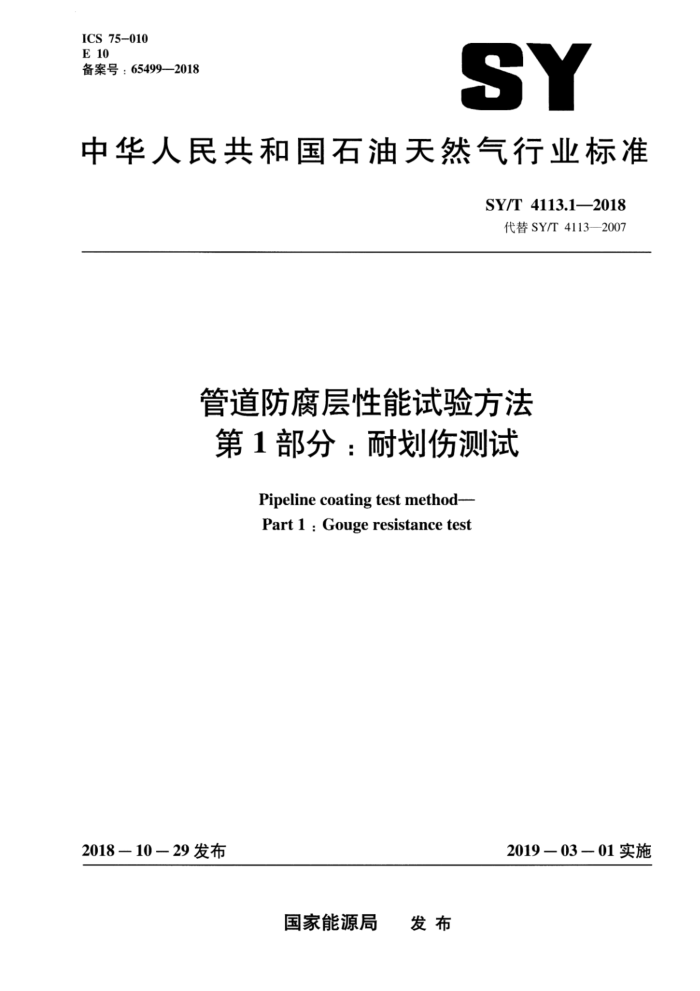
ICS 75-010 E 10 备案号:65499—2018
SY
中华人民共和国石油天然气行业标准
SY/T4113.1—2018
代替SY/T4113—2007
管道防腐层性能试验方法第1部分:耐划伤测试
Pipeline coating test method-- Part1:Gougeresistancetest
2018—10—29发布
2019-03-01实施
国家能源局 发布
SY/T4113.1—2018
目 次
前言
范围 2 规范性引用文件 3 设备
1
试件制备 5 测试程序
4
2
结果计算报告参考文献
6
4
7
SY/T 4113.1—2018
前言
SY/T4113《管道防腐层性能试验方法》分为以下部分:
第1部分:耐划伤测试;第2部分:剥离强度测试;
-
本部分为SY/T4113的第1部分。 本部分按照GB/T1.1一2009《标准化工作导则第1部分:标准的结构和编写》给出的规则起草。 本部分代替SY/T4113-2007《防腐涂层的耐划伤试验方法》,与SY/T4113—2007相比,主要
技术变化如下:
调整了标准范围,由“适用于管道外防腐层耐划伤性能的评价”调整为“适用于熔结环氧粉末防腐层、液体涂料防腐层、热固性复合材料等管道外防腐层耐划伤性能的测试”(见第1章);增加了划伤试验机结构设计示意图(见图1)调整了划伤头的要求,规定了单刃型和平滑型两类划伤头(见3.1.4);调整了划痕深度测量仪接触点直径,由1.8mm调整为“探头接触点的直径应低于1.2mm,但不应是针尖式探头”(见3.3);调整划伤速度,由254mm/min调整为250mm/min±25mm/min(见5.2.5)。
本部分由石油工程建设专业标准化委员会提出并归口。 本部分起草单位:中国石油天然气股份有限公司管道分公司、中国石油规划总院、APlus
CoatingSolutionsInc.、中国石油天然气管道科学研究院、中国石油集团工程技术研究院。
本部分主要起草人:李睿、冯少广、冯庆善、罗锋、饶珊、王德增、赵国星、李东阳、朱琳孔宪刚。
II
SY/T 4113.1—2018
管道防腐层性能试验方法第1部分:耐划伤测试
1范围
SY/T4113的本部分规定了实验室测试管道外防腐层抗机械划伤能力的试验方法。 本部分适用于熔结环氧粉末防腐层、液体涂料防腐层、热固性复合材料等管道外防腐层耐划伤性
能的测试。
2规范性引用文件
下列文件对于本文件的应用是必不可少的。凡是注日期的引用文件,仅注日期的版本适用于本文件。凡是不注日期的引用文件,其最新版本(包括所有的修改单)适用于本文件。
GB/T9217.10硬质合金旋转锉第10部分:锥形圆头旋转锉(L型) SY/T0063管道防腐层检漏试验方法 SY/T0066钢管防腐层厚度的无损测量方法(磁性法)
3设备
3.1划伤试验机应由负载系统、滑动平台、动力装置和划伤部件等组成。 3.1.1划伤试验机结构宜为图1所示。
负载系统
划伤部件
防腐层试样
动力装置
滑动平台
图1划伤试验机结构设计示意图
3.1.2负载系统应为可调节的,应满足划伤过程中防腐层所受到的总负载为30kg,50kg或其他数值的负载要求,精度应为土1%。划伤过程中,划伤头应始终与防腐层保持垂直。 3.1.3滑动平台应能以恒定速度移动,上方可固定防腐层试件,移动速度宜为250mm/min±25mm/min,可移动的距离应不小于75mm。 3.1.4划伤部件中的划伤头可选用图2所示的单刃型或图3所示的平滑型。 3.1.5单刃型划伤头应符合GB/T9217.10的规定,选尺寸宜为d=6mm,l=16mm,R=1.2mm。单刃划伤头使用次数不应超过60次。
1
SY/T4113.1—2018
3.1.6平滑型划伤头应无螺旋槽,选尺寸宜为d=6mm,[=16mm,R=1.2mm。平滑划伤头使用次数不应超过100次。 3.1.7在划伤试验过程中,划伤头接触到试件母材的金属部分时,该划伤头不应再继续使用。
图2单刃型划伤头示例
图3平滑型划伤头示例
3.1.8动力装置应能保证滑动平台保持恒定速率移动。 3.2 磁性测厚仪应符合SY/T0066的规定,精度为±1%。 3.3划痕深度测量仪探头接触点的直径应小于1.2mm,但不应为针尖式探头,测量精度为0.01mm。 3.44 钢直尺量程宜为0mm~100mm,精度为1mm。 3.5电火花检漏仪应符合SY/T0063的规定。
4试件制备
4.1试件可为实验室涂敷试件或现场取样试件。 4.2实验室试件尺寸宜为100mm×100mm×6mm,应根据防腐层的涂敷要求制备试件,防腐层厚度应与管道防腐层设计厚度及偏差保持一致。每组试件应不少于3件。 4.3管段裁切试件尺寸宜为100mm×50mm×管壁厚度,试件长度方向应与管道轴向平行。每组试件应不少于3件,试件表面应清洁干燥。 4.4防腐层表面不应有外观缺陷。涂层应按SY/T0063的规定进行电火花检测,应无漏点。 4.5测试前,试件宜放置在23℃±2℃的温度环境下至少24h并记录。
5测试程序 5.1 防腐层厚度测量 5.1.1 测试前,应按SY/T0066规定的方法使用磁性测厚仪进行防腐层厚度测量。 2
SY/T4113.1—2018
5.1.2厚度的测量应在试件将被划刻的轨迹上进行,应在每条轨迹的中间点和距中间点两侧各25mm 处测量,测量点应为3处,并应在防腐层表面标示清楚。 5.2测试步骤 5.2.1选择符合测试要求的划伤头。 5.2.2将试件固定在划伤试验机的滑动平台上。涂层面应朝上放置,应面对施力点并与划伤头垂直。 平板试件应与滑动平台平行。管段试件的长轴方向应与滑动方向平行。 5.2.3划伤试验应在距试件边缘距离不小于12mm的范围内进行。每个平板试件可做3条平行划痕,划痕间隔应不少于10mm。每个管段裁切试件只做1条划痕,且划痕应在试件正中间管道曲线顶端处。 5.2.4在负载系统上施加所需要的配重块,使总负载达到30kg,50kg或其他负载。施加负载后,应在5s内开始测试。 5.2.5试件宜以250mm/min±25mm/min的恒定速度在划伤头下匀速水平移动,划痕长度宜为75mm。 测试过程中不应出现划伤头抖动或跳动。整个测试过程中,测试区域应始终保持与划伤头垂直。 5.2.6达到规定划伤距离后,停止测试,升起配重,取出试件,并测量划痕深度。 5.3划痕深度测量 5.3.1测量前应采用适宜的方法清除表面上超过涂层正常厚度的松散涂层,清除过程应避免防腐层产生漏点。 5.3.2测量时,应将试件放在平稳的工作台上,且涂层面朝上。 5.3.3以划伤前已测试涂层厚度的各点为测量点,先将划痕深度测量仪放在防腐层表面,在该测量点一侧的未划伤区域调节零点。 5.3.4沿着划痕方向调节划痕深度测量仪,测试探头应落人划痕底部,逐一测量各划痕轨迹上各测量点的划痕深度。 5.3.5应记录测量点的划痕深度并计算出各测量点的剩余厚度,并计算样品的平均划伤深度。 5.4漏点检测 5.4.1检测应在23℃±2℃下进行。 5.4.2 测试前应根据各测量点防腐层的剩余厚度,确定检漏电压。 5.4.3 防腐层存在漏点时,应判定测试结果为不合格。
6结果计算
防腐层的耐划伤性能以一定划伤负载下的划痕深度及漏点情况表示,划痕深度应以9个测量点划痕深度的算术平均值表示,精确到0.01mm。
7报告
试验报告应至少包括下列资料: a)执行标准。 b)试件名称、规格及来源。 c)试件的类型、尺寸、防腐层的平均厚度。 d)划伤试验机的型号。
3
SY/T4113.1—2018
e) 划伤速度。 f)划伤头类型。 g)测试温度。 h) 检测结果,食 包括负载(kg)、划痕深度的平均值(mm)、检测电压(kV)和是否有漏点。 i)试验日期、试验人员、试验单位。
4
SY/T4113.1—2018
参考文献
[1]GB/T9217.1 硬质合金旋转锉 第1部分:通用技术条件
5