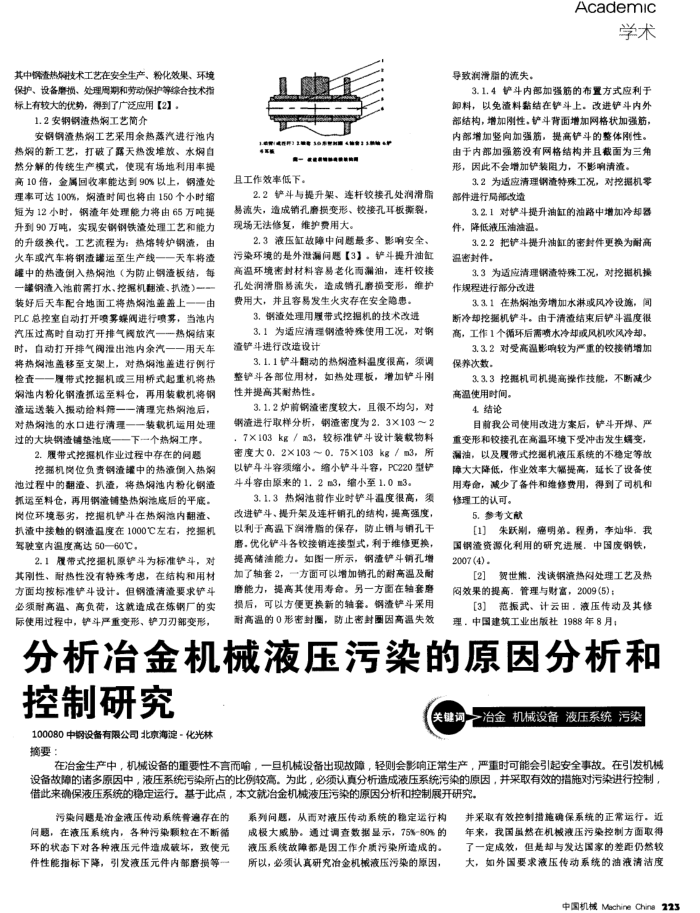
其中钢查热姆技术工艺在安全生产、粉化效果、环境保护、设备磨损、处理周期和劳动保护等综合技术指标上有较大的优势,得到了广泛应用【2】。
1.2安钢钢渣热焖工艺简介
安钢钢清热焖工艺采用余热蒸汽进行池内热焖的新工艺,打破了露天热泼堆放、水焖自然分解的传统生产模式,使现有场地利用率损高10倍,金属回收率能达到90%以上,钢渣处理率可达100%,焖渣时间也将由150个小时缩短为12小时,钢渣年处理能力将由65万吨摄升到90万吨,实现安钢钢铁澄处理工艺和能力的升级换代,工艺流程为:热熔转炉钢渣,由火车或汽车将钢渣罐运至生产线一一天车将渣罐中的热查例入热焖池(为防止钢渣板结,每一罐钢渣入池前需打水、挖掘机翻渣、扒渣)装好后天车配合地面工将热焖池盖盖上一
申
PLC总控室自动打开喷雾媒阀进行喷募,当池内汽压过高时自动打开排气阀放汽一热焖结束时,白动打开排气阔滑出池内余汽一一用天车将热焖池盖移至支架上,对热焖池盖进行例行检查一一厘带式挖掘机或三用桥式起重机将热焖池内粉化钢渣抓运至料仓,再用装载机将钢渣运送装入振动给料筛一一清理完热解泡后对热焖池的水口进行清理一一装载机运用处理过的大块钢渣铺整池底——下一个热焖工序,
2.履带式挖握机作业过程中存在的问题挖掘机岗位负责钢渣罐中的热渣倒入热池过程中的翻渣、扒渣,将热焖池内粉化钢渣抵运至料仓,再用钢渣铺垫热焖池底后的平底,岗位环境恶劣,挖据机铲斗在热焖池内翻渣、扒渣中接触的钢渣温度在1000℃左右,挖掘机驾驶室内温度高达50—60℃,
2.1履带式挖据机原铲斗为标准铲斗,对其刷性、耐热性没有特殊考患,在结构和用材方面均按标准铲斗设计。但钢渣清渣要求铲斗必须耐高温、高负荷,这就造成在炼钢厂的实际使用过程中,铲斗严重变形、铲刀刃部变形,
且工作效率低下。
m933mu61
######的间
2.2铲斗与提升架、连杆铰接孔处润滑脂易流失,造成销孔磨损变形、钦接孔耳板撕裂,现场无法修复,维护费用大。
2.3液压缸故障中间题最多、影响安全、污染环境的是外泄漏问题【3】。铲斗提升油缸高温环境密封材料容易老化面漏油,连杆铰接孔处润清脂影流失,造成销孔磨损变形,维护费用大,并且容易发生火灾存在安全隐惠,
3.钢查处理用暖带式挖据机的技术改进
3.1为适应清理钢渣特殊使用工况,对钢渣铲斗进行改造设计
3.1.1铲斗翻动的热焖渣料温度很高,须调整铲斗各部位用材,如热处理板,增加铲斗刚性并提高其耐热性。
3.1.2炉前钢渣密度较大,且很不均匀,对第清进行取样分析,钢流密度为2,3×103~2,7×103kg/m3,较标准铲斗设计装毂物料密度大0.2×103~0.75×103kg/m3,所以铲年斗容须缩小。缩小铲斗斗容,PC220型铲升斗容由原来的1.2m3,缩小至1.03。
3.1.3热焖池前作业时铲斗温度很高,须改进铲斗、提升架及连杆销孔的结构,提高强度,以利于高温下润滑脂的保存,防止销与销孔干磨,优化铲斗各较接销连接型式,利于维修更换,提高储油能力。如图一所示,钢渣铲斗销孔增加了轴套2,一方面可以增加销孔的耐高温及耐磨能力,提高其使用寿命。另一方面在轴套磨损后,可以方便更换新的轴套。钢渣铲斗采用耐高温的0形密封圈,防止密封围因高温失效
导致润滑脂的流失,
Academic
学术
3.1.4铲斗内部加强筋的布置方式应利于卸料,以免渣料黏结在铲斗上。改进铲斗内外部结构,增加性,铲斗背面增加网格状加强筋,内部增加竖向加强筋,提高铲斗的整体刚性。由于内部加强筋没有网格结构并且截面为三角形,因此不会增加铲装阻力,不影响清潼。
3.2为适应清理钢渣特殊工况,对挖据机零部件进行局部改造
3.2.1对铲斗提升油缸的油路中增加冷却器件,降低液压油油湿。
3.2.2把铲斗提升油缸的密封件更换为耐高温密封件,
3.3为适应清理钢渣特殊工况,对挖据机操作规程进行部分改进
3.3.1在热焖池旁增加水淋或风冷设施,间断冷却挖掘机铲斗。由于清渣结束后铲斗温度很高,工作1个循环后需喷水冷却或风机吹风冷却。
3.3.2对受高温影响较为严重的铰接销增加保养次数。
3.3.3挖摄机司机提高操作技能,不断减少高温使用时间。
4.结论
目前我公司使用改进方案后,铲斗开焊、严重变形和铰接孔在高温环境下受冲击发生姆变,漏油,以及履带式挖掘机液压系统的不稳定等故障大大降低,作业效率大福提高,延长了设备使用寿命,减少了备件和维修费用,得到了司机和修理工的认可。
5.参考文献
[1]朱跃别,癌明第。程勇,李灿华,我国钢渣资源化利用的研究进展,中国废钢铁, 2007(4)。
[2]
贺世熊,浅谈钢流热问处理工艺及热
问效果的提高。管理与财富,2009(5);
[3]
范振武、计云田,液压传动及其修
理.中国建筑工业出版社1988年8月:
分析冶金机械液压污染的原因分析和
控制研究 100080中钢设备有限公司北京海淀-化光林摘要:
>冶金机械设备液压系统污染
在冶金生产中,机械设备的重要性不言而喻,一旦机械设备出现故障,轻则会影响正常生产,严重时可能会引起安全事故。在引发机械设备故障的诸多原因中,液压系统污染所占的比例较高。为此,必须认真分析造成液压系统污染的原因,并采取有效的措施对污染进行控制,借此来确保液压系统的稳定运行。基于此点,本文就冶金机械液压污染的原因分析和控制展开研究。
污荣间问题是冶金液压传动系统普遍存在的
问题,在液压系统内,各种污染颗粒在不断循环的状态下对各种液压元件造成破坏,致使元件性能指标下降,引发液压元件内部磨损等
系列间题,从而对液压传动系统的稳定运行构成极大威胁。通过调查数据显示,75%-80%的液压系统故障都是因工作介质污染所造成的。所以,必须认真研究冶金机械液压污染的原因,
并采取有效控制措施确保系统的正常运行。近年来,我国虽然在机械渡压污染控制方面取得了一定成效,但是却与发达国家的差距仍然较大,如外国要求液压传动系统的油液清洁度
中国机械 Mechine Chine 223