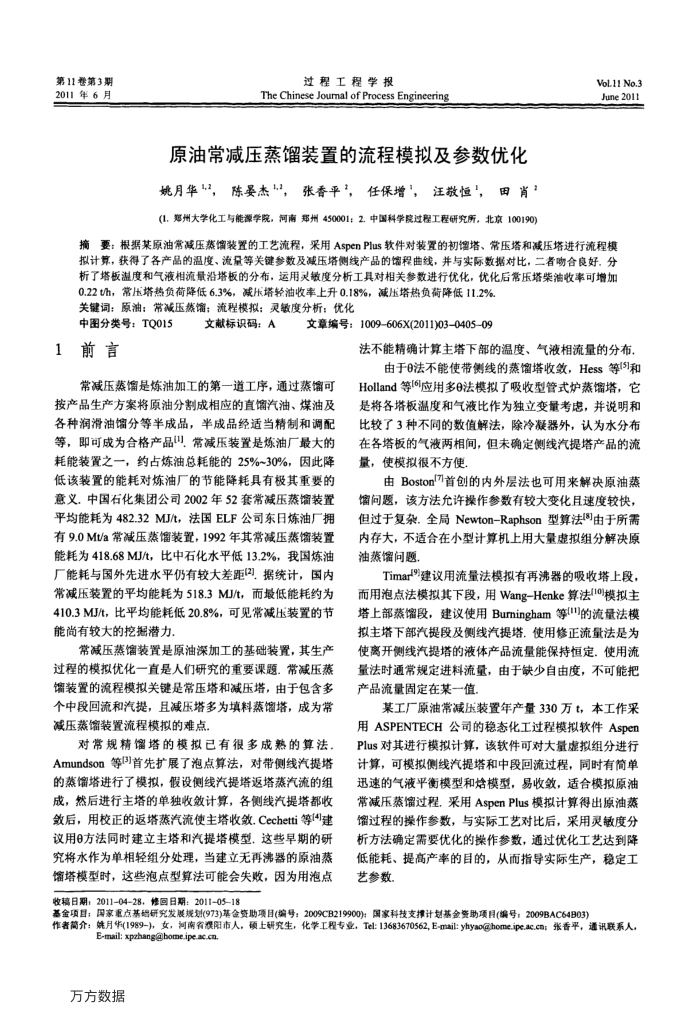
第11卷第3期 2011年6月
过程工程学报
The Chinese Jourmal of Process Engineering
原油常减压蒸馏装置的流程模拟及参数优化姚月华",陈晏杰,张香平”,任保增,汪敬恒",田肖(1.郑州大学化工与能源学院,河南郑州450001;2.中国科学院过程工程研究所,北京100190)
VoL.1I No.3 June2011
摘要:根据某原油常减压蒸馏装置的工艺流程,采用AspenPlus软件对装置的初馏塔、常压塔和减压塔进行流程模拟计算,获得了各产品的温度、流等关键参数及减压塔侧线产品的增程曲线,并与实际数据对比,二者吻合良好,分析了塔板温度和气液相流量沿塔板的分布,运用灵敏度分析工具对相关参数进行优化,优化后常压塔柴油收率可增加
0.22t/h,常压塔热负荷降低6.3%,减压塔轻油收率上升0.18%,减压塔热负荷降低11.2% 关键词:原油:常减压然馏;流程模拟:灵敏度分析:优化
中图分类号:TQ015 1前言
文献标识码:A
文章编号:1009-606X(2011)03-0405-09
法不能精确计算主塔下部的温度、气液相流量的分布。
由于0法不能使带侧线的蒸馏塔收敛,Hess等(5]和
常减压蒸馏是炼油如工的第一道工序,通过蒸馏可按产品生产方案将原油分割成相应的直馅汽油、煤油及各种润滑油馏分等半成品,半成品经适当精制和调配等,即可成为合格产品,常减压装置是炼油厂最大的耗能装置之一,约占炼油总耗能的25%~30%,因此降低该装置的能耗对炼油厂的节能降耗具有极其重要的意义,中国石化集团公司2002年52套常减压蒸馏装置平均能耗为482.32MJ/t,法国ELF公司东日炼油厂拥有9.0Mta常减压蒸馏装置,1992年其常减压馏装置能耗为418.68MJ/t,比中石化水平低13.2%,我国炼油厂能耗与国外先进水平仍有较大差距(2),据统计,国内常减压装置的平均能耗为518.3MJ/t,而最低能耗约为 410.3MJ/,比平均能耗低20.8%,可见常减压装置的节能尚有较大的挖掘潜力
常减压蒸增装置是原油深加工的基础装置,其生产过程的模拟优化一直是人们研究的重要课题。常减压蒸馏装置的流程模拟关键是常压塔和减压塔,由于包含多个中段回流和汽提,且减压塔多为填料蒸馏塔,成为常减压蒸馏装置流程模拟的难点。
对常规精馏塔的模拟已有很多成熟的算法, Amundson等[3)首先扩展了泡点算法,对带侧线汽提塔的蒸馏塔进行了模拟,假设侧线汽提塔返塔蒸汽流的组成,然后进行主塔的单独收敛计算,各侧线汽提塔都收敛后,用校正的返塔蒸汽流使便主塔收敛Cechetti等l4建议用方法同时建立主塔和汽提塔模型.这些早期的研究将水作为单相轻组分处理,当建立无再沸器的原油蒸馏塔模型时,这些泡点型算法可能会失败,因为用泡点
Holland等[6]应用多θ法模拟了吸收型管式炉蒸馏塔,它是将各塔板温度和气液比作为独立变量考虑,并说明和比较了3种不同的数值解法,除冷凝器外,认为水分布在各塔板的气液两相间,但未确定侧线汽提塔产品的流量,使模拟很不方便
由Boston[7]首创的内外层法也可用来解决原油馏间题,该方法允许操作参数有较大变化且速度较快,但过于复杂.全局Newton-Raphson型算法由于所需内存大,不适合在小型计算机上用大量虚拟组分解决原油蒸馏问题
Timarl"建议用流量法模拟有再沸器的吸收塔上段,而用泡点法模拟其下段,用Wang-Henke算法10)模拟主塔上部蒸馏段,建议使用Burningham等(]的流量法模拟主塔下部汽提段及侧线汽提塔.使用修正流量法是为使离开侧线汽提塔的液体产品流量能保持恒定.使用流量法时通常规定进料流量,由于缺少自由度,不可能把产品流量固定在某一值
某工厂原油常减压装置年产量330万t,本工作采用ASPENTECH公司的稳态化工过程模拟软件Aspen Plus对其进行模拟计算,该软件可对大量虚拟组分进行计算,可模拟侧线汽提塔和中段回流过程,同时有简单迅速的气液平衡模型和模型,易收敛,适合模拟原油常减压蒸馏过程,采用AspenPlus模拟计算得出原油蒸馏过程的操作参数,与实际工艺对比后,采用灵敏度分析方法确定需要优化的操作参数,通过优化工艺达到降低能耗、提高产率的目的,从而指导实际生产,稳定工艺参数.
收稿日期:2011-04-28,修回日期:2011-05~18
基金项目:国家重点基确研究发展规划(973)革金资助项目(编号:2009CB219900):国家科技支撑计划基金资助项目(编号:2009BAC64B03)
作者简介:姚月华(1989-),女,河南省限阳市人,硕上研究生,化学工程专业,Tel:13683670562,E-mail:yhyao@home.ipe.ac.cn;张香平,通讯联系人
E-mail: xpzhang@home.ipe.ac.cn 万方数据