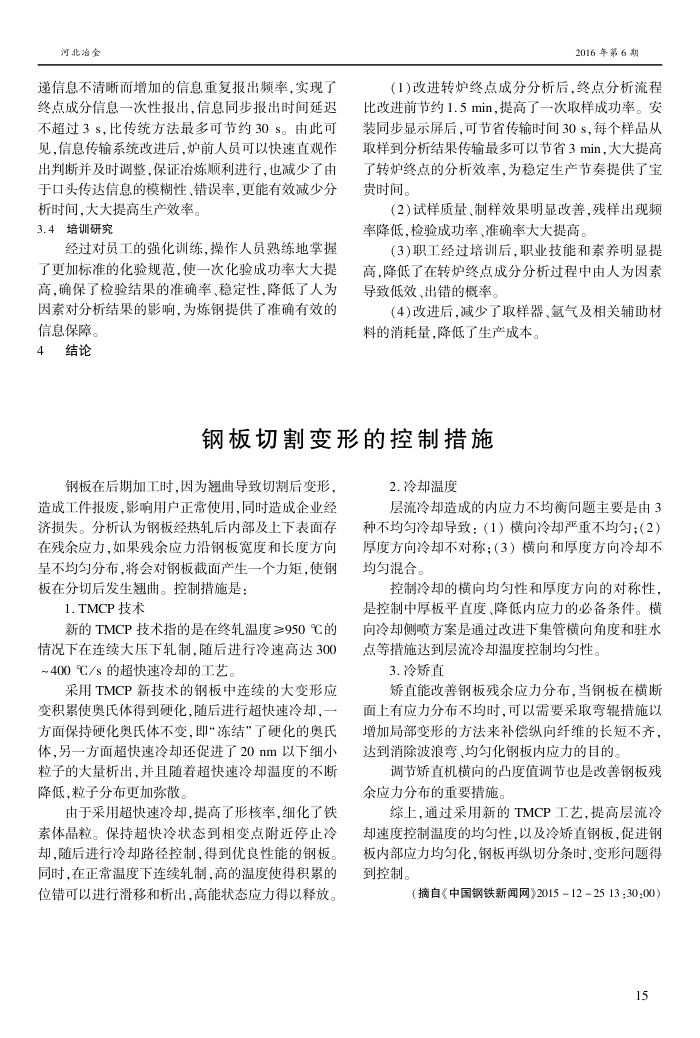
河北冶会
递信息不清晰而增加的信息重复报出频率,实现了终点成分信息一次性报出,信息同步报出时间延迟不超过3s,比传统方法最多可节约30S。由此可见,信息传输系统改进后,炉前人员可以快速直观作出判断并及时调整,保证冶炼顺利进行,也减少了由于口头传达信息的模糊性、错误率,更能有效减少分
析时间,大大提高生产效率。 3.4培训研究
经过对员工的强化训练,操作人员熟练地掌握了更加标准的化验规范,使一次化验成功率大大提高,确保了检验结果的准确率、稳定性,降低了人为因素对分析结果的影响,为炼钢提供了准确有效的
信息保障。 4结论
2016年第6期
(1)改进转炉终点成分分析后,终点分析流程比改进前节约1.5min,提高了一次取样成功率。安装同步显示屏后,可节省传输时间30s,每个样品从取样到分析结果传输最多可以节省3min,大大提高了转炉终点的分析效率,为稳定生产节奏提供了宝贵时间。
(2)试样质量、制样效果明显改善,残样出现频率降低,检验成功率、准确率大大提高。
(3)职工经过培训后,职业技能和素养明显提高,降低了在转炉终点成分分析过程中由人为因素导致低效、出错的概率。
(4)改进后,减少了取样器、氢气及相关辅助材料的消耗量,降低了生产成本。
钢板切割变形的控制措施
钢板在后期加工时,因为翻曲导致切割后变形造成工件报废,影响用户正常使用,同时造成企业经济损失。分析认为钢板经热轧后内部及上下表面存在残余应力,如果残余应力清钢板宽度和长度方向呈不均匀分布,将会对钢板截面产生一个力矩,使钢板在分切后发生翘曲。控制措施是:
1.TMCP技术
新的TMCP技术指的是在终轧温度≥950℃的
情况下在连续大压下轧制,随后进行冷速高达300 ~400℃/s的超快速冷却的工艺。
采用TMCP新技术的钢板中连续的大变形应变积累使奥氏体得到硬化,随后进行超快速冷却,一方面保持硬化奥氏体不变,即“冻结”了硬化的奥氏体,另一方面超快速冷却还促进了20nm以下细小粒子的大量析出,并且随着超快速冷却温度的不断降低,粒子分布更加弥散。
由于采用超快速冷却,提高了形核率,细化了铁
系体晶粒。保持超快冷状态到相变点附近停止冷却,随后进行冷却路径控制,得到优良性能的钢板。司时,在正常温度下连续轧制,高的温度使得积累的位错可以进行滑移和析出,高能状态应力得以释放。
2.冷却温度
层流冷却造成的内应力不均衡问题主要是由3 种不均匀冷却导致:(1)横向冷却严重不均勾:(2)厚度方向冷却不对称:(3)横向和厚度方向冷却不均匀混合。
控制冷却的横向均匀性和厚度方向的对称性
是控制中厚板平直度、降低内应力的必备条件。横向冷却侧喷方案是通过改进下集管横向角度和驻水点等措施达到层流冷却温度控制均匀性。
3.冷矫直
矫直能改善钢板残余应力分布,当钢板在横断面上有应力分布不均时,可以需要采取弯辊措施以增加局部变形的方法来补偿纵向纤维的长短不齐,达到消除波浪弯、均匀化钢板内应力的目的。
调节矫直机横向的凸度值调节也是改善钢板残余应力分布的重要措施。
综上,通过采用新的TMCP工艺,提高层流冷
却速度控制温度的均匀性,以及冷矫直钢板,促进钢板内部应力均勾化,钢板再纵切分条时,变形问题得到控制。
(摘自(中国钢铁新闻网》2015-12-2513:30:00)
15