自动线的参数应符合设计文件的规定。
1
JB/T13086—2017
3.3布局和外观 3.3.1 自动线应布局合理、造型美观、色彩和谐,符合人类工效学原则并便于调整及维修。 3.3.2自动线外观表面,不应有未规定的凸起、凹陷、粗糙不平和其他损伤。 3.3.3防护罩及防护装置应表面平整、匀称,不应翘曲、凹陷。 3.3.4外露焊缝应修整平直、均匀。 3.3.5外露零件表面不应有磕碰、锈蚀,螺钉、铆钉、销子端部不应有扭伤、锤伤等缺陷。 3.3.6电镀件、发黑件色调应一致,防护层不应有褪色、脱落现象。 3.3.7涂漆颜色及光泽应均匀一致,涂漆层应平整,涂漆表面不应有起泡及脱落等缺陷。未加工的零件表面以及设计要求的表面应涂上油漆。 3.3.8各种信息标志及标牌应在明显位置平整固定,清晰耐久,不歪斜。 3.3.9电气、液压、气压、润滑等的管路应布置紧凑、排列整齐、规范合理,不应产生扭曲、折叠及断裂等现象。 3.3.10自动线的零部件外露结合面的边缘应整齐匀称,不应有明显的错位,门、盖与自动线的结合面应贴合。错位量、错位不匀称量、贴合缝隙值及缝隙不均匀值不应大于表1的规定。
表1错位量,错位不匀称量、贴合缝隙值及缝隙不均匀值
单位为毫米
结合面边缘及门、盖
《500 1.5 1 1 1
>1250~3 150
>500~1250
边长尺寸错位量错位不匀称量贴合缝隙值缝隙不均匀值
2 1 1.5 1.5
3 1.5 2 2
注1:当结合面边缘及门、盖边长尺寸的长、宽不一致时,可按长边尺寸确定允许值。 注2:错位不匀称量指外露结合面边缘同一边或对应边最大错位量与最小错位量之差值。 注3:缝隙不均匀值指门、盖间对开缝或其相对于自动线本体间缝隙的最大值与最小值之差值。
3.4性能与结构 3.4.1加工单元、辅助单元和物流单元之间的机械对接接口应互相适应,加工单元中车削机床应有自动顶门,滚齿机(插齿机)、剃齿机等制齿设备应有自动上下料机构。 3.4.2自动线加工单元中各工序加工设备的节拍需平衡,保证各加工设备使用率。 3.4.3自动线控制单元的控制执行方式可采用总线集中控制或通过交互信号由物流单元中机械手控制系统控制。 3.4.4加工单元和物流单元与机械手间有上、下料请求信号,上、下料完成信号,循环、等待、故障、 停机、节能模式等信号的相互交换。 3.4.5工件在自动装卸、夹紧、放松过程中应有措施(吹气、气密检测等)防止切屑黏附在定位面和夹紧部位以保证定位准确和工件不损伤。 3.4.6加工单元中的滚齿机(插齿机)应有滚(插)后去毛刺机构,去毛刺刀需耐用。 3.4.7加工单元的各类夹具应为稳定可靠的自动夹具,必要时有防空拉功能。在加工两种或两种以上同类工件时,要求的定位和夹紧部位尺寸差别不大,夹具应采用更换零件时能快速只更换最少零件的结构型式。 3.4.8物流单元快速运行到位时应有缓冲功能。 3.4.9物流单元运行应平稳,动作应准确可靠,其中机械手在抓取或放置工件时应顺畅、无磕碰、平
2
JB/T13086—2017
稳。在车削工序的上料过程中,机械手放松工件推进时应具有柔性。 3.4.10人工上料的物流单元必要时应有工件放置防反功能。 3.4.11自动线中各个单元的操作应方便,必要时有副操作站。 3.4.12加工单元应有刀具寿命管理及加工尺寸补偿的功能。 3.5电气系统
自动线中的电气系统应符合GB5226.1一2008的规定。 3.6数控系统
自动线中的数控系统应符合GB/T26220一2010的规定。 3.7液压、气动和润滑系统 3.7.1自动线的液压系统应符合GB/T23572—2009的规定。 3.7.2自动线的润滑系统应符合GB/T6576一2002的规定。 3.7.3自动线的气动系统应符合GB/T7932-2003的规定。 3.7.4自动线的液压、润滑、气动系统及其他部位均不应渗漏。 3.8安全卫生 3.8.1自动线上有可能对人身健康或对设备易造成损伤的部位,应采取安全措施,自动线的安全防护应符合GB15760—2004、GB5226.1--2008的规定。 3.8.2在自动线加工区应设置防护装置,并应具有足够的强度和刚性。防护装置的设置应便于工件的置换以及操作者的观察。 3.8.3自动线的各机械手移动应设置可靠的限位装置。 3.8.4自动线的各机械手应具备断电保护功能,防止因断电引起的工件脱落和位移。 3.8.5人工操作区域应与机械手运动区域进行空间隔离,在重合区域应设置逻辑控制,并应有硬件防护机构。 3.8.6液压系统、气动系统应能提供稳定的正常工作的压力,当压力超出设定限值时,应发出警告信号或使自动线运动停止。 3.8.7加工单元的三色报警灯应设在易于观察的位置上,分别用绿色、红色、黄色表示正常、故障、 停止。 3.8.8压力表应标明压力范围,正常范围涂绿色,其余范围涂红色;油箱及冷却箱应有液位报警功能,并有液位上下限刻度标记,在明显位置有油品、油量标示。 3.8.9在空运转条件下,按GB/T16769一2008规定的方法检验自动线整线噪声,其噪声声压级不应超过 83 dB(A)。 3.9加工和装配质量 3.9.1机械加工件、焊接件应符合图样、工艺文件及GB/T25376—2010、GB/T23570—2009等的规定。 自动线的装配应符合GB/T25373一2010的规定。 3.9.2齿轮齿条、导向杆、夹爪等零件应采取耐磨措施,并符合材质及热处理有关标准的规定。 3.9.3直线导轨等结合面,其制造及验收应符合GB/T25376一2010和GB/T25373一2010的规定。 3.9.4自动线的清洁度的检测按GB/T25374一2010规定的方法进行。其齿轮齿条、导向杆、直线导轨输送单元等部位用目测法和手感法检验,不应有脏物
3
JB/T13086-2017
3.10自动线的空运转试验要求 3.10.1运转检验
自动线物流单元的运动部件在全行程上分别做低、中、高速进给的空行程试验,其运动应平稳、灵活,无异响,无爬行和振动现象。 3.10.2动作试验
动作试验一般包括下述内容: a)物流单元的每个工位运送工件(或工件托座)至机械手抓取或放入位置的动作连续起动、停止
各10次,动作应灵活、准确、无故障; b)检验机械手的进给、快速进给,检验机械手在行程范围内的任意给定位置的起动和停止,各检
验10次,动作应准确可靠、无故障; c)检验机械手夹爪夹紧、放松工件各10次,动作应可靠、工件无损伤; d)模拟工作状态,操纵“急停”按钮(或开关),连续10次,功能应准确、无故障; e)用数控程序操作,在中等速度下分别对各坐标轴进行正、反向的起动、停止(或制动)、工作进
给、快速进给,各进行10次,动作应灵活、准确、可靠; f)按设计要求,对各坐标轴定位,进给坐标超程保护,坐标位置显示,回基准点,手动数据输入,
程序,序号指示和检索,程序暂停,程序消除等功能分别进行试验,其功能应可靠,动作应灵活、准确;
g)对安全防护装置进行试验,功能应可靠,动作应准确。 3.10.3连续空运转试验
自动线模拟工作状态按设计规定的节拍进行整线连续空运转试验(带料不切削状态),其连续运转时间不少于48h。在空运转过程中,各部分工作应正常,运行应平稳;各项功能、性能应可靠,不出现故障。 3.11自动线的精度检验要求 3.11.1一般要求 3.11.1.1自动线中加工单元及辅助单元的精度,应先按各自相应的产品标准及协议进行检验。 3.11.1.2进行工作精度检验时,应提供足够数量(不少于50件)的符合要求的被加工零件。 3.11.1.3自动线应采用规定的切削规范和符合要求的刀具对被加工零件进行连续切削加工。 3.11.1.4按《被加工零件工序图》及节拍要求进行工作精度检验。自动线在连续加工过程中,若因故障停止,需排除故障后重新开始检验。 3.11.1.5工作精度有下列两种评定方法:
一方法1:直接评定;一方法2:用“实际工序能力指数CPK值”评定。
3.11.1.6自动线验收检验时,其工作精度只能采用3.11.1.5规定的方法1、方法2中的一种进行评定(由制造厂与用户协议确定)。 3.11.1.7需要用实际工序能力指数评定的项目和实际工序能力指数Cpk值的大小,由制造厂与用户协议确定。
4
JB/T13086—2017
3.11.2工作精度检验 3.11.2.1采用方法1评定时的工作精度检验
自动线完成规定数量(不少于50件)被加工零件的连续切削加工后,检验被加工部位的有关项目,均应全部合格。 3.11.2.2采用方法2评定时的工作精度检验
自动线完成规定数量(不少于50件)被加工零件的连续切削加工后,按加工顺序检验并记录被加工部位的有关精度,用“实际工序能力指数Cek值”评定:
a)实际工序能力指数Cpk按公式(1)~公式(4)计算。
Z(x ~x) n-1 Cp
(1)
T 6S
(2)
2|x-TM
K=
(3)
T
T-2|x-TM
Cpk = Cp (1- K)=
(4)
6S
式中: S—样本的标准偏差;
实测误差;样本平均值(分布中心);样本大小:
X x n
Cp -潜在工序能力指数;
工序公差;
T
K- 样本平均值(分布中心)与公差中心的相对偏离程度: TM 公差中心。
b)实际工序能力判断准则见表2。
表2实际工序能力判断准则
实际工序能力指数Cpk
实际工序能力状态
>1.67 >1.33~1.67 >1~1.33 >0.67~1 ≤0.67
过剩理想正常不足严重不足
4 检验验收
4.1# 概述 4.1.1每条自动线应在制造厂经检验合格后出厂,特殊情况下经用户同意可在自动线使用处进行检验。
5