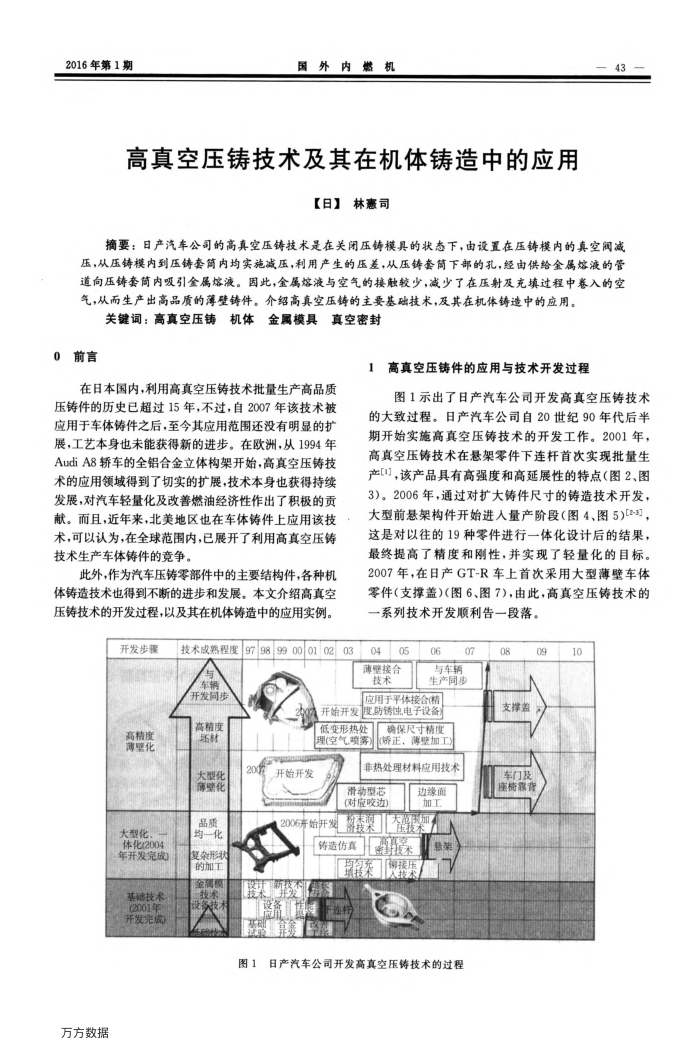
2016年第1期
国外内燃机
高真空压铸技术及其在机体铸造中的应用
【日】林惠司
43
摘要:日产汽车公司的高真空压铸技术是在关闭压铸模具的状态下,由设置在压铸模内的真空间减压,从压铸模内到压铸套简内均实施减压,利用产生的压差,从压铸套简下部的孔,经由供给全属熔液的管道向压铸套筒内吸引金属熔液。因此,金属熔液与空气的接触较少,减少了在压射及充填过程中春入的空气,从而生产出高品质的薄壁铸件。介绍高真空压铸的主要基础技术,及其在机体铸造中的应用。
关键词:高真空压铸机体金属模具
真空密封
0前言
在日本国内,利用高真空压铸技术批量生产高品质压铸件的历史已超过15年,不过,自2007年该技术被应用于车体铸件之后,至今其应用范围还没有明显的扩展,工艺本身也未能获得新的进步。在欧洲,从1994年 AudiA8轿车的全铝合金立体构架开始,高真空压铸技术的应用领域得到了切实的扩展,技术本身也获得持续发展,对汽车轻量化及改善燃油经济性作出了积极的贡献。而且,近年来,北美地区也在车体铸件上应用该技术,可以认为,在全球范围内,已展开了利用高真空压铸技术生产车体铸件的竞争。
此外,作为汽车压铸零部件中的主要结构件,各种机体铸造技术也得到不断的进步和发展,本文介绍高真空压铸技术的开发过程,以及其在机体铸造中的应用实例。
开发步摄高精度薄壁化
大型化、体化(2004 年开发完成)
基础技术(2001年开发完成
万方数据
1高真空压铸件的应用与技术开发过程
图1示出了日产汽车公司开发高真空压铸技术的大致过程。日产汽车公司自20世纪90年代后半期开始实施高真空压铸技术的开发工作。2001年,高真空压铸技术在悬架零件下连杆首次实现批量生产[1],该产品具有高强度和高延展性的特点(图2、图 3)。2006年,通过对扩大铸件尺寸的铸造技术开发,大型前悬架构件开始进入量产阶段(图4、图5)[2-3],这是对以往的19种零件进行一体化设计后的结果,最终提高了精度和刚性,并实现了轻量化的目标。 2007年,在日产GT-R车上首次采用大型薄壁车体零件(支撑盖)(图6、图7),由此,高真空压铸技术的一系列技术开发顺利告一段落。
技术成熟程度97989900010203
0405
车辆开发同步
高精度环材
大型化薄睡化
品质均一化复杂形状的加工金属颗技术技才
200m
开始开发
薄壁接合技术
06
07
与车辆生产同步
应用于平体接合(精
开始开发度防锈蚀电子设备)
低变形热处理(空气.喷雾
确保尺寸精度(矫正,薄壁加工
非热处理材料应用技术
滑型芯(对应咬边)
2006齐始开发
铸造仿真暖来
勇柔
边缘面加工
憨菜
铆接压
设
施来
基码
图1日产汽车公司开发高真空压铸技术的过程
08 支撑盖车门及
09
座椅靠背
10